物流倉庫の改善コラム
ピッキングシステムに活用される機器の種類と選び方
.jpg)
物流倉庫で利用されるピッキングシステムはさまざまです。ピッキングシステムを複数システム利用・導入している物流倉庫も多いのではないでしょうか。
ピッキングシステムを導入することで、作業生産性が改善したり、作業ミスが減り物流品質向上や在庫管理制度の高度化が期待されます。
富士電機の独自調査「製造業におけるピッキング作業のデジタル化とデジタル機器の利用動向調査」では、ピッキングシステム(DPS/DAS)を導入検討のきっかけは「業務効率、生産性の向上のため」「ミスやクレーム削減のため」「人手不足、省人化のため」が上位を占める結果となりました。
一般にピッキングシステムを導入する場合は、物流現場の課題整理し課題解決のためのピッキングシステムを選ぶ必要があり、このためにはどのような特徴があるかを理解しておくことは有益です。
店舗向け出荷仕分けを紙のリストからデジタルピッキングシステムへ。ペーパレス化により作業効率があがり、仕分けミスも削減に成功。仕分け作業の標準化を実現しました。
以下ではピッキングシステムに活用される機器の種類と選び方について詳しく説明します。
ピッキングシステムに活用される機器の種類と選び方
ピッキングシステムにはさまざまな種類がありますが、おおきく2つの機能に分けることができます。ひとつは上位システム(WMSや在庫管理システムなど)と連携するシステム部分と、もう一つは作業者が実際に使うデジタル機器の部分です。
-
デジタルピッキングシステム(DPS:Digital Picking System)
-
デジタルアソートシステム(DAS:Digital Assort System)
-
タブレットピッキングシステム
-
スマートフォンピッキングシステム
-
音声認識/ボイスピッキングシステム
-
プロジェクションマッピングによるピッキングシステム
システム部分については主に管理側が利用する機能です。WMSや在庫管理システムと連携することが一つの役割であるため、ピッキングシステム間で大きな差がでにくい傾向があります。導入方式としてはクラウドやオンプレミス、連携方式でバッチ式、APIによるリアルタイム連携などがあり、どのような構成をとるかで使える機能が変わってきます。
デジタル機器とは具体的にはハンディターミナル、デジタル表示器、スマートフォン、タブレットPCなどがあります。デジタル機器は作業者が直接操作する/作業を支援するもので、選定ポイントとしては作業生産性だけではなく使いやすさが重要になってきます。
理由はどのような最新のテクノロジーや機器を採用したとしても、作業者が利用できない機器であれば使われないからです。システムが使われなければ、結局は手作業や例外対応が多くなり、生産性や物流品質の低下する可能性があります。
では、ピッキングシステムを導入した場合、どれぐらいの割合で導入効果がでるのでしょうか。
ピッキングシステムの導入効果の動向
富士電機では製造業を対象にピッキング作業のデジタル化とデジタル機器の利用動向を調査し、デジタルピッキングシステム及びデジタルアソートシステムの導入効果有無について調べました。
デジタルピッキングシステムの利用動向
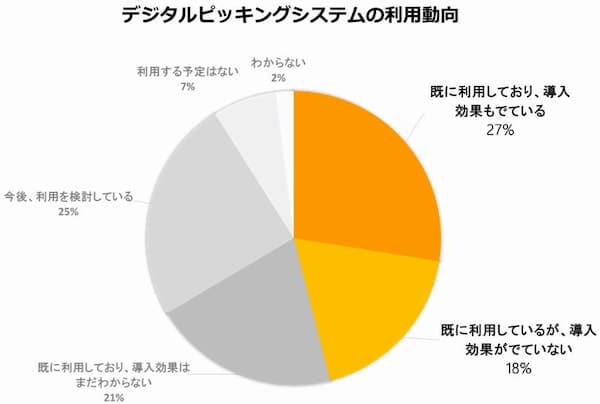
デジタルピッキングシステムとは
デジタルピッキングシステムはデジタル表示機を利用したピッキングシステムです。略称ではDPS(ディー・ピー・エス:Digital Picking System)と呼ばれます。主に摘み取り方式のピッキング作業に利用されます。
デジタルピッキングシステムで導入効果ありは約3割
