富士電機製品コラム
スマートファクトリーとは何か?
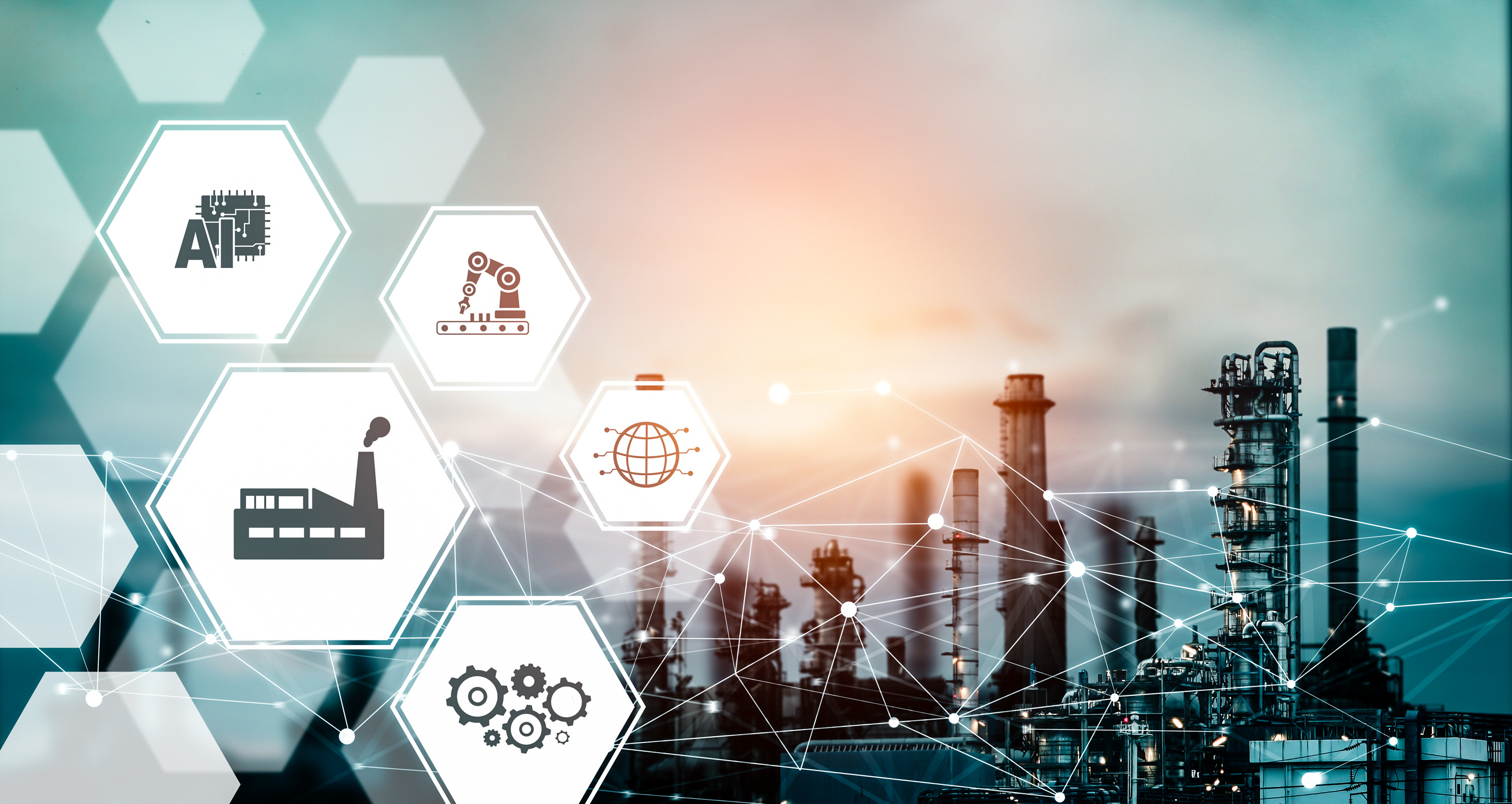
スマートファクトリーとは何か?AIやIoT技術導入によるメリットを事例と共に解説
近年「スマートファクトリー」や「スマート工場」という言葉を耳にする機会が多くなりました。スマートファクトリーをテーマにした展示会やセミナーなどのイベントも開催されるなど、関心が高まっているキーワードですが、スマートファクトリーとはどのような工場を指すのでしょうか。また、スマートファクトリーの実現によって、どのような生産現場の課題を解決できるのでしょうか。本記事では、スマートファクトリーの概要やメリットを導入事例も交えながら、詳しく解説します。さらにスマートファクトリー実現に向けた製品もご紹介いたしますので、ぜひご覧ください。
スマートファクトリー(スマート工場)とは?
