富士電機製品コラム
予知保全(予兆保全)とその事例
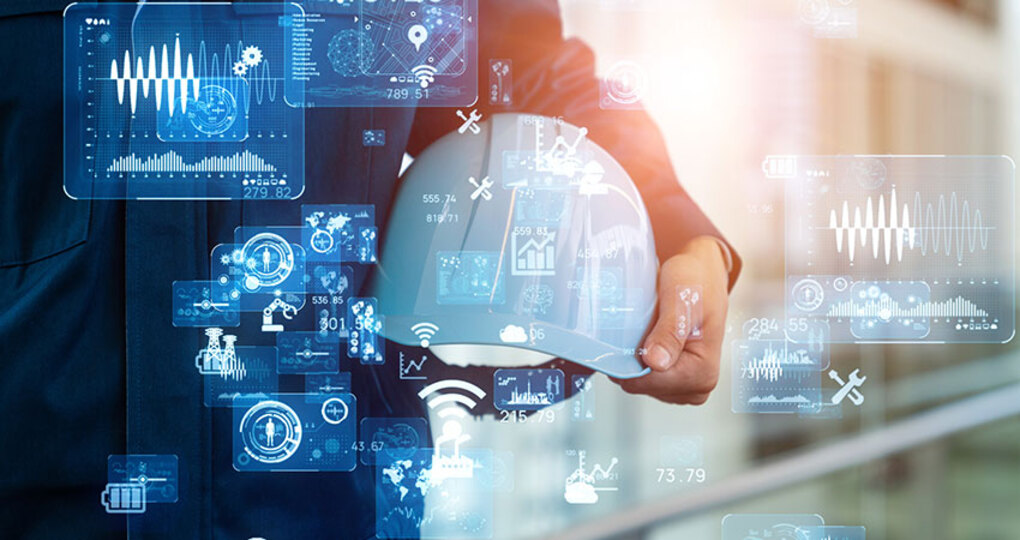
予知保全(予兆保全)とその事例
モノづくりの最前線である、工場や製造/生産現場には多くの機器や設備が林立し日々稼働しています。
製造業において“設備を稼働”させることは、企業活動そのものといえます。生産性の向上が企業の利益に直結する生産現場では、何より高い稼働率が重視されます。生産現場が高い稼働率を保つためには、設備や機器の保全活動を行わなければなりません。
保全活動を大別すると、定期メンテナンスを指す「予防保全」と、機器の状態を予め調査し未然に事故を防ぐ「予知保全」、それに修理や部品交換などを行う「事後保全」に分けられ、このうち「予知保全」は「予兆保全」とも呼ばれます。
この記事では、予知保全とその事例についてご紹介したいと思います。
予知保全とは
予知保全を簡単に言い換えると、“設備の状態を基準にしたメンテナンス”になります。具体的にいうと、日々稼働し続ける機器や設備の動きや働きを常に計測/監視し、対象物の劣化状態を掴み故障を予知して部品交換などを行う行為です。
それぞれの違い
予知保全は、「劣化予兆診断」(:Degradation symptom diagnosis)とい言い表すこともあり、いわば状態基準保全に近い考え方といえます。
-
(注)
-
状態基準保全(CBM:Condition Based Maintenance)とは:機器や設備などを一定の監視下に置き、故障や不具合の兆しを発見次第、保全対応を行うことを言います。
予知保全はコスト削減にもつながる
予知保全により、機器や設備が故障する予兆がデータによって見極められるようになると、今までベテラン工員の勘やノウハウに頼っていた部品交換時期のタイミングを、誰でも正確に知ることが可能になります。
予知保全を続ければ、データの解析精度が高まり故障の予兆もより把握しやすくなります。こうなると、設備に問題が発生する直前のタイミングでのみ設備保全を行えば良くなり、結果的に保全に掛かる経費を抑えることができるようになるわけです。
予知保全に必要な環境とは?
