富士電機製品コラム
脱炭素経営は「企業の要諦」~3ステップで製造業の脱炭素化に取り組む!
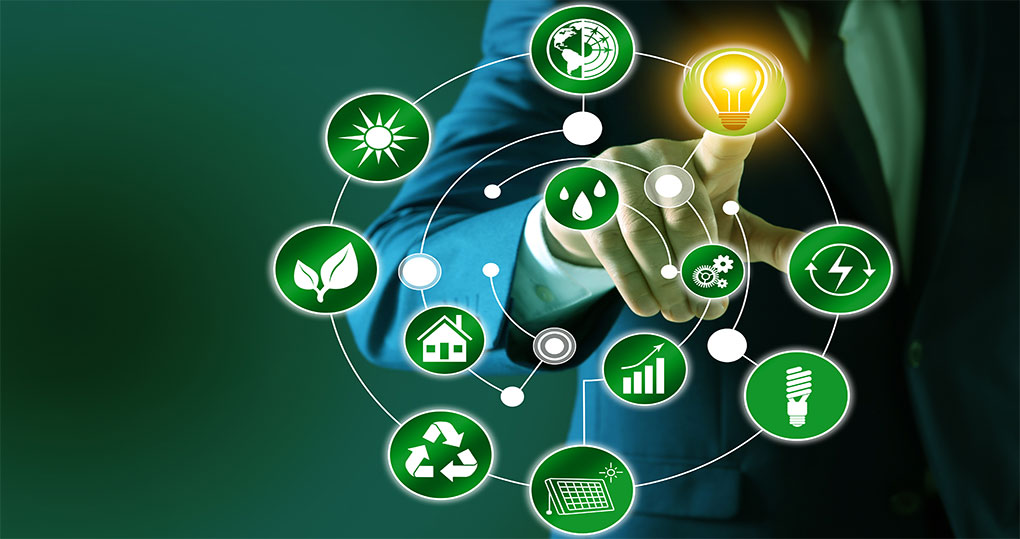
カーボンニュートラル
脱炭素経営は「企業の要諦」~ 3ステップで製造業の脱炭素化に取り組む!
なぜ製造業で脱炭素社会なのか? その大きな意義と課題
2015年の温室効果ガス削減に関する会議「国連気候変動枠組条約第21回締約国会議(通称COP21)」で採択された「パリ条約」以降、世界中で脱炭素への歩みが進んでいます。脱炭素とは、地球温暖化の主原因とされている二酸化炭素(以下、CO2) 、メタン、一酸化炭素、フロンガスなどの温室効果ガスの排出を実質的にゼロにした状態のことで、それを実現した社会が、脱炭素社会です。
日本では、温室効果ガスの排出量を2030年度までに46%(2013年度比)減らし、2050年に実質ゼロにするという目標を掲げています。現在、岸田政権は「気候変動問題は、新しい資本主義の実現で克服すべき最大の課題」とし、脱炭素で経済成長を目指す「クリーンエネルギー戦略」により、経済成長につなげようとしています。
しかし、環境省による2020年度(令和2年度)の温室効果ガスの速報値を見る限り(https://www.env.go.jp/press/files/jp/117187.pdf)、排出量は11億4900 万トン(CO2換算)で、前年より5.1%減ったものの、まだ脱炭素化の道のりは遠いようです。いま温室効果ガスで最も温暖化に影響を与えているのは、CO2と言われています。2020年度における、日本のCO2排出量は、産業部門(工場など)の割合が高いことがわかります。
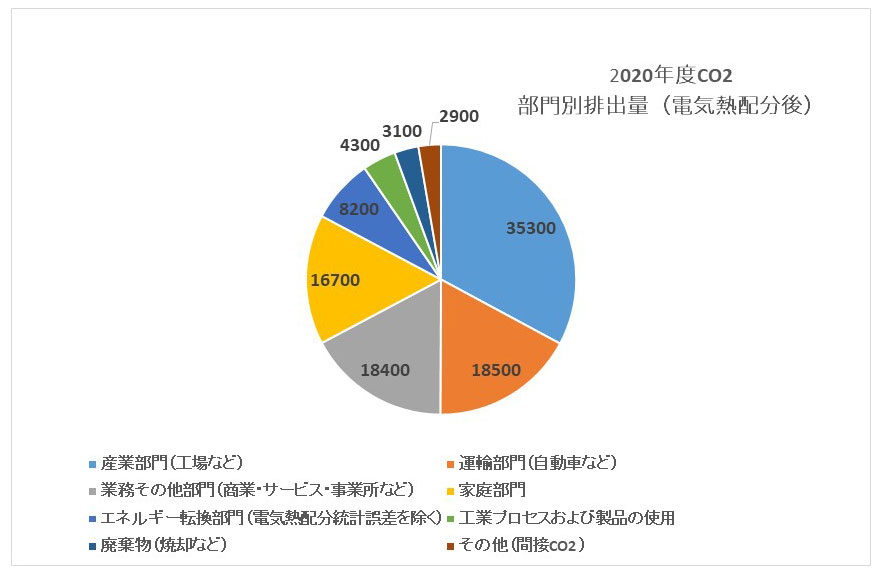
「2020 年度(令和 2 年度)の温室効果ガス排出量(速報値1)」(環境省)
(https://www.env.go.jp/press/files/jp/117187.pdf)を加工して作成
具体的には、産業部門は3億5300万トンで、全体のトップで33.8%を占めています。次に運輸部門(自動車など)が1億8500万トン、ほぼ同量で業務その他部門(商業・サービス・事業所など)が1億8400万トン、家庭部門が1億6700万トンと続きます。そこで、産業部門、特に製造業(工場など)のCO2削減が喫緊の課題になっているわけです。
いま製造業が脱炭素に取り組むメリットとデメリットとは?