概要
スマートファクトリー(スマート工場)とは、工場内の基幹システム(ERP)・製造実行システム(MES)や生産設備がネットワークによって接続され、工場経営の指標となる各種データの管理が効率化されることで、生産性の向上が実現された工場のことです。
スマートファクトリーのイメージ図は以下の通りです。
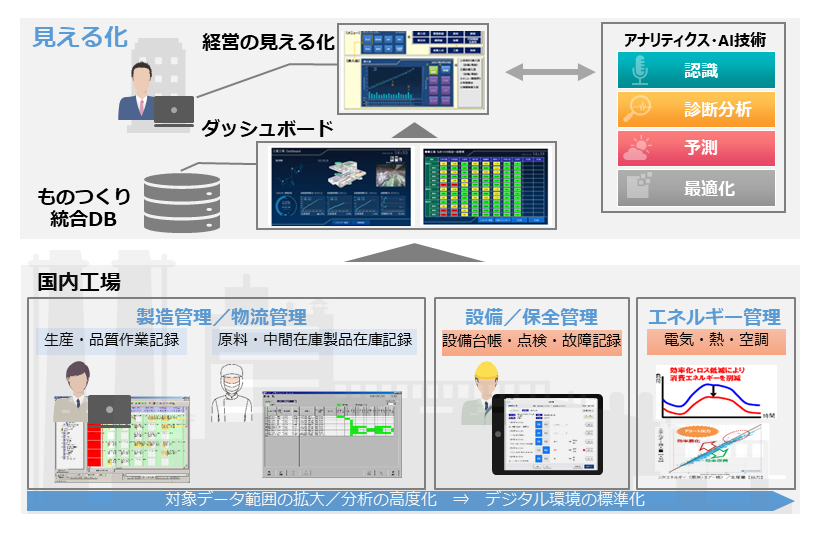
スマートファクトリーにおいては、AI(Artificial Intelligence:人工知能)やIoT(Internet of Things:モノのインターネット)の技術が導入されます。IoT機器によって集められたビッグデータはAIなどを用いて分析されることによって、生産ラインで日夜発生する課題の見える化とその解決が図られます。正確なデータに基づいた課題認識と生産現場の改善活動のサイクルは、工場全体ひいては会社全体の収益率の向上に大きく貢献します。
ドイツ政府が2011年に提唱したインダストリー4.0(第4次産業革命)の用語は世界的に知られていますが、そのコンセプトを具現化した工場がスマートファクトリーと言えるでしょう。インダストリー4.0の発表を皮切りに、中国やインドなどの各国でも同様のコンセプトや戦略が打ち出されており、日本も2017年にコネクティッドインダストリーズの概念を提唱しました。スマートファクトリーの実現は、まさに世界的な潮流となっており、今後も市場規模の拡大が予測されています。
また、スマートファクトリーに関連した最新技術として、ローカル5Gが話題を集めています。工場内にローカル5Gの通信網が本格的に整備されると、5G通信の「超高速」「超低遅延」「多点同時接続」の特長を生かして、データ容量と通信速度を飛躍的に高めることが可能です。2022年現在は主として実証実験段階にありますが、未来のスマートファクトリー構築の要として期待されています。
従来の工場との違い
スマートファクトリーの定義は上記の通りですが、従来の工場との最も大きな違いはどこにあるのでしょうか。それは、生産性の向上を実現する過程の効率化です。
従来の工場でも、生産性の向上は至上命題でした。しかし、現場に担当者が張り付いてデータを集計する、紙媒体の記録をPCに手作業で転記する、表計算ソフトを用いて属人的なデータ分析を行う、といった非効率的な作業形態では、スピード感が失われるとともに、改善活動自体に疲弊してしまうことでしょう。また、データ管理システムが導入されている場合でも、それぞれ独立した複数のシステムが乱立しており、本当に必要なデータを集めて紐づけていく作業が大変といった場面も見られます。
正確なデータが一元的に管理され、誰もが必要な時に必要なデータを取り出せることが、速やかな課題把握と改善活動の実行を促します。生産性向上の効率化は、自社内の業務改善効果のみならず、競合他社との競争力強化にもつながり、スマートファクトリー導入の最大のメリットと言えるでしょう。
DX(デジタルトランスフォーメーション)との違い
最近では、「DX」という言葉も多くのメディアで取り上げられています。「DX」はDigital Transformationの略語です。経済産業省のDX推進ガイドラインにおいては、「企業がビジネス環境の激しい変化に対応し、データとデジタル技術を活⽤して、顧客や社会のニーズを基に、製品やサービス、ビジネスモデルを変⾰するとともに、業務そのものや、組織、プロセス、企業⽂化・⾵⼟を変⾰し、競争上の優位性を確⽴すること」と定義されています。
つまり、DXを生産プロセスに適用した工場こそが、スマートファクトリーそのものです。言い換えれば、デジタル技術を活用して、ものづくりの業務プロセスを変革し、スマートファクトリーを実現することが、すなわち工場におけるDXの達成と言えるでしょう。
スマートファクトリーの導入における5つのメリット
品質の向上
スマートファクトリーの構築は従来の工場で発生していたさまざまな現場課題の解決に結びつきます。
ものづくりにおいて最も重要とされるのは、製品品質の保証です。スマートファクトリーにおいては、製造履歴データが製品情報と紐づいて保存されることで、品質トレサビリティ(注)が確保されます。どの製品がいつどのように製造されたのかを容易に特定することができれば、製品の品質管理が効率化されるとともに、製品を購入・使用するユーザからの評価向上効果も期待できます。
また、画像データとAI分析の活用による検査を導入したり、時系列データの監視により「いつもと違う」状態を検知したりする取り組みは、ヒューマンエラーの削減による不良品の流出防止につながります。
