サステナビリティ
生産時CO2排出削減 - SDGs貢献事例
地道な取り組みで地球温暖化防止に貢献
富士電機の生産拠点では、生産に伴う電力使用量を削減することで地球温暖化防止に貢献すべく、省エネ活動に全力で取り組んでいます。平成29年度、電力の有効利用の推進や負荷率改善等、電気使用の合理化に顕著な成果を収めたエネルギー管理優良事業者に贈られる中部経済産業局長表彰を受賞した鈴鹿工場の事例を通して、その取り組みを紹介します。
全従業員参加による省エネ活動の取り組み
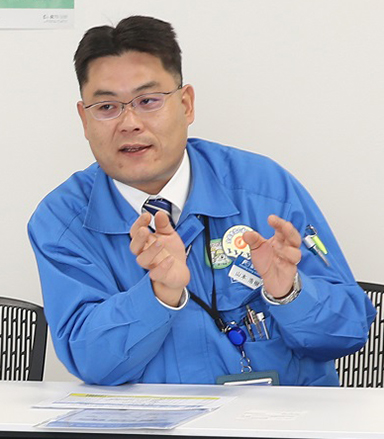
三重県にある富士電機鈴鹿工場は、パワーエレクトロニクス製品のグローバルマザー工場である。近年、効率化を目的としたパワエレ製品の生産集約により、エネルギー使用量が大幅に増加していた。そのため、大幅な消費電力の削減が鈴鹿工場の重要課題となっていた。
この課題に責任者として真正面から取り組んだのが、環境施設課長の山本浩樹だ。山本は2014年に活動を開始し、2015年には工場横断型の省エネ部会を立ち上げた。山本はその理由をこう語る。
「工場全体の省エネ活動とするためです。各部門に省エネ責任者を任命し協力してもらうことで、何とか省エネ活動を軌道に乗せることができました。」
具体的には、省エネ部会の事務局が掲示した部門別年度目標を、各部門が月ごとに目標とアクションプランに落とし込む。そして、その内容を毎月開催される省エネ部会において実績を報告、フォローしていくことで継続的に改善していく。
山本は「重要なのは全従業員参加の取り組みにすること」と語る。そのため従業員の省エネへの意識付けに重点を置いて取り組んできた。垂れ幕やポスターを工場の各ポイントに掲示し、省エネ部会の代表者はワッペンをつける。また腕章をつけた係員が省エネパトロールを行うなどして、常日頃から全従業員の省エネ意識を浸透させた。
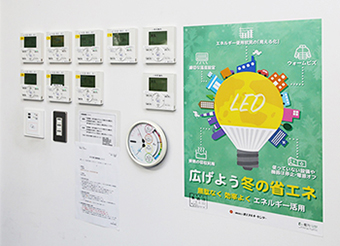
エネルギー使用の見える化で進む省エネ対策
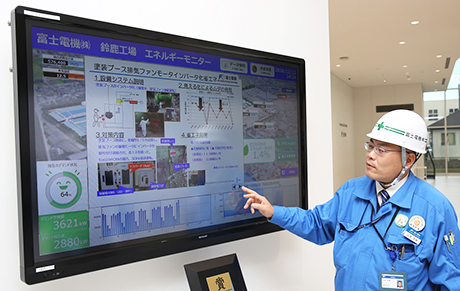
