富士電機製品コラム
予知保全を導入するメリットとは
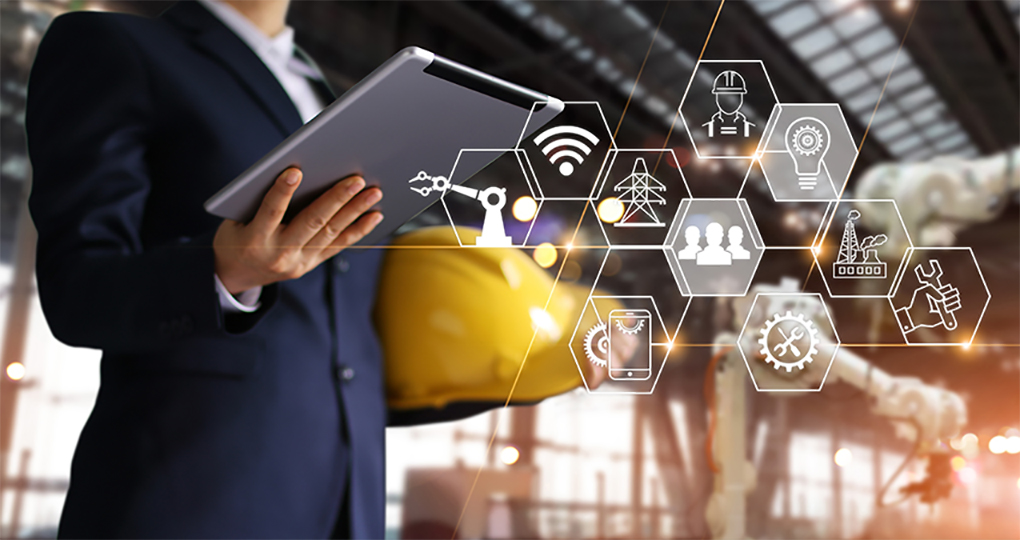
予知保全を導入するメリットとは
AI(:artificial intelligence = 人工知能)に対する注目や需要は、かつてないほどに高まっています。各界においても、AI技術を用いて業務効率化や生産性の向上を図る動きが加速しています。この現象は、モノづくりの現場である製造業おいても例外ではありません。
AIは既存業務を効率化することが可能ですが、予知保全においても、IoTやAIは非常に大きな力を発揮します。
この記事では、予知保全を導入するメリットを紹介。予知保全導入に対する財務面から見たメリットだけでなく、現場における各恩恵についても、分かりやすくお伝えします。
予知保全導入による財務面から見たメリット
他の記事でもご紹介しましたが、予知保全は故障が発生してから対処する“事後保全”や、定期的に点検や部品交換を行う“予防保全”よりも新しい保全の考え方です。
予知保全導入は生産性の向上につながる
事後保全では、故障により生産機器・設備が停止しており、修理や部品交換が終了するまでは、いわゆる「ダウンタイム」が発生します。予防保全においても、想定外の故障やトラブルを確実にとらえることが出来ないため、予期せぬダウンタイムが発生する可能性もあります。
その点完全に機能すれば、故障の予兆をほぼ確実につかむことの出来る予知保全は、他の2つの保全にはない大きなメリットがあると言って良いでしょう。「稼働 = 業務活動」といえる製造業において、ダウンタイムを最小限にとどめることは、企業に高い生産性をもたらします。
生産機器・設備の消耗部品の在庫数や発注頻度をさげられる
予知保全のメリットは、生産性の向上だけにとどまりません。予知保全は、生産機器・設備の状態に応じて、部品発注や補充が可能な保全。他の保全行為と比較して、交換部品の在庫数や、修理や交換工賃を大幅に削減することが可能です。
予知保全は保全人員の削減につながる
予知保全はモニタリングを、保全システムにある程度任せることができるという利点があり、事後保全・予防保全に比べ監視・観測の面でも優位です。つまり予知保全は、機器・設備にアラートが生じた時にのみ人員を割けば良く、保全に対する人件費においても他の保全に比べ少なくて済むのです。
予知保全の導入で生産現場に生じる4つのメリット
このように予知保全は、財務的なメリットが見込め企業経営上のメリットをもたらします。それだけではありません。予知保全は工場など生産現場においても大きなメリットをもたらすのです。具体的に、どんなメリットがあるのか見ていきましょう。
生産現場における設備の部品交換頻度を適切にできる
製造業では、生産現場の設備保全は必ず行わなければならない行為。保全行為において、修理やメンテナンス時の部品交換や修理などに掛る「時間コスト」は、切っても切り離せません。
ここでご注目いただきたいのが、予防保全と予知保全では部品交換に対する周期が異なる点。定期メンテナンスを行う予防保全の場合、定められた周期やタイミングで部品交換などの保全行為を行います。つまりまだ十分に使用可能な部品であっても、トラブル予防のため交換を行うので、無駄が発生してしまう訳です。予知保全は、異常を検知してから保全行為を行うので、消耗部品を寿命ギリギリまで使い切ることが可能です。
保全に従事する担当者を大幅に削減できる
