物流倉庫の改善コラム
ピッキングシステムを比較検討するための基礎知識
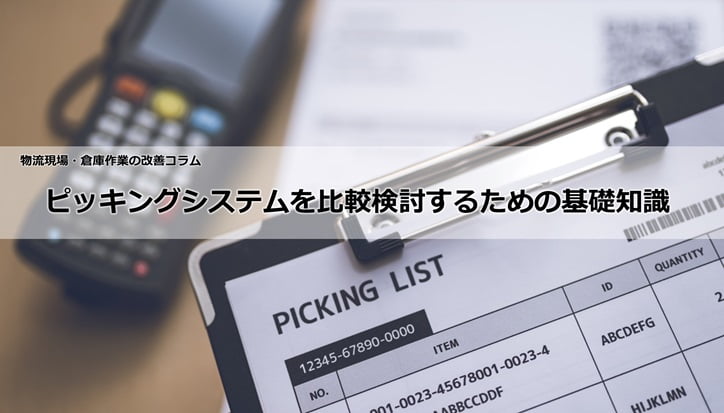
物流倉庫現場では業種業界問わず「仕分け・ピッキング作業のミスをどうすれば減らせるか」、「作業効率をどうすれば改善できるのか」などピッキング作業に関連する課題が必ずあります。貴社の物流倉庫現場ではいかがでしょうか。
近年、ECの拡大や市場ニーズの多様化により、様々な業界で多品種少量生産が進んでいます。このトレンドは今後も続くことが予想され、例えば製造業であれば製品用の部品管理数が増加し、卸売・小売業では取り扱う標品アイテム数が増加傾向にあるということになります。
多品種少量生産が進み、結果として物流倉庫の仕分け・ピッキング作業の作業量が増えれば、ピッキングミスの発生頻度が高くなり、作業時間も長くなります。人手不足の影響により、必要な人材が必要なタイミングで確保できない場合もあります。
これら問題になにも対策をしなければ、生産性の低下や物流品質にもマイナスの影響があるのではないでしょうか。
デジタルピッキングシステムの場合、種まき式・摘み取り式に対応でき、ハンズフリーで初心者でも作業がしやすいメリットがあります。ロケーションの工夫もしやすく、柔軟性がある運用ができるのが特徴です。
このような問題・課題を解決する一つの方法が「ピッキング作業のデジタル化」です。
ピッキングシステムとは
ピッキングシステムとは、簡単に言えば倉庫や工場などで行われるピッキング作業を効率化するための仕組みです。このピッキングシステムにはさまざまな方法がありますが分類すると、大きく2つのタイプに分けることができます。
一つは、ハンディターミナルや表示器のように人の作業を補助するピッキングシステムです。デジタル機器やIT等を活用しピッキング作業を効率化するタイプで、さまざまな業種・業界の物流・倉庫部門で利用されています。
もうひとつは、ピッキング作業そのものを機械化・自動化する方法です。大型倉庫や工場で利用されることがあます。
いずれにも共通するのは、ピッキング作業を仕組み化することによって、物流倉庫現場の課題を解決するという目的で導入されるシステムです。
ピッキングシステムの基本的な仕組み
ピッキングシステムの基本的な仕組みは、紙のリストを使って行っていた「作業指示」「作業記録」「上位システムへ実績データ反映」をデジタルに置き換えたものです。
ピッキングシステムは大きく3つの機能で構成されています。作業者にピッキング指示をだす機能、実績を記録する機能、WMSや在庫管理システムなど他システムと連携するための機能です。
作業指示・実績記録は一般にデジタル機器とシステムが連携する形で利用され、具体的にはデジタル表示機、ハンディターミナル、タブレットPC、スマートフォンなどが利用されています。一般的に作業項目はソフトウェアやWebシステムにより整備されており、この仕様に業務を合わせることでピッキング作業の標準化が可能になります。
