富士電機製品コラム
工場におけるデータ収集の重要性
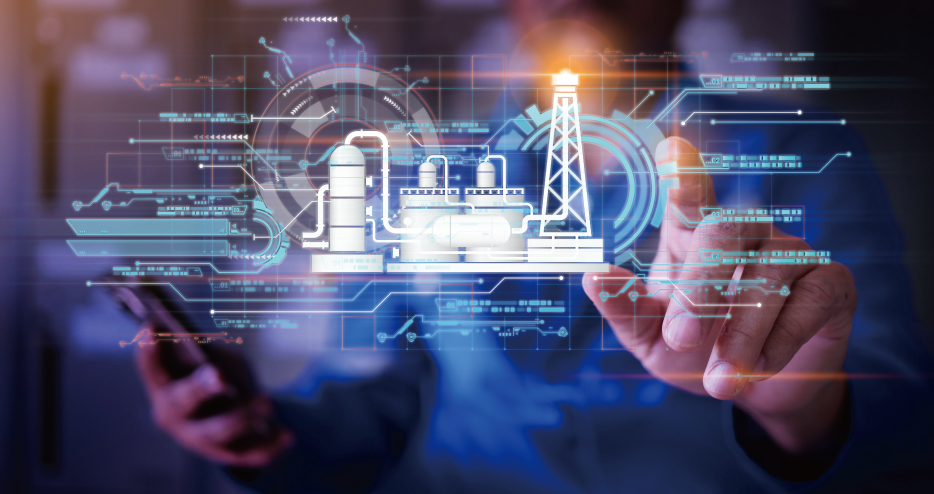
工場におけるデータ収集の重要性-IoT導入のメリットと進め方をご紹介
IoTやAIなどデジタル技術の浸透により、製造業各社では工場のデータ収集に取り組む動きが広がっています。さらに、収集したデータを有効活用して、DX(デジタルトランスフォーメーション)やスマートファクトリー(スマート工場)を実現し、従来の業務プロセスを変革することが、自社の収益力と競争力を高めることにつながります。そのような変革の出発点として、工場のデータ収集を着実に進めて、生産現場の状態を定量的に評価できる状態を整えることが重要です。本記事では、工場におけるデータ収集のメリットや進め方を詳しくご紹介いたしますので、ぜひご覧ください。
工場におけるデータの種類と収集方法
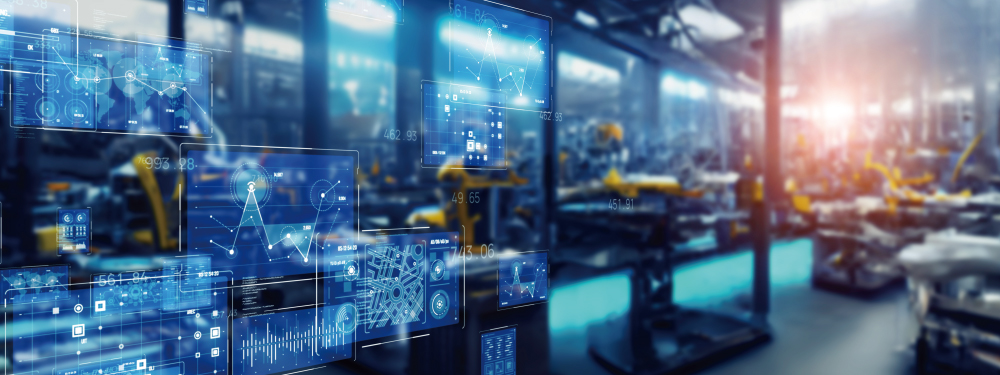
工場にはどのようなデータが存在しており、それぞれどのような方法で収集できるのでしょうか。ここでは、工場内のデータを大きく3種類に分けてご紹介します。
生産システムのデータ
工場には、生産管理・生産指示などを担う上位システムが導入されていることが一般的です。そのようなシステムから、生産計画や生産実績などのデータを収集することで、事前に立てた計画に沿って問題なく生産が行われているかどうか、定量的なデータに基づいて確認できます。
具体的には、企業全体の基幹システムで最上位の計画層にあたるERP(Enterprise Resources Planning:企業資源計画)や工場で効率的なものづくりを行うことに特化した実行層にあたるMES(Manufacturing Execution System:製造実行システム)と呼ばれるシステムがあります。各システムの工場における役割のイメージ図は以下の通りです。
.jpg)
このようなシステムでは、取り扱いやすい定型的なデータが保存されており、データ収集も比較的容易です。ただし、生産現場に目的別で複数のシステムが並立しており、それぞれのデータに紐づきがないような場合には、求めるデータ形式とするためにデータの結合や整形などの前処理が必要になってしまう可能性があります。
