富士電機製品コラム
製造業DXとは何か?
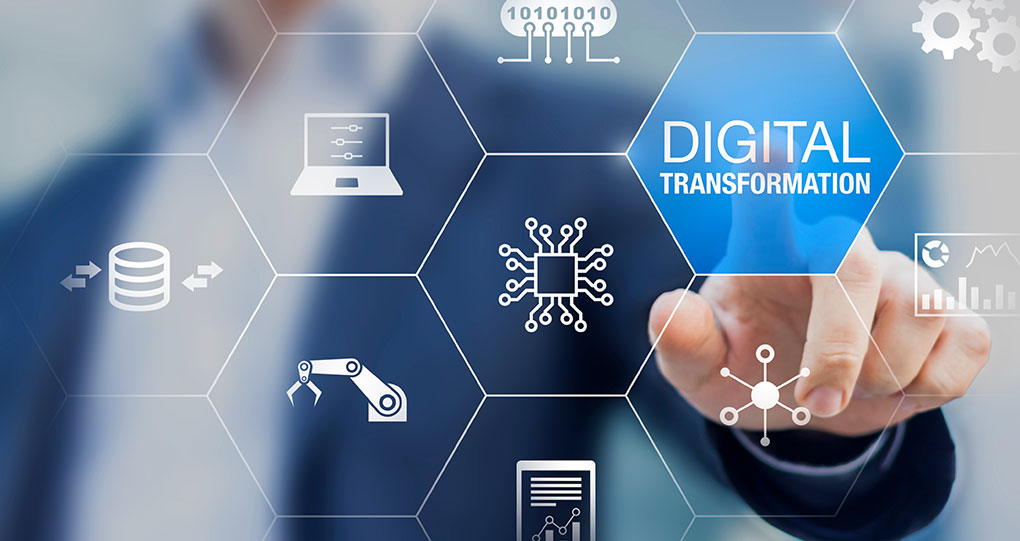
製造業DXとは何か?日本の現状課題や成功事例を解説
さまざまな社会課題を解決するための方法として、DXというコンセプトが認知されつつあります。日本国内においても、各企業でDX推進を担う組織が新設されるケースが相次いでおり、国や地方自治体もDX推進ガイドラインの公開やDX関連投資への補助金交付などの施策を実行してDXの実現を後押ししています。このようなDX推進のトレンドは社会経済全体の多岐に渡る分野に影響を及ぼしていますが、実際に当事者としてどのようにDXを進めていくべきなのか、お悩みの方もおられるのではないでしょうか。本記事では、特に製造業におけるDXに着目して、DXに関する基本知識から、実際に製造業でDXに取り組むにあたってのプロジェクトの進め方や課題、製造業DXの成功事例などを解説いたします。ぜひご一読いただき、製造業におけるDX推進のヒントとしてご活用ください。
製造業DXとは
DX(デジタルトランスフォーメーション)の定義
DXとは、Digital Transformationの略語であり、2004年にスウェーデン・ウメオ大学のエリック・ストルターマン教授が提唱した概念とされています。経済産業省が2018年に発行したDX推進ガイドラインにおいては、「企業がビジネス環境の激しい変化に対応し、データとデジタル技術を活⽤して、顧客や社会のニーズを基に、製品やサービス、ビジネスモデルを変⾰するとともに、業務そのものや、組織、プロセス、企業⽂化・⾵⼟を変⾰し、競争上の優位性を確⽴すること」と定義されています。
つまり、DXを実現するということは、単にアナログデータをデジタル化することを指すのでなく、デジタル化によって自社のビジネスモデルを変革していくとともに、組織の文化そのものにも変化をもたらし、競合他社に対する優位性を獲得していく戦略に他なりません。
製造業DXの概要
