富士電機製品コラム
工場の見える化とは?
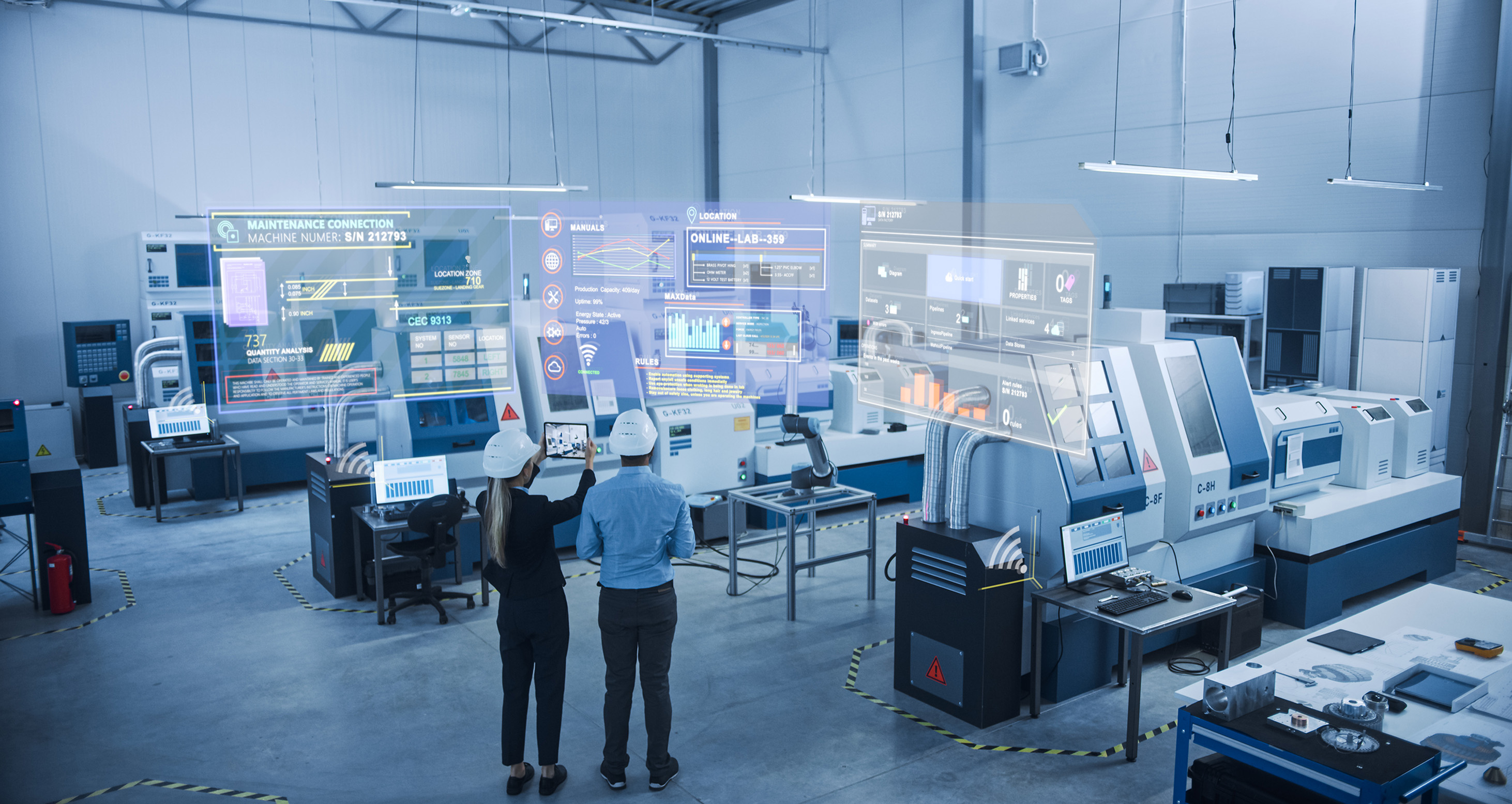
工場の見える化とは?目的やメリット・導入事例まで解説
近年の製造業の生産現場では、経営層から工場の見える化を求められるケースが多くあります。工場に勤務されている方であれば、実際に見える化の取り組みをされた経験をお持ちの方もおられるのではないでしょうか。しかし、見える化に対する目的設定が曖昧なまま、見える化自体を目的にしてプロジェクトを進めてしまうと、さまざまなデータは見えるようになったにも関わらず、十分な成果につながらなかったというケースも見受けられます。そのような事態に陥らないためのポイントも交えながら、工場の見える化を図る真の目的や導入メリット・導入事例について、詳しく解説いたしますので、ぜひご覧ください。
工場の見える化とは?
