富士電機製品コラム
FA(ファクトリーオートメーション)
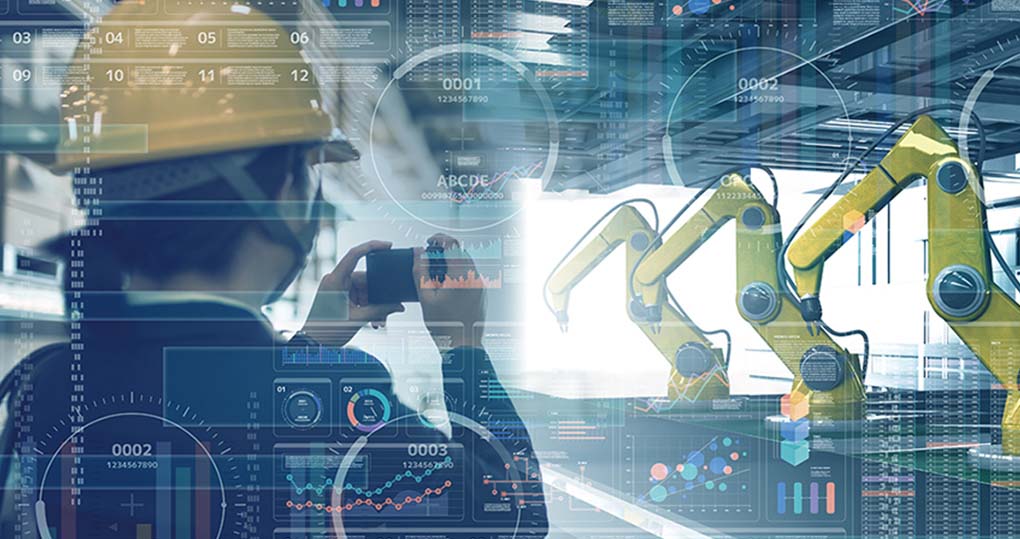
FA(ファクトリーオートメーション)
3つのステップで最先端のFA化を実現
世界屈指のFA大国、日本の自動化のニーズと技術を辿る
ファクトリーオートメーション(FA)とは、文字どおり「工場の自動化」を指す言葉です。工場でモノが製造される工程には、受注、生産、出荷といった一連の流れがありますが、時代の進展とともに、工場に導入されるテクノロジーも変化してきました。
工場の自動化は戦後から始まりました。当初は、圧延機などの複数の加工機械を近くに配置し、鋼板や鋼材を連続的に安定した品質で生産できるように工夫を凝らしていました。日本では1960年前後から工作機械業界でイノベーションが起き、その後に数値制御(NC)による工作機械が量産され、MC(マシニングセンタ)や、第一世代の産業用ロボットなどが工場に配置されるようになりました。
ターニングポイントは、1980年の「産業用ロボット元年」でしょう。自動車産業を中心に、溶接や塗装などで多くの産業用ロボットが導入され、日本は世界屈指のFA大国になりました。さらに、高性能なセンサやコンピュータの登場により自動化も高度に進化していったのです。
また、1980年代半ばから、コンピュータによる設計製図/製造支援システムの「CAD/CAM」が導入され、設計から製造まで自動化の流れが広がりました。
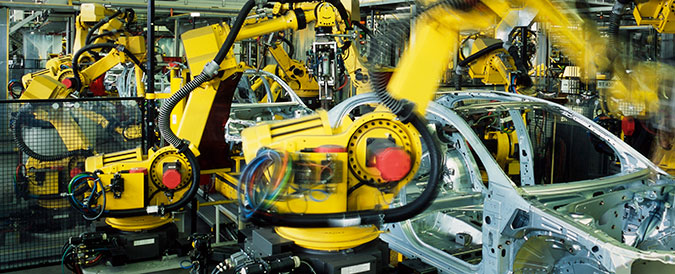
FA化の新潮流! ICT、IoT、AIが「第4次産業革命」を後押し
近年では、ICT、IoT、AIといった技術の進展を受けて、インダストリー4.0、いわゆる「第4次産業革命」が叫ばれるようになり、FA化にも新たな波が押し寄せています。IoTセンサとネットワークの技術の連携によって、工作機械や産業用ロボットなどがネットワークでつながり、エッジ側(工場現場)のデータを自動的に収集できるようになったのです。
そして、収集されたデータは機械の故障検知などの予兆保全に貢献します。また、データの分析結果が現場にフィードバックされ、機械の制御に使われたり、品質の向上に貢献したり、サプライチェーン全体の最適化に役立てられるようになってきました。
現在、工場全体のスマート化(知能化)は進んでおり、より高度な自動化に向かっています。先進的なFAを実現するためには、工程・部門ごとの「部分最適化」ではなく、工場や企業を俯瞰した「全体最適化」がポイントになってきました。
最先端のFA化を実現するための3つの具体的なステップとは?