省エネ活動の鍵は、当社システムであるFEMS(工場のエネルギーマネジメントシステム)の導入をベースにした「エネルギーの見える化」だ。
鈴鹿工場の敷地は26万9000平米ほど。東西1km、南北に300mという広大なものだ。以前はエネルギー使用状況をリアルタイムでは把握できず、毎月末に担当者5時間かけてメーターを検針し、手集計で数値を管理していた。これを改善するためFEMS導入による工場のスマート化を実施。各建屋のライン・設備毎の電力使用状況がリアルタイムに一目で分かるデジタルサイネージを用いたエネルギーモニターのシステムを構築した。このモニターは電力使用の積算量を示すほか、1日あたりのキロワットアワーの電力量、円換算での電力料金の表示も可能になっている。
このモニターは契約電力の上限に近づくと、表示バーの色が変わって知らせてくれる。従業員は一目で表示の変化がわかるため、すぐに不要な照明や空調の電源をオフにする対応が出来る。
しかし、見える化は必ずしもこのような大掛かりなものだけではない。エアコンの吹き出し口に垂れているリボンもそうだ。エアコンの風が吹き出しているかどうかが一目で分かり、消し忘れを防ぐのに役立っている。
設備技術センターをもっと地域の人に見てもらいたい
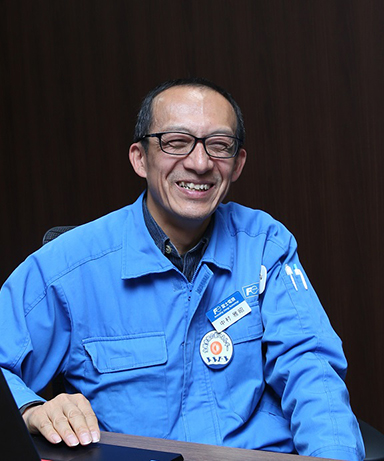
こうしたFEMSによる消費電力の見える化は、設備の更新にも大きく役立っている。
「鈴鹿工場は1968年に操業開始。昨年50周年を迎えた歴史ある工場です。そのため使用電力量が大きい設備も残っていたのですが、どこから手を付けてよいのかがわからず困っていたのです。FEMSのおかげで効率的かつ計画的な設備の更新が可能となりました。」そう語るのは環境施設課主任、中村雅昭。
まずは、巨大な排気ファンが常時稼働していた大型モーター生産ラインの塗装ブース。ここに自社製のインバータを導入したことで、ファンの回転が効率化した。作業者がスプレーガンを、通常引っ掛けているフック(留め金)から外すと、ファンが通常速度(60Hz)で運転する。そしてフックに戻すとファンが低速運転(30Hz)するよう効率化している。有機溶剤などの臭気対策により、フックに戻してから10分間はファンを停止できないが、何もしなければ10分後には自動的に停止(0Hz)する。