トラブルが生じてから保全行為が発生する事後保全、定期的にメンテナンスを行う予防保全と違い、異常を検知してから保全を行うのが予知保全です。この各保全行為の違いは、生産現場における保全人員の在り方を大きく変えます。事後保全・予防保全では、どうしても現場に保全担当者を配置せねばなりません。
予知保全の場合、最低限の人数でモニタリングを行えば、機器や設備の状況を把握することが出来ます。言い換えれば、異常を検知後、規模に合わせ無駄のない人員を適切な時期に配置すればよいといえるわけです。人員は企業にとってもっとも大事な資産であり、大きな経費がかかる存在でもあります。予知保全を導入すれば、この貴重な人員をより多く製造工程に充てることができ、現場の稼働率を向上させることが出来ます。
トラブル時におけるスタッフの負担を最小限に抑えることができる
定期的なメンテナンス(予防保全)を行うことで、生産設備のトラブルを防ぐことは出来ますが、トラブルの原因は部品の不具合だけではありません。生産設備のトラブルの原因は、多岐に渡ります。そのため、予め想定していない事柄が原因で故障が発生した場合、どうしても調査に時間がかかります。生産現場では多くの場合、保全行為を含むいくつもの業務を兼任していることが多いため、ダウンタイムが発生すると、著しく生産効率が低下します。ひとたびトラブルが発生すると、通常時と同じような生産効率を維持させるためには、現場スタッフの負担はかなりのものとなります。
予知保全であれば、生産現場の機器や設備にトラブルが生じる前に、通常運転時とは異なる振動や温度などを感知することで、問題の発生源をいち早く探知。機器や設備が停止してしまう前に、対処することも出来ます。予め原因や対処の方法が分かっているのであれば、適正な人員を最適なタイミングで動かせば良くなります。結果的に、スタッフの負担も少なくて済みます。
保全担当者の教育コストを削減することができる
長期間かけて保全技術を培ってきたベテラン担当者であれば、直感で修理箇所がわかったり、故障前に対応できることがあるかもしれません。けれど、知識や経験・ノウハウを持たない人材だとそうはいきません。なにより、同じぐらいの技術を身につけるには、それなりの時間と教育コストが必要です。
保全担当者に対する教育コストを、大幅に削減できるのが予知保全です。予知保全が完全に稼働していれば、生産ラインにおける異常個所が早く明確にわかります。そのため、保全担当者の教育に時間とコストを大幅に掛ける事なく即戦力化できるのです。
生産現場のスタッフは多忙で、通常の業務の他に何役も担っているのが常です。そんな中、保全業務の知識やノウハウ伝承に割く時間や労力を削減できるのは、大きなメリットになるはずです。
このように予知保全を導入し稼働させることで、ベテラン担当者でしか行えなかった保全対処が、新人や部署替え間もないスタッフにも可能になります。それ以外にも、人の感覚だけでは気付くのが難しい機器・設備のトラブルを未然に予知できるため、生産現場は新たな保全ノウハウという財産も得ます。
予知保全システムを導入した場合の例
切削加工機の工具保全を最適化する
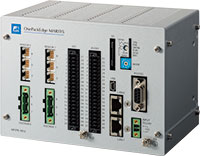
切削加工機の加工状態を簡単に「見える化&診断」できるOnePackEdge MARSYS
お客さまのお悩み
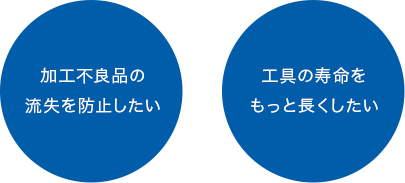
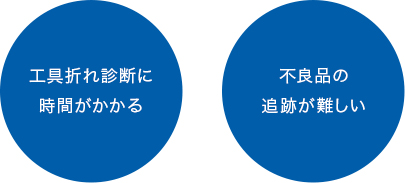
問題点
-
1.
切削工程における「工具折れ」「カケ」などにより、一定数の不良品が流出。
-
2.