製造業においては、従来から製造コスト削減・設備保全最適化・省エネ目標達成・開発効率アップなど、生産性向上・収益力強化を目指す取り組み自体は絶えず進められてきました。そのような改善の取り組みの流れの中で、IoTやAIを始めとしたデジタル技術を新たな武器としてエンジニアリングチェーン・サプライチェーンに革新をもたらし、新たな付加価値創出につなげていくことが、製造業にとってのDXだと言えます。そのようなDXを実現した工場はスマートファクトリー(スマート工場)と呼ばれることもあります。
エンジニアリングチェーンにおけるDXの取り組みの具体例としては、最新のシミュレーション技術の活用による製品開発期間の短縮や信頼性の向上、バーチャル空間での事前検証を用いた生産ラインの円滑な立上げの実現などが挙げられます。また、サプライチェーンにおけるDXの取り組みの具体例としては、AIを活用した需要予測の精度向上による生産数や在庫数の最適化、IoT機器を活用した生産設備の予知保全による故障の未然防止やメンテナンスコストの削減などが挙げられます。
このように、製造業DXの実現にはさまざまなメリットがありますが、近年は特に感染症の流行や紛争の勃発などで世界経済全体の不確実性が増大している上に、脱炭素社会を目指したカーボンニュートラルへの対応にも迫られています。国内の製造業各社が情勢の変化に取り残されることなく臨機応変に対応できるレジリエンス(注)を確保した上で、グローバル社会における海外企業との競争力を維持していくためには、DXの実現が重要な鍵となることは間違いなく、どのようにDXを進めていくかは喫緊の課題となっています。
-
(注)
-
レジリエンス:困難な状況における回復力や適応力
製造業DX促進における現状・課題
データ収集・データ利活用の現状
製造業DXの重要性が高まっている一方で、経済産業省が公開した調査報告書の結果によれば、製造業におけるDXの取り組みはまだまだ十分に浸透しているとは言えない状況が続いています。
2021年時点の本調査において、「生産プロセスに関する設備の稼働状況等のデータ収集を行っている」と回答した企業の割合は57.0%(前年比3.0%増)でした(図表248)。過去数年間のトレンドを比較した結果を見ても、データ収集の取り組みが拡大しているとは言えない状況です(図表249)。また、データを収集している企業のうち40.0%はデータ利活用が「あまり進展していない」と認識しており(図表251)、データを収集していない企業のうち56.6%は「今後データ収集に取り組む予定はない」としています(図表253)。