ここからは、先進的なFAを構築するために、「見える化」「分かる化」「最適化」という3つのステップをご紹介していきましょう。重要なポイントは、高度なFA化をするためには、単にデータ収集するだけで終わらせないという点です。あくまで最終的な目的は、全体最適化を図ることにあるからです。
第1ステップ:見える化
第1ステップでは、まず見える化に着手します。FA化を行う際に最初に必要なことは、現場の状況を把握することです。今、工場の各プロセスで何が起きているのか、それを正確に知るためには、現場からデータを吸い上げなければなりません。
たとえば、現場の設備や機械にIoTセンサを付け、データをリアルタイムに収集していきます。製品を組立・加工する1サイクル単位で、音や振動や温度などの情報を有線あるいは無線で収集し、社内システムに蓄積したり、インターネットを介してクラウドに蓄積していきます。
データを収集したら、それらを整理・加工して、人が理解しやすい形に「見える化」することが重要です。そして、工場の各ライン状況だけでなく、工場全体の生産に関する情報などを統合し、「見える化」すれば、工場全体の効率的な運用・管理に活用できます。
第2ステップ:分かる化
第2ステップは、前のステップで見える化したデータをもとに、生産状況や品質など、現場の課題や問題点の原因を洗い出す「分かる化」の段階になります。
前出のように、すでに収集されたデータには、音や振動、温度など、多くの情報が含まれています。これらの情報から、具体的な解析を行います。
その際に、たとえば「多変量解析(MSPC)ソフト」を使うと、複数の変数から相関をとらえることができ、とても便利です。正常に稼働するラインの各種データから作成した正常モデルと、実データのズレを比較することで、製造時に起きた異常をいち早くキャッチし、品質の改善や歩留まりの向上に大きく貢献します。
第3ステップ:最適化
第3ステップは、前のステップで分かった原因が発生する前にその予兆をとらえ、先手を打って運転条件の変更やメンテナンスなどの対策を実施するなど、継続的な改善サイクルを回す段階になります。生産量や品質の向上に加え、全体プロセスや人員配置、原材料の需要・供給までを含めたサプライチェーンを考慮に入れながら、「QCD」(Quality、Cost、Delivery)をうまく回せるよう現場にフィードバックし、全体最適化を図っていきます。
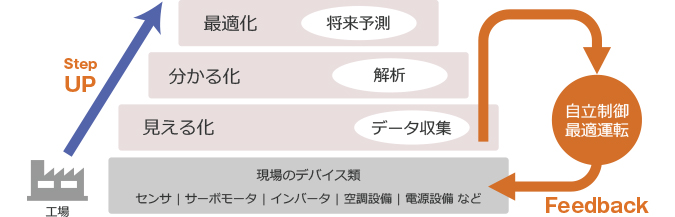
このように先進的なFA化を実現するためには、まず現場の状況を把握(見える化)し、課題となる原因を突き止めて(分かる化)、将来を予測しながら工場全体を継続的にうまく回していくこと(最適化)が最終ゴールになります。しかし、いきなり一足飛びに第3ステップにまで進む必要はありません。図のように、一歩ずつ段階を踏みながら最先端のFA化を進めていくことが重要なポイントです。