また他システム(上位システム)との実績データの連携が可能です。実績データの再入力や手集計の手間とミスをなくすことができます。WMSや在庫管理システムなどの上位システムとの連携は手動もしくはバッチ処理で行われます。
このような機能を活用することで、作業指示・実績管理・システム連携をシステム化することができ、結果としてピッキング作業の仕組み化が可能になります。
ピッキングシステムを導入する5つのメリット
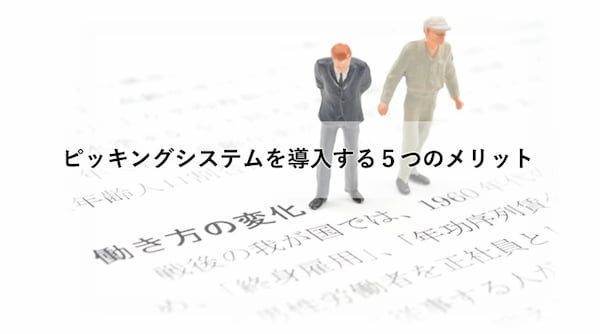
一般的にはピッキングシステムを導入することで、以下のようなメリットが考えられます。
ピッキングシステムを導入するメリット
・ペーパレス化による作業効率化
紙のピッキングリストをデジタル化することで、作業効率が向上します。また、手書きが原因のミスもなくなるため作業効率が向上します。さらに、紙がなくなるため印刷コストや保管コストもなくすことができます。
・人件費の削減
ピッキング作業の効率化により、作業員一人当たりの作業量が増加します。例えば、いままで10人でピッキングしていた作業工程が、7人で作業できるようになり、3人分の人件費を削減することが可能になります。
・ピッキング作業の標準化による生産性向上
ピッキングシステムを導入することで、ピッキング作業の標準化が可能になります。標準化することで初心者でも熟練者と同等の作業が可能になり、ピッキング作業の生産性向上が期待できます。
・作業ミスの抑止/物流品質の向上
デジタル機器やITを活用することで、作業ミスを防止することができます。例えばタブレット上にアラートを出したり、RFIDでミスを予防したりすることが可能になります。作業者のスキルに依存せず仕組みでミスを防ぐことができることで、誤出荷やピッキングミスを減らすことができます。結果的に物流品質の向上が可能になります。
・実績管理の効率化
ピッキングシステムを活用することで、実績データがすべてデジタルで記録されるようになります。これにより、WMS(倉庫管理システム)や在庫管理システムなどのへの入力作業や転記作業をなくすことができるため、実績管理にかけていた時間を削減でき、ミスも減らせます。
このようにピッキング作業をシステム化することによって、ピッキング作業の生産性向上・効率化が可能になります。
ピッキングシステムの3つのデメリット
ピッキングシステムを導入したからといって必ずしも期待する効果が得られない場合があります。とくに紙のピッキングリストを使った運用から、ピッキングシステムに切り替えを検討する際は注意が必要です。
ピッキングシステムの3つのデメリット
・例外対応、緊急対応がむずかしい
何らかの理由により、計画外の仕分け・ピッキング作業を行う必要がある場合はピッキングシステムの利用が追い付かない場合があります。例外対応が多い場合は、紙によるピッキング作業の方がよい場合もあります。
・投資対効果がわかりにくい
