富士電機製品コラム
工具の寿命とは?
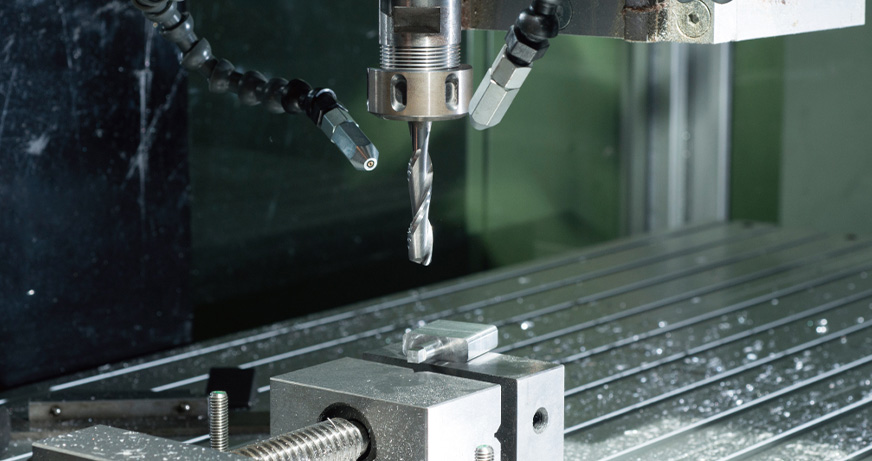
工具の寿命とは?損傷の種類や寿命管理方法を解説
工作機械を用いて、金属材料を目的の形状に加工する「機械加工ライン」では、加工の種類・ワークの材質・必要な加工精度等の加工条件に応じて、切削用のドリルや研磨用の砥石など、さまざまな工具が使い分けられています。寿命が来ているにもかかわらず摩耗しすぎた工具を使い続けると、ワークの加工品質が悪化してしまうため、適切な頻度で交換する必要があります。しかし、逆に頻繁に交換することにより、余計なコストが発生してしまうことも問題です。したがって、工具寿命の最適管理は機械加工ラインにおける重要な取り組みです。本記事では、主に切削工具(刃具)を対象として、工具の寿命を適切に管理するために役立つ情報をご紹介いたします。
工具の寿命とは?
工具の寿命を適切に管理するためには、「工具の寿命が到来した」ことを生産現場で判断する必要がありますが、一般的にどのような状態に至った時点が「工具寿命」とされるのでしょうか。
一般社団法人日本機械学会が公開している機械工学辞典の「工具寿命」の項目では、「切削工具が破損あるいは摩耗し使用に耐えなくなるまでの正味切削時間で,通常(分)を単位として表される.工具寿命の判定基準としては,生産現場では製品の寸法精度や仕上面粗さあるいは切りくず形状の変化などが用いられ,実験室的には逃げ面の摩耗幅やすくい面摩耗深さがある値に達した時点とされる.」と定義されています。つまり、生産現場における「工具寿命」の定義は、製品品質として求められている加工精度や表面粗さの基準を満たす加工ができなくなった時点だといえます。
工具損傷の分類
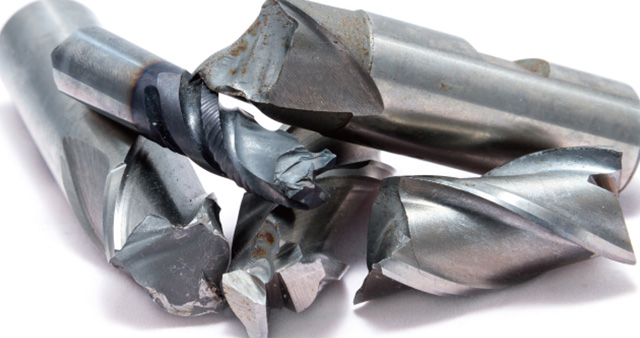
工作機械は切削工具を通じて大きな力を与えることでワークを削るため、工具は常に過酷な環境下に置かれます。そのため、工具が劣化することは避けられませんが、工具が受ける損傷にはどのような種類があるのでしょうか。
脆性損傷(チッピング・欠損・破損等)
工具の使用期間に関係なく突発的に発生する損傷を脆性損傷と呼びます。損傷状態の違いによって呼び方が異なり、一般的に刃先の微小な欠けはチッピング、刃先の大きな欠けは欠損、刃先や工具全体に及ぶ損傷は破損と呼ばれています。それ以外にも、はく離・き裂などの損傷形態もあります。
摩耗
脆性損傷以外の主に工具の使用期間に比例して生じる漸進的な損傷を磨耗と呼びます。突発的な損傷ではなく、工具を使用するごとに徐々に進行する損傷です。磨耗のなかでも、「切削距離に比例する機械的磨耗」と「切削温度に大きく影響を受ける熱的磨耗」に分けられます。
工具の寿命を管理する方法
工具に損傷が発生すると、製品品質の基準を満たす加工ができなくなります。そのような工具は寿命に達しており、適宜交換しなければなりませんが、その交換時期はどのように管理すればよいのでしょうか。
不良発生基準(事後保全)
単純な方法は、加工不良の発生を確認してから工具を交換するという方法です。一般的な設備保全方法の分類では、事後保全と呼ばれる類型です。
