富士電機製品コラム
予知保全・予兆保全とは?保全の種類や違い、事例を解説
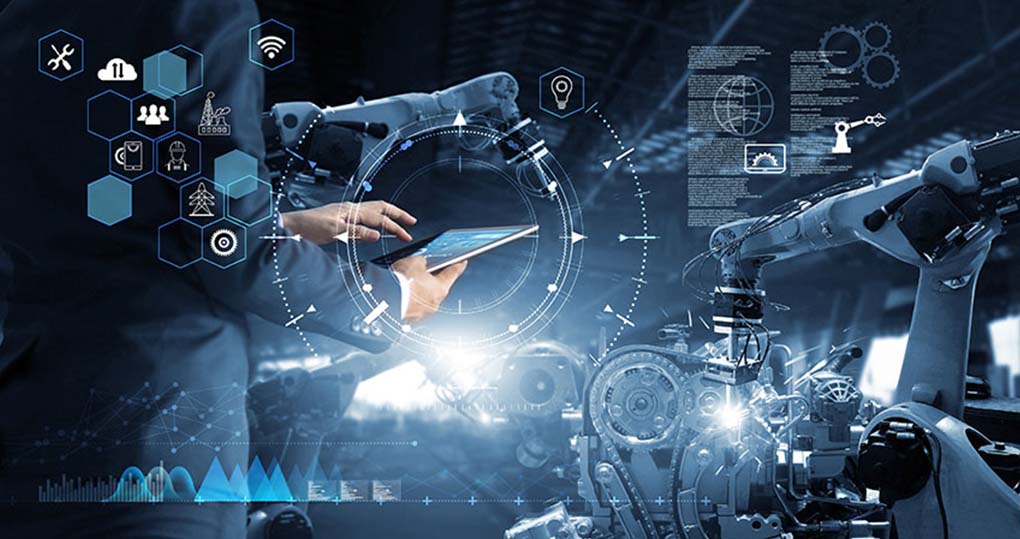
予知保全・予兆保全とは?保全の種類や違い、事例を解説
設備を稼働させることは、企業活動そのものといえます。設備を安定して稼働させるためには、設備や機器の保全行為は必須です。
いままでの保全行為は、製造現場で使われる設備や機器が故障した際に、修理や部品交換を行う「事後保全」。予め立てたスケジュールに沿って、部品交換やメンテナンスを行う「予防保全」が主流でした。しかしIoTの概念が浸透するにつれ、製造ラインの稼働率をより高く維持することができる「予知保全」に注目が集まっています。
この記事では、混同されがちな「予知保全」「予防保全」、それに「事後保全」の概要やそれぞれの違いをご紹介したいと思います。
保全方法の種類と比較
設備稼働や維持に欠かせない保全には、予知保全・予防保全・事後保全があることは前段で述べました。このパートでは、各保全の違いについてご説明したいと思います。
事後保全
事後保全は読んで字のごとく、故障や不具合が生じてから行為を開始する保全行為です。この保全は、故障や不具合が発生するまで保全行為を行わないので、どうしても突発的な対応となってしまいます。
そのため、計画的にスケジュールを立てることができません。事後保全だけに頼っていると、生産設備の稼働率を高く維持することは難しいといえます。
予防保全
故障や不具合が発生してから保全行為を行う事後保全は、いわばトラブルを引き金(トリガー)とします。この事後保全を改善するために、「時間」をトリガーポイントとしたのが予防保全です。
日常点検や3ヶ月・半年・1年定期点検などがこれに該当する訳ですが、定期的にメンテナンスや部品交換を行うことで、重大な事故を未然に防ぐことができます。
保全行為の目安については、一定期間で行為を行う「時間基準保全」と、使用している部品の劣化具合に応じて対応する「状態基準保全」の2つのパターンがあります。
予防保全は、時間を基軸に保全を行う「時間基準保全」なので、計画や見通しが立てやすいのがメリット。その反面、まだ使用可能な部品を交換してしまったり、不必要に過剰な回数の点検を行うことに繋がりかねません。何より想定しているタイムテーブルが正しいか否か?の見極めが難しいといえます。
事後保全と予防保全の違い
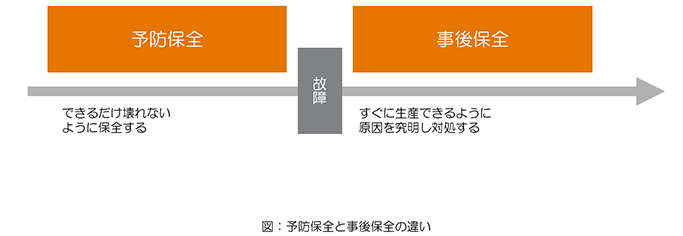
出典:予防保全とは?事後・予知保全との違い、メリット、IoT活用による効果を解説(富士フィルムビジネスイノベーション株式会社)
予知保全
予知保全は、生産現場の設備状況を常に監視しつつ、対象機器の不具合の兆候を察知し、故障が発生するのを防ぐ「状態基準保全」の考え方です。予防保全よりも、保全担当者の作業工数や部品交換を減らすことが出来、より生産現場の稼働率を上げることができます。
予知保全は、機器の不具合をトリガーとするため、別名「予兆保全」とも言います。この保全行為は、不具合の兆候が起点となるため、保全のタイミングや回数などにロスが出にくいのが特徴です。
予防保全と予知保全の違い
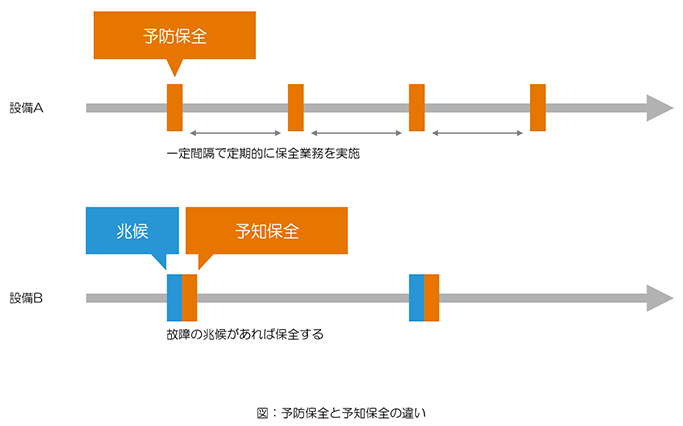
出典:予防保全とは?事後・予知保全との違い、メリット、IoT活用による効果を解説(富士フィルムビジネスイノベーション株式会社)
各保全の種類とトリガー・メリット・デメリット
事後保全から予防保全そして予知保全に
製造業は、設備を利用してつくった製品を、市場に提供することを生業としています。冒頭でも述べた通り、製造業者が生産活動を続けていくには、「設備の機能を一定水準以上で維持」しなければなりません。