現行のピッキング作業の規模によっては、ピッキングシステムを導入しても投資対効果が期待できない場合があります。
・システムの運用管理が必要
ピッキングシステムを導入した後、このシステムを運用管理する人材が必要になります。どれだけ高機能なピッキングシステムを導入したとしても、運用管理する人材がいなければ結局使われないシステムとなってしまう可能性があります。
上記をまとめると、ピッキングする対象となる商品アイテム数が少ない場合や、例外対応が多い物流倉庫現場ではピッキングシステムの導入が難しいということになります。
ピッキングシステムの比較検討時に確認すべき3つのポイント
ここまで主要なピッキングシステムに関する基礎知識やデジタルピッキングシステム導入動向について解説しました。続いて、導入・運用面からピッキングシステムを見た場合に確認すべき3つのポイントについて説明します。
種まき方式と摘み取り方式
ピッキング作業は種まき方式(シングルピッキング)と種まき方式(トータルピッキング)に分類できます。
・摘み取り方式(シングルピッキング/オーダーピッキング/リストピッキング)
摘み取り方式はオーダー(発注伝票)をうけ、保管場所から商品等を取り出す作業のことです。単一のオーダーの場合は特にオーダーピッキングと呼ばれることがあります。この他、摘み取り方式/ケース単位で行う場合はケースピッキングといわれます。
この方式は出荷数が多く、商品アイテム数が少ない場合に適しています。ピッキング作業が簡単なことが特徴です。一方で、オーダー単位で作業するため、作業に時間がかかったり、作業者の移動距離が長くなったりする傾向があります。
・種まき方式(トータルピッキング/アソート方式)
種まき方式はオーダーされた商品をまとめて保管場所からとりだしして、その後、荷さばき場などで発送先毎に仕分けを行う作業のことです。この方式は出荷数が少なく、商品アイテム数が多い場合に適しています。商品単位でまとめて作業するため、移動距離と時間が短縮できることが特徴です。一方で、一度に仕分け作業を行うだけの荷捌きスペースを確保する必要があります。
ピッキングシステムを選定する場合には、このどちらの方式に対応しているかを確認する必要があります。
無線式と有線式
ピッキングシステムの導入・利用方法には無線式と有線式があります。
例えばデジタル表示機を使ったピッキングシステムの場合、無線式の表示機と有線式の表示機が選べます。無線式は配線工事がないため導入が簡単で自由度も高いですが、充電には手間がかかります。一方で、有線式の場合は工事が必要で、ロケーションの変更があるたびに配線の見直しが必要ですが、充電する手間がいりません。
ピッキングシステムを導入することは、ピッキング作業が見直される機会でもあります。どのようなピッキング作業を理想とするかにより、ピッキングシステムを無線にするか有線にするか検討する必要があります。
オンプレミス型とクラウド型への対応状況
