サステナビリティ
水資源の有効活用 - SDGs貢献事例
半導体製造工程・水有効活用プロジェクト
~水資源の有効活用で、循環型社会の実現に貢献~
~水資源の有効活用で、循環型社会の実現に貢献~
2023年10月公開。所属・業務内容は取材当時のものです
富士電機は「循環型社会の実現」を目指して、サプライチェーン全体での3R(リデュース、リユース、リサイクル)活動を推進しています。「水資源の有効利用および排水基準の遵守」はその取り組みのひとつ。とくに、パワー半導体の製造拠点である松本工場・山梨工場では、長年にわたって水資源の有効活用に取り組んできました。富士電機が掲げるSDGs重点目標「12 つくる責任 つかう責任」を体現する、両工場の「水有効活用プロジェクト」にクローズアップします。
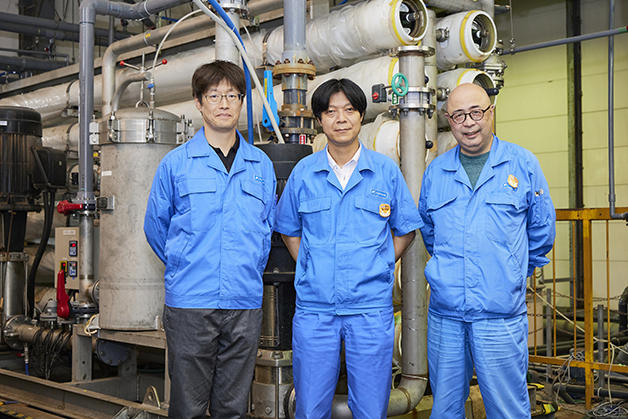
「水資源の有効利用」は、富士電機の使命。
富士電機の半導体事業は、省エネのキーデバイスである「パワー半導体」の製造が中心だ。同製品は、電気自動車や鉄道、太陽光・風力発電システムなどに用いられ、脱炭素社会の実現に向けて、重要な役割を果たすことになる。
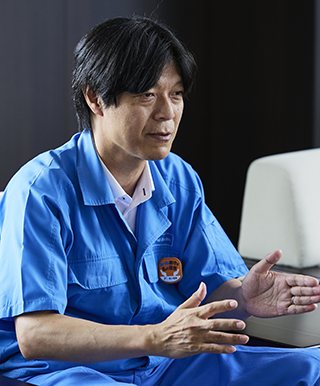
その製造過程において、松本工場と山梨工場が担うのは、パワー半導体製造の前工程だ。シリコン製の薄い板(シリコンウエハ)に電気回路を形成し、チップ状に切り出していく。パワー半導体の性能を決定づける重要なプロセスにおいて、水は必要不可欠な資源だ。半導体の製造プロセスでは、成膜・塗布・エッチングなどの工程を何度も繰り返し、その都度、洗浄に大量の超純水が必要となる。また、生産設備の冷却水、クリーンルームに求められる厳格な温度・湿度を保つための空調、温室効果の高いフロンガスの分解・除害化などにも多くの水が必要となる。松本工場チップ製造部・部長の高橋英紀は、「水資源の有効利用」に取り組む理由を次のように話す。
「水は、半導体の製造に欠かせないものです。地域環境への影響を最大限に考慮する。排水に伴うコストをできるだけ抑える。その貴重な資源をできるだけ有効活用することは、私たちがこの地域で事業を継続していく上での使命だと思っています。松本工場・山梨工場それぞれの環境を踏まえながら、『水を捨てずに再利用する取り組み』が進んでいるのです」
「改善の積み重ね」が、確かな成果を生んだ。
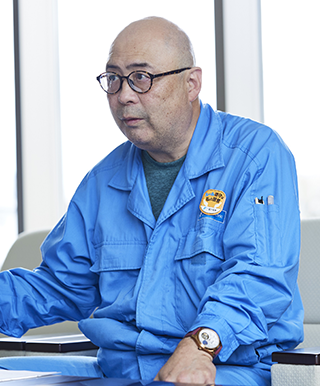
松本盆地は豊富な地下水に恵まれ、各家庭や地場産業を潤している。とはいえ、地域全体の水資源を保全するためには、資源量の把握と節水活動が欠かせないものとなる。松本工場では、生産設備排水の中から、再利用可能な水を切り分けてリサイクルする取り組みを長期にわたって実施してきた経緯がある。転機となったのは2005年。さらに水のリサイクル量を増やそうと、IWM(Integrated Water Management)設備を導入。これまではリサイクル困難とされてきた「排水の再生利用」に取り組むことを決めたのだ。松本工場で設備保全を担う荻村好友は、そのメリットを次のように話す。
