富士電機製品コラム
工具折損を検知する方法とは?
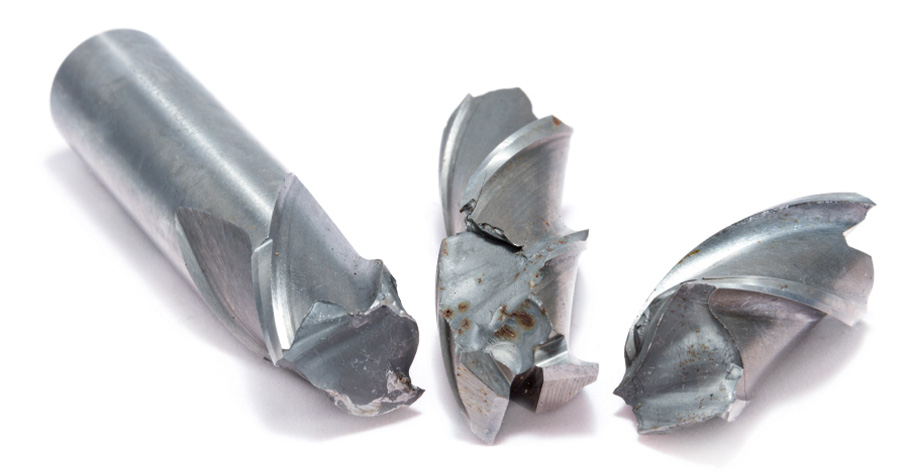
工具折損を検知する方法とは?折損の原因や問題も解説
工作機械を用いて、金属材料を目的の形状に加工する「機械加工ライン」では、数値制御(NC:Numerical Control)による均質な加工が可能なNC加工機が普及しています。そのなかでも、自動工具交換機能(ATC:Automatic Tool Changer)を備えたマシニングセンタでは、作業者が工具を交換しなくても、複雑な加工を連続しておこなうことができます。しかし、このように自動化が進んだ機械加工ラインでは、突発的な工具折損を見逃してしまう可能性があります。折損した状態で加工を続けると、さまざまな問題が生じるため、工具折損を確実に検知する仕組みが必要です。本記事では、工具折損を検知する方法について、主に切削工具(刃具)を念頭に実際の取り組み事例も交えてご紹介いたします。
工具折損とは?
定義
工具折損とは、文字どおり切削工具が加工中に折れてしまう現象です。工具折損が起こると、その後のワークを正常に加工することができないため、折れた工具を交換する必要があります。
原因
工具が折損する直接的な原因は加工中の工具に許容値以上の負荷がかかったためですが、過大な負荷が生じた要因としては、以下の例のようにさまざまな要因が考えられます。
-
工具(刃形・刃数・材質・摩耗状況・取り付け不備等)
-
工作機械(送り速度・回転数・切り込み量・個体差等)
-
ワーク(前工程の加工状況・材質等)
-
切粉(排出不良等)
-
切削油(水圧・液温・種類等)
-
周辺環境(気温・振動等)
実際には、上記のうち複数の条件の組み合わせによって工具折損が発生する場合も考えられます。したがって、それぞれの生産現場の状況を踏まえて、折損の真の原因を分析・特定した上で、適切な対策を講じる必要があります。
工具折損によって起こる問題
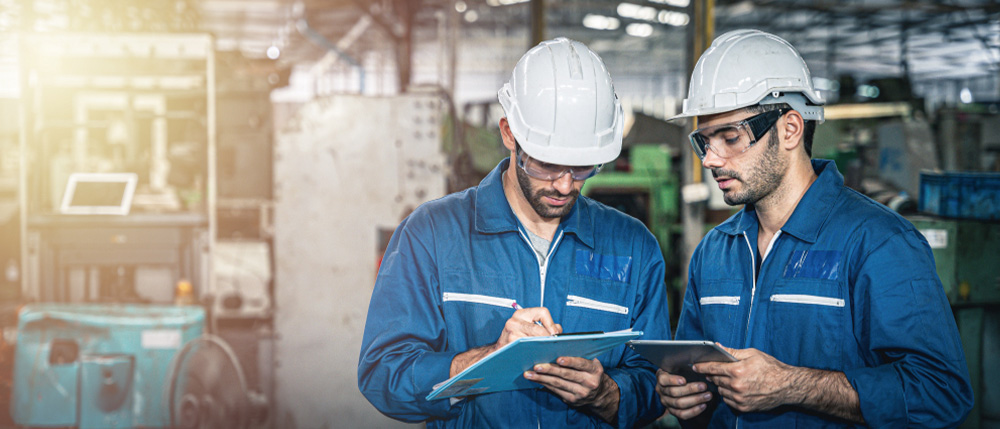
工具折損の原因はさまざまですが、実際に工具折損が発生すると、生産現場にどのような問題がもたらされるのでしょうか。
不良ロスの発生
1つ目は不良ロスの発生です。特に無人化された連続自動加工ラインにおいては、工具折損に気が付かず加工を継続してしまうと、加工品質を満たさない不良品が生じてしまいます。加工不良に気づいて装置を停止させるまでの間、不良品の加工に費やされたコストと時間はすべて無駄になってしまうため、多額の不良ロスが生じてしまいます。
品質確認工数の増加
2つ目は品質確認工数の増加です。工具折損が起こった時刻を明確に特定できないと、一定期間内に加工された疑わしいワークを全数検査して、加工不良がないかを確認しなければならないケースも考えられます。品質管理部門の担当者に余計な作業が発生する上、品質確認が終わるまで一時的に生産を止める場合、さらに稼働率が低下してしまいます。
工具折損を検知する方法
以上のとおり、工具折損を素早く確実に検知することは、機械加工ラインの生産ロスを最低限に抑えるために重要な取り組みです。それでは、実際に工具折損を検知するには、どのような方法があるのでしょうか。以下では、代表的な3種類の検知方法をご紹介します。
接触式センサ(ニードル等)による検知