ピッキングシステムにはクラウド型とオンプレミス型があります。
ピッキングシステムをクラウド型で導入する場合は、初期費用を抑えることができ、サーバーそのものの管理も不要になるというメリットがあります。デメリットは、カスタマイズが難しいこと、既存システムとの連携する場合、手動で行う作業がのこる場合が多いことです。また、インターネットを介するのでセキュリティ面での配慮が求められます。
一方、オンプレミス型でピッキングシステムを導入する場合は、クラウドと比較して初期費用がかかり、管理も必要になることがデメリットになります。メリットは既存システムとの連携が比較的容易で、カスタマイズもしやすく、既に自社でサーバー室やデータセンターを持っている場合はトータルコストを抑えることができるというメリットがあります。
ピッキングシステムを提供している企業により、提供形態がことなるため、事前にクラウド型かオンプレミス型かの確認が必要になります。
物流倉庫で活用される様々なピッキングシステム
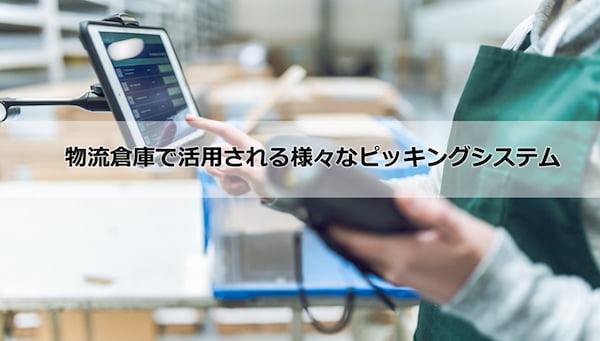
ピッキングシステムにはさまざまな種類があります。ピッキングシステムを比較検討するためには、ピッキングシステムにどのような種類があるのか知っておくことが重要です。
どのようなピッキングシステムの選択肢があるのか、どのようなメリット・デメリットがあることを知っておくことで、自社の課題にあったピッキングシステムを見つけることが可能になるからです。
-
デジタルピッキングシステム(DPS:Digital Picking System)
-
デジタルアソートシステム(DAS:Digital Assort System)
-
タブレットピッキングシステム
-
スマートフォンピッキングシステム
-
音声認識/ボイスピッキングシステム
-
プロジェクションマッピングによるピッキングシステム
続いて、これらのピッキングシステムを詳しく説明します。
デジタルピッキングシステム(DPS:Digital Picking System)
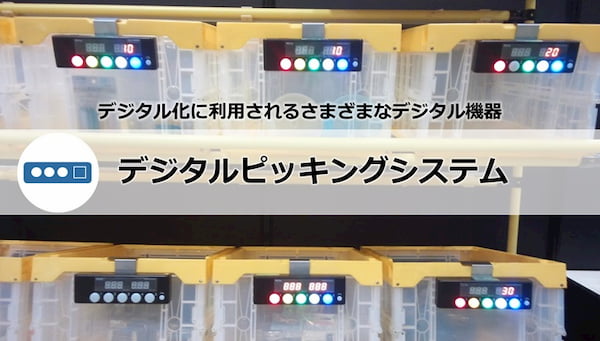
デジタルピッキングシステムとはデジタル表示機を活用したピッキング作業支援システムのことです。略称はDigital Picking Systemの頭文字をとり、DPS(ディー・ピー・エス)と呼ばれます。近年ではデジタル機器を利用したピッキングシステムを総称してデジタルピッキングシステムと呼ばれる場合もあります。近年では省エネのためランプがLEDに対応しているものが多くLED/ランプ式のピッキングシステムとも言えます。
ピッキング指示をデジタル表示器で作業者に知らせることができるのが特徴で、主に摘み取り式のピッキング作業に適用されます。デジタル表示機はカゴ車・商品棚・オリコン等に取り付けることができます。