-
(注)
-
製品品質に影響する要因(使用原材料・製造工程・出荷検査結果など)の追跡可能性。
コストの削減
製造コストの削減は、工場が利益を生み出すための重要なポイントです。製造コストの削減に取り組むには、まず現状を把握する必要がありますが、従来の工場では正確な製造コストを把握することは困難でした。
部材の調達コストのみならず、各製品の製造に要する工数や不良品の発生率、各設備の稼働時間や消耗部品の交換情報、電気や熱などのエネルギー使用状況など、さまざまなデータが一元的に集約されるスマートファクトリーでは、より正確な製造コストの把握が可能となります。目標と実態のギャップが見える化されることで、改善点や対策内容が明確になり、製造コストの削減につながります。
人材不足の解消
各業界で人材不足が叫ばれていますが、製造業も例外ではありません。少子高齢化による熟練技術者の減少や若手技術者の採用難、外国人労働者の増加などで、従来の日本のものづくりの在り方は岐路に立たされています。
AIやロボット・自動化設備の導入によるものづくりの自動化や、ビッグデータを活用したスキルやノウハウの標準化、各種手順書やマニュアルの電子化などを通じて、スマートファクトリーの構築を進めていくことで、慢性的な人材不足の解消や円滑な技能伝承を図ることが可能となります。
故障の未然防止
生産設備の故障を事前に検知することは、工場の安定操業のポイントとなります。従来は余裕を持った時期を定めてメンテナンスを行う「予防保全」の取り組みが中心でしたが、時間基準保全であるために、まだ使える可能性のある部品も交換対象となってしまうデメリットもありました。
現在は状態基準保全である「予知保全」が注目を集めています。対象機器のデータから不具合の兆候を検知して、故障発生直前の最適な時期に保全を行う考え方で、作業工数や交換部品コストを削減できることが特長です。予知保全システムの確立は止まらない生産ラインの実現につながりますが、そのためには工場の生産設備全体の適切なメンテナンス時期の予測が必須となります。ネットワークによって各設備からデータを収集するスマートファクトリーの構築が必要と言えるでしょう。
予期せぬトラブルへの対応
たとえ、スマートファクトリーを構築できたとしても、生産ラインに予期せぬトラブルが発生することがあるでしょう。しかし、そのような局面でこそ、スマートファクトリーの強みである効率化の効果が発揮されます。
従来の工場では多くの時間と労力を要していた現状把握や原因究明をスマートファクトリーの利点を生かして効率的に実施することで、生産ラインの早期正常化・トラブル発生影響の最小化を図ることができます。原因分析から同様の事象の再発を防止していくことで、より安定した生産ラインを構築することができます。
スマートファクトリー構築の進め方と注意点
スモールスタートで導入効果を検証
スマートファクトリーの構築には、システム構築・機器購入・ネットワーク整備などの投資が必要ですが、いきなり大規模な投資に踏み切ることは、高いリスクを伴う上に、導入自体が目的となってしまいがちです。また、正確な導入効果を事前に試算することが難しい場合も多いため、導入予算の確保自体に苦戦するケースも見られます。
そのため、スマートファクトリーの構築は段階的に進めていくことが一般的です。小規模なPoC(Proof of Concept:概念実証)を重ねて、解決すべき課題に対する最適な手段は何か、期待通りの導入効果を得られる見込みはあるかを事前に検証することで、リスクを最小限に抑えながら、スマートファクトリーの実現を目指しましょう。
また、スマートファクトリーやDXへの投資には、補助金が活用できる場合もありますので、国や自治体から発信される情報を定期的に調べてみましょう。
継続的な取り組みで業務プロセスを変革
スマートファクトリーの構築は一朝一夕で成るものではなく、実現に向けたロードマップを作成した上で、数年単位の時間をかけた継続的な取り組みが必要となります。一過性の取り組みでは、投資金額に見合う導入効果は得られません。
また、AIシステムやIoT機器の導入は手段であり、目的ではないということも、十分に意識しておきましょう。スマートファクトリーの実現・DXの達成というゴールに到達するには、それらのシステムや機器を活用した効率的な業務プロセスを工場全体に定着させなければなりません。既存の業務プロセスの変革には、社内各部門との調整や合意形成にも多くの労力を費やす必要がありますので、実行推進役を担うプロジェクトを組織するなど、体制面でのバックアップも必要となるでしょう。
