富士電機製品コラム
予知保全に最適な AIと導入のメリット・デメリット
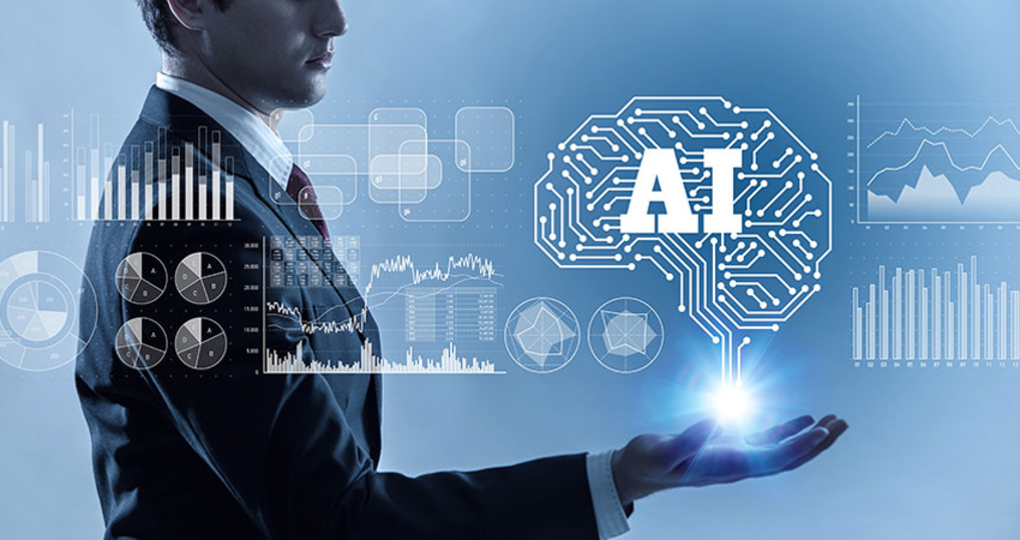
予知保全に最適な AIと導入のメリット・デメリット
止まることが許されない「ものづくり」の製造現場において、AIによる「予知保全」が注目を集めています。生産保全(:Productive Maintenance)は、設備を完全な状態に保つことであり、設備における通常と異なる異変を見つけ出す行為でもあります。
この保全に、AIはどのような形で関わり役立っているのでしょうか。この記事では、予知保全とAIの関係性やAIを活用するための方法を、ご説明いたします。
予知保全とはどんなものか?
予知保全は、製造設備を継続的に監視し、データを収集・解析することで機器や設備の劣化や不具合を予知・予見する行為です。予知保全を行うと、機器や設備を常に監視し、不具合の兆候を察知して故障が生じる前に保全し、生産ラインを止めることなく円滑に稼働させることが出来ます。
予知保全の定義につきましては、以下の記事でも詳しく解説しています。
AIを導入することで生産性を高める時代に
初期の予知保全は、人を介して行われていました。生産ラインに携わるベテランのエンジニアや作業担当者が、経験から得たノウハウや感覚に基づき、機器や設備を構成する部品の状態をチェックし交換時期を決めていたのです。
しかし昨今進む作業担当者の高齢化に伴い、保全に関わるノウハウや経験を持ったベテランのスタッフが不足。マンパワーだけに頼ることない、AIを利用する方法に注目が集まってきているのです。
AIの活用がもたらす生産現場における恩恵
AIを活用すれば…
-
製品の品質を改善
-
稼働率の改善
-
歩留まりの改善
-
リードタイム短縮
-
作業人員の適切な配置
-
ノウハウのデジタル化
-
メンテナンスの効率向上
が可能になります。
AIは、従来の機械学習に加え「ディープラーニング」と呼ばれる学習手法により、高い能力性能を習得することが出来ます。高い性能を持ったAIであれば、従来の人に頼った保全に替わって、生産ラインの故障やトラブルを的確に見つけ出すことが可能です。
ディープラーニングとは?
ディープラーニング(:Deep Learning)とは深層学習のことで、頭文字を通ってDLと記述されることもあります。ディープラーニングは、人間が仕事や様々な活動を通じて自然に学習していく行程を、コンピュータに学習させることができます。
ディープラーニングは、人工知能であるAIを加速度的に発展させる技術です。学習させるデータを更新さえすれば、AIは変化に追随していきます。
この技術の出現により、従来難しいとされていた分野・場面においても、次々にAI導入が進むようになりました。
予知保全システムに最適なAIのアルゴリズムとは?