概要
工場における「見える化」とは、生産現場の設備や各種センサからのビッグデータを一元的に収集した上で、それらのデータを整理・加工して、現場の作業者が理解しやすい形で可視化することを指します。見える化の対象範囲としては、設備数台レベルの簡易的な監視から、工程・工場全体に及ぶ大規模なシステムまで、生産現場毎の導入状況によって異なります。
また、「見える化」ではなく「見せる化」という単語が使われる場面もありますが、いずれにせよ単にデータを見せるのみに留まらず、見えるようになったデータから作業者に気づきを生み出し、生産現場の改善を促していく仕組みづくりが重要です。
目的やメリット
見える化の概要は以上の通りですが、見える化を実現すること自体をゴールに設定してしまっては、まさに本末転倒です。工場の各工程や設備がどのような状況になっているのか、各作業者に迅速かつ分かりやすく伝達することによって、生産性の向上につながる活動を促すことが、見える化を行う目的であることを忘れてはなりません。
このようにして、工場の見える化を図ることで、各作業者の経験やノウハウに依存することなく、現場の誰もが共通の現状把握を行うことができるというメリットがあります。業務の属人化を防ぐとともに、経験が未熟な若手人材のスキル向上にもつながります。
見える化はなぜ重要なのか
それでは、見える化はなぜこれほど重要なキーワードとして認知されるようになったのでしょうか。その理由は、見える化が工場における全ての改善活動の基礎となる重要なプロセスであるためです。
正確な現状把握を行うことは、効果的な改善活動を実行するための大前提です。しかし、長年に渡り工場の現場を熟知されている作業者であっても、工場全体の状況をタイムリーかつ客観的に把握して、速やかに対策を講じることは至難の業です。そこで、リアルタイムに分かりやすく稼働状況を表示する見える化システムが、現場の作業者の正確な現状把握を支援します。
また、工場全体の競争力がさらに強化されたスマートファクトリーを実現するためには、データの解析・評価を通じた原因の「分かる化」や将来予測に基づいてフィードバックを行う「最適化」を実現するシステムを構築することが理想的ですが、「見える化」はその第一段階と言えます。
まとめると、今まで見えなかった状態が「見える化」されることは、対策と改善の好循環を発展させていくための基礎であり、最も重要な基本のプロセスです。逆に言えば、最初の見える化の方法が誤っていると、その後の打ち手も間違えてしまう可能性があります。だからこそ、「見える化」が重要なこととして広く知られているのです。
見える化でできる3つのこと
それでは、見える化によって具体的にどのようなことができるようになるのでしょうか。代表的な見える化の例は以下の3つです。
-
生産進捗状況を見える化
-
ロス時間を見える化
-
設備保守業務を見える化
それぞれの内容を詳しくご紹介します。
生産進捗状況を見える化
まずは、工場全体の生産進捗状況の見える化です。事前に登録した生産計画と生産実績の対比から、計画通りにものづくりが進んでいるのかどうかを把握することができます。さらに、単に工場全体の生産が遅れているというだけではなく、工程毎・設備毎にブレイクダウンして状況を明確にすることで、生産ラインのボトルネックを突き止めることができます。
このように、リアルタイムで見える化される情報から、生産計画からの遅れとその原因をいち早く把握することが可能です。見える化ができていない場合と比べて、速やかに対策を講じることができます。
ロス時間を見える化
次に、製造工程全体の一元的な監視による生産性低下(ロス時間)の見える化です。各設備から収集した設備の状態データをダッシュボードで一元的に表示することで、正常稼働している設備/待機中で非稼働状態の設備/異常や故障が発生している設備など、工場内の各設備の状態を視覚的に分かりやすく表示します。