ピッキング指示に従いランプが点灯、数量情報を表示できるようになっています。作業者はランプが点灯した場所に行き、表示器に表示された個数の商品や部品を必要個数ピッキングすることができます。
この仕組みを活用することで、作業者は商品や部品を知らなくともピッキング作業ができるようになり、結果としてピッキング作業の効率化やペーパレス化が可能になります。
デジタルアソートシステム(DAS:Digital Assort System)
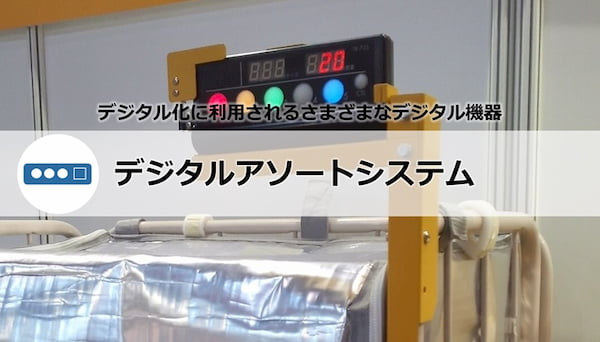
デジタルアソートシステムとは、デジタル表示機を活用した仕分け作業(アソート)を支援するシステムです。略称ではDigital Assort Systemの頭文字をとり、DAS(ダス)と呼ばれます。
デジタルアソートシステムはデジタルピッキングシステムと仕組みとしては同じで、デジタルピッキングシステムの機能を兼ねる場合が多い傾向にあります。そのためこの2つをまとめてデジタルピッキングシステム(DPS/DAS)とする場合もあります。こちらも省エネのためLED/ランプ式のピッキングシステムが主流となりつつあります。
仕分け先ごとにカゴ車・棚・オリコン等を準備し、取り付けられたデジタル表示器で作業者に指示することができるのが特徴です。例えば倉庫から商品を出し、出荷先ごとに仕分けするといった作業に適しています。
仕分け指示を出すと、出荷先の場所のランプが点灯、数量情報が表示されます。作業者はランプが点灯した場所に行き、表示器に表示された個数の商品を必要個数仕分けしていきます。
この仕組みはデジタルピッキングシステムと同様に仕分け作業者は商品知らなくとも作業ができるので、結果としてピッキング作業の効率化やペーパレス化が可能になります。
タブレットピッキングシステム
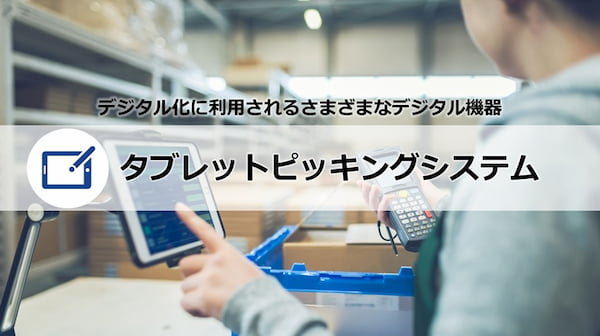
タブレットピッキングシステムとは、タブレットPCを活用してピッキング先や数量、商品・部品の画像やマップ情報等を表示してピッキング作業をサポートするシステムのことです。タブレット端末はハンディターミナル同様に多機能で、操作性もよく、台車と組み合わせてマルチピッキングカートとして利用したり、マテハン機器と組みあわせて利用できるのが特徴です。
商品や部品アイテム数が多い場合、棚毎に表示機を付ける必要があるデジタルピッキングシステムではアイテム数分の表示機が必要になってしまいますが、タブレットピッキングシステムの場合はタブレット上で棚の場所の確認や必要数量が確認できるため導入費用を抑えることができます。
特に製造業のように同じような部品が多い物流倉庫や工場で導入が進んでおり、部品ピッキングシステムとして利用することで誤取り出しを防ぐことができます。工場向けのピッキングシステムであり、富士電機東京工場でもこのタブレットピッキングシステムと部品ピッキングシステムとして導入しています。
スマートフォンピッキングシステム
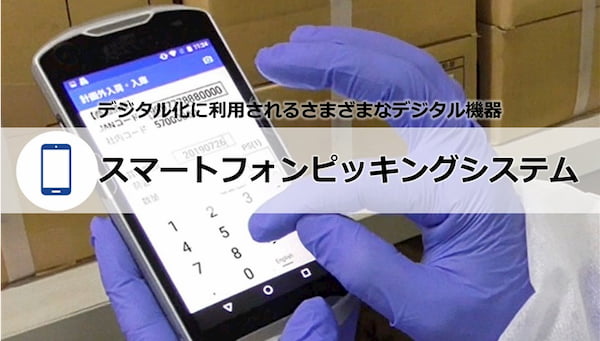