「製造業におけるピッキング作業のデジタル化とデジタル機器の利用動向調査」によると、デジタルピッキングシステム(DPS)を「既に利用している」とした回答は全体の66%となりました。「既に利用している」「今後、利用を検討している」を含めるとDPSの利用意向は9割を超え、多くの物流倉庫現場で利用されているピッキングシステムだということがわかります。
「導入効果がでている」という回答は全体で27.5%となっている一方で「既に利用しているが、導入効果がでていない」との回答は全体で18.5%となりました。導入済みの回答から「導入効果がまだわからない」を除いた回答数に対する導入効果が出ていない割合は約40%という結果になりました。
デジタルアソートシステムの利用動向
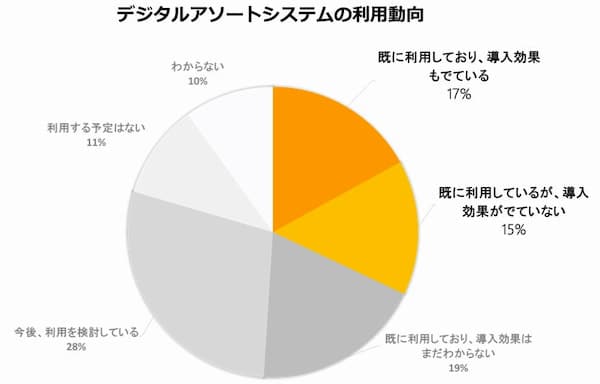
デジタルアソートシステムとは
デジタルアソートシステムもデジタルピッキングシステム同様にデジタル表示器を活用したピッキングシステムです。略称ではDAS(ダス:Digital Assort System)と呼ばれます。主に種まき方式のピッキング/仕分け作業に利用されます。
デジタルアソートシステムでは導入効果ありは約2割
同調査でデジタルアソートシステム(DAS)を「既に利用している」とした回答は全体の51%となりました。「既に利用している」「今後、利用を検討している」を含めるとDASの利用意向は約8割となり、デジタルピッキングシステム同様に普及しているピッキングシステムであると考えられます。
「導入効果がでている」という回答は全体で17%となっている一方で「既に利用しているが、導入効果がでていない」との回答は全体で15%となりました。導入済みの回答から「導入効果がまだわからない」を除いた回答数に対する導入効果が出ていない割合は約47%という結果になりました。
この調査からピッキングシステムを導入することで、必ずしも導入効果が得られるわけではないことがわかります。
導入効果が得られない場合に考えられる3つの要因
ピッキングシステムを導入しても、ピッキング作業が改善しない場合は以下の3つの要因が関連している場合があります。
ピッキングシステムと作業規模があっていない
ピッキングシステムは現場の課題に合わせた選択が必要になります。機能が多すぎたり、ピッキングシステムの性能と実際の作業が合わなければ導入効果は得られません。
例えば、仕分け先が50間口(店舗)しかないのにピッキングシステムはかならずしも必要としない場合があります。アイテム数が少ない倉庫現場では、マルチカートピッキングシステムよりデジタルピッキングシステムが低コストで、簡単に導入できる場合があります。
必要な機能が不足している
ピッキングシステムに必要な機能がなければ、課題解決が難しくなる場合があります。例えばシステム連携やチェック機能など、機能が業務効率化に直結するものがこれに該当します。
ピッキングシステムに必要な機能がなければ、例外対応や手動で対応することが必要になります。手動の作業をすることは、作業ミスが発生しやすくなったり、自動化と比較すると作業時間が長くなります。このような対応を余儀なくされることで、結果的に導入効果が得られないということが考えられます。
ピッキングシステムが複雑で利用が進まない
最新のテクノロジーを活用したピッキングシステムを導入しても、作業現場で利用できなければ導入する意味はありません。
例えばピッキング作業については季節変動があるなどの理由によりパート・アルバイト比率が高い傾向にありますが、複雑なピッキングシステムを導入した場合はシステムを使うための「ガイドライン」や「マニュアル」を準備し、かつ、教育訓練が必要になります。
このようにピッキングシステムの導入効果が得られない原因の一つは、物流倉庫現場の課題とピッキングシステムが合っていないことであると考えることができます。
