富士電機製品コラム
予知保全システムの導入とその課題解決について
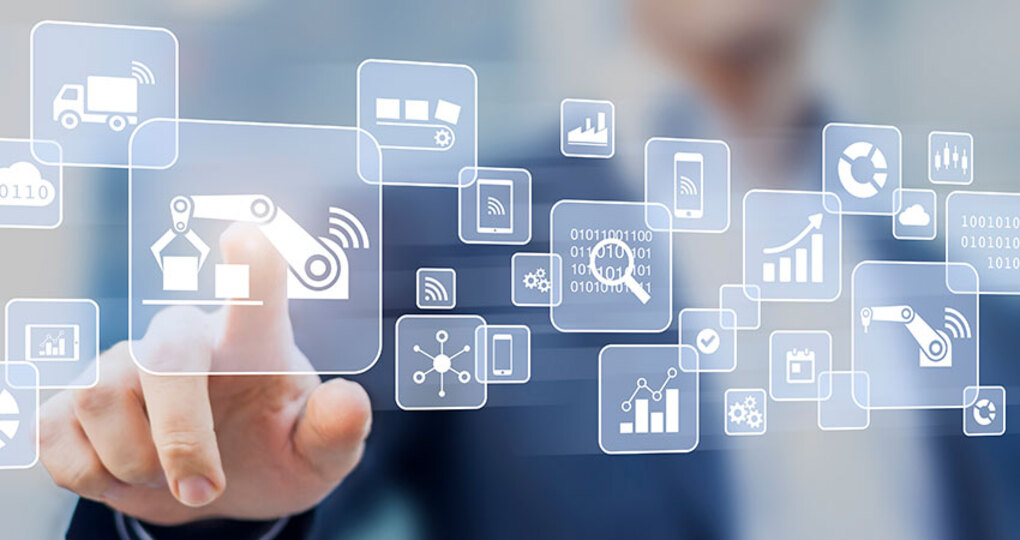
予知保全システムの導入とその課題解決について
機器類の経年劣化や故障が発生すると、工場などの製造ラインはストップしてしまいます。製造業において、生産は企業活動そのものですから、このような事態は避けなければなりません。
そこで昨今製造業において、生産機器や設備で起こるトラブルを回避するため、IoTに基づく予知保全システムの導入が進みつつあります。
予知保全のシステムを構築するためには、対象となる機器に設置する「各種センサ」、データ収集のための「エッジコントローラ」、データ分析をするための「ソフトウエア」などが必要になります。
このコラムでは、製造業の方々が予知保全システムを導入するにあたり、障壁となりうる課題とそれに対処する方法をご紹介いたします。
予知保全のシステム構築における4つの課題
工場における機器類のメンテナンス行為は、まだまだ熟練工の経験や、そこから得られた勘に頼った対応が多く見受けられます。しかし熟練工の高齢化や世代交代・技術伝承の難しさ、定期的なメンテナンス(=予防保全)のコスト高の問題など、最適な保全の実施には改善の余地が数多くあるといえるでしょう。
このような問題を解決するのが、事前に機器類の不具合を察知できる「予知保全」になるのですが、導入にあたって課題が無いわけではありません。以下に予知保全システムを導入する際に生じる、代表的な4つの課題をご紹介します。
課題1 予知保全システム構築のためのデータが不足している
機器や設備のトラブルを予知するにあたり、多くの場合、機械学習アルゴリズムが利用されます。アルゴリズムの構築には、多くのデータが必要になるのですが…。
-
データの収集自体を行っていない
-
収集の期間が短く、データ量が十分でない
-
センサの取り付け位置が悪く、データ収集がうまく行かない
このように、予知保全システムを構築するために必要なデータ量を確保できていないという課題が生じます。このデータ不足は、予知保全システム導入時に起こる、最も一般的な課題といえるかもしれません。
課題2 故障に繋がるデータがない
課題1では、データ量が不足していることをご紹介しましたが、逆にデータ量が確保できていれば良いのか?と問われると、必ずしもそうは言えません。
-
収集したデータに故障に結びつくものがない
-
データ収集期間中に、故障が発生することがなかった
-
収集したデータと故障の因果関係が分からない