予知保全を行うには、対象機器を監視し続けるシステムが必要です。このような監視システムの構築は、現場の上位サーバやクラウドに影響を与えないよう、容量を意識した設計をしなければなりません。ケースによっては、既存のシステムに影響を与えないように、監視システムを追加で導入しないといけない場合もあります。
また、システム環境だけでなく、監視対象となる機器自体にも振動や温度を感知するセンサを設置しなくてはなりません。
データ収集にあたっては、予測アルゴリズムとそれを判断する仕組み・計算負荷・通信ネットワークの負荷などを考慮した、個々の生産現場に応じたシステム構築が必要です。
富士電機は、予知保全を導入する前段階からシステム実装まで一括対応することが可能です。弊社は各種センサ・データ収集システム・監視ネットワーク構築などをトータルソリューションでご提案。お客さまの、予知保全実現に貢献いたします。
富士電機の予知保全システム導入事例
生産設備の異常検知を解消
OnePackEdgeで、生産設備のあらゆる情報をワンパッケージ化。
データ設備と見える化で生産性を向上させることを達成!
お客さまのお悩み
現場のお客様のお悩み
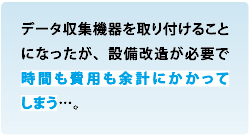
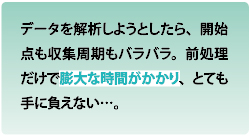
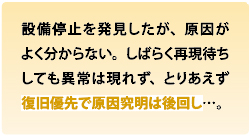
具体的な現場の課題

問題点
-
1.
予知保全システム導入前は、異常や故障の発生を知らせるアラームを受けて、設備の保守担当者が現場に急行。
発生した問題への対応をその都度行っていた。 -
2.
現場確認作業が復旧で終わってしまい、抜本的な対策につながらない。
-
3.
通常時の点検がトラブルの未然防止につながっていかない。
という問題を抱えていた。
予知保全導入前のフロー
-
1.
現場確認
-
2.
復旧処置と、いわゆる「罠かけ」による問題の再現待ち
-
3.
問題再発時に改めて調査開始
富士電機の提案
生産設備の異常検知システム「OnePackEdge」の導入で・・・
-
生産設備のあらゆる情報を、一元管理する
-
データ収集と見える化により、生産性を向上させる
-