これを可能にするのが“保全行為”であり、製造業者は保全を通じてロスとリスクを可能な限り抑え、利害関係者であるステークホルダーに貢献します。
つまり生産設備が健全であることが、経営の永続につながる訳ですが、トラブルが生じてから対処する事後保全だけでは、稼働率の維持は望めません。
そこで今までは、定期的にメンテナンスや部品交換などを行う予防保全を行い、生産設備の稼働率を維持してきた訳です。
IoTの活用により予知保全が可能に
しかし予防保全は、まだ使える部品を交換することになる、「オーバーメンテナンス」と呼ばれるデメリットも孕んでいます。そこで近年、新たな保全方法として導入が進んでいるのが予知保全です。
予知保全は上記でも記述したように、機器や設備の不具合を予防するのではなく、予知してトラブルを防ぐ行為。この予知に大きく絡むのが、モノのインターネットとも呼ばれるIoTです。
IoTを工場の生産ラインで稼働している機器に導入すると、各機器に取り付けられた複数のセンサから得た稼働時間・温度・振動などのデータを、ネットワークを通じて一元化出来ます。
これら収集したデータを分析すれば、機器の稼働状況をリアルタイムで把握したり、過去の傾向からトラブル発生の時期を予知することができるようになります。以下に、保全行為にIoTを活用したメリットをご紹介します。
熟練工に頼っていた「勘やコツ」から脱却できる
従来は保全行為を開始するタイミングは、どうしても熟練工の勘やコツに頼りがちでした。しかしIoTを導入すれば、各種センサで得た情報を数値化できるようになります。これらのデータを蓄積していけば、定量的な判断が可能となり、保全行為の属人化を廃止できます。また保全に対する知識と技術の伝承も、容易になります。
保全データの集計や分析を高速化することができる
設備の状態管理を紙で記録していると、集計や分析に多大な時間や労力が必要です。IoTでは、すべてのデータはデジタル化。今までマンパワーに頼りがちだった、集計や分析が早く行えるようになります。これにより、保全行為の工数を大幅に軽減出来ます。
古い機器や設備の予知保全も可能になる
レガシー設備と呼ばれる、古い機器や設備。このような機械は、IoTに対応していません。しかし例えレガシー設備であったとしても、カメラやセンサを後付けすれば状態監視を行えるようになります。IoTを導入すれば、いままで人数を割いていた見回りをやめ、少人数による生産ラインの保全が可能となります。
機器や設備のトラブルをいち早く察知することができる
従来の保全行為は、生産ラインを作業員が自身の目と耳を使って見回っていました。しかしIoTを導入するにあたり、保全行為を起こす「しきい(閾)値」を予め決めてさえいれば、アラートを出すだけですぐに機器類の異常を検知できるようになります。
設備を止めたくなければ「予知保全」の導入を
このように、生産ラインにIoTを導入すれば、トラブルの予兆をデータで把握できるようになります。その結果、予知保全を実施することが可能となります。
保全行為にIoTを活用すれば、今まで以上に効率的・効果的に保全行為を行えます。生産現場により安定した稼働率をもたらしたいのであれば、IoTの導入による、予知保全の実現は必須です。
高い稼働率を維持してこそ、生産現場は高い品質の製品を生み出すことができるのです。
富士電機の予知保全システム事例
富士電機は、IoTを活用した予知保全システムをリリースしています。ここでは、弊社の予知保全システムの一部をご紹介します。
生産設備の異常検知を解消
データ設備と見える化で生産性を向上させることを達成!