1つ目は工具に直接センサを接触させることによって、工具が折損していないかどうかを確認する方式です。具体的には、加工終了後にニードル(針)を工具に接触させるセンサを加工機内に取り付けることで、工具が折れていないことを確認します。
接触式センサのメリットとしては、クーラントやオイルミスト等の外乱影響を受けにくく、誤検知が少ないという点があります。しかし、ニードルを接触させるために必要な時間(1から2秒程度)の分だけ、サイクルタイムが長くなってしまうというデメリットもあります。また、ニードルが接触する位置より下の部分で発生した工具の折損や小さな欠けなどを検知することは困難です。
非接触式センサ(レーザ等)による検知
2つ目はレーザ式などの非接触式のセンサによって、工具が折損していないかどうかを確認する方式です。直接的に工具の状態を確認する点は接触式センサと同じ考え方ですが、レーザ照射のような非接触の方法を用います。
非接触式センサのメリットとしては、接触式よりも高速に工具折損有無を判定できるという点があります。デメリットとしては、レーザの照射部分が加工機内のクーラントやオイルミストで汚れてしまうと、誤検知が起こる可能性が高くなる点があります。
間接式センサ(振動センサ・電流センサ・電力センサ等)による検知
3つ目は工具折損が発生する前後の変化をデータとしてとらえることで、間接的に工具の折損を検知する方式です。データを収集するセンサとしては、振動センサ・電流センサ・電力センサ等が用いられます。
このような方法を採用するメリットとしては、工具折損を加工中(リアルタイム)に検知できるため、サイクルタイムの長さに影響を与えない点があります。さらに、データの傾向変化を監視することで、工具折損に至る前の工具の異常兆候を検知できる可能性があります。しかし、工具や加工条件毎に判定基準を設定する必要があり、他の方法よりも専門的なノウハウが必要とされます。
工具折損検知の導入事例
富士電機では、工具折損検知にお役立ていただける製品として、工具診断システム「OnePackEdge MARSYS」を多数の機械加工ラインに導入して参りました。本製品は、切削加工機の主軸モータの負荷電力を専用の電力センサを用いてリアルタイムに測定することで、加工状態を簡単に「見える化」し、工具状態を「診断」できるシステムです。専用の解析支援ソフト「ProHealth」を用いて、ツール/ワーク別に閾値を設定できるため、加工条件に合わせてより正確な診断・検知をすることが可能です。
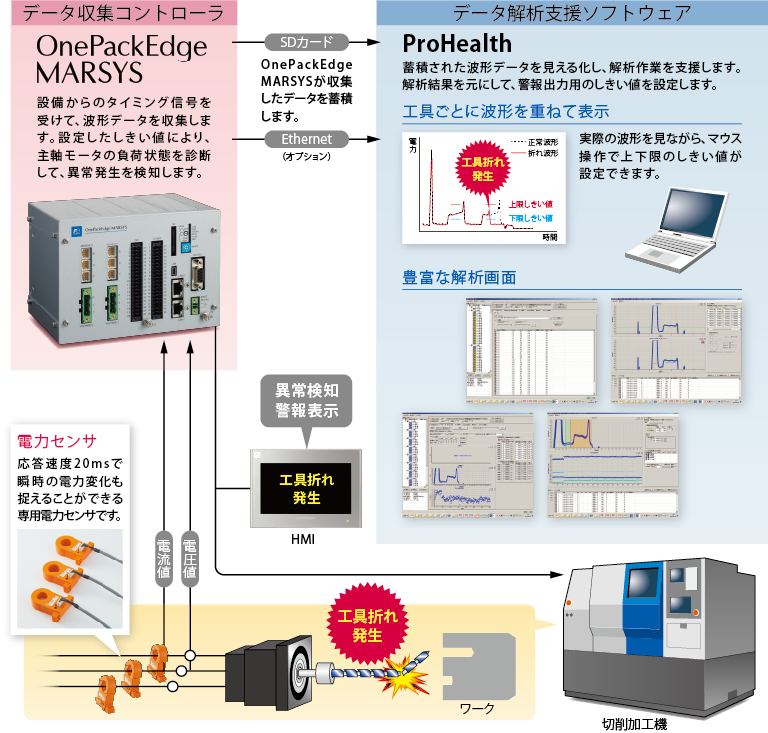
本製品を導入したお客様の生産現場では、工具折損を即座に検知できるようになったため、大量の加工不良ロスの発生や次工程への不良品流出の防止などの効果につながりました。また、従来は必要だった加工後の工具折損診断時間が不要となり、加工サイクルの短縮効果で生産性の大幅な改善を実現できました。
まとめ
ここまで、工具折損によって起こる問題やそれを防ぐための検知方法をお伝えして参りましたが、いかがでしたでしょうか。機械加工ラインにおいて、工具折れを確実に検知する仕組みの重要性について、ご理解頂けたかと思います。
富士電機の工具診断システム「OnePackEdge MARSYS」は、長年にわたってお客様の生産現場で工具折損の検知に貢献しております。本製品にご関心をお持ちの方は、以下のリンクからぜひ富士電機にお問い合わせください。