富士電機製品コラム
カーボンニュートラルで求められる、工場の取り組みと3つの成功例
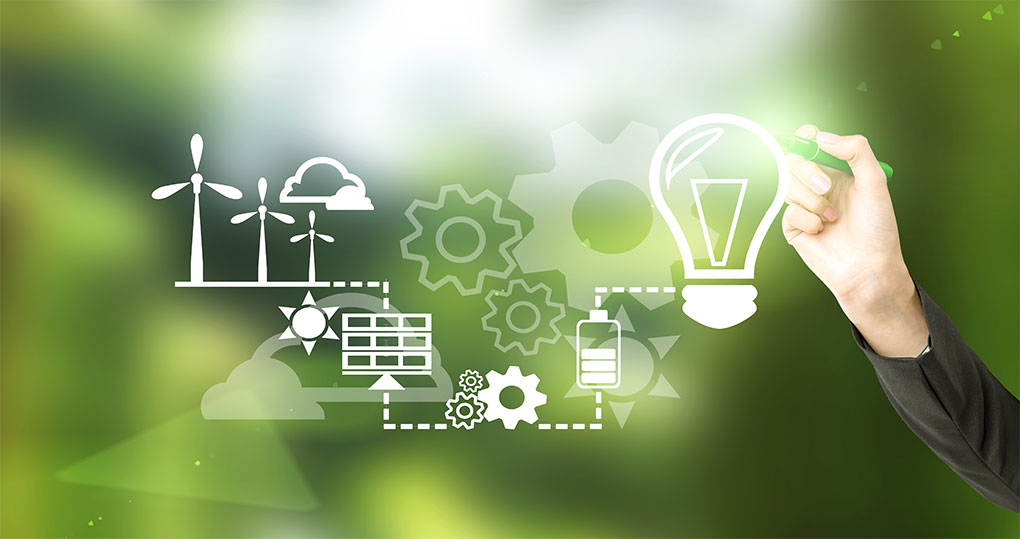
カーボンニュートラル
カーボンニュートラルで求められる、工場の取り組みと3つの成功例
最近よく耳にする「カーボンニュートラル」とは何か?
このところ国内外で自然災害が多発しています。その背景には、気候変動にともなう地球温暖化が関係していると言われています。災害大国の日本では、今後もゲリラ豪雨や猛暑などのリスクが高まるものと予想されます。気候変動の懸念は、国内だけではなく、世界的に高まっており、2015年には温室効果ガス削減に関する協議「国連気候変動枠組条約締約国会議(通称COP21)」で、「パリ協定」が採択されました。本協定では、産業革命以降の気温上昇を2℃未満、可能であれば1.5℃に抑えることが合意されました。
この野心的な数値目標を達成するために、2030年まで温室効果ガス(CO2など)の削減を各国に求めてきました。2021年11月に英国グラスゴーで開催されたCOP26では、1.5℃の達成に近づけるために、企業の取り組みに対して、さらなる努力が求められました。
カーボンニュートラルとは、このような背景の基に「(2050年までに)温室効果ガスの排出を全体としてゼロにする」という取り組みを指すキーワードです。全体としてゼロにするというのは、温室効果ガスの排出量と、植林や森林管理によるCO2吸収量や、CO2回収・貯留技術(CCS)による除去量などを、均衡させてゼロにすることを意味します。
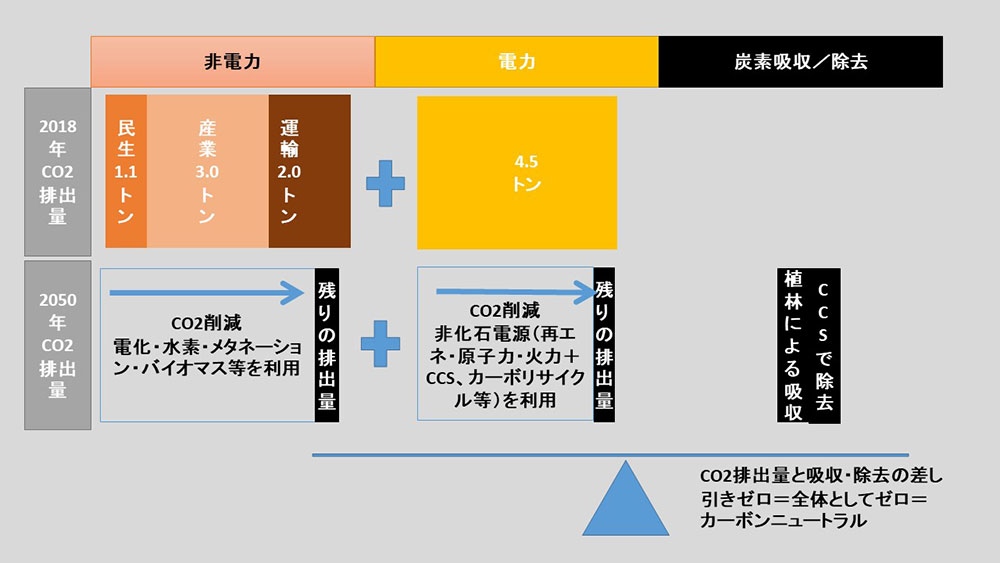
すでに各所でカーボンニュートラルの取り組みがスタートしており、日本では産業分野、製造業を中心として、CO2削減に取り組みを続けてきました。製品をつくる工場の生産プロセスで、電気・ガス・石油などを由来とするエネルギーを使い、大量のCO2 が排出されているため、CO2削減に向けた努力を積み重ねているところです。特に生産設備では、電気や熱の使用量が多く、省エネが求められています。
どこから着手? 工場におけるカーボンニュートラルの現実解
しかし、カーボンニュートラルを進めるといっても、なかなかハードルが高いのも事実です。現状では、従来のエネルギー源を再生可能エネルギーに切り替えると、ドイツのように電気料金が高騰する恐れもあります。また、工場の生産設備を高効率な最新設備に刷新するのも、かなりのコストと労力がかかります。体力のある大企業であれば、対応可能かもしれませんが、中堅・中小企業では、生産設備の刷新は予算的に難しいでしょう。
そのため、いま製造業が取り組める現実解としては、既存の生産設備から発生しているエネルギーロスを減らすことや、電力契約の見直しを図るといったアプローチが取り組みやすいと考えられます。そのためには、まず現場の実情を把握する必要があるでしょう。つまり、「見える化」「分かる化」「最適化」というサイクルが重要です。