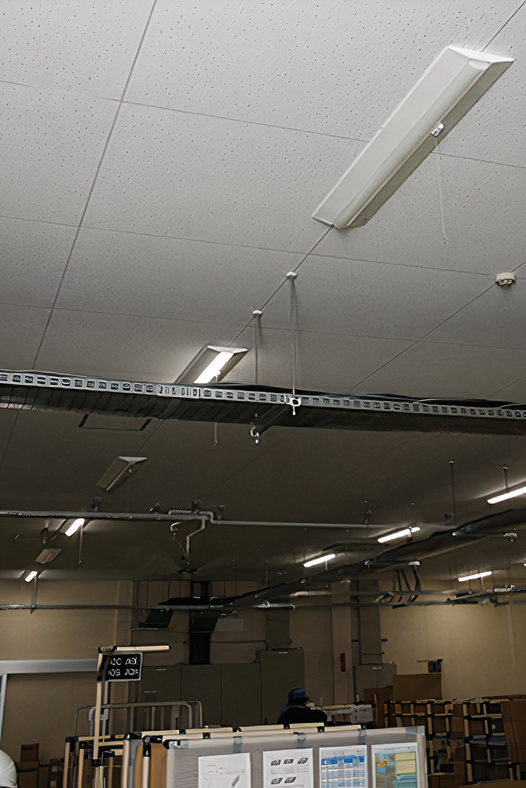
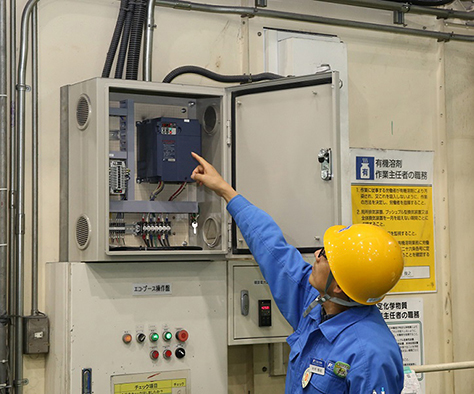
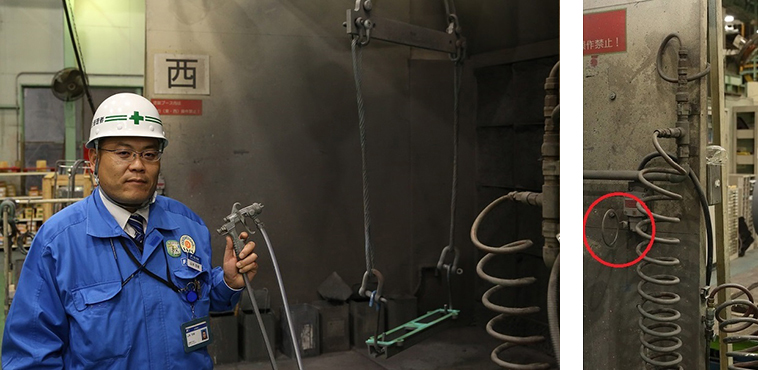
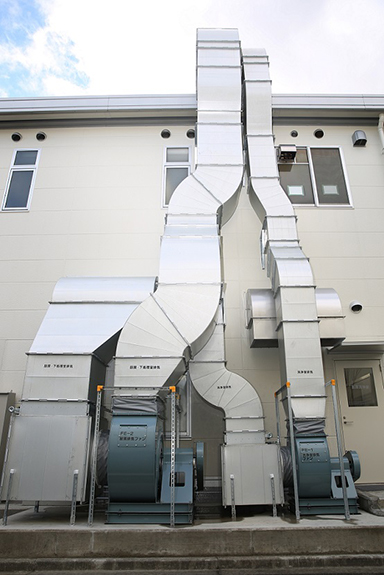
インバータの活躍場所は様々だ。社員食堂の厨房では、朝・昼・夕食の調理時にフル稼働している調理用排気ファンを、60Hz運転から40Hzに制御しファンの回転数を最適値にしている。加えて、省エネを最大化するには工夫も欠かせない。食事の後、食器洗浄時に発生する湯気を排出するためにファンを回す必要があるが、調理時に稼働する排気ダクトとは発生する風量が全く異なるため、同様に稼働させると無駄が生じる。そのため、調理時と洗浄時は排気ダクトを完全に分けた。洗浄用排気ダクトには別途インバータを取り付け、周波数を最適値である55Hzに制御することで、省エネ効果を最大化した。
さらに、他の設備更新で省エネ効果が大きかったのは、地道な活動ではあるが蛍光灯や水銀灯など照明のLED化である。更新の際、照明器具に紐式のスイッチをつけ、照明器具一つひとつを小まめに消灯できるよう工夫した。これで、照明器具自体の使用電力削減に加え、従業員の自主的消灯による省エネ効果も付加された。
このように大掛かりな設備改善から小さな工夫まで、さまざまな努力を重ねることで大幅な省エネルギー化を実現し、結果として鈴鹿工場全体で年間約737,000kWhの省エネ効果をもたらしている。
全従業員参加型の省エネ活動
では、現場で働く従業員はどのような意識で省エネに取り組んでいるのだろうか。省エネ部会に出席している人たちの話を聞いてみよう。
「離席の際の部分消灯の徹底、冷暖房の適正温度の徹底、夜間退勤時の照明・冷暖房の切り忘れ対策の3つを中心に部門で取り組んでいます。離席時の小まめな消灯は不慣れなうちは忘れてしまいがちですが、習慣にしていきます。」
