適用事例
-
※各適用事例は活用方法の一例です。実際の導入効果はお客様の設備・環境などによって異なります。
-
01 加工不良品流出防止
BEFORE(導入前)
工具異常(折れ・欠け)による加工不良品が次工程に流出。抜取検査で不良品を発見したが、影響範囲が分からず、緊急で全数検査を余儀なくされる。
加工不良品を生産し続けてしまい、大量の不良ロスが発生してしまう。
突発的な全数検査によリ、余計な作業工数が生じてしまう。
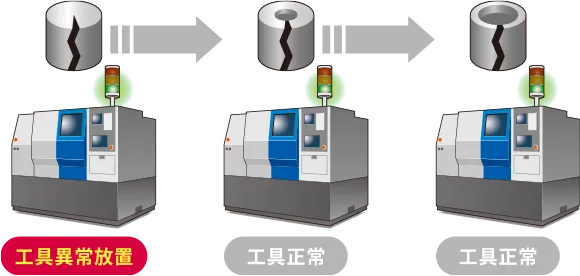
AFTER(導入後)
工具異常(折れ・欠け)を検知すると、速やかに加工機や作業者に通知。加工不良品の発生を最小限に抑えるとともに、次工程への流出を防止。
即座に設備を停止することで、不良ロス発生を最小限に抑制できる。
次工程流出を防止することで、品質確認作業工数を削減できる。
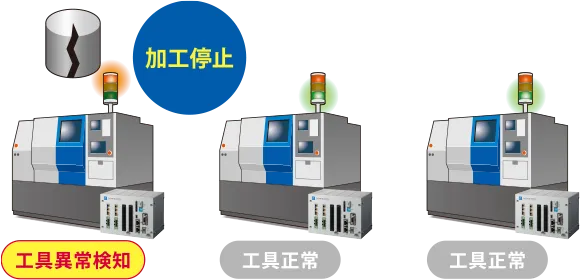
02 刃折れ検査誤判定削減
BEFORE(導入前)
接触式センサは刃先の異常を検知できない。レーザ式センサは外乱影響で誤判定を起こす。電流センサや振動センサは小径ドリルの異常を見逃す。
刃先だけの異常や小径ドリルの異常を見逃してしまう。
加工機内の外乱影響による誤判定で無駄な確認工数が生じてしまう。
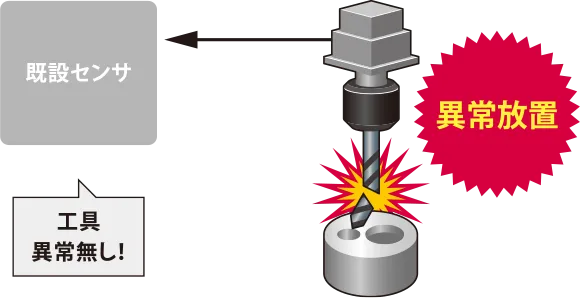
AFTER(導入後)
専用の電カセンサで刃先の異常を検知可能。盤内設置で外乱影響が僅少。小径ドリル(φ1)やM4タップ加工の異常検知実績多数。
専用の電カセンサにより、微小な異常も検知できる。
盤内設置型のため、加工機内の外乱影響による誤判定を抑制できる。
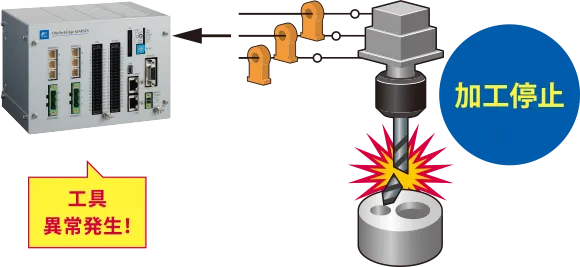
03 長時間加工異常診断(新機能)
BEFORE(導入前)
大型で高価なワークを長時間加工する場合、一度加工不良が発生すると多額の損失が生じてしまうが、加工監視要員を常時配置することは難しい。
大型で高価なワークの加工異常を放置すると、多額の損失が発生する。
長時間に渡る加工を監視し続ける要員を確保することが難しい。
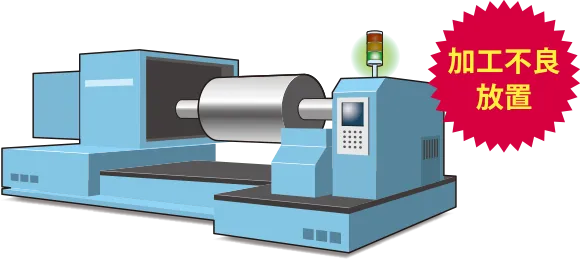
AFTER(導入後)
専用の電カセンサで長時間加工時の加工状態を自動で監視し、異常発生時は加工機を停止。不良品を継続加工することによる損失を最小限に抑制。
異常時に加工機を即座に停止することで、不良ロスの発生を抑制できる。
加工監視要員を配置しなくても、加工異常を常時監視できる。
