食品工場の基礎知識
機械・設備の7大ロス
機械・設備の7大ロスとは
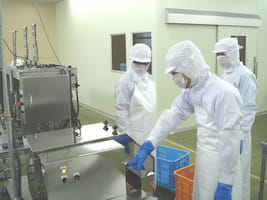
機械・設備の7大ロスとは、設備効率を悪化させる大きな要因のことで、一般に設備の7大ロスなどと呼ばれています。生産効率を上げるためには、このロスをなくしていく必要があります。
食品工場にもさまざまな機械・設備があり、この7大ロスを取り除くための改善策を検討・実行することで、食品工場の機械・設備の生産性向上が期待できます。
配管工事不要で簡単に取付けられ、圧力損失の心配なしに蒸気流量を測定可能。高精度で飽和蒸気の流量を測定し、蒸気流量の「見える化」を実現。EMS連携で省エネにも貢献します。
機械・設備の7大ロス
段取り・調整ロス
段取り・調整ロスとは、製品Aの生産終了から、次の製品Bの良品ができるまでのロスです。生産終了から次の生産を始めるためには段取り・調整が必要になり、このときに発生するロスのことを指します。
段取りや調整作業そのものには付加価値はないため、時間がかかればかかるほど生産性は低下することになります。
消耗品交換ロス
消耗品交換ロスとは、刃具などの消耗品の定期交換や、交換・切り替えなどによって発生する時間的ロスや、調整などによるロスがあります。
立ち上がりロス
立ち上がりロスとは、定期修理後・長期間停止後・休日後・昼休み後などからのスタート時に発生するロスです。機械や生産設備によってはウォームアップや予冷・予熱運転が必要なものがあり、これに伴うロスなどが該当します。
チョコ停ロス
チョコ停ロスとは、設備機能が一時的に停止することや空転している状態によるロスのことです。短時間の停止のため、1回あたりの生産性低下への影響は小さいですが、これが長期間発生し続けていると、累積して大きなロスとなります。
故障ロス
故障ロスとは、設備が突発的・慢性的な故障によるロスです。故障のために生産設備や機械の機能が停止し、さらに修理期間中も稼働できない状況で、結果として生産性が低下してしまいます。
これを防ぐためには予防保全や予知保全などの対策を行うことが有効です。計画的に保全を行うことで、故障から復旧するまでの時間を最小化や、故障する前の異常を検知し、適切なメンテナンスを実施するなどを行うことで、突発的な故障を未然に防ぐことが可能になります。
予知保全によるコスト削減・IoT活用事例。予防保全から予知保全へ保全方式を切り替えることで、メンテナンスコストの低減やいままで対応が難しかった異常値の検知ができるようになります。
速度低下ロス
速度低下ロスとは、設備で設定されている速度と、実際の速度に差がある状態で発生するロスのことです。本来の設備能力が発揮されていない状態であり、設備能力の現状と、速度低下の原因を明確にする必要があります。
不良・手直しロス
不良・手直しロスとは、不用品の発生や、これのための手直しなどのロスのことです。不用品の発生原因の追究や、再発防止策等を検討する必要があります。
重要なのは現状把握と原因の明確化
機械・設備の7大ロスは、生産性の低下の典型的な原因であると言えます。各ロスの対策として共通することは現状把握と原因の追究と明確化が必要であるということです。
現状把握と原因の明確化ができて改善策を実施することが可能になります。原因が明確にできなければ、同じことが繰り返される可能性が高く、結果として生産性が低下するためです。
7大ロス対策とIoT・データ活用
新しい取り組みとして、データを活用した7大ロス削減に向けた取り組みが進んでいます。
近年にIoTやビッグデータに関連した技術革新が進んだことで、製造現場の機械・設備のデータ取得も容易になり、データ分析・活用を進める企業が増え、 これに向けた製品・サービスも充実しつつあることが背景にあると考えられます。
人による対策
人のスキル・経験に依存した対応は、いままで培ってきた経験により、どのようなタイミングで故障が発生しやすいか、どのような部分を確認すれば機械や設備の 状態に問題がないか知っているため、マニュアルに記載されていない問題への対応や部品の交換など判断ができます。
言い換えれば機械・設備の7大ロスに対して、柔軟な作業ができることがメリットになりますが、その作業はマニュアルの精度や個人の経験に依存するため、 ロス対策には個人差・バラつきがあり、同じスキルを持つ人材の育成や、ノウハウの共有・活用することが簡単でないことが考えられます。
例えば、熟練作業者が現場にいれば、マニュアルなどなくとも設備や機械のロスは防げる可能性がありますが、 退職や異動などにより熟練作業者が不在となった場合、簡単に予防できるロスも防げなくなる可能性があります。
データを活用した対策
一方、データを活用した対応の場合は、IoTやセンシングなどにより収集したデータと統計処理により、データ値を確認することで未知の原因の故障予兆や部品交換の必要性を把握することができます。
設備状態のデータを確認することは、これまでの経験に依存せず、データを見る知識は比較的容易に習得することができるため、ノウハウの共有や人材育成に時間がかかりません。 ただし、統計処理に必要なデータが取得できることが前提となるため、これが適用できる範囲は限られます。
例えば、機械部品の交換するタイミングについて、交換判定に必要なデータがそろっていれば、初心者でも部品交換のタイミングを簡単に知ることができます。 反対にデータがなければ、従来の方法に頼らざるを得ません。
データ活用基盤を構築することで、レポーティングの自動化、製造データ解析による品質改善、AI・機械学習の導入も容易になり、食品工場の経営課題の解決や生産性向上を可能にします。
熟練者の知識を活かしつつ、できるところからIoT・データを活用する手法
このように考えると、人のスキル・経験に依存したメンテナンスやデータを活用したメンテナンスどちらに偏っても、大きな成果は期待できない可能性があるのではないでしょうか。
機械・設備の7大ロスを減らしていくためには、熟練者のノウハウを活用しつつ、IoT・データを活用したロス削減の手法を確立できる部分を見つけ出し、仕組み化していく手法が今後進むのではないかと考えられます。