富士電機製品コラム
徹底解説! 工場の脱炭素の取り組みを加速する「SHIFT事業」
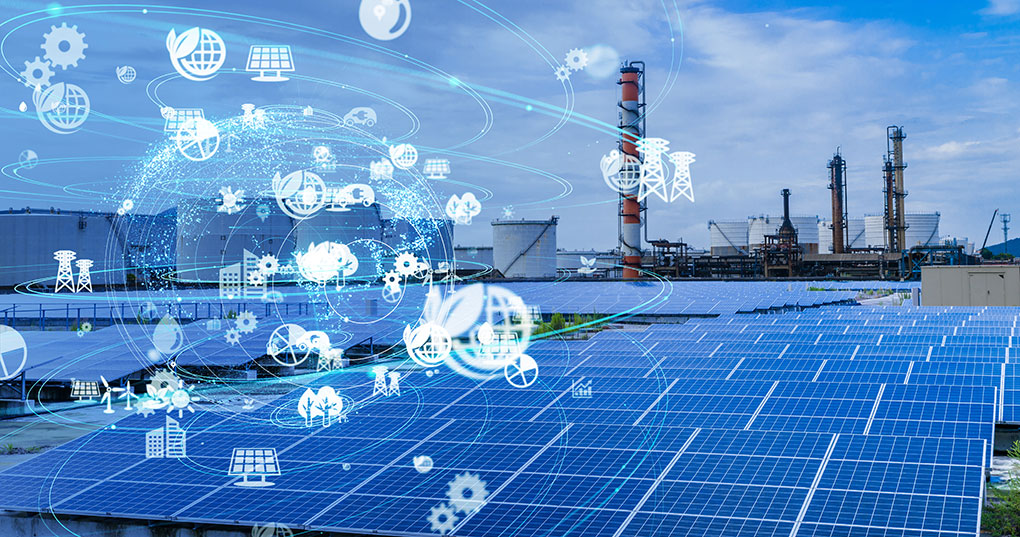
カーボンニュートラル
徹底解説! 工場の脱炭素の取り組みを加速する「SHIFT事業」
-
脱炭素化によって、企業が得られるビジネス面でのメリットは?
-
SHIFT事業の3つの柱で脱炭素化を! 補助金のスキームと留意点
-
脱炭素に向けたアプローチは、エネルギーの「見える化」から
-
部分最適による小さな積み重ねの省エネから、全体最適によるトータルエネルギー削減へ
脱炭素化によって、企業が得られるビジネス面でのメリットは?
2015年に温室効果ガス削減に関する協議「国連気候変動枠組条約締約国会議(通称COP21)」が開催され、そこで「パリ協定」が採択されて以来、脱炭素社会に向けた取り組みが世界各国で進んでいます。
その理由の1つとして、気候変動の影響が顕在化していくなかで、環境(Environment)・社会(Social)・ガバナンス(Governance)に配慮する企業に対して行われる「ESG投資」が企業価値につながり、新たな取引先やビジネスチャンスにも結びつく点が挙げられます。
脱炭素化は、企業にとって地球環境を守ることはもちろん、省エネ化につながるため、電気・熱や燃料のコストが削減されるという直接的なメリットもあります。国内では、菅政権が策定した「エネルギー基本計画」や「グリーン成長戦略」を引き継ぎ、現在の岸田政権が「新しい資本主義」の重要な目玉政策として、脱炭素社会を経済成長の起爆剤につなげようとしています。現在、日本では2050年に温室効果ガス排出を全体でゼロにするカーボンニュートラルを達成すべく、中間目標となる2030年度までに温室効果ガスを46%(2013年度比)削減するための努力を続けているところです。
しかし、これらは一朝一夕では実現できない高い目標であることも事実です。脱炭素化は最終ゴールですが、そのためには燃料の転換や新しい設備への更新などが必須であり、かなりコスト面で負担が掛かってしまいます。そこで国としても、企業の脱炭素化を後押しするための、制度や補助事業を数多く用意しています。
SHIFT事業の3つの柱で脱炭素化を! 補助金のスキームと留意点
いま代表的な補助事業の1つとして注目されているのが、環境省が令和3年度から令和7年度まで進めている「工場・事業場における先導的な脱炭素化取組推進事業」(以下、SHIFT事業)です。事業の主な目的は「業務部門・産業部門における2030年目標や2050年目標の達成に向けて、工場・事業場における先導的な脱炭素化に向けた取り組みを推進すること」「脱炭素化に向けて更なる排出削減に取り組む事業者の裾野を拡大すること」です。