設備の稼働状態を見える化できていない場合は、例えば赤色表示灯で設備の異常を発見する方法が考えられますが、即応性が高い手段とは言えません。また、次のワーク供給までの待機時間などは異常ではなく把握しにくいものです。工場の見える化を導入することで、これらのロス時間の削減を目指した生産ラインの改良を図ることができるようになります。
設備保守業務を見える化
また、設備の状態や部品の使用状況・在庫状況を見える化することも可能です。各設備から収集されるセンサのデータに対して、予め上下限の閾値などを設定することで、設備の状態をデータに基づいて管理することができます。これにより、設備の突発故障をいち早く検知して損害を最小限に抑えることにつながります。また、交換部品の劣化傾向を事前に把握して、適切な保守計画を立てることで、予知保全の実現による交換時期の最適化や作業負荷の軽減を図ることができます。
近年の製造業を取り巻く環境として、熟練技術者の減少や人材確保難といったトレンドが続いています。主観的な経験値から、客観的なデータに基づいた保全業務への移行を図ることの重要性は増しており、一刻も早い対応が求められています。
工場へ導入する際の2つのポイント
ここからは、工場の見える化システムを導入する際の注意点をお伝えします。
現場で使いやすいシステムを導入すること
最も重要な点は、実際にシステムを利用する生産現場の作業者のユーザビリティが考慮された使いやすいシステムを導入することです。多額の投資をしてせっかく見える化システムを導入しても、画面の表示内容や操作方法が現場の作業者の業務フローに合っていないなどの要因で現場に浸透せず、宝の持ち腐れとなるような事態は避けなければなりません。
会社の組織体制によっては、情報システム部門が主導して工場の見える化システムを導入する場合も見受けられます。そのような場合は特に生産現場との認識の違いが生じないように注意する必要があります。具体的には、導入検討段階から丁寧に現場の意見を汲み取ってシステムの仕様に反映させるようにしましょう。
まずは小さいところから始めること
また、まずは小さな単位での見える化システムを導入してスモールスタートを図り、徐々にステップアップして導入範囲を拡大するプロセスをたどることも大切なポイントです。
一般的に、見える化システムのようなIoTの取り組みは事前に投資対効果を試算することが難しいとされています。トライ&エラーの要素が多く、実際にデータを収集してみないと、どのような効果が生じるのかを予測しにくいためです。したがって、PoC(Proof of Concept:概念実証)を通じて、想定した導入効果と実際の導入効果がマッチしているかを確認しながら、プロジェクトを進めていくべきでしょう。
また、前述した「現場で使いやすいシステム」を模索していくためにも、まずは小規模なシステムを導入して、実際に現場の作業者に活用してもらい、使い勝手を検証することも有力な選択肢と言えます。
工場を見える化した事例
富士電機では、自社工場の見える化の取り組みを進めるとともに、お客様工場の見える化にも貢献してきました。ここでは、3つの工場での事例をご紹介します。
富士電機・大田原工場の事例:「見える化で生産性5%向上」
栃木県の大田原工場では、受配電機器の生産を行っています。従来からIoT技術を活用した先進的なものづくりに取り組んできましたが、単に機器やシステムを導入するだけでなく、どのように生産性向上効果に結び付けるかが課題となっていました。
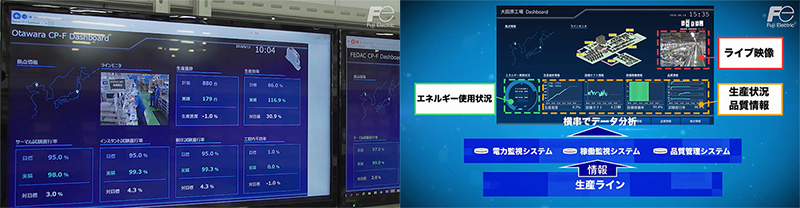
そこで、工場全体の全体最適化を図るため、生産ラインや工場全体の生産情報、工場の日々の経営情報まで、あらゆる情報を一元化して見える化する「ダッシュボード」を導入しました。品質や生産進捗・稼働率・エネルギーといった「QCD」をリアルタイムで見える化することで、現場で発生した問題に対して、迅速に対策を実行することが可能となりました。例えば、ダッシュボードで生産タクトタイムのバラつきを発見した際には、カメラ映像と稼働データを分析することで、バラつきの原因を特定して対策を講じることができました。