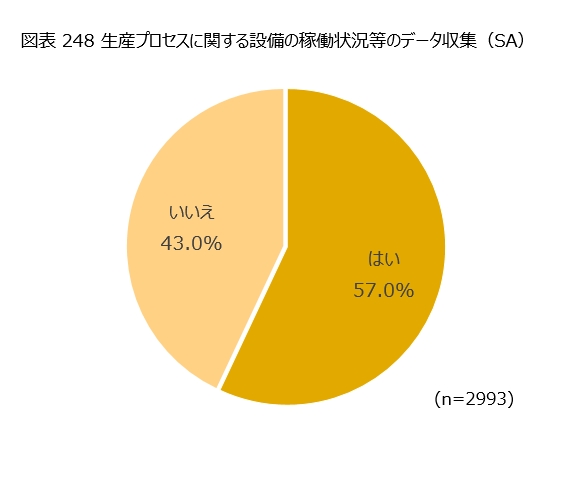
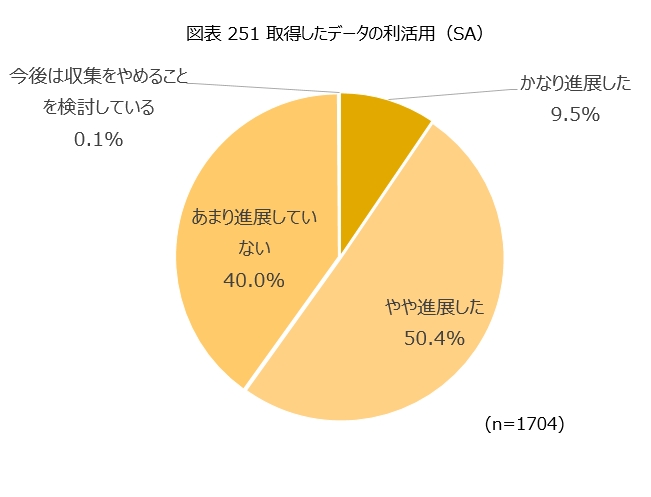
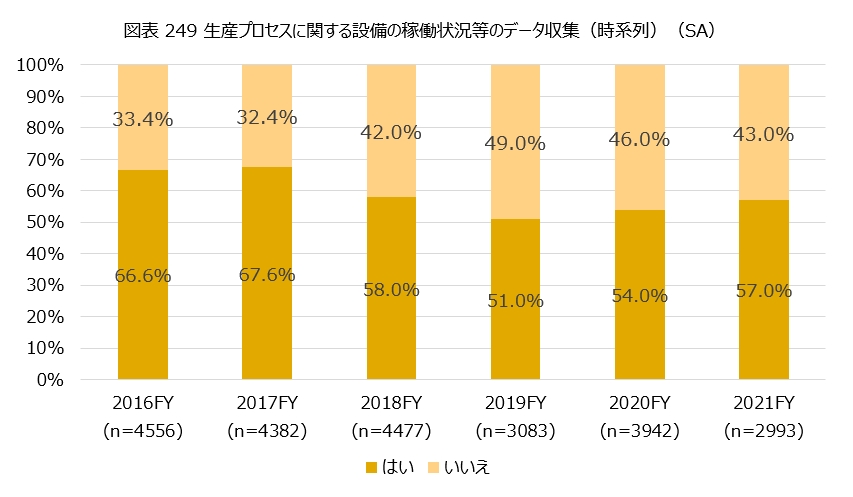
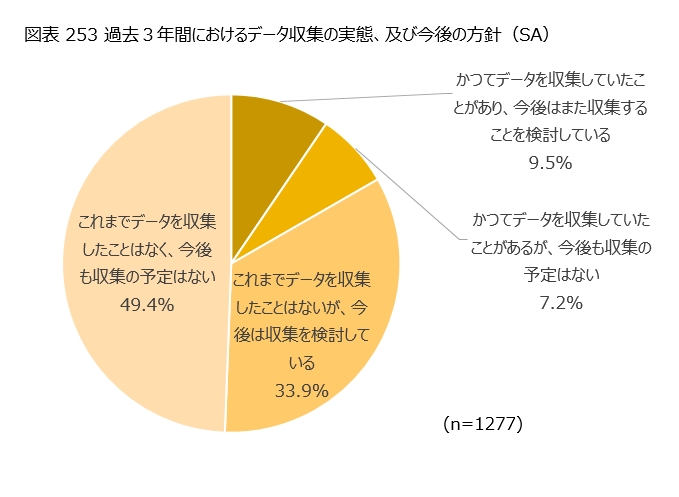
出典:「令和3年度製造基盤技術実態等調査(我が国ものづくり産業の課題と対応の方向性に関する調査) 報告書」 経済産業省 より作成
次に、最も基礎的なデータ活用方法である機械の稼働状況の見える化について、個別工程の機械の稼働状況の見える化を「実施している」と回答した企業は21.1%、「実施する計画がある」との回答は8.9%でした。また、ラインもしくは製造工程全般の見える化を「実施している」と回答した企業は18.2%、「実施する計画がある」との回答は9.7%となっています。2つの質問の結果から、機械の稼働状況の見える化に関する具体的な取り組みを開始している企業は全体の約30%にとどまっていることが分かります(図表263)。
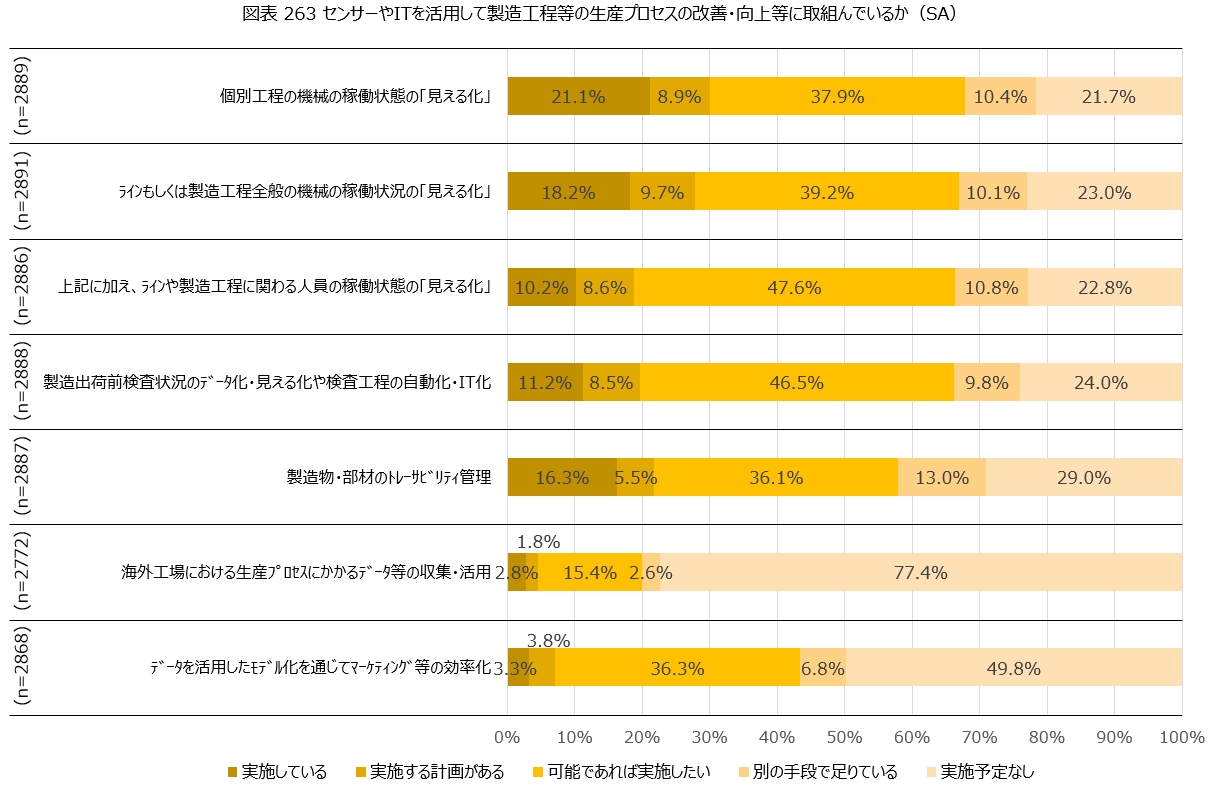
出典:「令和3年度製造基盤技術実態等調査(我が国ものづくり産業の課題と対応の方向性に関する調査) 報告書」 経済産業省 より作成
このように、製造業におけるデータ収集やデータ利活用の進捗は思わしくないという現状が見えてきました。製造業においてDXが注目され始めてから年月が経った現在においても、なぜこのような状況が変わらず続いているのでしょうか。
製造業DXに向けた課題
その原因について、同調査の結果からも、製造業DXの実現に向けて乗り越えなければならない課題として浮かび上がっています。