このようにせっかくデータを収集しても、故障に結びつくデータが得られなかったり、データから故障の予兆を得ることができないケースもあります。これも、予知保全システムの導入ではよく見られる課題です。
課題3 故障は発見できるが予測ができない
製造ラインを維持する上で、故障原因の追究は重要です。しかし故障の原因を特定することと、故障の予測ができるということには、大きな乖離があります。
すでに生じてしまった故障やトラブルの原因を究明することは、故障箇所を事後的に確認することで調査できるのに対し、故障の予測は故障に至るまでのメカニズムを理解した上で、しきい値を決定するという異なったロジックが必要です。
課題4 予知保全システム導入への費用対効果の実証が難しい
どの仕組みにもいえることですが、新たなシステムを導入するにあたり、投資に対する根拠・正当性の検証は必須です。投資に対する費用対効果の実証にかかる時間は、短ければ短いほど財務面での理解を得られやすいと言えます。
中でも予知保全の場合は、「システムを導入して稼働させてみなければ、効果が分からない」という性質を持つため、特に事前の投資対効果の検証が難しいといえるかもしれません。
このような財務面での課題は、他の課題に比べ経営陣や経理部門・他部署との調整も必要なことから、技術的な問題よりも解決することが難しいと言えます。
その他の検討事項
生産現場においては、稼働設備に関する日次報告が必要とされる場合や、リアルタイムでの処理が必要な場合もあります。自社の設備に必要とされる監視の頻度について、今一度見直してみましょう。
また、収集するデータ型 (信号・画像・テキスト・データ)に加えてそれらが故障の予測に役立つかどうかも十分に検討してみる必要があります。
大量のデータを扱うには、十分な計算処理能力も必要です。その他、予測結果をどのように表示するべきか、警告が出された理由についてどの程度の情報量が必要か、そして誰がこれらの通知を受け取るべきかを検討する必要もあるでしょう。
予知保全システム構築の課題を解決するには?
このように予知保全システムの導入には…
-
十分な量のデータがない
-
十分な量の故障データがない
-
故障は発見できるが予測ができない
-
費用対効果の理解を得るのが難しい
という4つの課題を乗り越える必要があります。
富士電機はデータ解析やアルゴリズム開発、シミュレーションモデル作成などにも対応する重電企業です。弊社は、予知保全導入で、お客さまが直面しやすいこの4つの課題を解決し、予知保全システムを早期に実現、導入するお手伝いをいたします。
