富士電機製品コラム
予防保全とは?他の保全方法との違いやメリット・デメリット、改善事例を解説
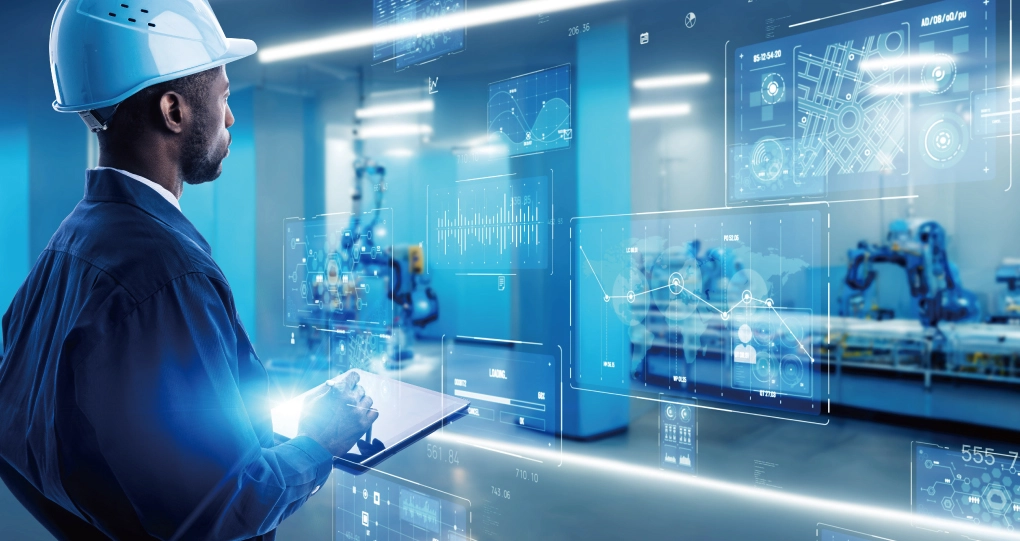
予防保全とは?他の保全方法との違いやメリット・デメリット、改善事例を解説
製造業において、工場の生産性向上は今も昔も変わらない至上命題であり、ものづくりの効率性が企業全体の業績を左右すると言っても過言ではありません。近年では、人が行う作業を機械装置によって自動化することで、生産効率を高める動きも進められていますが、故障などで生産設備が長期間停止してしまった場合は大きな損失が発生するリスクもあります。したがって、適切なタイミングで保全を行うことによって、故障発生リスクを抑え、安定的な操業を維持することが不可欠です。保全方法の一種として、「予防保全」という考え方があります。本記事では、予防保全のポイントを確認した上で、「事後保全」や「予知保全」といった予防保全以外の保全方法との違いも押さえつつ、保全業務効率化の事例もご紹介いたします。予防保全に関心をお持ちの方はぜひご覧ください。
予防保全とは
予防保全とは、時間基準保全(TBM:Time Based Maintenance)とも言い換えられるように、生産設備・部品の動作時間や動作回数を基準として保全に着手することです。具体的には、保全対象毎に予め基準となる動作時間や動作回数を定めておき、それに達した時点で計画的に保全を行うことにより、故障発生を未然に防止することを最優先とする考え方です。一般的に行われている設備の年次点検のような定期点検も予防保全の考え方と類似した保全方法です。
予防保全の基準をどのように設定するかはケースバイケースですが、サプライヤが推奨する使用時間や回数に従う場合、過去の経験則から適切だろうと見込まれる期間・回数を設定する場合などがあります。
保全方法の違い
予防保全の概要は上記の通りですが、その他の保全方法として、事後保全や予知保全といった手法もあります。ここでは、それらの保全方法と予防保全との違いを確認していきます。
事後保全との違い
事後保全とは、その名の通り、故障やトラブルが発生した後に保全に着手することです。つまり、保全を行う基準は故障やトラブルが発生した時点となります。予防保全はそのような突発的な故障やトラブルを予防することに主眼を置いているため、事後保全とは対極にある考え方だと言えます。
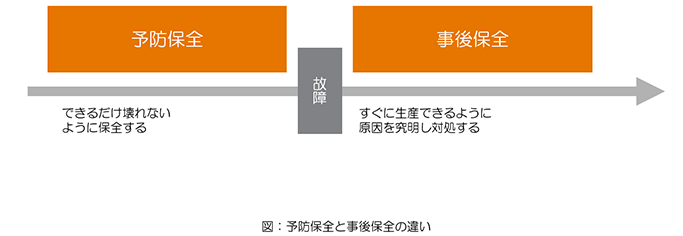
出典:予防保全とは?事後・予知保全との違い、メリット、IoT活用による効果を解説(富士フィルムビジネスイノベーション株式会社)
予知保全との違い
予知保全とは、状態基準保全(CBM:Condition Based Maintenance)とも表現されるように、生産設備・部品の劣化状態を基準として保全に着手することです。つまり、生産設備の異常箇所及びその兆候を何らかの手段で検知して、その時点で部品の修繕や交換を行うことになります。故障やトラブルの発生を防ぐという観点では、予防保全と似た考え方ですが、保全に着手する基準を異常兆候の検知としている点が異なります。