そう語るのは総務部を代表して出席した林明宏。
また、回転機製造課長の櫻井洋史はこう語る。
「建屋の照明を水銀灯からLEDに変えたのですが、省エネ効果はもちろん立ち上がりの早さに現場は驚いています。これまで使っていた水銀灯はスイッチを入れてから明るくなるまで10分から20分かかっていました。水銀灯立上げ時の負荷増を考慮すると、こまめな消灯はやりたくてもできなかったのです。」
工業電熱設計課を代表して出席した松永靖子はこう語る。
「フロアに共有の会議スペースがあるのですが、つい消灯を忘れがちになります。この会議への出席に伴い、節電の意識が高まってきました。日頃から共有スペースを気にかけて消灯を心掛けています。」
鈴鹿工場がまさに全従業員参加で省エネ化に取り組んでいる姿勢が伝わってくる。
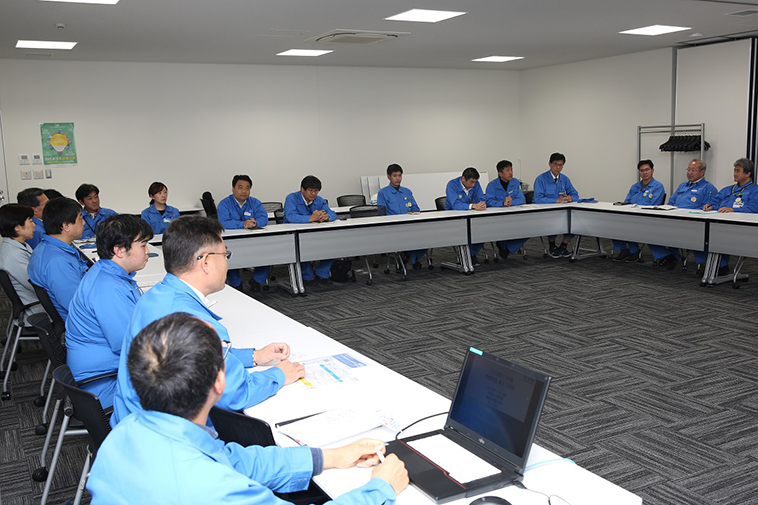
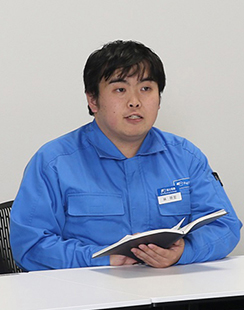
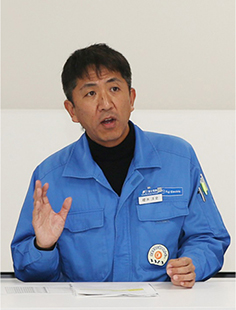
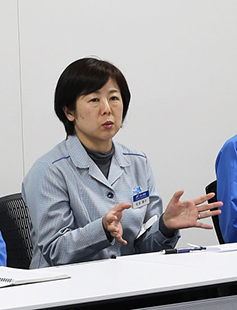
今後さらに強化する省エネ全員活動
このように、設備の更新だけではなく、そこに従業員一人ひとりの地道な取り組みを積み重ねることで、省エネは効果を発揮する。そのことを、鈴鹿工場の従業員はよく理解し実践している。では、これからどのように省エネを進めていくのだろうか。最後に環境施設課長の山本に聞いてみよう。
「省エネ施策は計画的に実行し、その効果ははっきり数字に表れています。しかしこれで満足しているわけではありません。まだまだこれからです。残っている空調・照明の設備更新は、この5年ですべて完了するよう投資計画済みです。私たちが取り組むべき省エネ目標のハードルは決して低くありませんが、省エネ部会のメンバーとも知恵を出し合い全員活動で達成します。」
これからも鈴鹿工場は省エネの取り組みを加速させることで、地球環境保護に貢献していく。