生産プロセスに関するデータ収集や利活用にかかる課題を複数回答で尋ねた結果では、「データ収集にコストがかかる」という回答が34.4%と最も多く、次いで「データの利活用で期待した効果が得られない(27.9%)」、「データの利活用にコストがかかる(22.6%)」、「データの活用方策が分からない(19.4%)」となっています。逆に「特に問題はない」との回答は25.5%にとどまりました(図表255)。また、デジタル人材の確保について、「必要である」と回答した企業も68.8%に上りました。(図表229)
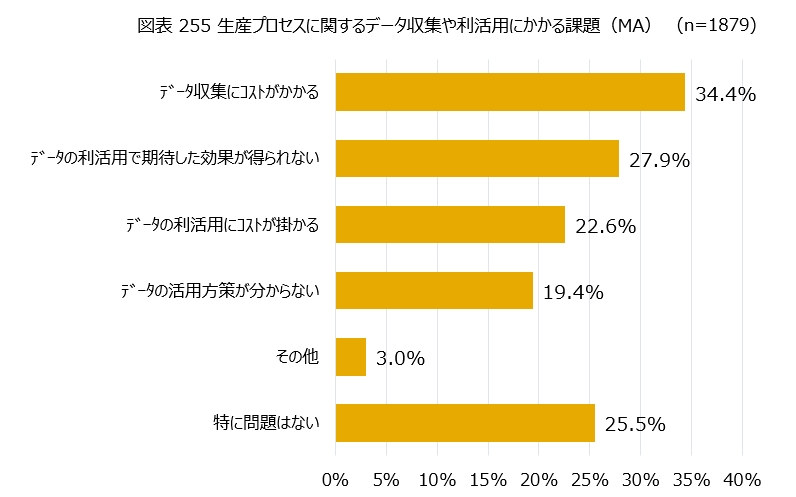
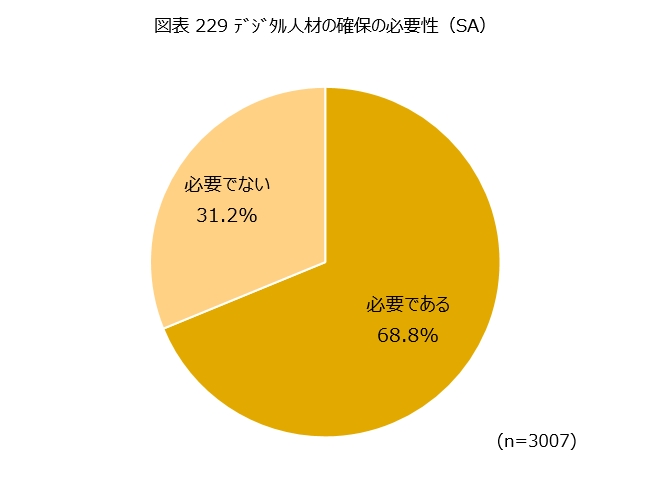
出典:「令和3年度製造基盤技術実態等調査(我が国ものづくり産業の課題と対応の方向性に関する調査) 報告書」 経済産業省 より作成
このような結果を踏まえると、データ収集や利活用の取り組み自体にコストが伴う一方で、そもそもデータの活用方法が分からない、データ活用を試みても期待したような効果が得られないという課題を抱えている企業が多いことが分かります。そのような障壁の存在が、データ収集や利活用がなかなか進まない原因になっているとみられます。また、製造業全体が人手不足に陥っている中で、そのようなDXの取り組みを適切に推進できるデジタル人材が十分に確保できていないことも、ボトルネックの一つとなっているようです。
しかし、このような現状や課題があるとしても、それがDXに取り組まなくてもいい理由とはならないのもまた事実です。DXの波に乗り遅れてしまった企業は国内外の競合他社のスピード感に追従することができず、グローバル市場では淘汰されていく可能性があります。そうならないためにも、ここからは、実際に製造業でDXを進めていく方法を確認していきましょう。
DXの進め方
現場の課題理解
製造業の生産現場でDXを進めるにあたって、最初に必要となることは、各現場で抱えている課題の正確な理解です。自社の現状やポジションを踏まえて、DXという手段を用いて、何を解決するべきなのか明確にしておく必要があります。目的設定が不明確なまま取り組みを進めてしまうと、いつの間にかDXに取り組むこと自体が目的となってしまい、本末転倒の事態になりかねませんので、このプロセスが最も重要と言えます。