生産設備のあらゆる情報をワンパッケージ化するOnePackEdge
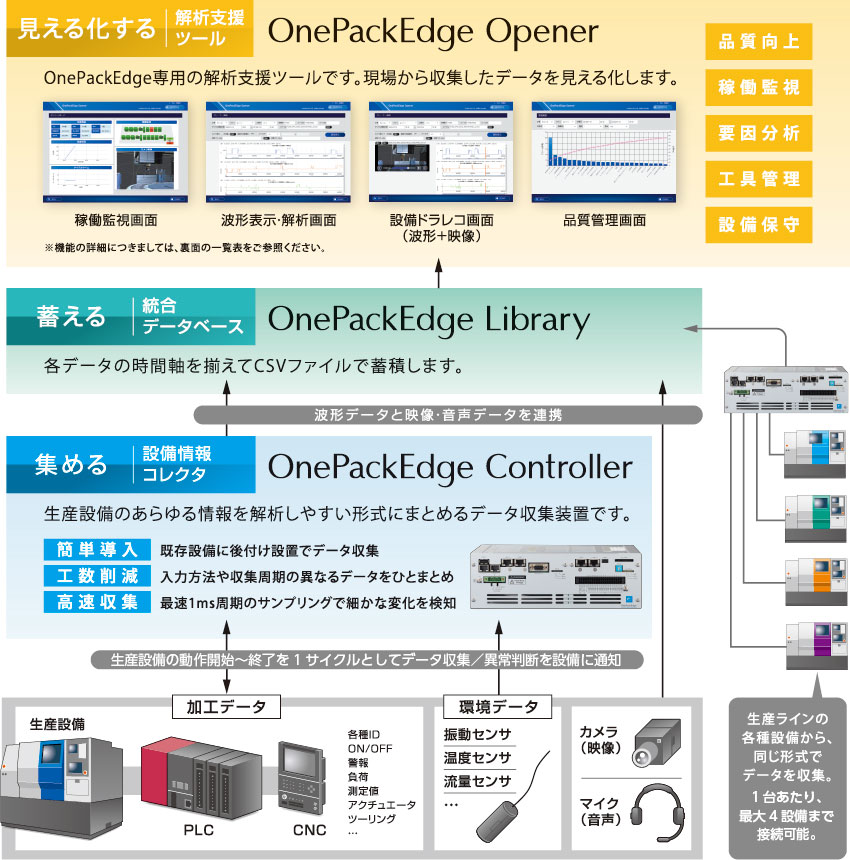
本製品は国内の大手自動車メーカである日産自動車・栃木工場のエンジン部品生産ラインにおいて、予知保全・生産性向上に貢献しています。お客様が抱えておられた様々な課題や導入後の改善効果をお伺いしたインタビュー動画・記事を公開しておりますので、下記リンクからぜひご覧ください。
納入先:日産自動車株式会社 栃木工場様
対象:エンジン部品生産ライン
切削加工機の工具保全最適化
切削加工機の加工状態を簡単に「見える化&診断」できる
OnePackEdge MARSYS
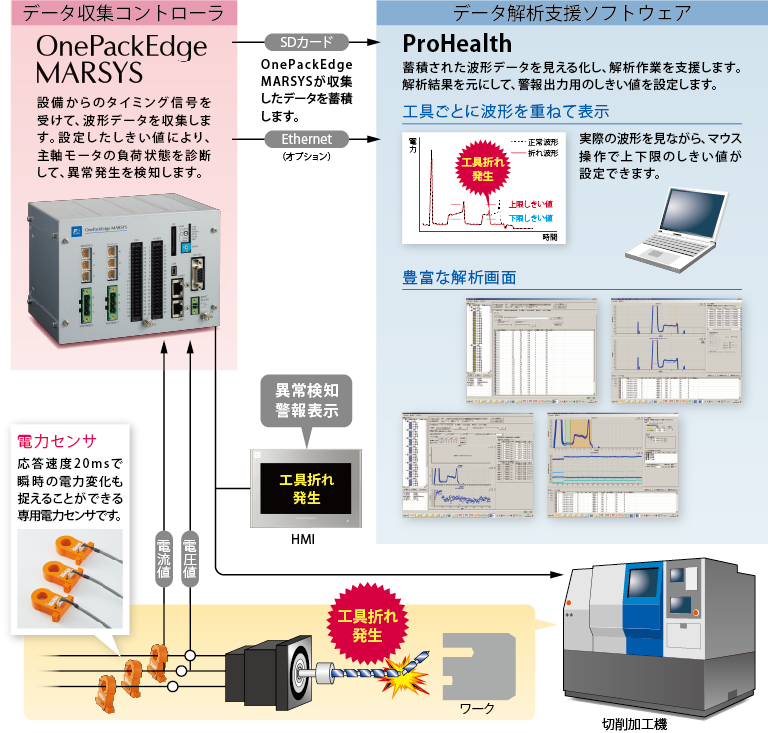
プレス機のかす上がり検知
板金部品のプレス工程で発生する品質不良を改善