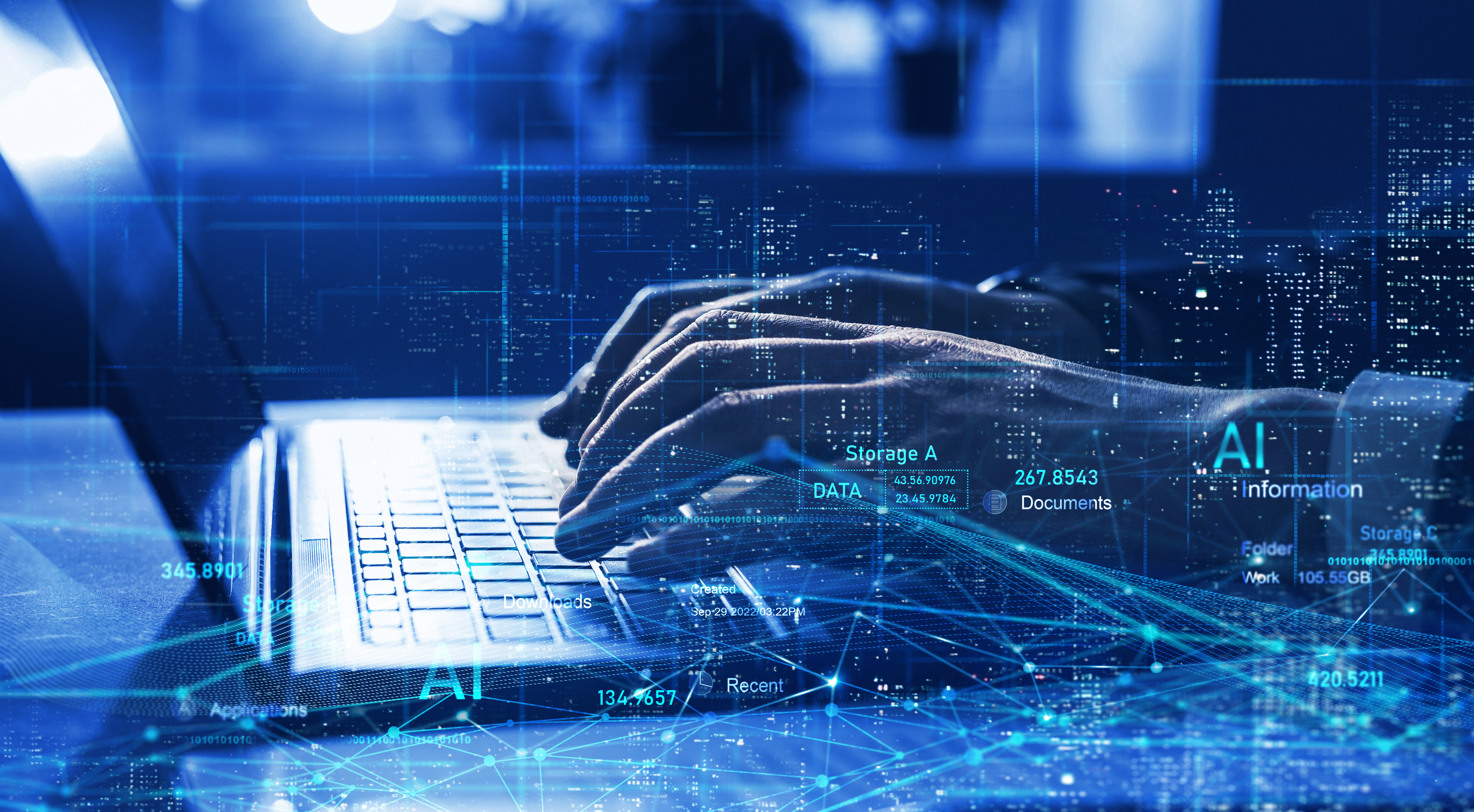
このように優れた能力を持つAIですが、実務レベルで活用するには、利用する側が人工知能に取り扱わせるデータを理解し、その特徴を把握しておかねばなりません。
AIを始め、コンピュータに計算をさせる手順(やり方)のことを、「アルゴリズム」といいます。ディープラーニングでは画像認識が利用されることが多いのですが、予知保全で活用するAIには、時系列データに対して単純な上下限の閾値(しきい値)を引いて判断するようなアルゴリズムでは不十分。
正常時の波形をモデル化して、その波形に対して「いつもと違う」という特徴量(正常時との乖離の程度)を抽出できるようなアルゴリズムが必要になります。
予知保全では画像ではなく時系列データを元に判断する必要がある
予知保全の領域においては、画像ではなく対象となる機器や設備に設置したセンサで得た時系列データが重要な役割を果たします。
予知保全で良く用いられる代表的なセンサとして、振動・温度・圧力・電流のセンサがあげられますが、ここでご留意いただきたいのは、センサの設置箇所やデータ計測の方法。
対象となる機器や設備によっては、複数箇所の測定が必要な場合や、測定目的に応じて最適な性能のセンサを選定するなど臨機応変な対応が必要です。
予知保全の目的は、対象となる機器類が「正常か否か」を知ることです。予知保全システムにAIを活用すれば、従来の単純な上下限の閾値による判断だけでなく、時系列で変動する波形をモデル化できます。
このモデル化によって、収集したデータが「いつもと違う」波形かどうかが分かるようになり、正常/異常が判断できるようになるのです。
時系列データの特徴
時系列データの特徴として、「時間と規則性の関係」があげられます。この時系列データの特徴を踏まえれば、周期・周波数・振幅・値の平均やばらつき方等、監視するポイントを定めやすくなります。
予知保全にAIを導入するメリット
予知保全を完全な形で実施するには、機器・設備から収集したテータを分析し、そこから得た情報をもとに未来予測を行う必要があります。これまでは、このような工程はすべて人に頼って行ってきました。
ここにAIを導入すれば、機器・設備から得たデータを誰でも簡単に利用することが可能になります。以下の記事では、予知保全システムにAIを導入するメリットについて、より詳しくご説明したいと思います。
予知保全にAIを導入すれば大きな損害を事前に回避可能
予知保全システムにAIを取り入れることで、機器・設備からの情報を常に監視。そこで得たデータをAIが解析することで、不具合やトラブルの予兆を常時知ることができます。つまり、AIを導入すれば、生産ラインの状態確認を自動化することが出来るのです。
生産ラインを構成する、機器・設備のトラブルの発見が遅れると、故障が生じる恐れがあります。故障となれば生産ラインは停止し、企業は部品交換よりもはるかに大きな代償を払わねばなりません。