課題を洗い出す際には、単純に業務上抱えている課題を並べるだけではなく、目標とする姿に対して現実がどの程度乖離しているのか、なぜそのような乖離が発生しているのかを慎重に分析するようにしましょう。また、課題解決の重要度と緊急度によって重みづけをすることも重要です。正確な値でなくても構いませんので、想定される導入効果を試算しておくことで、何から取り組むべきなのか、その取り組みにどのくらいの予算をかけられるのかの目安となります。
実現手段の検討
解決すべき課題を設定した後は具体的な手段を検討する段階となります。実現手段を比較検討する上では、それぞれ必要となる費用や納期、自社内で必要となる作業工数、そして課題解決の実現度などが比較材料となります。
注意点としては、むやみに特定の手段に固執することなく、想定される方法を漏れなく洗い出して検討するようにしましょう。例えば、100%正確な判定が要求事項なのか、90%程度の精度でも運用上は支障がないのかによって、それぞれ最適な手段が異なる可能性があります。また、最新の技術を使わずとも、従来から普及しているツールでも十分期待通りの効果が出るようなケースでは、後者の方が合理的な選択です。
PoCの実施
DXの取り組みにおいては、いきなり大規模な本番のシステムを導入するのではなく、PoC(Proof of Concept:概念実証)と呼ばれるプロセスを踏むことが一般的です。PoCは小規模なシステムを最低限のコストで限定的に導入することによって、本当に想定通りの効果が出るかどうかを実際の現場環境で確かめるプロセスであり、最初から大規模な投資を行ってプロジェクトが大失敗に陥るリスクを抑えるために行います。
ここで想定通りの効果が出ない場合、無理に進めるのではなく、実現手段の再検討や解決すべき課題設定自体から見直すなど、前のステップに戻って再検討をすべきです。また、一般的にPoCは失敗することも多いものですので、うまくいかないことがあることを前提として、たくさんのアイデアを効率よく評価していく姿勢で進めるようにしましょう。