生産設備を改造することなく高速データ収集を実現させる
-
あらゆるデータを解析しやすい形式にまとめて蓄積を行う
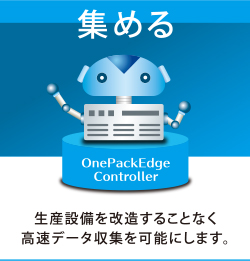
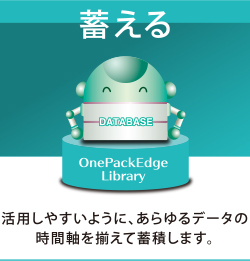
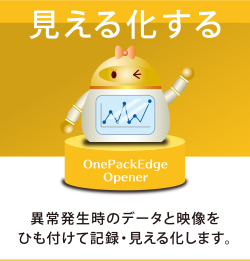
予知保全のシステム全容
システム構成
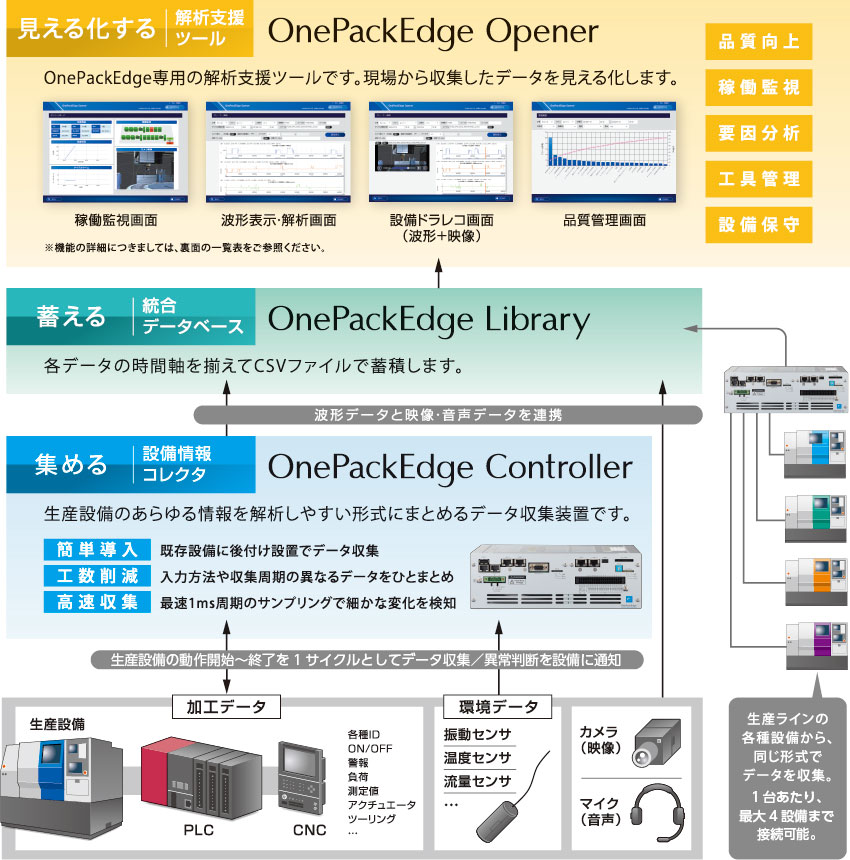
予知保全システムの導入後
生産現場における異常や故障の傾向や予兆を事前に検知し、計画的に保守・点検を実施することができるようになった。収集したデータで原因を究明し、改善や対策を実施する好循環が発生している。
予知保全システム導入後のフロー
-
1.
導入したセンサとシステムにより、異常を自動検知
-
2.
予知保全による計画停止で、即時調査を開始
-
3.
「しきい値」で機器や設備の監視を継続することが可能に
-
(注)
-
しきい値:「異常と正常」を判別する境目となる値のこと。
本製品は国内の大手自動車メーカである日産自動車・栃木工場のエンジン部品生産ラインにおいて、予知保全・生産性向上に貢献しています。お客様が抱えておられた様々な課題や導入後の改善効果をお伺いしたインタビュー動画・記事を公開しておりますので、下記リンクからぜひご覧ください。
納入先:日産自動車株式会社 栃木工場様
対象:エンジン部品生産ライン
切削加工機の工具保全最適化
OnePackEdge MARSYSの導入で、切削加工機の加工状態を簡単に「見える化&診断」が可能に。
お客さまのお悩み
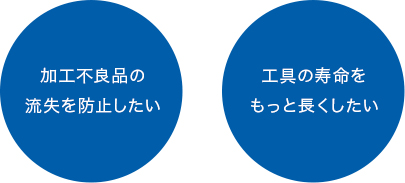
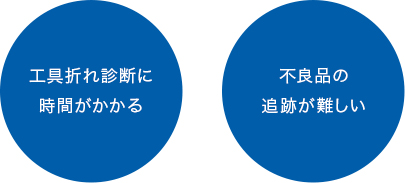
問題点
-
1.
切削工程における「工具折れ」「カケ」などにより、一定数の不良品が流出していた。
-
2.
工具寿命の把握が出来ておらず、一定時間経過した物はすべて交換。工具のライフサイクルが短かった。
-
3.
工具折れ診断を、接触式もしくは非接触式のセンサで加工終了毎に確認していたため、診断に時間が掛かっていた。
-
4.