AIが生産ラインの機器・設備の状態を正確に把握できれば、人件費を減らしながら部品交換の時期をより正確に見極めることが出来るようになります。
高い生産性の継続的維持が可能
定期的に部品交換やメンテナンスを行う予防保全だけでは、稼働状況の変化等により突発的な故障が生じた場合、生産ラインの停止を防ぐことが出来ません。このような原因不明のトラブルは、究明に時間が掛かり、長期に渡るダウンタイムが発生します。
AIによる常時監視体制があれば、機器・設備の不具合を事前に察知。故障が生じる前に対処することで、生産活動を維持。生産ラインのダウンタイムを限りなく少なく出来ます。
コスト面においても、故障の予兆が生じるまで部品・その他の設備を稼働させられます。これにより、使える部品を交換する無駄をなくし、従来の保全行為と比べて運用コストを削減させられます。
人件費削減や人材不足の問題も解決
従来の予知保全は、経験ある技術者のノウハウに頼って対応が行われてきました。昨今の少子高齢化のあおりを受け、このような熟練の経験とノウハウを持った技術者は減少の一途をたどっています。
AIを導入し保全の自動化が促進されると、センサで対象機器からデータを取り込むなど、点検プロセスを簡略化できます。また点検内容においても、AIが未熟な技術者の判断を助けてくれるので、ベテラン技術者と遜色ない判断を行えます。
さらに、手作業による誤検知防止の工数の削減・人材育成に必要な教育費の削減など、保全に必要な全体コストの削減にも繋がる他、業務効率化の向上にも寄与します。
予知保全にAIを導入するデメリット
このように保全システムへのAI導入には、数多くのメリットがありますが、デメリットも無いわけではありません。
ここからは、予知保全にAIを導入するデメリットについて、詳しく見ていきます。
高品質な学習用データ計測が求められる
AIをうまく活用させるには、学習用のデータを準備し人工知能を教育していかねばなりません。予知保全システムでAIを使うのであれば、生産現場からの高品質な学習用データ収集は必須です。
具体的には、対象となる機器や設備に情報収集を行うセンサを設置し、機器類の状態を把握。次いで、入手したデータを学習用データとしてAIにインプット。機器や設備の稼働に応じて、常に学習を繰り返していく必要があります。
予知保全では規模によりレベルを区分する
予知保全ではシステムの規模により、対象レベルを区分します。各レベルは、分析が必要なデータの種類が異なるため、注意しなければなりません。
<予知保全で対象となる主なレベル>
-
工場レベル
-
生産ラインレベル
-
機械(マシン)レベル
-
部品レベル など
工場レベルのように、規模が大きくなればなるほど全体的なデータが重要になります。逆に、部品レベルなど、規模の小さくなると「音」「振動」「動き」のような精密なデータが重要となります。