では、製造業が脱炭素化に取り組むメリットとデメリットとは何でしょうか? 気候変動を解決し、地球環境を守ることが大前提の話ですが、メーカーにとって直接的なメリットもあります。省エネの取り組みによって、電気・熱や燃料のエネルギーコストが削減される点です。
一方で、デメリットもあります。目標達成のために具体的な数値を掲げても、そのハードルが高く、燃料転換や新たな設備更新などにかなりコストが掛かることです。ただし、日本では脱炭素を進めようとする企業に対して、政府が様々な支援策を用意しています。
代表的な施策として、環境省では、令和3年度から令和7年度まで「工場・事業場における先導的な脱炭素化取組推進事業」(SHIFT事業)を推進しており、企業にかかるコスト負担の軽減策を打ち出しています。条件付きで脱炭素化の計画策定に掛かるコストの1/2、上限100万円の補助や、設備更新費用を最大1/3まで(上限1億円あるいは5億円)補助してもらえます。(詳しくはこちら)
いずれにしても、「脱炭素経営」は世界的な潮流であり、ゲームチェンジの中で日本企業が勝ち抜くために重要なファクターになりそうです。脱炭素を実現するには、経営者のスタンスや事業構造の転換、ステークホルダーとの関係などに配慮しながら、長期的なスタンスでバランスのよい現実解を導き出す必要があります。
クリーンエネルギー使用と製造工程の見直しは、見える化・分かる化・最適化で!
こ製造業が脱炭素化を実現するには、どのような方策があるのでしょうか? 製造業では、主に次のアプローチが考えられます。
【1】再生可能エネルギーへの切り替え
【2】製造工程の見直し
【3】協力会社などからの間接的なCO2排出改善
【4】消費される製品自体の脱炭素化
鉄製造業は、モノづくりのプロセスにおいて、石油・石炭などの化石燃料から作られた熱や電気エネルギーで、各種機械を稼働させています。これらのエネルギーをクリーンなものにすれば、即効性があります。そこで、太陽光・水力・風力・バイオマス・地熱といった【1】の再生可能エネルギーへ切り替えるという方法が挙げられます。ただし、まだ代替エネルギーとして、発電コストが高いという課題は残っています。とはいえ、これからは自社再エネや再エネ調達まで、再エネ発電事業者と再エネを必要とする需要家や、再エネを流通販売する電力事業者が協力して、脱炭素化に貢献することが重要になるでしょう。
次に、【2】のように製造工程の既存設備を見直すことは、比較的取りかかりやすいアプローチといえるでしょう。ここで重要な点は、もともと製造業は電気だけではなく、高温を使う熱利用の製造工程が多くあるという点です。これは省エネにおいて意外と見落とされがちですが、実は非常に重要な視点になります。
例えば、工場の製造工程で、ボイラや工業炉などには化石燃料が使われます。製造時に熱効率のよいボイラ設備を導入したり、排熱・排水、コンプレッサの冷却水などの低温熱をヒートポンプで回収して高温熱に変えたり、IoTセンサを駆使した「FEMS」(Factory Energy Management System)でエネルギーを可視化すれば省エネを推進できます。