不良発生日時の特定が難しく、不良品の追跡が困難な状態だった。
富士電機の提案
切削加工機の工具診断システム「OnePackEdge MARSYS」の導入により・・・
-
工具の異常を波形で検知し、不良品流失を防止する
-
波形サンプリングデータを蓄積し、限界まで工具の使用を可能にする
-
工具のリアルタイム診断を行い、加工後の工具折れ診断時間を不要にする
-
製品加工データをワンパッケージで蓄積することで、不良品の追跡を容易にする
予知保全のシステム全容
OnePackEdge MARSYS で収集した波形データを、解析支援ソフト「ProHealth」で解析することにより、工具の状態を「見える化」。
異常傾向を抽出し、警報出力用のしきい値を決定。継続的な監視と改善を実施することで、切削加工機の安定操業・工具費削減・サイクルタイム短縮を実現する。
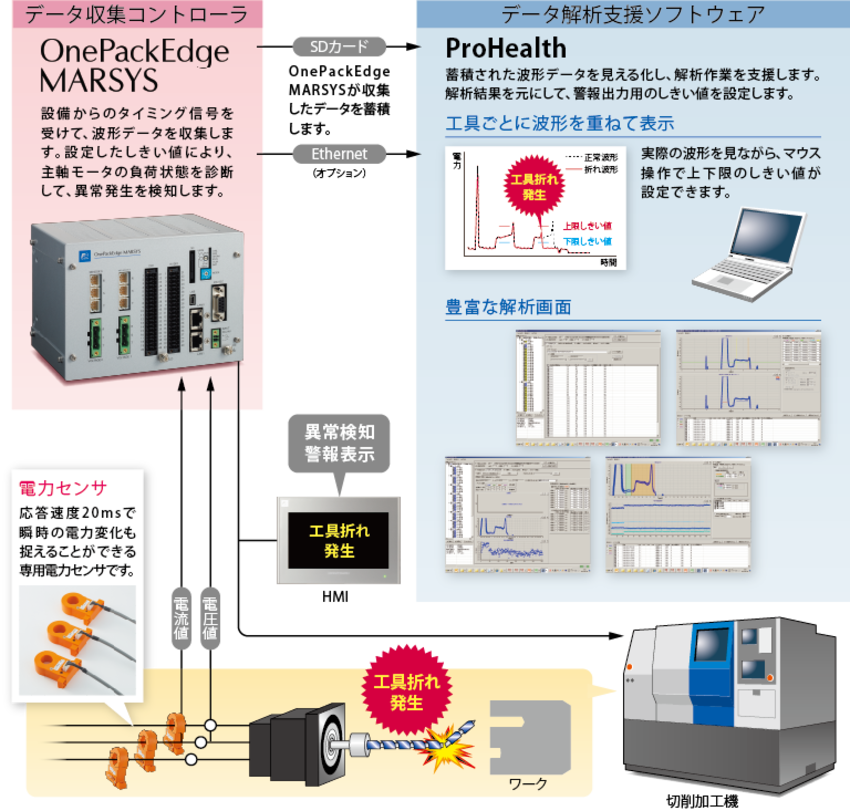
予知保全システムの導入後
不良品の流出を防止
工具状態の波形を読み取り「工具折れ」「カケ」などの異常をリアルタイムで検知。異常検知時に速やかに設備を停止させることで不良品の流出を防止。無駄な不良加工も最小限に抑え、加工品質が安定した。
工具を寿命限界まで使用可能に
各工具を波形サンプリングし、使用限界値ギリギリまで工具を使い切る目安ができた。そのため、工具の寿命限界までの使用が可能に。また工具折れを減らすこともできるようになり、工具交換回数や費用を削減できた。
工具折れ診断時間が不要
加工中に電力値を監視するため、従来センサに必要な数秒の工具折れ診断時間が不要。また、加工条件(切削プログラム)を波形として「見える化」し、加工時間や加工時の回転数を最適化。サイクルタイムの短縮を達成できた。