メリットとしては、工具寿命の判断が簡単であることが挙げられます。デメリットとしては、全数検査ではなく抜き取り検査の場合、加工不良を発見した時点ですでに多くの加工不良を見逃している可能性があります。その場合、次工程にも損害が波及することになってしまいます。
使用時間基準(予防保全)
工具の使用時間や使用回数を基準として交換する方法もあります。工具損傷に至る前に余裕をもって交換できる時期を寿命と定義して、加工不良の発生を未然に防止します。一般的な設備保全方法の分類では、予防保全と呼ばれています。
交換時期の設定が比較的容易かつ加工不良の発生を防止できる可能性が高いという点がメリットですが、まだ使用できる工具を寿命と判断して交換してしまう可能性があること、突発的な工具損傷による加工不良は防ぐことができない点がデメリットです。
工具状態基準(予知保全)
近年では、各種センサを取り付けて加工時のデータを測定して、工具の劣化状態を定量的に監視することで、工具寿命を管理する手法もあります。一般的な設備保全方法の分類では、予知保全とされる方法です。
メリットとしては、工具毎にその状態に合わせて適切な時期に交換を行うことで、加工不良の発生を防ぎつつ、工具交換費用を最小限に抑えることができる点が挙げられます。デメリットとしては、工具状態を監視する手間とコストがかかる点や交換基準の設定が比較的難しい点があります。
工具の寿命を延ばすには?
それでは、製品品質への悪影響を防ぎつつ、工具の寿命を延ばすには、どのような方法があるのでしょうか。
上述のとおり、摩耗による工具寿命はおおむね工具の使用期間に比例して決まります。しかし、実際の寿命はその時の加工条件や環境条件によって差異が生じるため、標準的な使用時間を交換基準とすると、実際の寿命に対してある程度余裕をもった交換時期にならざるを得ません。そのため、工具を少しでも長く使用するには、実際の工具の劣化状態に応じた状態基準(予知保全)で交換することがおすすめです。
富士電機では、工具寿命の管理にお役立ていただける製品として、工具診断システム「OnePackEdge MARSYS」をラインアップしています。本製品は、切削加工機の主軸モータの負荷電力を専用の電力センサを用いてリアルタイム計測することで、加工状態を簡単に「見える化」し、工具状態を「診断」できるシステムです。専用の解析支援ソフト「ProHealth」を用いて、ツール/ワーク別に閾値を設定できるため、加工条件に合わせてより正確な診断をすることが可能です。「OnePackEdge MARSYS」によって加工サイクル毎に工具別の計測波形を蓄積していくことで、工具を寿命ギリギリまで使い切る目安を作ることができます。それによって、使用時間を基準とした工具交換から、各工具の劣化状態を基準とした工具交換に移行することが可能となります。

まとめ
ここまで、工具寿命を左右する要因となる工具損傷の種類や工具寿命の管理方法についてお伝えして参りましたが、いかがでしたでしょうか。機械加工ラインにおいて、工具寿命を適切に管理する仕組みの重要性について、ご理解頂けたかと思います。
富士電機の工具診断システム「OnePackEdge MARSYS」は、長年にわたってお客様の機械加工ラインにおける工具状態の管理・診断に貢献して参りました。本製品にご関心をお持ちの方は、以下のリンクからぜひ富士電機にお問い合わせください。