AIには目的に合った学習データが必要で、計測データが目的と合致しないと役にたちません。AIを保全システムに導入し活用するには、保全対象を明らかにし、目的に応じたデータ収集対応が求められるのです。
膨大なデータ量を分析するにはコストが掛かる
予知保全にAIを導入し完全な形で稼働させるには、機械学習の他、ディープラーニングで分析力と判断力を身につけさせる必要があります。
先に述べたように、予知保全で取り扱うのは「時系列データ」です。時系列データは、機器や設備に取り付けた、温度・振動などの各センサから得たデータを蓄積。それぞれの規則性を把握しつつ、正常/異常を比較できるよう数多くのデータが必要です。
時系列データのように、膨大な量のデータを解析処理するには、精度の高いソフトウェアとハードウェアが必要となります。またソフトとハードの連携による動作確認も求められることから、導入や精度改善のためのコストもそれなりに掛かります。
AIのブラックボックス「根拠不明の判定」問題
ディープラーニングは、様々なビジネスプロセスを自動化してくれる人工知能(AI)技術です。AIは膨大なデータを自ら学習し、答えを導き出すという特性を持ちます。それ故、「思考のプロセスが人間には分からない」という問題点を孕みます。
この問題は、AIのブラックボックス(人間には根拠不明の判定)と呼ばれています。
例えば…
人間の思考レベルは、数次元が限界。一方で現行の人工知能は、数十から数百次元のレベルで物事を思考することができます。要は、ディープラーニングによりAIが導き出した答えが、どうしてその答えに至ったかという過程を、我々人間では追いきれないのです。
人は本質的に、根拠の分からない判定結果を受け入れがたいものです。経験や実績・ノウハウが重んじられる「ものづくり」の現場では、尚更この傾向が強いと思われます。
予知保全の実現には富士電機のAIプラットフォームがおすすめ
富士電機のAIプラットフォームの特徴は、「説明できるAI」であること。自動車産業をはじめとする、過去様々な分野で得たAI活用ノウハウをもとに、新しい価値を生み創造します。富士電機は、AIプラットフォームを“ブラックボックス化”させません。
富士電機の説明できるAI
重電ならではの実績豊富なアナリティクス・AIを駆使し、生産現場で収集したデータから新しい価値をつくり出します。
富士電機AIを導入するメリット
-
エネルギー利用の最適化
-
エネルギーコスト削減
-
エネルギー原単位削減
-
-
操業の最適化
-
生産性向上(リードタイム短縮、品質向上、歩留まり改善)
-
プロセス異常回避
-
-
設備管理の最適化
-
不測のダウンタイムゼロ化
-
メンテナンスコスト削減
-
-
人財の効果的な活用
-
熟練技術の継承
-
労働時間の削減
-
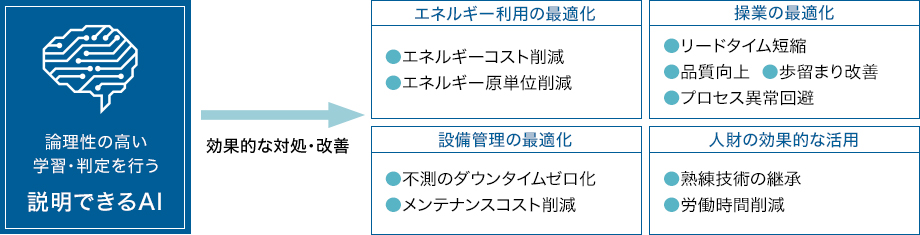
システムの特徴
富士電機の「説明できるAI」は、
-
1.