「半導体工場の排水は、フッ酸・重金属等の有害物質の処理をおこなった後、松本工場内の終末処理場で中和をおこない、公共下水道に排水されています。IWMは、中和を終えて公共下水道に排水される直前の水を再利用する設備です。排水量の削減や排水費用の削減を実現するだけでなく、地下水の揚水量抑制にもつながるため、地下水資源の保護にも貢献することができるのです」
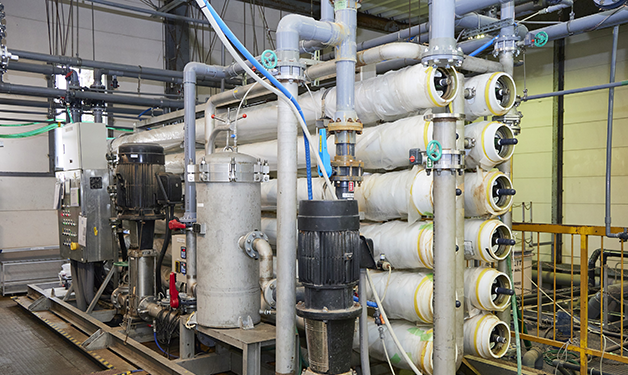
ただし、設備を導入するだけで、すべての課題がクリアできたわけではない。これまでに再生利用できなかった水資源を再利用可能にする。それを可能にしたのは、歴代の設備担当者たちの試行錯誤があったからだ。
「膜ろ過過程でのフッ酸濃度の上昇要因・ろ過膜詰まりを生むバクテリアの繁殖要因となっていたリン酸の流入経路を明らかにし、濃度を常時監視・流入防止したこと。バクテリア殺菌の強化と、定期ろ過膜洗浄方法の変更によってろ過膜の延命を実現したこと。そして、高価なRO膜を定期のろ過膜洗浄薬品に漬置きして再利用することで、維持費用の削減を行ったこと……。さまざまな改善の積み重ねによって、IWM設備は工程排水の20%以上をリサイクルできるサステナブルな稼働へと転じることができました。この成果は、20年の長期間に及ぶデータと試行錯誤があったから生まれたもの。歴代の担当者たちと共に、この喜びを噛みしめたいと思っています」(荻村)
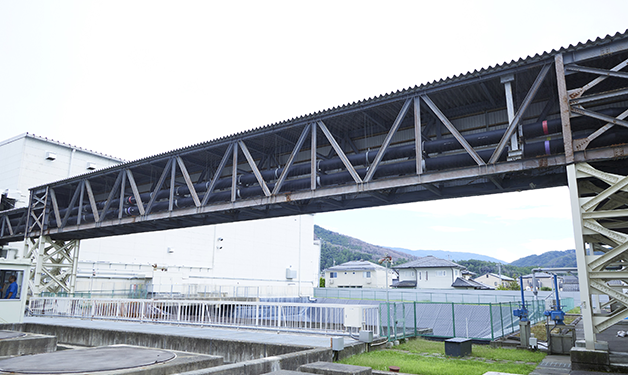
ものづくりを止めず、狙い通りの装置を創る。
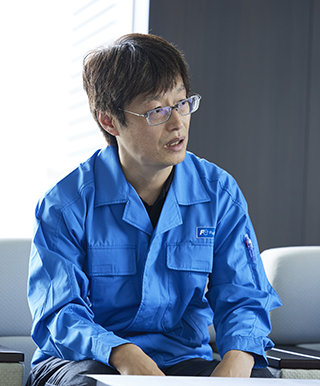
一方、盆地の高台に位置する山梨工場は、事業に利用できる地下水が少なく、工場で使用する水量の20%ほどを占めるのみ。使用する水のほとんどは公共水道から供給される市水に頼らなければならない。山梨工場チップ製造部の市川量一は、山梨工場における水リサイクルの取り組みを次のように説明する。
「市水の供給量には制限がありますし、排水回収量を増加させることは、水道料金の削減にも直結することになります。排水の回収・再利用は、山梨工場で半導体製造を継続するためには必須の取り組みだと言えるでしょう。これまでも、比較的にリサイクルしやすい洗浄後のリンス排水・低濃度薬液排水の酸系排水に関しては回収を行っていましたが、今回、さらに回収量を増やすべく、新たに研削工程排水の回収に着手しました」