富士電機の予知保全システムと導入事例
MSPC:Multivariate Statistical Process Control(多変量統計的プロセス管理)
当社では、MSPC(Multivariate Statistical Process Control:多変量統計的プロセス管理)という統計的解析手法を用いて、お客様の生産設備の「いつもと違う」状態を検知する予知保全システムをご提供しています。
多変量解析ツールであれば故障時のデータ収集は必要ない
そもそも生産設備に、故障はあってはならないもの。そのため、故障に繋がるデータを収集すること自体が難しいと言えます。
正常な生産時データを使って、予知保全システムを構築できる
弊社のリリースするMSPCであれば、例え故障時のデータがなくても、予知保全システムを構築することが可能です。
多変量解析ツールMSPCは、製品が正常に作られた際のデータを収集し、基礎となる正常モデルを構築。この正常モデルと、日々収集されるデータとの比較により、機器の異常を事前に検出します。
MSPC導入フロー Small, Quick Start
解析ツール活用により、システム導入後の効果を早期に検証することができます。
■ 既存データがある ⇒ オフライン解析により最短1日で簡易診断が可能。
■ 既存データがない ⇒ エッジコントローラの後付で容易にデータ収集可能。
富士電機では、既存データがない場合でも簡単にデータ収集ができるエッジコントローラも取り揃えています。
< 富士電機のデータ収集型エッジコントローラ >
弊社はMSPC導入による効果を、お客さまと一緒に確認しつつ、解析内容の深堀り・オンライン解析システム構築の運用・維持・拡張まで対応します。
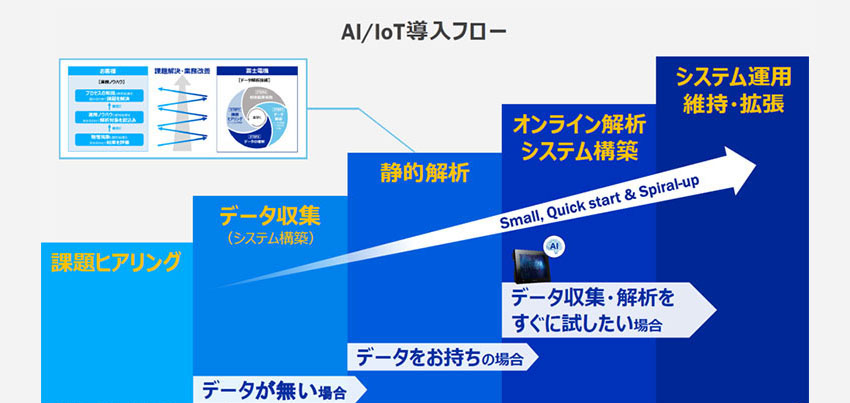

出典:富士電機Webセミナー「お客様と共に創り上げるAI/IoTとは?現場環境・ニーズに合わせたAI/IoT導入と現場改善への道筋をご紹介!」より
MSPCの特徴
お客様との課題解決により、磨き上げられた解析アルゴリズム
-
因子数(注)の制約なしに、因子間の特徴抽出が可能
-
未知の異常でも検知可能
-
連続系プロセスに加え、バッチ系プロセスデータの解析も可能
バッチMSPCによる解析
バッチ系プロセスでは平均プロファイルからの差異を因子間で相関分析することにより診断・分析します。
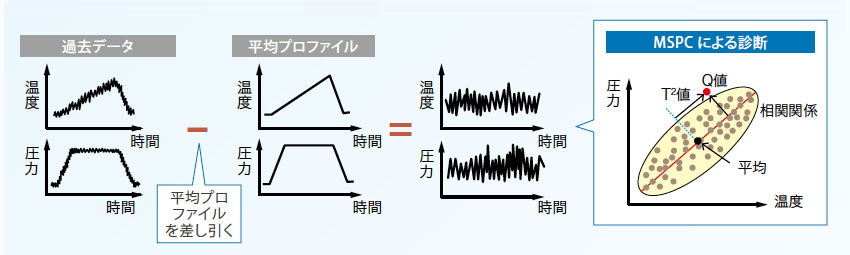
-
(注)
-