不良品の追跡を容易に
波形サンプルを毎加工時に記録するため、加工不良時の加工状態を後から詳細に確認できるようになった。波形のトレンドから不良発生日時が一目で把握できるため、不良品の追跡が容易になり、不良品を次工程に流すことなく取り除くことが可能に。
予知保全システムの導入効果
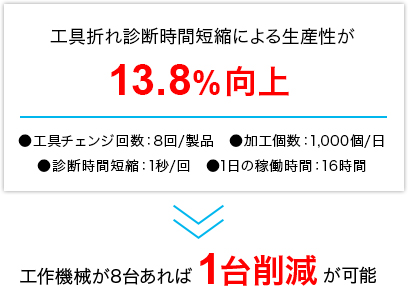
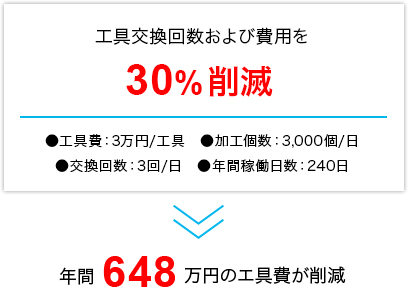
プレス機のかす上がり検知
SignAiEdge × 診断センサHUBの導入で、板金部品のプレス工程で発生する品質不良を改善。
お客さまのお悩み
プレス工程で頻繁に発生する、「カス上がり」に苦慮。
問題点
プレス加工時、ダイの中にパンチで抜いたカスが落ち、それがパンチについて上がってくる「カス上がり」が発生。このカス上がりが起きると、部品に打痕が付いてしまうため、不良品が発生してしまう。
富士電機の提案
現場型診断装置「SignAiEdge」を導入し、既存のプレス機の搬出部分に設置した「診断センサHUB」と連携。そこから稼働状況や振動情報を収集し、異常の解析を行う。
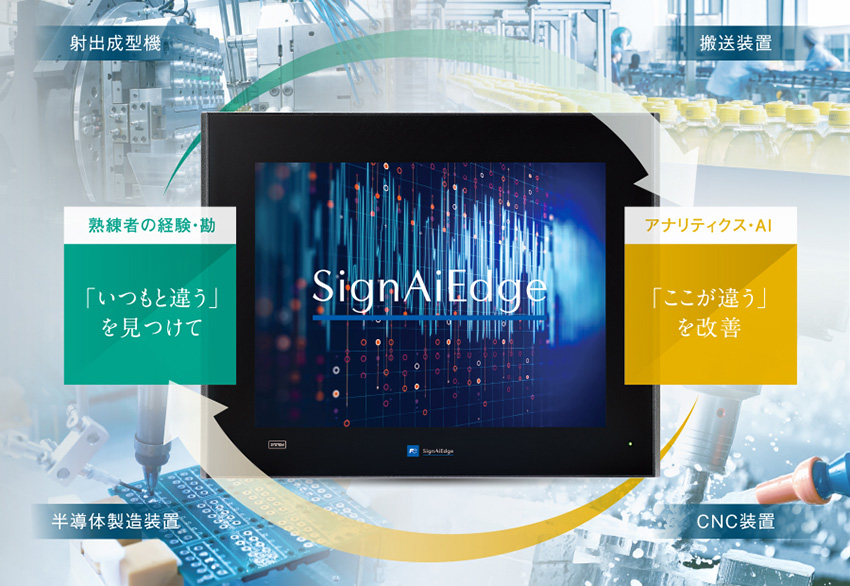
診断センサHUB対応機能概要
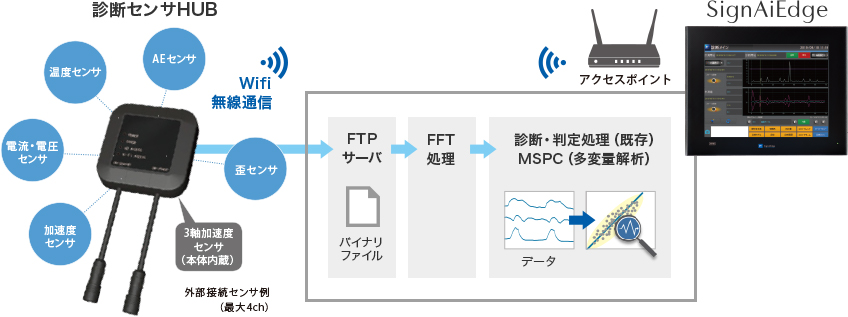
診断センサHUBは、装置稼働開始時の動きを起点にワンサイクル単位で複数の計測データを収集することが可能。またMSPC(多変量解析)は、正常稼働時の各種データの相関関係から作成した正常モデルと、実際の収集データとのズレを比較することで、異常を検出することが出来るようになる解析技術。
MSPCによる正常/異常の診断
正常モデルからの「ずれ」をしきい値で判定