そのために本事業では、次の3つに取り組んだ企業に対して補助金を提供してくれます。
【1】脱炭素化促進計画の策定支援
CO2排出量50t以上、3000t未満の工場・事業場を持つ企業などに対し、排出量を削減できる余地があるかの診断と、脱炭素化促進計画の策定を支援するのもの。補助率は1/2、補助上限額は100万円です。事前準備の診断や計画策定のハードルが高いと思われる中小企業を主な対象にしています。
【2】設備更新に対する補助
【1】の脱炭素化促進計画に基づいて、自社の設備を更新する場合に補助されるもので、補助率は1/3です。補助金の上限設定によって、1億円(設備補助A)と5億円(設備補助B)の2パターンがあります。設備補助Aの条件は「工場・事業場単位でCO2を15%削減、または主要なシステム系統で30%削減できるもの」。一方、設備補助Bは補助金の上限が高いぶん条件も厳しくなり、「ガス化または電化等の燃料転換」「CO2排出量を4000t-CO2/年以上削減」「システム系統でCO2排出量を30%削減」を満たす場合に適用されます。
【3】CO2排出量の算定・取引・事例分析
設備更新の補助を受けたら、CO2排出量の算定や分析などのために、第三者機関で結果を検証してもらう必要があります。つまり、補助金を受けて終わりではなく、その成果もしっかり点検されます。もし削減目標を達成できなければ、ほかの本補助金採択者などから排出枠を購入することになります(逆に、目標以上を達成できれば自社の排出枠を売れます)
SHIFT事業の大まかな流れを次に示します。
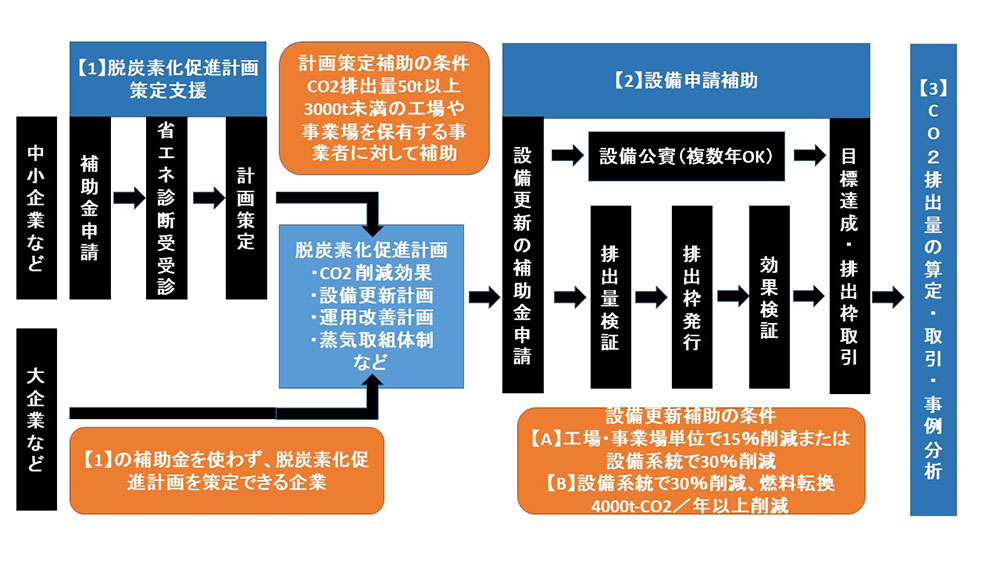
脱炭素に向けたアプローチとしては、自社工場の利用エネルギーを再生可能エネルギーに切替えたり、生産プロセスの効率化によって使用エネルギーを削減したり、設備自体の省エネ化を進めるといった施策が挙げられます。
このなかで最も取り組みやすいのは、自社工場で使っている設備の省エネ化でしょう。省エネ化のために重要なことは、使用エネルギーの「見える化」です。まずは生産設備の、どこに、どのぐらいのエネルギーが使っているのかを俯瞰し、無駄が潜んでいそうな部分や工程を炙り出していきます。
その上で、従来と同様の生産工程の効率化を図ったり、電気・熱のエネルギーロスを減らす工夫を凝らしたり、低消費な最新設備を導入するなど、具体的な施策を練っていきます。例えば、工場の熱設備ならば、ボイラやタービンの余剰の熱・蒸気、電気・水・空気などのデータを各種センサーで計測したうえで、再利用できそうなエネルギーを把握し、最適な運用を行って省エネを実現します。ヒートポンプによって、排熱を利用することも有効でしょう。