生産設備のデータ
多種多様な生産設備が用いられている工場では、生産設備から直接データ収集を行うことで、生産現場の詳細な状況を把握できるため、稼働率低下や品質不良などの諸課題を解決するための糸口となり得ます。生産設備からデータ収集を行う場合、その方法はさまざまです。以下の図は生産設備からデータ収集を行うシステムの一例です。
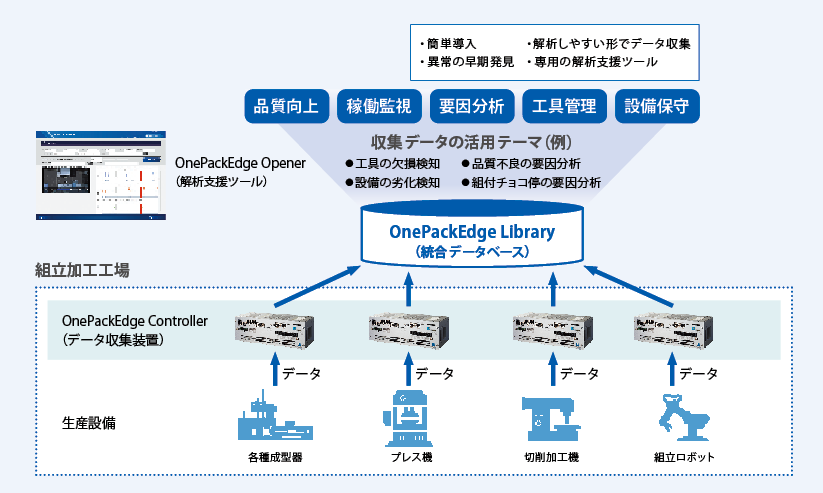
新しい設備であれば、生産設備の動作を制御するPLC(Programmable Logic Controller)やCNC(Computer Numerical Control)から通信でデータを収集できることが多いですが、設備メーカごとにデータ収集方法が異なる場合も見られます。そのような課題を解消するため、業界の共通規格であるオープンネットワークに対応する設備もあります。
しかし、古い設備の場合、通信でのデータ収集手段がないことも多々あります。そのような場合は、表示灯が点灯した色のデータから稼働状況を把握する、後付けで各種センサを取り付けて異常を監視するなどの方法が考えられます。また、設備のメータをカメラで撮影することで、数値データに変換して自動でデータ収集できる機器も登場しています。
作業者のデータ
工場で働く作業者の動きをデータとして取り込むことも可能です。データの収集方法としては、所定の場合に作業者にスイッチを押してもらうような単純な仕掛けから、カメラで撮影した映像データとAIを組み合わせて作業内容を自動で見える化するような高度な方法までさまざまです。また、工場内でGPSやビーコンなどを用いて位置情報を収集することで、作業者の動線を解析するような取り組みもあります。
その他にも、工場で作業者が記録した点検結果や故障対応結果なども重要なデータです。しかし、それらのデータは紙で管理されていて、データとして十分に活用できていない場合も見受けられます。例えば、それらの保全業務をシステムとして管理することで、従来は紙でしか確認できなかった情報を電子化して、保全部門内の共有データとして活用することが可能です。
データ収集のメリット