SignAiEdge × 診断センサHUB
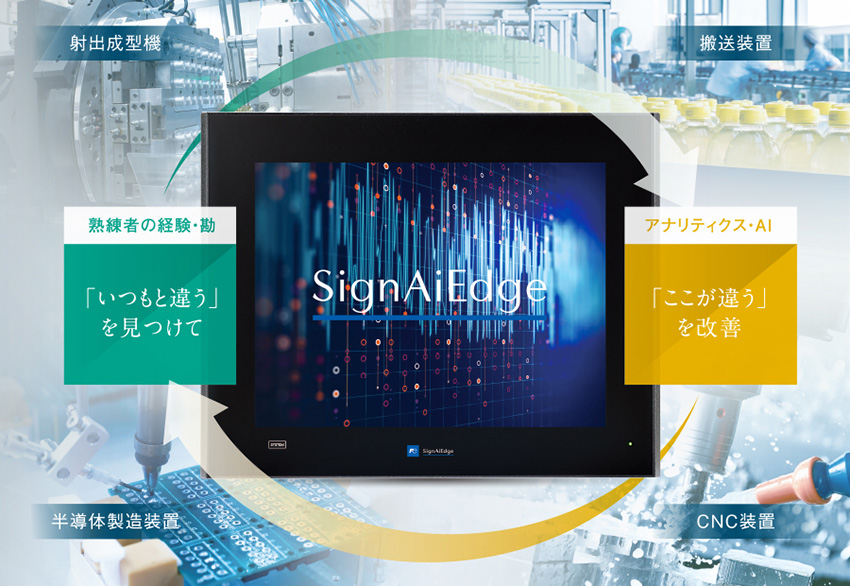
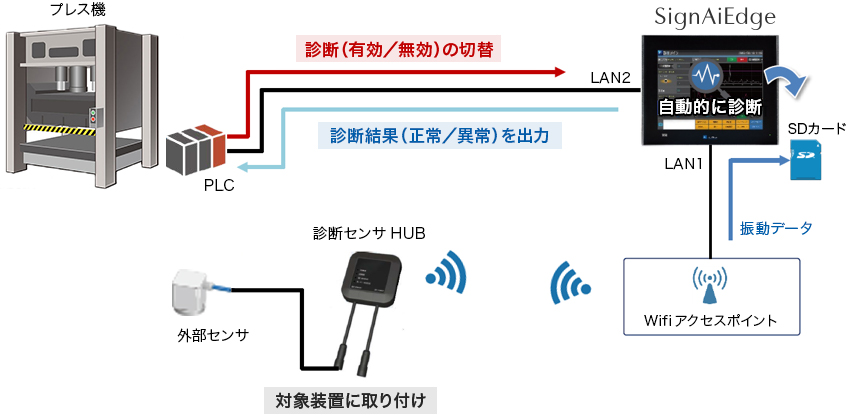
まとめ
機器や設備をIoT化するための技術や設備、それらを導入する費用やデータ解析のノウハウなど。予防保全のデメリットを補うことのできる予知保全ですが、その導入にはいくつか課題も存在します。
IoTを活用した予知保全は、マンパワーを要する紙での記録管理や熟練工の勘とコツに頼った保全行為からお客さまを開放します。そこから生じるリスクの軽減は、自社ビジネスに変革をもたらし、競合に対する高い優位性をもたらす可能性があります。
富士電機は、お客さまの予知保全の導入に、現地調査・機器導入・システム構築まで幅広く対応いたします。