工具寿命の把握が難しく、定期的に交換。工具の寿命が短い。
-
3.
工具診断を、接触式/非接触式センサで加工終了毎に確認。診断に時間が掛かる。
-
4.
不良発生日時の特定が難しく、不良品の追跡が困難。
富士電機の提案
切削加工機の工具診断システム「OnePackEdge MARSYS」の導入により・・・
-
工具の異常をデータで検知し、不良品の発生を抑える。
-
生産ラインの稼働データを蓄積し、工具の使用を限界まで引き上げる。
-
常時工具の診断を実施、加工後の工具診断時間を不要に。
-
製品加工のデータをワンパッケージで蓄積、不良品の追跡を容易に。
予知保全のシステム全容
予知保全システムで、波形データを収集。解析支援ソフトで解析することにより、工具の状態を「見える化」する。これにより、異常傾向を抽出。警報出力用のしきい値を決定し、継続的な監視と改善を実施。切削加工機の、安定操業・工具費削減・サイクルタイム短縮を行う。
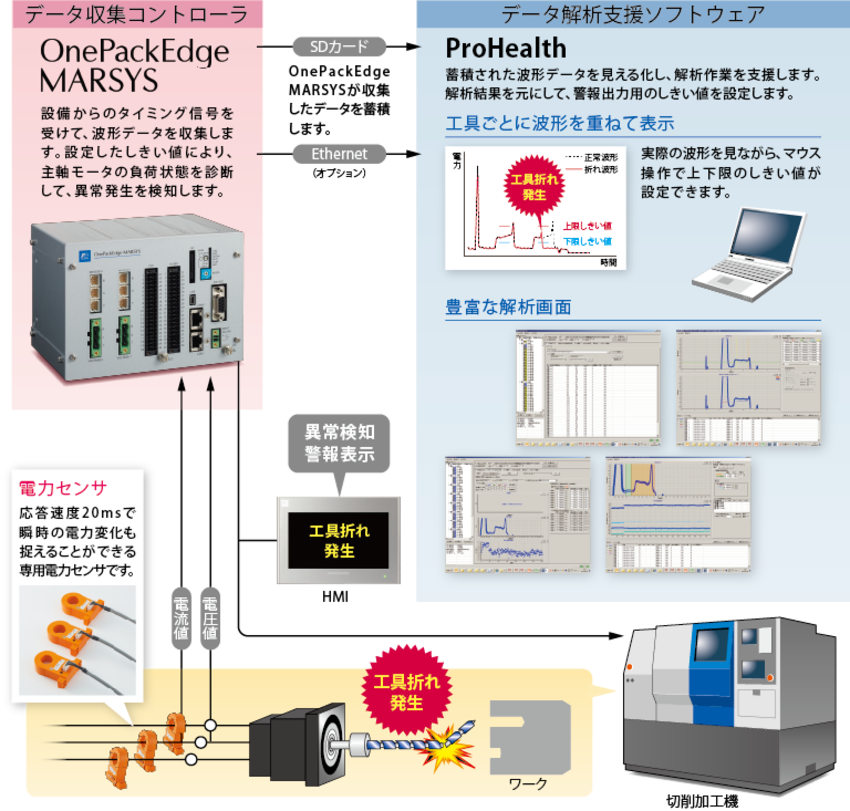
予知保全システムの導入効果
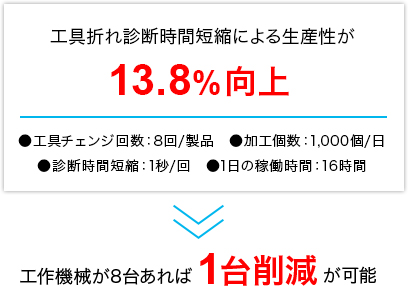

まとめ
予知保全は、様々なメリットを財務面だけでなく生産現場においてももたらします。しかしメリットだけでなく、システム導入にはイニシャルコストとランニングコストの双方が必要であることも忘れずにお伝えしなくてはなりません。
予知保全を生産現場に導入するか否かの判断は、導入コストと削減できる費用を踏まえた費用対効果次第であるといえるでしょう。
生産現場では様々な機器・設備が稼働しているので、優先順位を設け、大幅なダウンタイムが生じる可能性があるものから順次、予知保全を導入しても良いかもしれません。
富士電機では、お客さまの生産現場において「どの程度の保全人員を削減可能か?」「具体的な工数削減は?」といったシミュレーションを行います。システム導入におけるPoC(概念実証)にも対応していますので、お気軽にご相談ください。