一歩先へ!富士電機の基盤技術
製品開発力強化に向けた、基盤技術を紹介します。
接合・接着技術
自動車の軽量化を背景に新素材の接合技術が求められている
世界的な環境規制を背景に、自動車メーカー各社はCO2 排出量削減に取り組んでおり、燃費性能向上を目的とした「車体の軽量化」が重要な課題の一つとなっています。そのため、近い将来、自動車の車体は超高張力鋼(注)やアルミニウム合金、樹脂などの新たな軽量素材が主流になると見込まれています。現時点でこうした新素材の接合にはレーザー溶接機などの高価な設備を導入する必要があり、量産に適したより安価な接合技術の適用が期待されています。
現在、車体の溶接における主流は「スポット溶接」です。スポット溶接は他の溶接技術と異なり、接合材を用いず部材そのものに電流を流し、接触部分に起こる電気抵抗による発熱で部材の一部分を溶かし、接合します( 図1 )。溶接の良否は部材のもつ機械・電気特性に大きく左右されるため、新しい素材にスポット溶接を用いるには、それぞれの素材に適した溶接条件(通電時間・通電電流)を定める必要がありました。
こうした背景において当社は、新素材に最適な溶接条件を見出す高精度なシミュレーション技術を開発しました。
-
注
-
従前より強度を上げ軽量化した鋼材
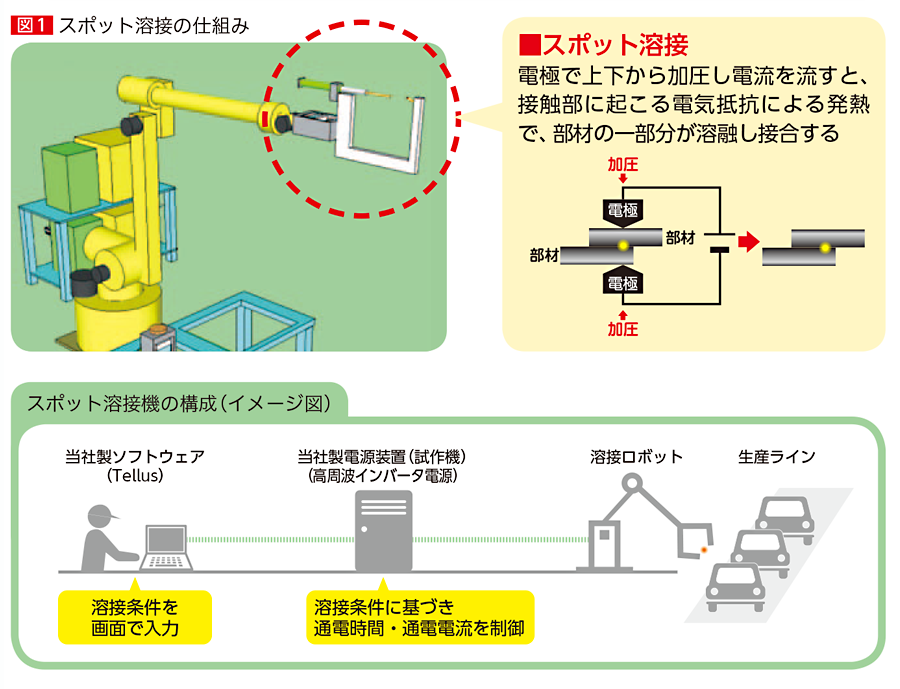
電気抵抗で生じる熱の変化を予測できるシミュレーション技術を開発
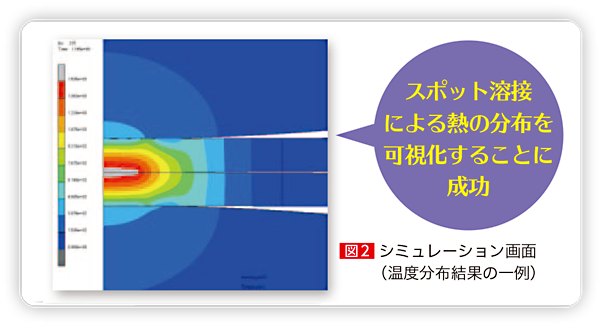
スポット溶接における接触部分の電気抵抗(接触抵抗)は、部材(特に表面)の熱伝導率や面に加わる圧力、電流の大きさなどさまざまな要素に依存し、それらは短時間(数ms)で変化するため、それまでシミュレーションを適用することは困難とされていました。
そこで当社は、同分野の膨大な論文を精査して抵抗値の変化予測モデルを考案。大学との共同研究でソフトウェアに適用できる計算式を作り上げ、実機試験に近い高度なシミュレーションを可能にしました。( 図2)。
これにより、高張力鋼とアルミニウム合金の溶接条件を確立。さらに溶接条件を確立するまでの検証期間を、実機単体での実証に比べて約80%削減しました。
今後は、本技術が対象とする素材の範囲を拡げるとともに、「配電盤」「半導体モジュール」「自動販売機」など当社の製造工程への応用を進めていきます。
開発者の声
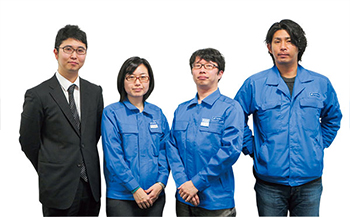
競合と差別化できる技術開発を実現
今後はスポット溶接で、超高張力鋼・アルミニウムなどの異なる部材同士を接合する技術開発を実現することで、競合と差別化できる商材を開発し、社内の製造工程にも貢献します!
-
注
-
記事の内容と所属は取材時のものです。