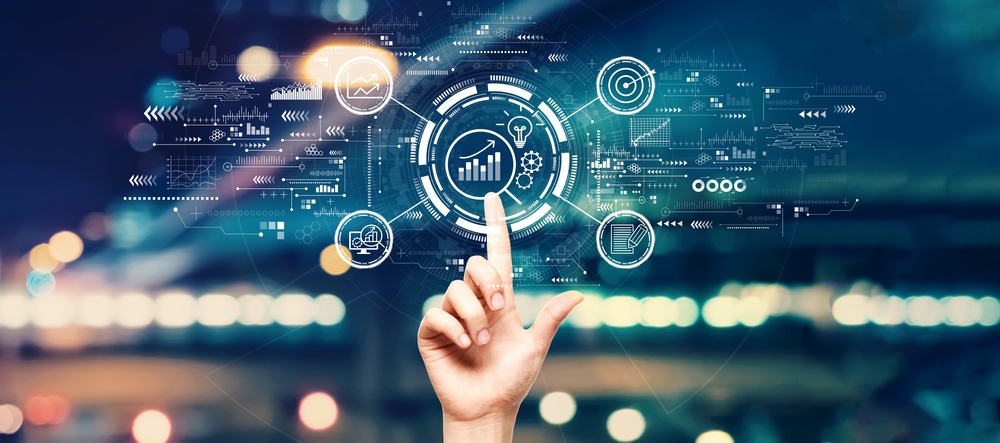
それでは、工場のデータ収集を進めることによって、どのようなメリットを得られるのでしょうか。
生産性の向上
1つ目は生産性の向上です。工場は製造業の利益を生み出す源泉であるため、経営層にとっても工場の生産性向上は至上命題です。そのため、生産現場の改善の取り組みは絶えず求められています。工場の生産性向上を目指す改善活動を始めるためには、まずはデータ収集を進めることで、あるべき姿と現状とのギャップを正確に理解することが必要です。定量的なデータ収集を伴わない活動では、打ち手を間違えてしまう可能性もある他、改善活動の効果を測定することも難しくなってしまいます。
トラブル発生時の対応力
2つ目はトラブル発生時の対応力です。データ収集を継続することで蓄積されたデータベースは工場での不測の事態における対応にも役立ちます。
工場で発生する緊急トラブルの例として、不良品の発生が挙げられます。早期に影響範囲を特定した上で、他に不良品がないかの検査を行ったり、すでに次工程や市場に流出している場合は製品を回収したりする必要性も生じます。また、不良が生じた原因を究明して対策を講じなければなりませんが、そのような一連の対処を行うなかで、生産システムや生産設備から収集したデータを活用すれば、無駄なく的確に対応を進めることができます。
データ収集に必要な準備
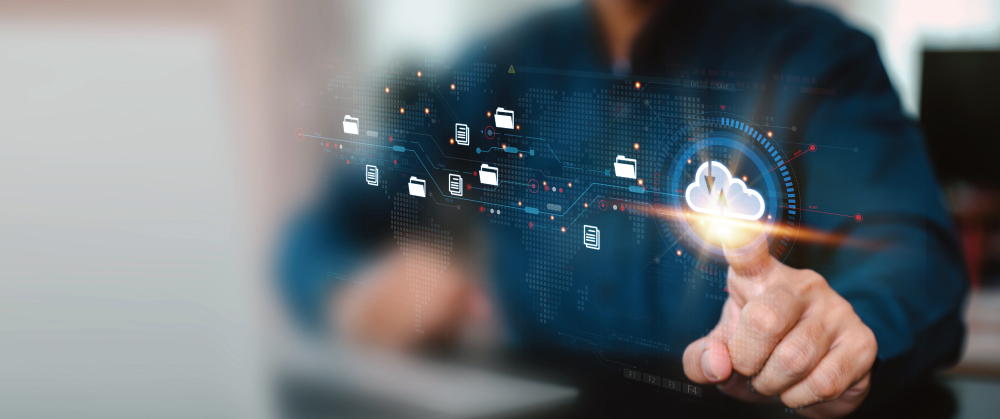
工場におけるデータ収集の重要性はご理解いただけたと思います。ここからは、主に生産設備データを収集する場合において、どのような準備が必要になるかを確認していきます。
データ収集機器・ソフトウェア
まずは、工場における生産設備のデータを収集するための機器やソフトウェアを準備する必要があります。
データ収集機器には、生産設備のPLC/CNCと通信を行うことでデータを収集する機器と生産設備に後付けで設置することでデータを計測するセンサがあります。また、汎用のPCなどにインストールすることで、生産設備からのデータ収集が可能となるソフトウェアもあります。どちらの場合においても、収集できるデータの種類・点数・サンプリング周期・入出力インタフェースなどの性能を確認した上で、目的に応じた適切な機器を選定する必要があります。