まずは、現場のどこの、どんなプロセスで、どのくらいのエネルギーを使用しているのかを可視化し、省エネが可能な個所を洗い出します。その上で、現場の状況に即しながら、どんな取り組みが効果的か、を見極め、すぐに改善できそうなことは手を打ちましょう。そして、より具体的な施策に取り組み、効果測定を実施します。さらに、改善を図り、部分あるいは全体で、エネルギーの最適化を図っていきます。
見える化、分かる化、最適化にあたっては、何も指針や尺度がなく、ただ闇雲にトライしても上手くいきません。そこで、国際標準のISOに則ったエネルギー性能指標「EnPI」(Energy Performance Indicator)を導入するとよいでしょう。EnPIは、「組織が定めたエネルギー性能の定量的な値(または尺度)」で、エネルギーを計る物差しのようなもの。目的に応じた組織の判断で、いくつでも設定できます。ここでいうエネルギー性能とは、「エネルギー使用量やエネルギーの使用(用途)、エネルギー効率に関連する測定可能な結果」と定義され、エネルギー使用量(GJ、kWh)、ピーク電力(kW)、用途別エネルギー使用量、各種エネルギー効率(エネルギー消費原単位、エネルギー変換効率)などを示します。
工場の受配電設備や生産設備などのエネルギーを測定するために活躍するのが、工場のエネルギーマネジメントシステム「FEMS」(Factory Energy Management System)です。FEMSを導入すると、エネルギー使用状況を数値やグラフでわかりやすく見える化でき、EnPIのエネルギー消費原単位(単位エネルギー使用量あたりの生産額、生産数量、延床などのエネルギー使用量)も算出できます。これにより、どの場所や設備、工程を改善すべきか、を理解できるようになります。
ここまで実現できる! CO2削減に成功した3つの工場事例
ここからは、実際に省エネ化を推進し、CO2削減に成功した富士電機の工場での取り組みについて紹介しましょう。
半導体製造の省エネ事例
2パワー半導体チップを生産する山梨工場は、5年間で34%も使用エネルギーを削減することに成功し、平成28年度省エネ大賞の「経済産業大臣賞」を受賞しています。
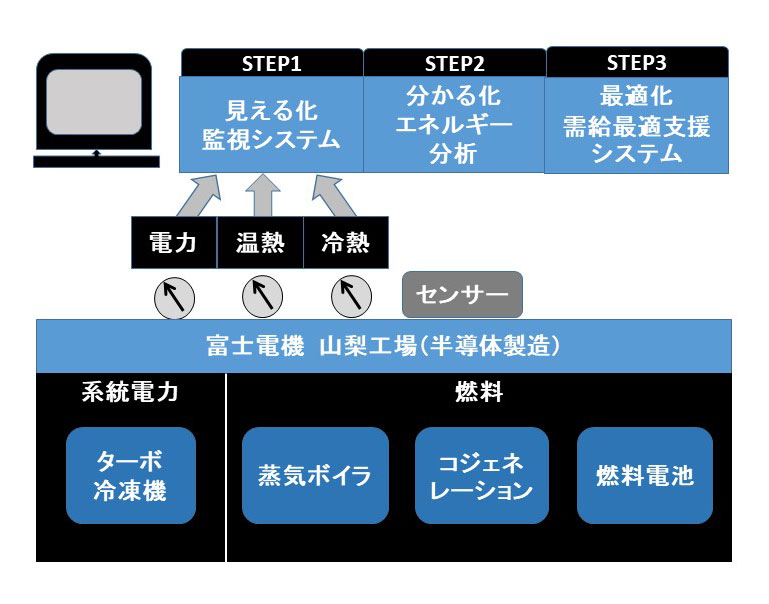
同工場では、電気と熱エネルギーを最適に運用する仕組みを構築しました。 省エネのために「見える化」「分かる化」「最適化」の3ステップでエネルギー管理を進めたのです。センサーでデータを収集し、前出のFEMSを使用しながら、実績データを多角的に分析。また、AIエンジンにより、直近のエネルギー需要を予測し、エネルギーコストを最小化する最適な運転パターンの計画を立案しました。