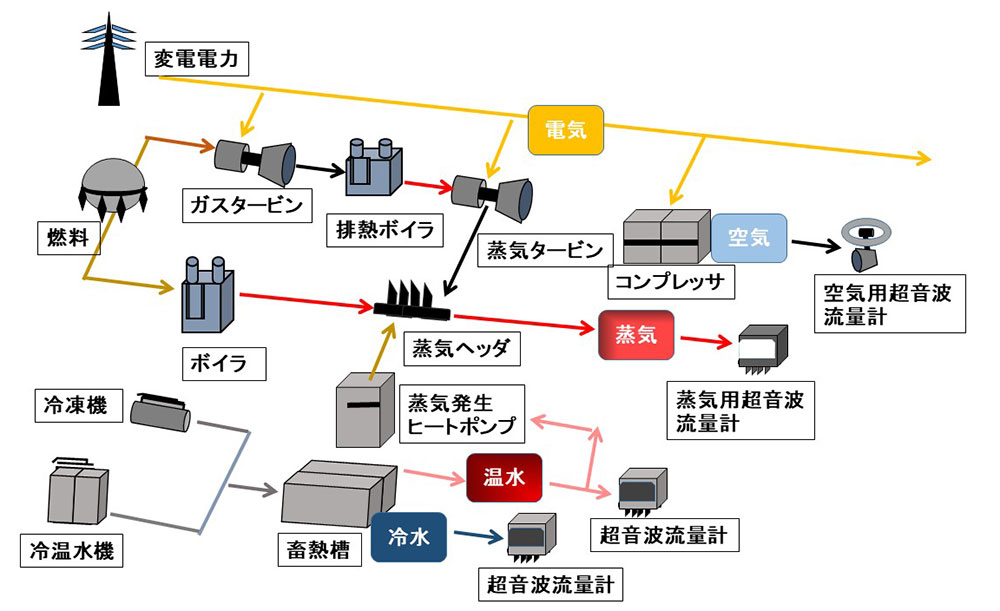
生産設備の省エネ化を進めたら(あるいは、同時並行で)、自社工場を稼働させるエネルギー自体を見直します。太陽光や風力などの再生可能エネルギーで賄えるかどうか、創エネルギーも検討しましょう。いわゆる「自家消費太陽光発電」(以下、自家消費)を導入すれば、CO2の環境問題はもとより、電気料金の削減にもつなげられます。
電力使用量がピークになる時間帯の電力量を制御すれば、基本料金を減らせます。基本料金は、主に単価と契約電力で決定されます。契約電力は、「当月を含む過去1年間の各月の最大需要電力(30分ごとに計量された月間で一番大きい値)のうち最も大きい値」がベースになるので、その時間帯に太陽光発電で電力を補填すると、ピーク電力を抑えられて、結果的に基本料金を下げられるのです(逆に、少しでもオーバすると1年間高い基本料金になってしまいます)。
また、自家消費に蓄電池を併用すると、蓄電した電力を使って消費の波を平準化できます。電気料金の削減という経済的なメリットのほか、災害時の備えという観点から、事業継続性(BCP対策)にもつながるでしょう。
しかし、自社のエネルギーをすべて再エネで創りだすことは、現実的には難しいかもしれません。CO2削減の施策を打っても目標達成が困難ならば、排出の削減量・吸収量をクレジットとして国が認証する「J-クレジット制度」などを利用し、他事業者の削減クレジットを購入することで、排出量を間接的に埋め合わせる選択肢もあるでしょう。
部分最適による小さな積み重ねの省エネから、全体最適によるトータルエネルギー削減へ
いずれにしても、最終ゴールの脱炭素化をめざす過程においては、前出のようなエネルギーの「見える化」が第一ステップになります。つまり、「改善のためには、まず原因特定から始めよ」ということです。その際に役立つのは、電気・熱の利用を「見える化」「分かる化」「最適化」するためのFEMS(Factory Energy Management System)です。
最初は省エネのために「部分最適化の小さな積み重ね」から始めることになりますが、最終的には「工場のライフサイクル全体にわたるエネルギー最適化」までつなげることが大切です。そのために、将来を見据えて、横断的な選択肢を揃えるメーカーのソリューションを選ぶことが大きなポイントになるでしょう。