ストレージ・サーバ・アプリケーション
収集したデータは一定期間保存しておかなければ、十分に活用できません。また、製造業においてデータを活用する際には、目的に応じてデータを見やすく表示したり、分析したりすることが重要です。
したがって、データの保存領域であるストレージやデータを活用するアプリケーションに加えて、データ収集機器やアプリケーションとデータのやり取りを行うためのサーバを立てる必要があります。設備数やデータ点数が少なければ、一般的なPCやNAS(Network Attached Storage)で事足りることもありますが、工場全体を対象にした大規模なデータ収集を行う場合などは、高い負荷にも耐えられるように専用のサーバを構築すべきでしょう。
また、昨今ではインターネットに接続可能なIoT機器でデータを収集して、直接クラウド上にデータを保存することも可能となっています。自社でサーバなどのメンテナンスを行う必要がない、状況に応じて保存容量や利用サービスを柔軟に変更できるなどのメリットがあります。
データ収集の進め方
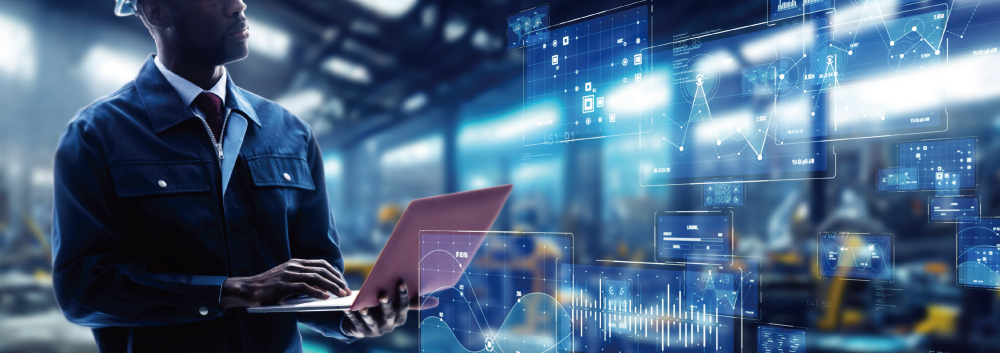
データ収集を始めるにあたって、どのような準備が必要なのかおわかりいただけたところで、最後にどのようにデータ収集を進めていくべきかを確認していきましょう。以下の図は富士電機の組立加工データ収集システム OnePackEdge によってデータ収集を進めた場合のシステム構築の一例です。
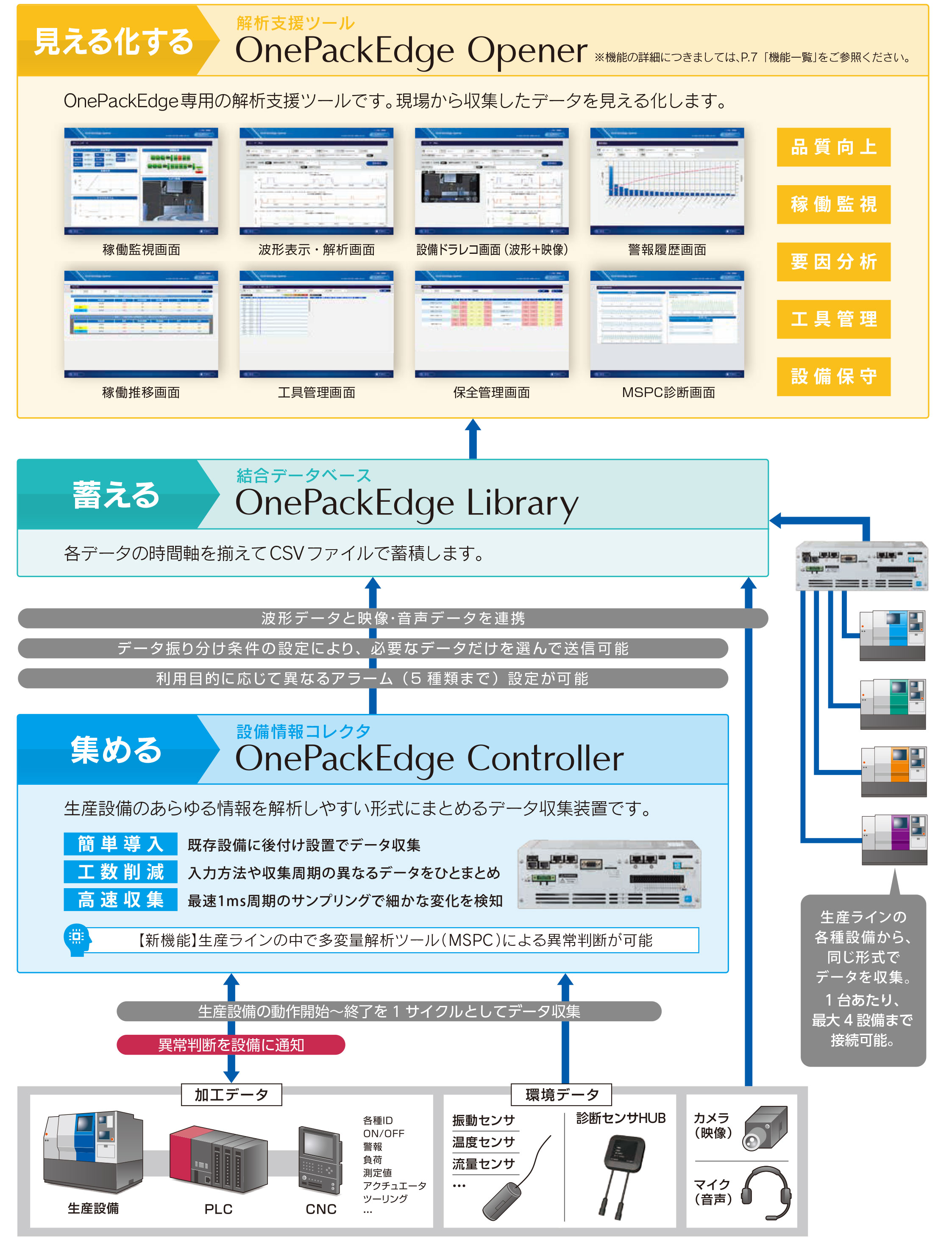
どのようなデータを収集すべきか検討する
まずは、データ収集を行う目的を決定した上で、どのようなデータを収集するか検討しましょう。工場におけるどのような課題を解決したいのか、データ収集を行う目的を事前によく検討した上で、過不足なく収集するデータを決定する必要があります。目的が曖昧なままプロジェクトを進めてしまうと、いつの間にかデータを収集すること自体が目的にすり替わってしまいます。データ収集はあくまで手段であるという点に留意しながら、最終的に達成したいゴールを意識して取り組みを進めていきましょう。