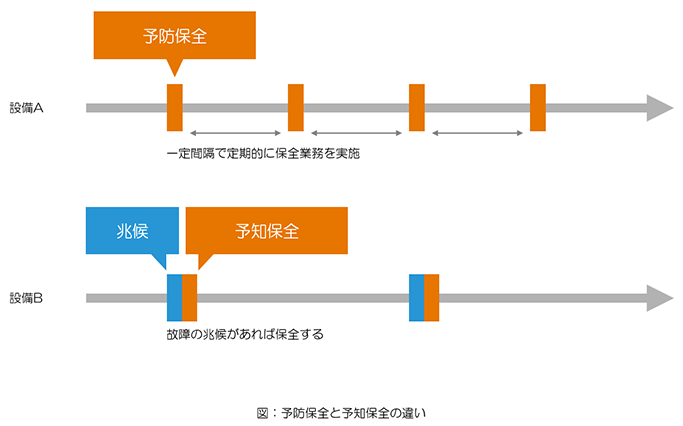
出典:予防保全とは?事後・予知保全との違い、メリット、IoT活用による効果を解説(富士フィルムビジネスイノベーション株式会社)
予知保全について詳しく知りたい方は関連の記事もご覧ください。
予防保全のメリットとデメリット
それでは、予防保全にはどのようなメリット・デメリットがあるのでしょうか。その他の保全方法と比較しながら、それぞれ確認してみましょう。
メリット
最も基本的な予防保全のメリットは、事後保全では回避できない故障やトラブルの発生を予防できる可能性が高いという点です。故障発生の影響が軽微な場合やすぐに部品を交換できる場合には、事後保全でも特に支障がないこともあるでしょう。しかし、故障やトラブルに伴って、大量の仕損品が発生したり、長期間の設備停止に至ったりするリスクが大きい場合には、事後保全よりも予防保全を行うことが賢明です。
また、予知保全と比較した場合においては、予防保全は保全着手の基準設定が比較的容易である点がメリットです。予知保全を行うためには、設備状態をモニタリングして異常兆候を検知する必要があるため、そのためのセンサの設置コストやデータの解析スキルが必要な場合があるためです。
デメリット
予防保全のデメリットとしては、突発的な故障やトラブルを防ぐことができない点が挙げられます。つまり、推奨使用期間や経験則に基づいて計画した基準よりも前に、何らかの要因で早期に劣化が進行していた場合、故障に至るまでの異常兆候が見過ごされてしまい、故障やトラブルの発生をもたらしてしまう可能性が高いのです。
また、逆にまだ十分に使用できる部品を交換してしまう可能性があることもデメリットとなります。予防保全では、必ずしも劣化状態と連動しているとは限らない時間や回数といった画一的な基準によって保全に着手するため、実際は必要性が低い保全作業を進めてしまうこともあり得ます。それに伴う人件費や部品代などは、結果的に無駄なコストとなってしまいます。
予防保全の推進に向けた活動内容
さて、予防保全を実現するためには、どのような活動を推進する必要があるのでしょうか。
まずは、保全計画を策定する必要があります。設備の管理台帳から、対象となる生産設備・部品をリスト化し、それぞれに使用期間・回数などによる保全基準を設定します。交換部品の入手性や作業者の割り当てのような制約も加味しながら、保全計画を立案しましょう。次に、実際に保全計画に基づいてメンテナンスを行ったかどうかを管理する仕組みを整えなければなりません。保全を実施した日時や作業者の記録を残して、進捗管理を行うようにしましょう。さらに、無駄なコストの発生というデメリットを回避するためには、保全基準が適正かどうかを定期的に見直すことが効果的です。
事後保全・予防保全から予知保全へ
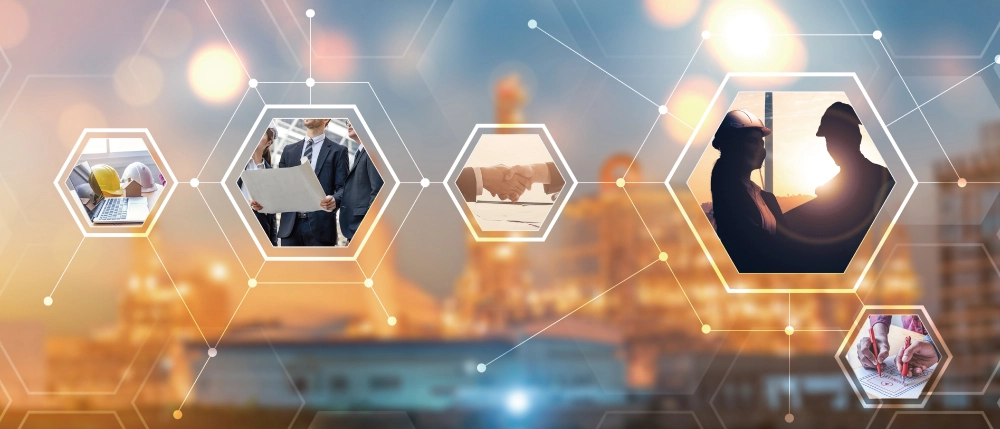
ここまで、予防保全の基本的な考え方やその他の保全方法と比較した場合のメリット・デメリットなどを確認してきました。どの保全方法にも一長一短があるため、対象設備の性質に応じた適切な手法を選択する必要がありますが、工場の安定的な操業を維持しつつ、さらなる生産性向上を図るというゴールに対しては、予知保全が最も効果的な保全方法だと言えます。