本番システムの構築・運用
PoCで導入効果が出ると判断されたテーマは本番システムとして構築・運用する段階となります。実際の生産現場で活用されるシステムですので、PoCとは異なりシステムの稼働品質を担保する必要があります。
さらに、現場作業者の業務プロセスに配慮したユーザビリティを確保することも重要です。DXが重要なテーマだとしても、誰しも自らの業務に変化点が生じることは嫌がるものです。システムを作り終えてからいきなり現場に押し付けるのではなく、要件定義の段階から現場の意見を取り入れて仕様に反映させる、導入目的に関しても事前に丁寧な説明を重ねて理解を取り付けるといったプロセスも重要です。
一度構築したシステムを運用する場面では、定期的に問題点を点検しながらブラッシュアップを図りつつ、継続的に成果を刈り取っていくようにしましょう。また、十分な導入効果が得られた場合に導入範囲を広げるケースも予め想定して、将来拡張性も考慮した仕様としておくべきでしょう。
富士電機のDX取り組み事例
最後に当社のDXに関連する取り組み事例の一部をご紹介いたします。
富士電機では、電力・交通などの社会基盤、製鉄や化学、自動車製造、電気・電子などの産業用設備やシステム、そしてビルや店舗、自動販売機、車載機器などの民生分野に至るまで、製造業として多岐に渡る事業を展開しております。そのような事業環境の中で、自社工場のDX推進とお客様工場のDXへの貢献を両輪として、工場系DXの取り組みを進めております。
富士電機の工場系DX
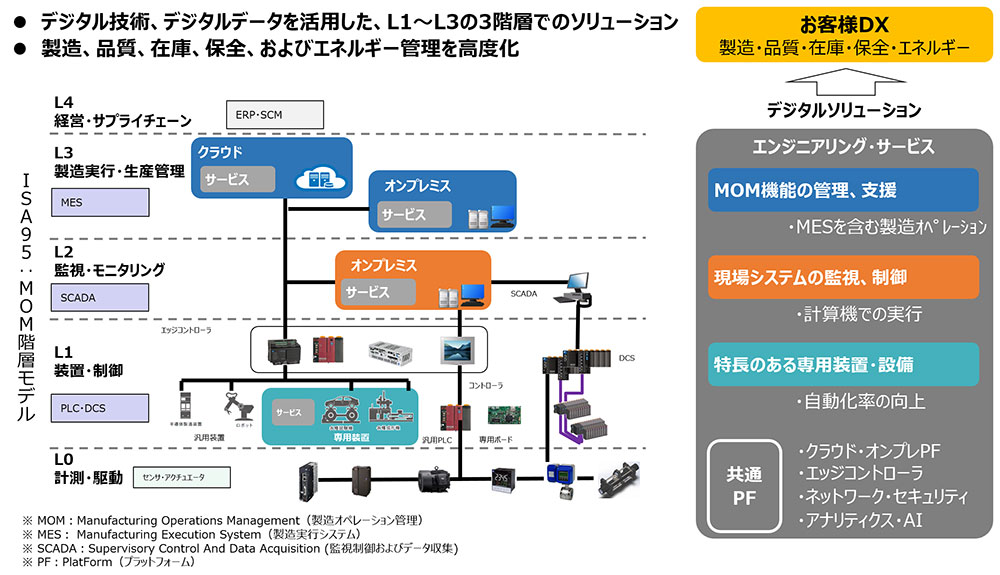
自社工場のDX推進事例
自社工場のDX推進事例として、山梨工場における省エネ達成の事例があります。
パワー半導体のチップを生産している山梨工場では、生産工程において多くのエネルギーが必要となることから、特に省エネ化が求められているという課題がありました。
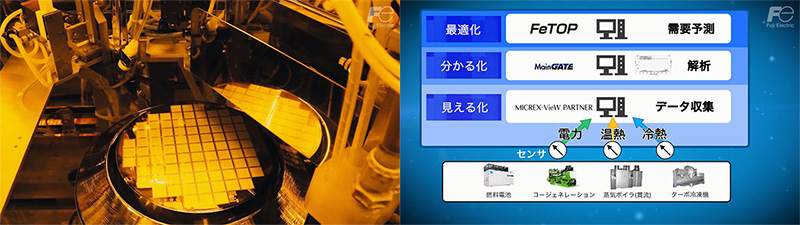