一方で、落雷や鳥獣被害などで停電し、生産ラインが止まると大きな損失につながるため、止まらない生産ラインも目指しました。何かあったら、遮断機で重要負荷を瞬時に切り離し、途切れることなく、高効率の燃料電池とコージェネレーションの自立運転に切り替えて工場の操業を続ける仕組みを取り入れました。また、最重要の負荷は、UPS(無停電電源)で保護することにより、二重・三重の対策を施しました。
制御機器製造の省エネ事例その1
大田原工場では、IoTなどの先進技術の活用により、QCD(Quality、Cost、Delivery)をリアルタイムで見える化するFEMSのダッシュボードを導入し、生産性を5%向上することに成功しました。このダッシュボードによって、生産ラインや工場全体の生産情報から日々の経営情報までを一元管理できます。工場内のカメラ映像やエネルギー使用、生産状況、品質の情報などを横串で閲覧することで、それぞれの因果関係もわかりました。
また、稼働監視システムにより、生産タクトタイムのバラつきも把握。バラつきの原因は、監視カメラ映像と稼働監視データを分析することで特定できました。例えば、カバーのネジ締め工程では、ネジ供給設備にボトルネックがあることを発見し、プロセス改善を試みました。このように生産性を向上することが省エネにつながるのです。いま海外拠点でも同じダッシュボードを導入し、相互に情報を交換しています。今後も継続的な改善を図り、より良い製品をジャスト・イン・タイムで提供できる体制を整備していく予定です。
制御機器製造の省エネ事例その2
2019年度「省エネ大賞(省エネ事例部門)」を受賞した埼玉県鴻巣市の吹上工場は、東京ドーム3個分の敷地面積があります。発電設備は市内世帯の約2倍にあたる10万世帯の電力を一度に賄える能力を持っています。同工場が省エネに取り組んだ結果、従来の1/4にあたる省エネ効果-25.7%(エネルギー効率)を達成しました。
吹上工場のアプローチは、電力予測システムの活用による省エネ化です。生産計画の見直しが必要な電力のピークカットやピークシフトではなく、ピークチェンジを組み合わせた電力制御を行っていることがポイントです(https://www.fujielectric.co.jp/fcs/on-line-factory/)。過去の蓄積データと、状況や季節要因などの情報を加味し、契約電力の超過前に自家発電に切り替えるピークチェンジを導入しました。それでも電力が足りない場合は、優先順位の低い空調を調節したり、照明などの負荷から順番に自動停止させたりして、契約電力を超えないように制御しました。
また、工場の天井が高く、空調の効率が悪い建屋は、生産ラインをテントブースで囲むことで、部分的に空調の良い作業区域に変えました。さらに、荷物の搬入出時に扉を開閉できる「乗り移りクレーン」を配置し、室温変動を抑える工夫も凝らしました。これらの小さな積み重ねが、大きな省エネ効果につながりました。
ここで取り上げた3つの事例の詳細については、富士電機のBlue Navigationをご覧ください。