学習データ
-
2.
AIモデル
-
3.
結果の根拠がそれぞれ説明可能
このため、問題・課題に的確な対処が行え、安全性・信頼性が必要な分野に適用できます。
弊社は自社工場の「ものつくり」現場で、最新のアナリティクス・AI技術を導入し、AI活用ノウハウを蓄積しています。富士電機は、自社で培ったノウハウにお客様の知見を加え、お客様と一緒になって課題を解決します。
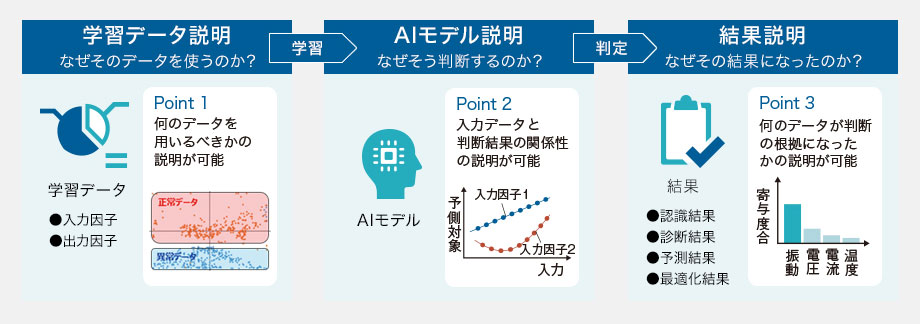
【システム構成】エッジコントローラ、オンプレミス/クラウドなど、様々な形態でアナリティクス・AIを活用したシステム&サービスをご提供
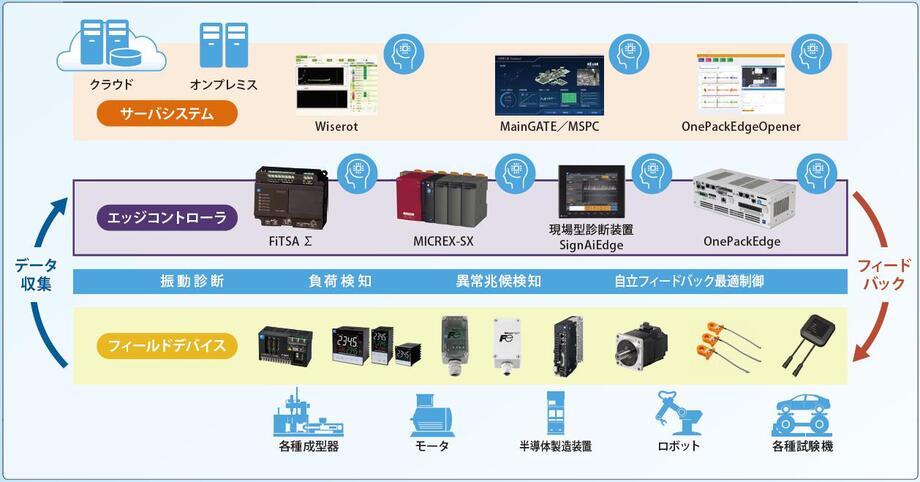
まとめ
予知保全は、これまで経験豊富なベテラン技術者しか行えなかった保全業務です。AIはベテラン技術者が培ってきた経験やノウハウをデータ化し学習できるため、データの軽微な違いから機器・設備の不具合の予兆を発見できます。ベテラン技術者不足の折、的確に保全を行うためには、AIの活用が不可欠です。
富士電機はアナリティクス・AIを、認識・診断/分析・予測・最適化と、機能別に4種類のカテゴリに分類。「画像Deep Learning」「MSPC(多変量統計的プロセス管理)」「JIT(Just in time)予測」「 構造化Deep Learning」で、説明できるAIをご提供します。
弊社は高度な解析技術で、エネルギーマネジメントや生産設備の稼働率向上による全体最適を支援します。