いずれにしても省エネの実現には、日常的・継続的に少しずつ改善を積み上げていく基盤が重要になります。FEMSを利用し、「見える化」「分かる化」「最適化」というステップで進めると、非常に効果的でしょう。
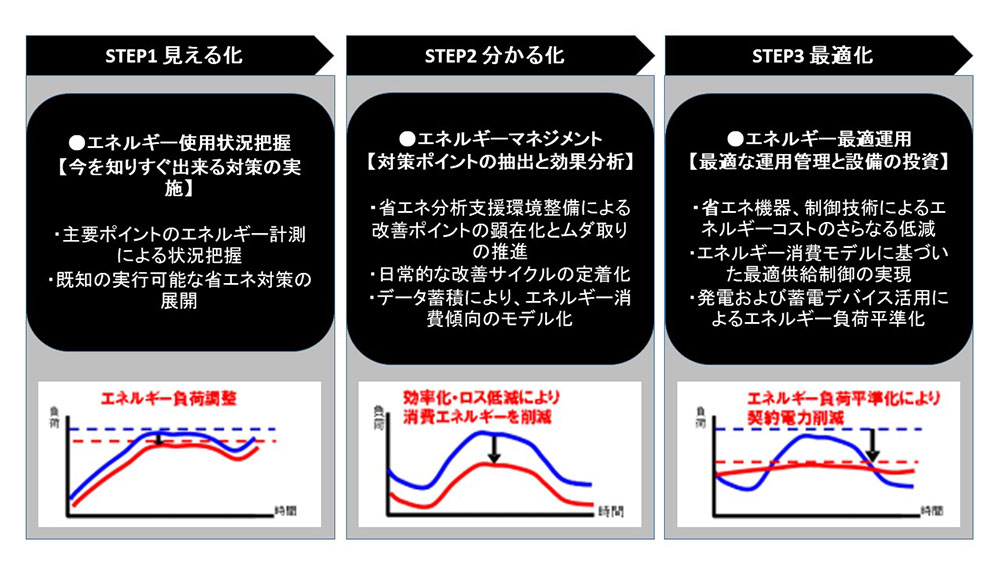
STEP1の「見える化」により、エネルギー状況を俯瞰して、すぐに可能な対策を打ちます。STEP2では、エネルギー管理による対策ポイントの抽出と効果分析で「分かる化」を進めます。その上で、エネルギーの運用・管理や設備投資のSTEP3の「最適化」を図るというステップを踏むことが大切です。
脱炭素化を目指す製造業は、サプライチェーン全体の見直しも重要!
【3】の協力会社などからの間接的なCO2排出改善については、サプライチェーン全体にわたる見直しになります。当然のことですが、大企業が排出量の大目標を設定すれば、そこに連なるサプライヤーも、排出改善に足並みを揃えながら協力していくことになります。大企業のみならず、中堅・中小企業も含めた取り組みが求められるわけです。
サプライチェーンの排出量については、下記のような「Scope」という概念があります。
Scope1:燃料の燃焼、工業プロセスなど、事業者らによる温室効果ガスの直接排出
Scope2:他社から供給された電気、熱、蒸気の使用に伴う間接排出
Scope3 : Scope1、Scope2以外の間接排出で、事業者の活動に関連する他社の排出(原材料、燃料、エネルギー、輸送・配送などの上流側の排出や、製品使用、輸送・配送、廃棄処理といった下流側の排出など)。
したがって、サプライチェーン全体の排出量を削減するには、Scope1からScope3までの排出量を点検する必要があるわけです。
冒頭で触れたように、運輸部門や業務その他部門、家庭部門でも、かなりCO2が排出されています。製造のための原材料や部品調達、完成品を運ぶ際にも輸送手段が必須ですが、自動車、航空機、船舶を動かすにはガソリンや軽油が燃料として使われています。
そこで、【4】の自社製品が流通する際に、CO2が排出されない製品を世に送り出すことも意識する必要があります。前例でいえば、世界で熾烈な開発が行われているEVが、まさに代表的な製品でしょう。特に自動車に関しては、国内でも2035年までに新車販売をEV、HEV(ハイブリッド)、PHEV(プラグインハイブリッド)、FCV(燃料電池車)にすることが国の方針です。
トヨタ自動車は、明確な脱炭素戦略を打ち出し、脱炭素経営でも業界をリードしています。日本を代表するモノづくりメーカーが本腰を入れ始めたことからも理解できるように、これからの製造業の脱炭素化は、「経営の要諦」になるでしょう。モノづくりの将来に向けて、いまのうちに優れたソリューションを検討してみてはいかがでしょうか。富士電機では、製造業が脱炭素の課題を解決できるような数多くのソリューションをご用意しています。