研削工程の排水を回収し、リサイクルする。その装置の導入・立ち上げにおいて意識したのは、現場の作業を増やすことなく、既存のものづくりに影響を与えない「自動化した仕組み」を構築することだった。人の手を極力介せず、自動で水資源のリサイクルを行うこと。既設の排水処理装置と新設する研削工程排水回収装置に適した制御システムを作り込むこと。そして、何より、半導体製造を止めることなく、大規模なシステムを起ち上げることには、大きな苦労が伴ったようだ。
「山梨工場の半導体製造が稼働を止めるのは、年間で数日のみ。操業に影響しないように、しっかりと機能するものをつくりあげることが、設備のプロフェッショナルである私たちの使命でした。綿密な打合せとすり合わせを繰り返し、操業の合間を見ながら、試験運転での検証を行う……。狙い通りの回収水が得られ、装置稼働に至ったときの安堵感は今でも忘れることができません。水資源を有効活用した半導体づくりに貢献できた。メンバーたちは一様に、確かな誇りを感じていたようです」(市川)
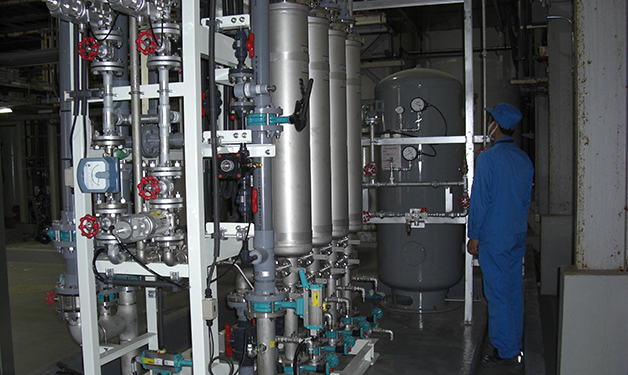
環境貢献製品を、循環型社会に配慮したものつくりで。
メンバーたちの懸命な努力の甲斐あって、一連のプロジェクトは見事に成功。富士電機の半導体製造に必要な水資源のうち、1/4のリサイクルを達成することができた。ここから生まれた「パワー半導体」という製品は、環境貢献製品として脱炭素に貢献するだけでなく、循環型社会にも配慮したものつくりによって生み出されていくことになる。社会の期待に応えて続けていくために。サステナブルな地域環境を守り続けていくために。メンバーたちは、それぞれに想いを抱き、さらなるチャレンジに向き合っていこうとしている。
「省エネのキーデバイスである『パワー半導体』のニーズはさらに高まっており、脱炭素社会の実現に向けて、今も増産が続いている状況です。そして、そのニーズに応えていくためには、水の需要がさらに高まっていくことは間違いありません。排水や給水の面でさらなるイノベーションが必要になってくるでしょう。地域の環境に考慮しながら、社会が求めるものづくりを継続する。そのためにも、水資源の利用効率化への努力は、私たちにとっての最重要課題です。これまで以上に強い意志を持ち、メンバー一丸となってその課題に取り組んでいきたいと考えています」(高橋)
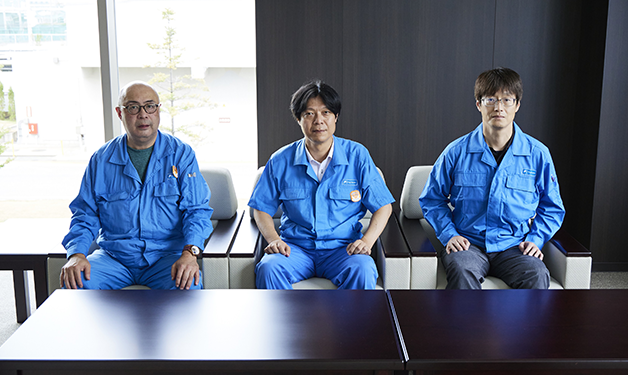
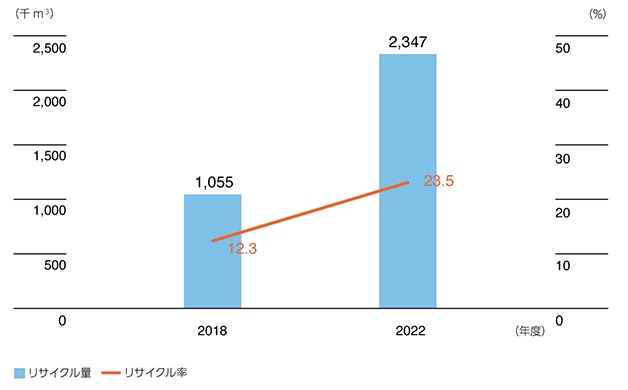
貢献するSDGs目標
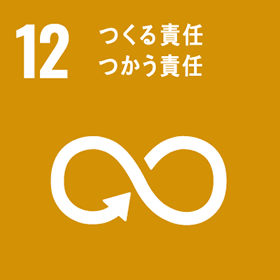
当社は、SDGs目標「12. つくる責任 つかう責任」を当社が取り組む重点目標の一つに掲げており、環境ビジョン2050に基づき、「循環型社会の実現」を目指しています。サプライチェーン全体で3R(リデュース、リユース、リサイクル)を指向した活動を推進し、その一環として、水資源の有効利用および排水基準の遵守に取り組んでいます。