スマートフォンピッキングシステムとは、ハンディターミナルの代わりにスマートフォンを利用したピッキングシステムです。スマートフォンはハンディターミナルと比較すると安価で、導入費用を抑えてピッキングシステムを構築したいという物流倉庫現場に適しています。
ハンディターミナル同様にデータの入力・修正が可能で、バーコードの読み取りにも対応できます。また、普段使い慣れているスマートフォンと同様に簡単に操作できるのが特徴です。重さや大きさもハンディターミナルより軽量・小型なため携帯性(持ち運びしやすさ)も優れています。ピッキング作業、棚卸、入出荷検品などの作業に利用可能です。ピッキング作業のうちとくに、ケースピッキングに適しています。
音声認識/ボイスピッキングシステム
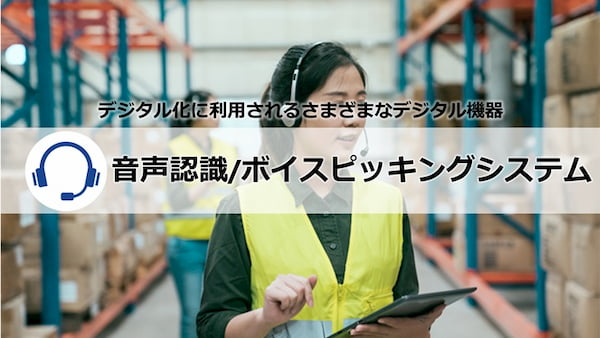
音声認識/ボイスピッキングシステムとは、ピッキング作業の指示を音声で行うピッキングシステムです。作業者はヘッドセット(イヤホン+マイク)を装着して、ピッキング指示を音声(アナウンス)で受け、音声による確認(返答)を行うことができます。
この仕組みにより、作業者は紙やタブレットを見たり、入力したりすることが不要になるためパーパレス化とハンズフリー化が可能になります。また、見る作業をピッキングに集中することができるため、作業ミスを減らしたり、商品の取り扱いに注意を払うことが可能になります(アイズフリー)。
複雑なマテハン機器の操作を覚えることと比較すると、受け答えのシンプルなルールを覚えれば作業が可能です。また、フォークリフトなどのマテハン機器を操作しながらも利用できるため、様々な物流倉庫現場で利用できるメリットがあります。
プロジェクションマッピングによるピッキングシステム
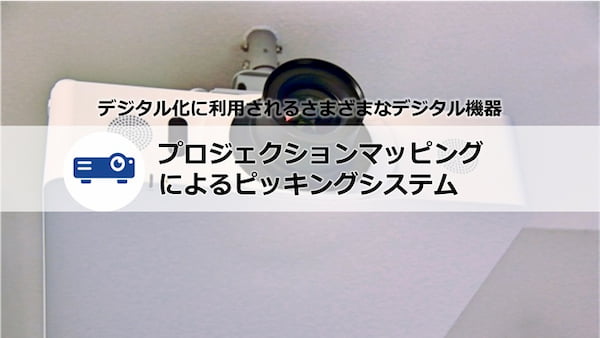
プロジェクションマッピング(Projection Mapping)とは、プロジェクターなどを用いて物体の表面や空間に映像を映す技術のことです。これをピッキング作業に適用したのが、プロジェクトマッピングによるピッキングシステムです。
映像投影によりピッキング指示が出せるので、作業者に分かりやく、配線が不要で、投影するデータや対象を変えればさまざまなものに応用できることにメリットがあります。
このように人の作業を補助する機能を持ったピッキングシステムだけでも様々な種類があります。したがって、自社の課題にあったピッキングシステムを選択するには、どのようなピッキングシステムの選択肢があり、どのようなメリット・デメリットがあるのかを検討することが必要になります。
ピッキングシステムは2000年以前からある考え方ですが、実際にどれぐらいの利用が進んでいるのでしょうか。上記で紹介したデジタルピッキングシステムを例に、活用状況や導入・検討のきっかけなどの利用動向を以下で詳しく説明していきます。