スマートファクトリーの導入事例
富士電機・大田原工場の事例
富士電機では、自社工場のスマートファクトリー化に向けて、様々な取り組みを行っています。
栃木県の大田原工場では、受配電機器の生産を行っています。従来からIoT技術を活用した先進的なものづくりに取り組んできましたが、単に機器やシステムを導入するだけでなく、どのように生産性向上効果に結び付けるかが課題となっていました。
そこで、工場全体の全体最適化を図るため、生産ラインや工場全体の生産情報、工場の日々の経営情報まで、あらゆる情報を一元化して見える化する「ダッシュボード」を導入しました。品質や生産進捗・稼働率・エネルギーといった「QCD」をリアルタイムで見える化することで、現場で発生した問題に対して、迅速に対策を実行することが可能となりました。例えば、ダッシュボードで生産タクトタイムのバラつきを発見した際には、カメラ映像と稼働データを分析することで、バラつきの原因を特定して対策を講じることができました。
このような課題把握と改善活動のサイクルを繰り返すことにより、生産性の5%向上を達成することができました。
日産自動車・栃木工場の事例
当社以外のスマートファクトリーの取り組み事例についても、簡単にご紹介します。
国内の大手自動車メーカである日産自動車では、革新的な生産技術で次世代のクルマづくりを支え、カーボンニュートラルの実現に貢献するためのクルマづくりコンセプトである「ニッサン インテリジェント ファクトリー」を同社栃木工場の生産ラインに初めて導入したことを2021年10月に発表しています。
このような取り組みの背景としては、高齢化社会の進展に伴う深刻な人手不足、気候変動やパンデミック等の発生、自動車の電動化や知能化といった急速な環境の変化への対応を迫られているという課題があります。自動車業界全体の大きな変革期の中で、新たなコンセプトのものづくりをグローバルに適用し、スマートファクトリー化を図ることが、直面する課題を打破して飛躍を遂げるために、まさに必要な手段だとされていると言えるでしょう。
「ニッサン インテリジェント ファクトリー」においては、富士電機の製品も導入されており、設備稼働率の向上に貢献しています。生産用ロボットの常時監視による異常兆候の自動診断システムにおいて、「診断センサHUB」が活用されています。
また、エンジン部品生産ラインにおいては、「組立加工データ収集システムOnePackEdge」がスマートファクトリー化・生産性向上に貢献しています。お客様が抱えておられた様々な課題や本製品導入後の改善効果をお伺いしたインタビュー動画・記事を公開しておりますので、下記リンクからぜひご覧ください。
納入先:日産自動車株式会社 栃木工場様
対象:エンジン部品生産ライン
スマートファクトリーを実現する富士電機の製品
富士電機では、IoT製品・システムのご提供を通じて、お客様の工場のスマートファクトリー化に貢献しています。
組立加工データ収集システムOnePackEdgeは自動車部品の機械加工ラインを中心に豊富な導入実績がございます。生産ラインのさまざまな生産設備から、ものづくりのサイクルと同期した統一的なデータ収集を可能にするとともに、設備不具合への対応・品質の維持管理・適切な工具交換時期の予測などに活用するための、生産現場のオペレーションに即した実用的な機能を多数搭載しています。
診断センサHUBは主に産業用ロボットやプレス機の予知保全用途で多数ご採用いただいています。製品本体に内蔵された3軸加速度センサと外部接続センサを組み合わせることで、対象設備や異常箇所に応じた最適なデータを収集することが可能です。収集したデータは無線で送信される仕組みのため、省配線で設置コストの抑制にもつながります。
その他にも目的に応じた様々な製品・ソリューションのラインアップを取り揃えておりますので、関連製品のリンクからぜひご覧ください。
まとめ
日本の製造業を取り巻く状況は変化を続けています。外部環境の変化に柔軟に対応し、自社の競争力を維持し続けるためには、スマートファクトリー化による迅速な課題解決と生産性の向上は必要不可欠な取り組みとなるでしょう。
しかし、その実行にあたっては、十分に注意しなければならない点もあります。漠然としたイメージだけで一足飛びに事を進めるのではなく、事前の綿密な検討と導入効果の検証、工場内への新たな業務プロセスの定着があってこそ、スマートファクトリーは実現できるものです。
富士電機は計画・検討段階から、PoC実施・機器導入・システム構築・現場運用支援に至るまで、幅広くお客様のスマートファクトリー化に貢献します。