このような課題把握と改善活動のサイクルを繰り返すことにより、生産性の5%向上を達成することができました。
富士電機・山梨工場の事例:「見える化・分かる化・最適化のステップで34%の省エネ達成」
パワー半導体のチップを生産している山梨工場では、生産工程において多くのエネルギーが必要となることから、特に省エネ化が求められているという課題がありました。
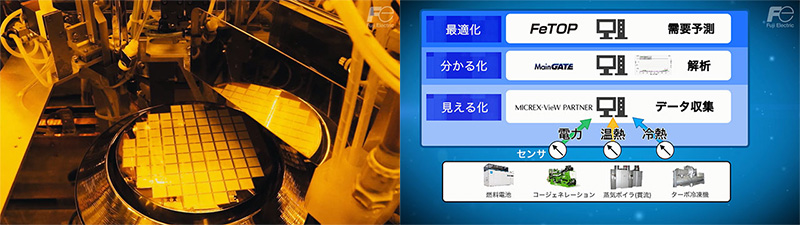
そこで、エネルギー使用量の「見える化」を足掛かりとして、エネルギー使用量の削減を目指しました。センサで電力や温度などのデータを収集し、解析ソフトウェアを使用しながら、蓄積された実績データを多角的に分析することで、「見える化」を起点として「分かる化」に発展し、さらなるエネルギーのムリ、ムダ、ムラの発見することができました。また、AIを活用した需要予測により、エネルギーコストが最小となるような運転パターンの計画を立案するなど、「最適化」のフェースまでステップアップすることができました。
このような取り組みにより、生産量の増加にも関わらず、5年間で34%の省エネを達成することができました。エネルギー自給率100%の達成の実績も評価され、省エネ大賞の経済産業大臣賞を受賞しました。
日産自動車・栃木工場の事例:「ニッサン インテリジェント ファクトリー」
国内の大手自動車メーカである日産自動車では、革新的な生産技術で次世代のクルマづくりを支え、カーボンニュートラルの実現に貢献するためのクルマづくりコンセプトである「ニッサン インテリジェント ファクトリー」を同社栃木工場の生産ラインに初めて導入したことを2021年10月に発表しています。
このような取り組みの背景としては、高齢化社会の進展に伴う深刻な人手不足、気候変動やパンデミック等の発生、自動車の電動化や知能化といった急速な環境の変化への対応を迫られているという課題があります。自動車業界全体の大きな変革期の中で、新たなコンセプトのものづくりをグローバルに適用し、スマートファクトリー化を図ることが、直面する課題を打破して飛躍を遂げるために、まさに必要な手段だとされていると言えるでしょう。
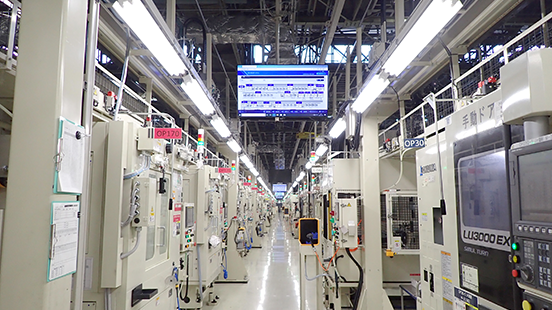
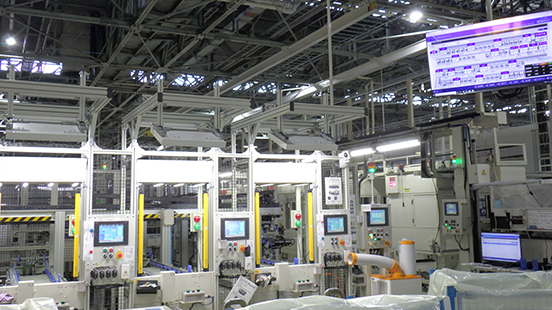
エンジン部品加工ライン(日産自動車提供)
「ニッサン インテリジェント ファクトリー」には、富士電機の製品も導入されており、エンジン部品生産ラインにおいては、「組立加工データ収集システムOnePackEdge」が見える化・生産性向上に貢献しています。お客様が抱えておられた様々な課題や本製品導入後の改善効果をお伺いしたインタビュー動画・記事を公開しておりますので、下記リンクからぜひご覧ください。
納入先:日産自動車株式会社 栃木工場様
対象:エンジン部品生産ライン
まとめ
製造業の競争力を維持・強化していくためにも、業務効率化や生産性向上は急務となっており、さまざまな業務改善につながる第一歩として、工場の見える化が重要な取り組みとして位置付けられています。
富士電機では、自社工場での見える化を通じた生産性向上の取り組みを進めて参りました。そして、お客様の工場の見える化にも貢献したいとの思いから、現場側のデータ収集機器から上位系の情報システムまで一気通貫での対応を行っております。また、豊富な商材のラインアップから、導入目的やご予算に応じた最適な商材をご提案することも可能です。工場の見える化システムをご検討されている方は、ぜひ以下のお問い合わせフォームからご相談ください。