デジタルピッキングシステムの利用動向
富士電機はピッキングシステムの利用動向を把握するために「製造業におけるピッキング作業のデジタル化とデジタル機器の利用動向調査」を実施しました。この調査ではピッキング作業のデジタル化の動向に加えて、導入効果の有無や、どのようなデジタル機器を利用しているのかなどについて調査しました。
調査概要についての詳しい内容については「製造業におけるピッキング作業のデジタル化とデジタル機器の利用動向調査」で調査結果を公開しておりますので、こちらをご覧ください。
ここでは、調査結果のうちデジタルピッキングシステム/デジタルアソートシステムを例にピッキングシステムの利用動向を説明します。
物流倉庫現場では種まき・摘み取りを併用する割合が高い
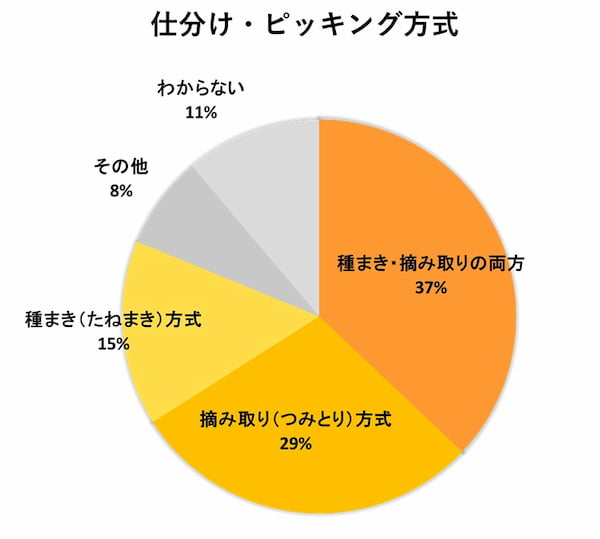
富士電機が実施した「製造業におけるピッキング作業のデジタル化とデジタル機器の利用動向調査」によると、仕分け・ピッキング作業の方式については「種まき・摘み取りの両方」を採用しているとの回答が最も多い結果となりました。一方で、「摘み取り(つみとり)式」のみ実施しているとする回答は全体の29% 、「種まき(たねまき)式」とのみの回答は全体の15%となりました。
製造業におけるデジタルピッキングシステムの利用は今後90%を超える
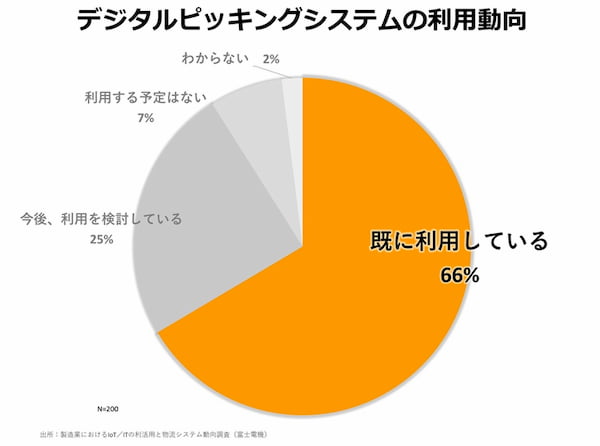
同調査のデジタルピッキングシステムの利用状況に関する設問では 「既に利用している」 との回答は全体の66%となりました。「今後、利用を検討している」の回答を含めると90%を超えます。
続いて、デジタルアソートシステムについて「既に利用している」 との回答は全体の51%となりました。「今後、利用を検討している」の回答を含めると79%となりました。
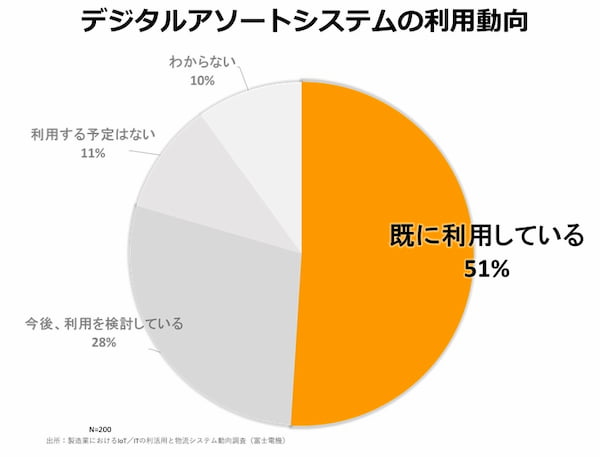
それぞれ商品アイテム数別に利用状況を集計すると、「利用する予定はない」との回答は商品アイテム数に関係なく約1割ありました。
つまり、多くの物流倉庫でデジタルピッキングシステムが利用されており、今後の予定を含めるとデジタルピッキングシステムを利用していない現場は少数派であることを意味しています。
導入・検討のきっかけは「生産性向上」「ミスの削減」
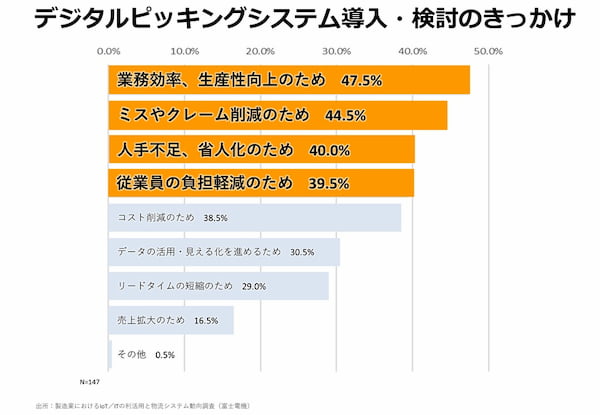
同調査で「デジタルピッキングシステム/デジタルアソートシステム導入・検討のきっかけ」に関する回答では、導入・検討したきっかけは「生産性向上」「ミスの削減」「人手不足の解消」や「従業員の負担軽減」などの回答が上位となりました。
「生産性向上」は企業活動のひとつとして重要です。「ミスやクレームの削減のため」は、物流品質の向上するためには改善しなければなりません。また、「人手不足の解消」や「従業員の負担軽減」は物流倉庫現場の働き方改革に寄与します。