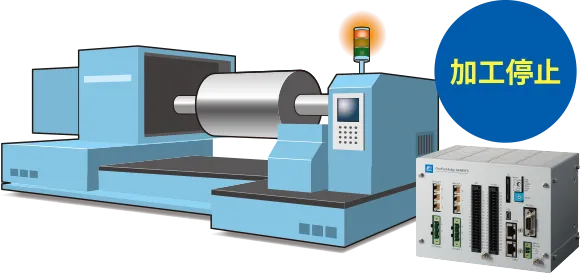
04 加工サイクルタイム短縮
BEFORE(導入前)
接触式センサやレーザ式センサで加工後に刃折れ検査を行うと、数秒の診断時間が必要なため、工具交換ごとにサイクルタイムが長くなってしまう。
加工後の診断時間がロス時間となり、生産性が低下する。
生産性の低下を補うため、追加の設備投資が必要となる。
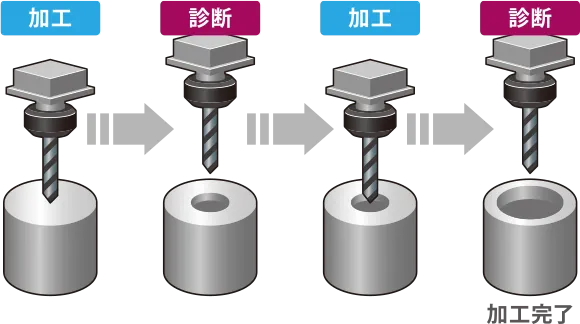
AFTER(導入後)
専用の電カセンサで加工中にリアルタイム異常検知が可能。加工後の診断時間が不要となり、加工機1台あたりの生産性が向上。
加工後の診断時間が不要となり、生産性を向上できる。
既存の生産能力を生かすことで、新たな設備投資を抑制できる。
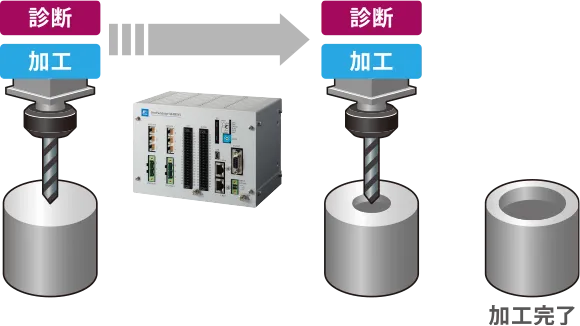
05 加工状態定量化
BEFORE(導入前)
ベテラン人材のカンコツを元に加工品質や工具交換時期を管理しておリ、若手人材への技能伝承がうまく進んでいない。
品質・保全面の管理基準が定量化されておらず、曖昧になっている。
特定の人材に依存しており、安定的な生産ができなくなるリスクを伴う。
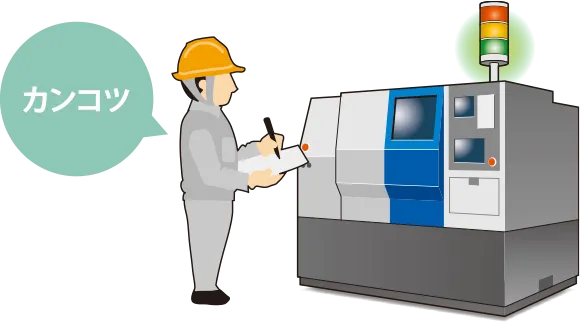
AFTER(導入後)
加工毎にサンプリングした波形を蓄積することで、加工状態を定量化。暗黙知が形式知となることで、誰もが同じ基準で品質・保全管理が可能。
定量的な管理基準を策定することで、業務品質を均一化できる。
柔軟な人材配置が可能となり、トラブル発生リスクを低減できる。
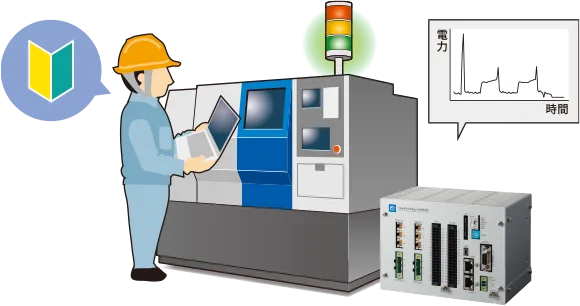
06 工具寿命管理
BEFORE(導入前)
工具メーカーが推奨する使用回数・使用時間や今までの経験則に基づいて、エ具を交換するタイミングを決めている。
まだ十分に使える工具を過剰に交換している可能性がある。
加工条件の差異による突発的な工具劣化速度の変化に対応できない。
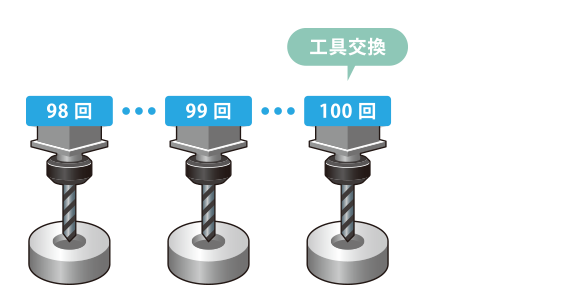
AFTER(導入後)
工具状態の傾向を監視することで、エ具寿命の目安となる基準を設定可能。エ具劣化状態を把握することで、工具交換頻度の適正化を実現。
工具を寿命間近まで使い切ることで、工具費用や交換工数を削減できる。
負荷状態の変化をデータで把握し、状態基準でエ具交換できる。
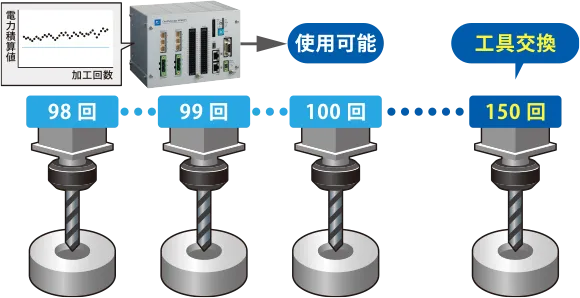