そこで、エネルギー使用量の「見える化」を足掛かりとして、エネルギー使用量の削減を目指しました。センサで電力や温度などのデータを収集し、解析ソフトウェアを使用しながら、蓄積された実績データを多角的に分析することで、「見える化」を起点として「分かる化」に発展し、さらなるエネルギーのムリ、ムダ、ムラの発見することができました。また、AIを活用した需要予測により、エネルギーコストが最小となるような運転パターンの計画を立案するなど、「最適化」のフェースまでステップアップすることができました。
このような取り組みにより、生産量の増加にも関わらず、5年間で34%の省エネを達成することができました。エネルギー自給率100%の達成の実績も評価され、省エネ大賞の経済産業大臣賞を受賞しました。
お客様工場のDXへの貢献事例
お客様工場におけるDXの実現に貢献した実績の一例として、当社製品のOnePackEdgeを活用した組立加工分野のお客様向けのデータ収集・データ利活用システムの構築がございます。生産ラインを構成する多種多様な生産設備から生産サイクルと同期した一元的なデータ収集を行い、それぞれのデータを統合データベースに整理して集約するシステム構成とすることで、お客様社内の各部門で必要とされていたデータの利活用が容易になりました。製品品質の管理・生産設備の稼働監視・加工不良発生要因の分析・加工機の工具管理の円滑化など、さまざまな用途にご活用いただいております。
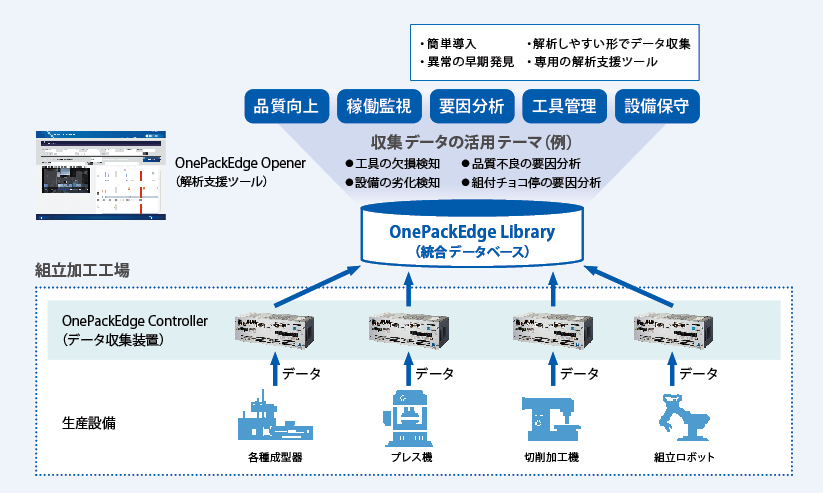
まとめ
ここまで、製造業におけるDXの現状と課題、DXの進め方に関するポイントや当社の取り組み事例を解説して参りました。DXは変化の激しい時代の中で自社の優位性を保ち続けるために必要な取り組みであり、さまざまな課題を乗り越えて成果を掴み取っていくことは今後の大きなアドバンテージとなることがお分かりいただけたかと思います。
富士電機では、自社工場のDXを推進していくとともに、製造業のお客様におけるDX実現にお役立ていただける商材を取り揃えており、上位系のシステム構築を含めたエンジニアリング対応も含めてご提供することが可能です。製造業でDXに取り組んでおられる方は、ぜひ一度当社製品Webページをご覧ください。