近年では、IoT・AIといった技術が広く普及したことで、熟練工のような研ぎ澄まされた感覚(勘・コツ)を持たずとも、定量的なデータの収集・解析によって、予知保全に取り組むことができる環境が整っています。もちろん、導入時にコストやスキルが必要というデメリットはありますが、予知保全の仕組みを確立できれば、そのメリットはデメリットを大きく上回るものになるはずです。まずは現状の保全業務の課題を分析した上で、投資対効果が見込まれるテーマから、予知保全の実現を目指すことをおすすめいたします。
保全業務効率化の事例
富士電機では、保全業務の効率化にご活用いただける製品を多数取り揃えています。最後に、当社製品を適用した保全業務効率化の事例を3つご紹介いたします。
事例①切削工具
業種:自動車部品メーカ
対象:切削工具
適用商材:工具診断システムOnePackEdge MARSYS
工具寿命の適切な管理は機械加工現場の課題でした。そこで、OnePackEdge MARSYSを導入することで、加工時の負荷を見える化。工具折れの発生をリアルタイムに発報することで、保全業務の効率化を実現しました。さらに、負荷傾向を連続監視することで、使用回数基準(予防保全)から、寿命基準(予知保全)での工具交換時期の目安を作ることができました。
事例②プレス機部品
業種:自動車メーカ
対象:プレス機部品
適用商材:現場型診断装置SignAiEdge&診断センサHUB
保守部品の寿命管理を最適化し、保全費を削減することが現場の課題となっていました。そこで、部品の定期交換時期に合わせて”SignAiEdge”と”診断センサHUB”を導入し、部品交換前後の振動解析に着手したところ、交換前後で明確な差異が見られました。その後もオンラインで監視・診断を継続することで、予知保全システムを確立することできました。
事例③加熱機ファン
業種:食品メーカ
対象:加熱機ファン
適用商材:回転機故障予兆監視システムWiserot
加熱機ファンには、計12台のモータが設置されていますが、高温・高所の環境下での点検作業は困難でした。また、1台の故障でも製品品質にムラが生じてしまうため、廃棄ロスで数百万円/回の損害につながってしまいます。”Wiserot”を予め取り付けておくことで、ベアリングの故障診断を簡単に実現できるようになり、予知保全による突発故障の発生リスク低減が可能となりました。
まとめ
ここまで、予防保全のポイントや保全業務効率化の事例をお伝えして参りましたが、いかがでしたでしょうか。予防保全のメリット・デメリットに加えて、事後保全・予知保全といったその他の保全方法との比較を通じて、それぞれの保全方法についての理解を深めて頂けたかと思います。
富士電機では、生産現場の保全業務の効率化にお役立ていただける製品を多数ラインアップしております。従来の予防保全の取り組みから一歩踏み込んで、保全業務のさらなる改善をご検討されている方は、以下のリンクからぜひ富士電機にお問い合わせください。