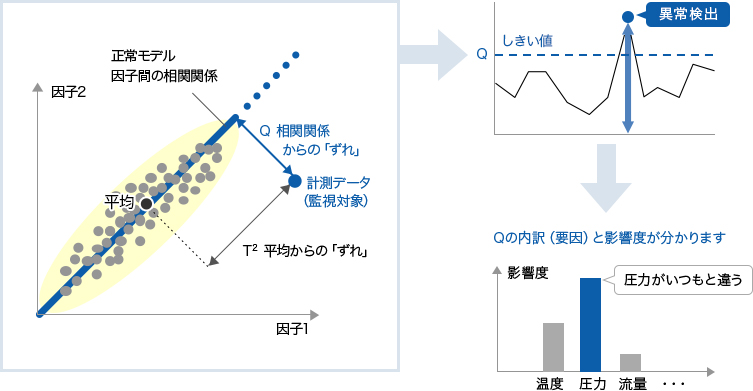
バッチプロセスデータの診断基本動作
バッチ開始を検出し、自動的にデータ収集から診断から結果表示を実施します
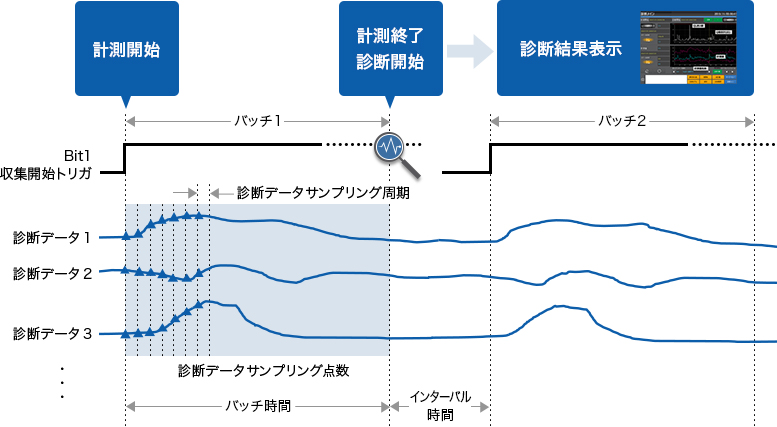
設備への設置イメージ
PLCと接続することで、診断結果の通知や診断の切替えが可能。
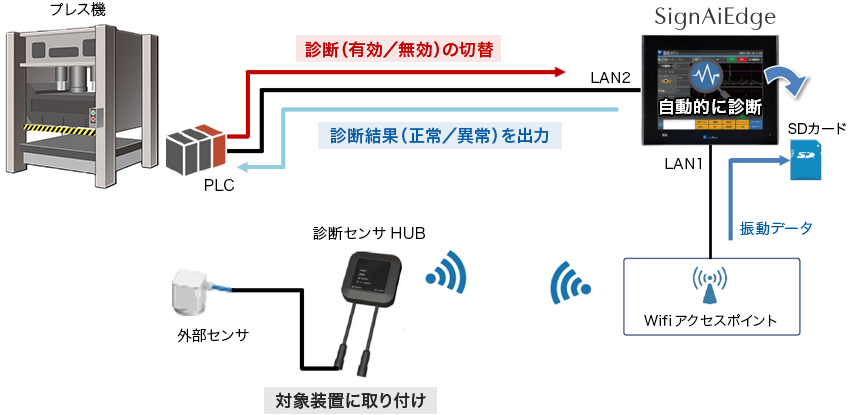
-
(注)
-
PLCとは、Programmable Logic Controller(プログラマブルロジックコントローラ)の略称。リレー回路の代替装置として開発された制御装置のこと。
予知保全システムの導入後
SignAiEdge×診断センサHUBを導入することで、異常が発生する前に、プレス機の稼働をストップさせることが出来るようになった。これにより適切なタイミングでメンテナンスが可能となり、高価な金型を痛めることもなくなった。同時に品質不良も、大幅に削減させることができた。
まとめ
ここまで予知保全の概要と、導入によるコスト的メリットと必要な環境。それに弊社の導入事例をご紹介してきました。
予知保全は生産現場のトラブルを未然に防ぐ、防波堤の役割を果たす概念です。もはや生産現場の生産性や稼働率を高めるのに、予知保全は欠かせない対策といえます。
しかし、予知保全に対する正しい知識を持たずにシステム構築を行っても、効果的な仕組みをつくることは難しいかもしれません。
予知保全導入にあたって必要なのは、対象や目的を明確にすること。富士電機では、丁寧なヒアリングでお客さまの生産現場における問題点を把握。お客様と導入目的を共有し、的確な戦略を練った上で、最適な予知保全システムの構築を行います。