データ収集に必要な環境を整備する
データ収集の目的と項目が決まったら、それに応じたデータ収集手段を準備して環境を整備します。本記事の「データ収集に必要な準備」も参考にしながら、必要な機材を選定・手配・設置していきましょう。最初からいきなり大規模なシステムを導入することは、大きなリスクをともなうため、PoC(Proof of Concept:概念実証)と呼ばれる検証プロセスで導入効果が得られそうかを確かめながら、徐々に適用範囲を広げていくことが一般的です。プロジェクト推進にあたっては、社内の関係者との合意形成を図りながら、決められた予算の範囲内で最大の効果が得られるようにしましょう。
収集したデータを分析する
実際にデータが収集できる状態になったら、まずは収集されたデータと求めていたデータに齟齬がないかを確認しましょう。設定手順のミスなどによって、違うデータを収集していたり、データが欠損していたりする場合もあります。収集したデータに問題がないことが確認できたら、その後はデータを蓄積・活用していくフェーズです。例えば、稼働率などの生産指標をリアルタイムにわかりやすく共有したい場合はダッシュボードを表示させたり、特定の設備の異常予兆を捉えたい場合は波形を詳細に解析する画面を用いたりするなど、目的に応じて必要なアプリケーションは異なります。工場のデータ収集の準備段階から、このようなデータ活用のあり方もイメージした上で、最適なアプリケーションをセットで用意しておきましょう。
まとめ
ここまで、工場でデータ収集に取り組む上で必要な情報をお伝えして参りましたが、いかがでしたでしょうか。IoTの導入によるデータ収集によって得られるメリットやデータ収集を進めていくために押さえておくべきポイントについて、おわかりいただけたかと思います。データを適切に活用することは工場のDXやスマートファクトリーの実現につながります。
富士電機では、工場のデータ収集にお役立ていただける製品を多数ラインアップしています。お客様の目的に応じて、最適な機器やアプリケーションをワンストップでご提供することが可能です。工場のデータ収集をご検討されている方は、以下のリンクから製品Webページをご覧いただき、ぜひ富士電機にお問い合わせください。