因子数:製造実績データ、設備稼働実績データ、検査結果データなどの各項目の数
MSPCの導入事例
射出成形機におけるスクリュー交換時期の検知
■ 射出成形機のデータをMSPCで解析することで、スクリューの摩耗状態を検知。
■ スクリュー交換時期の特定が可能となり、製品不良率の低減や点検作業の効率化に貢献。
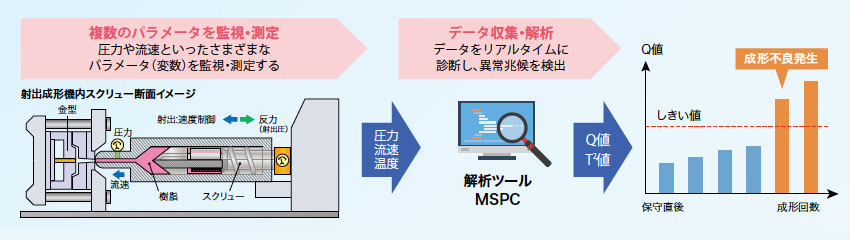
MSPCを搭載したパッケージソフトウェアとして、約550件の導入実績があります。
適用事例 業界別
上記以外の業界にも、多数の導入実績があります。
予知保全システム導入の財務面における解決方法
予知保全システムに興味はあるものの、
「導入効果が分からず、大規模な投資に踏み切れない」
「導入予定の製品が費用対効果に見合うか判断できない」
というお客さまもいらっしゃるかと思います。
このような財務面の課題を解決するにあたっては、PoC(Proof of Conceptの略で、「概念実証」という意味)という考えがお役に立つかもしれません。
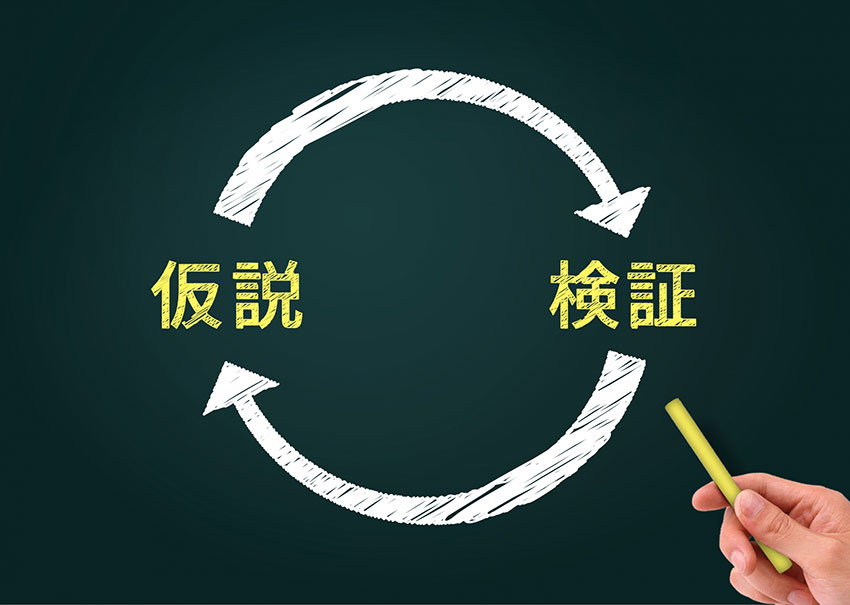
PoCは、無償・有償のスモールモデルをテスト的に導入し、導入効果を確認してから大きく展開していくという検証工程です。
まずは生産ラインの中でターゲットを絞って、予知保全システムの取り組みを始め、大規模に展開しても効果が得られると分かった時点で、工場全体の導入を進めると良いのではないでしょうか。
予知保全システム導入に国や地方自治体の補助金や助成金を利用してみる
また昨今は、予知保全のような新たなシステム導入に際し、IT補助金を始め公的な各種補助事業や助成制度も利用できるようになってきました。可能であれば、このような公的な援助も利用してみるのも良いかもしれません。
まとめ
富士電機は、様々な分野で培った豊富な開発実績を生かしてIoTデバイス開発から、収集したデータの蓄積・可視化・分析等のアプリケーション開発まで、お客さまの課題解決を支援します。
IoTに限らず生産現場における設備導入時には、財務面の問題は必ずといって良いほど起ります。弊社は重電メーカーとして過去、何度もこのような生産設備に絡む大規模なインフラ導入を行った実績をもっています。
富士電機では予知保全システムの提供のみならず、導入障壁となる財務面の問題を解決するPoCもサポート。PoC導入前のロードマップ作成から、費用対効果の実証に関しても、お客さまと一緒になって進めてまいります。予知保全システムの導入に関することなら、どんな些細なことでもご相談ください。