「コスト削減」は2つの意味があると考えられます。一つは人件費の削減、もう一つは作業時間の削減で、これらの削減は結果的にコスト削減になるからです。「データの活用・見える化」は人の経験などに頼らず、論理的にデータを活用した生産性向上をする必要があるということを意味します。「リードタイムの短縮」「売上拡大」は生産性向上に寄与します。
導入のきっかけとは言い換えれば現状の物流倉庫現場の課題ということになります。このような課題解決のためにピッキングシステムの導入が検討されています。
導入しない理由は「導入効果が期待できない」「従業員が使いこなせない」
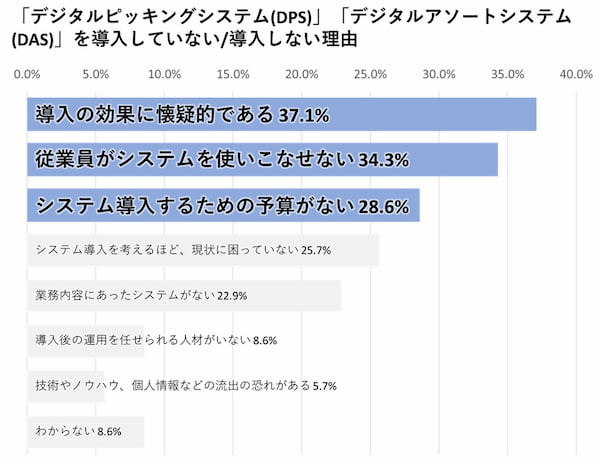
ピッキングシステムの導入を企画した場合でも、会社の都合により導入を見送るという場合もあります。
富士電機の調査結果によると、導入していない/導入しない理由については「導入効果に懐疑的である」の回答が最も多い結果となりました。次いで、「従業員がシステムを使いこなせない」「業務内容にあったシステムがない」などの理由が上位にとなりました。
「導入効果に懐疑的である」とは「デジタルピッキングシステムを導入しても効果がきたいできない」という意味です。言い換えれば、導入効果が期待できれば導入を検討する余地があること意味し、自社の物流倉庫の課題解決ができる可能性があるということになります。
「従業員がシステムを使いこなせない」は、いかに最新のテクノロジーを導入したとしても、それが使えなければ意味がありません。多機能であっても実際に使わない機能が多く、機能が多いことで作業員への教育に時間がかかるなど別の問題も出てくる可能性があるからです。
まずは物流倉庫の課題整理から
ここまで主要なピッキングシステムに関する基礎知識、デジタルピッキングシステム導入動向や確認すべきポイントについて解説しました。
選択肢としてどのようなピッキングシステムがあるのか、どのようなメリット・デメリットがあるのか、費用対効果が期待できるのか、などを考慮することで、物流倉庫の現場に適したピッキングシステムを比較検討が可能になります。
ピッキングシステムには多様でそれぞれにメリット・デメリットがあります。ピッキングシステムを複数導入している企業も少なくなく、場合によりピッキングシステムを適材適所で導入する必要があるため、自社の課題分析は重要です。
なぜなら自社の状況把握・課題が不明確なままでは導入したものの費用対効果がよくわからず、操作が難しすぎて現場の作業に利用できないということも考えられるためです。
これからピッキングシステムを検討する場合は、まずは自社物流倉庫の課題を明確にすることからはじめではいかがでしょうか。
業務改善を進めるためには現状を把握することが必要です。このサービスは「物流現場のIT化や自動化を検討したい」と考えている企業様向けに、物流・倉庫現場のデータを分析し、改善方針とその改善効果を、簡易的に報告するサービスです。