ピッキングシステムを選ぶ際の3つのポイント
ピッキングシステムを選定する際には、どのようなことに気を付ければよいでしょうか。ピッキングシステムの選定基準はさまざまですが、共通する選定ポイントをいくつか紹介いたします。
商品アイテム数
物流倉庫で取り扱っている商品アイテム数からピッキングシステムを選定する方法があります。商品アイテム数が100程度の場合と、1000を超える場合とでは最適なピッキングシステムは異なります。
商品アイテム数に対してどのピッキングシステムが適当なのかに関する明確なガイドラインはありません。方法としてはピッキングシステムを販売するメーカーに提案を求めたり、後述する「商品アイテム数別でみるデジタル機器利用動向」を参考にすることで、ピッキングシステムを絞り込むことが可能です。
既存システムとの連携有無
一般にピッキングシステムは上位システム(WMSや在庫管理システムなど)からの作業指示を受けることによって作業が可能になります。
従って、既存の上位システムとの連携ができるか・できないのか・連携するためには個別対応が必要なのかについて事前確認することは重要になります。このシステム間連携が手動の場合と、自動の場合とでは作業効率に大きな差がでてきます。
使いやすさ・教育訓練のしやすさ
ピッキングシステムが簡単で分かりやすい仕組みであれば、教育訓練の期間は短く済み、用意するマニュアル等も少なく済みます。
例えば操作がシンプルで操作も覚えやすければ、ピッキング作業の初心者やパート・アルバイトでも即戦力として仕事ができることが期待できます。
このようにピッキングシステムを選択する基準を考慮し、物流現場の課題解決できる仕組みを構築することで、期待する導入効果を得られる可能性を高めることができます。
商品アイテム数別でみるデジタル機器利用動向
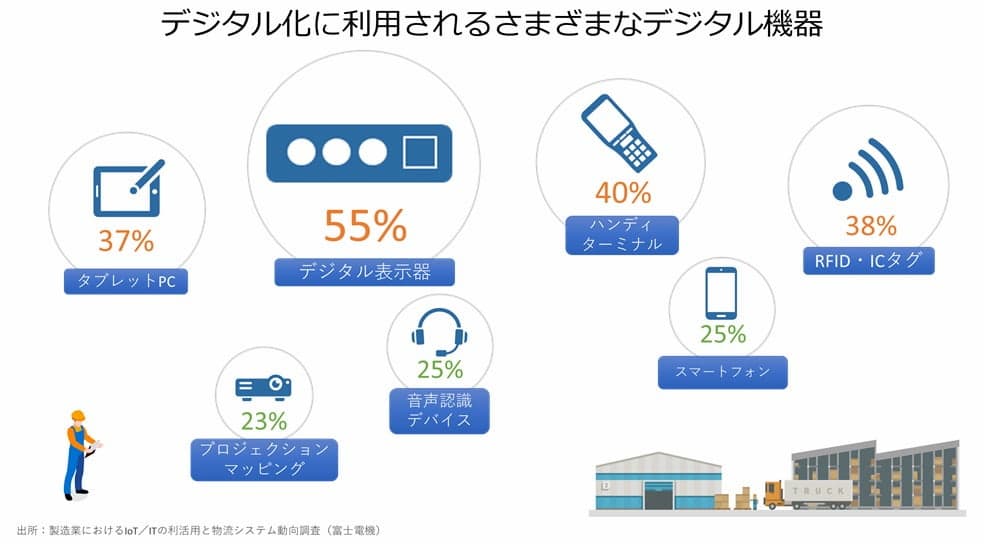
富士電機が実施した「製造業におけるピッキング作業のデジタル化とデジタル機器の利用動向調査」内で「仕分け・ピッキング作業に活用している、もしくは今後活用を予定しているデジタル機器・技術」について調査しました。
調査の結果、現在活用している・活用が見込まれているデジタル機器については 「デジタル表示機」で55.4%、次に多いのが「ハンディターミナル」で40.1%、次いで「RFID・ICタグ」が38.1%、「タブレットPC」36.5%という回答結果になりました。
この回答は複数回答によるもので、ピッキングシステムを用途に合わせて複数導入しているとの回答結果も多くありました。経験的に物流倉庫現場では現場の課題に合わせて、適切なデジタル機器を選択したり、併用して利用していると推定されます。
続いて、主なデジタル機器の特徴と商品アイテム数別でどのような利用動向があるのかについて解説します。あくまで調査結果でしかありませんが、一つの傾向として把握しておくことで、自社の物流倉庫現場にどのようなデジタル機器が適用できそうか考える判断材料として利用できます。
デジタル表示機
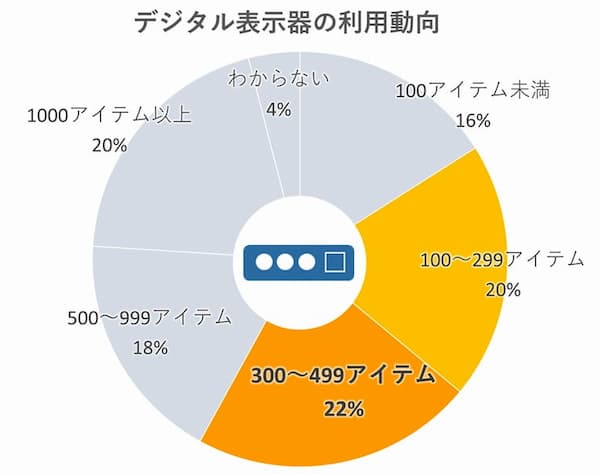
「デジタル表示機」はボタンを押すという操作で仕分け・ピッキング作業ができるのが特徴です。複雑な操作を必要としないので、作業のシンプル化をしたい場合に適しています。
デジタル表示機は主に「デジタルピッキングシステム」「デジタルアソートシステム」に利用されます。
「デジタル表示機」の商品アイテム数別利用動向では、300以上~500アイテム未満で多く活用されているという結果になりました。デジタル表示機は直観的に利用できる一方で、棚やカゴ車に1台取り付ける必要があるため、規模が大きくなるほど導入費用が膨らむ傾向にあります。
ハンディターミナル
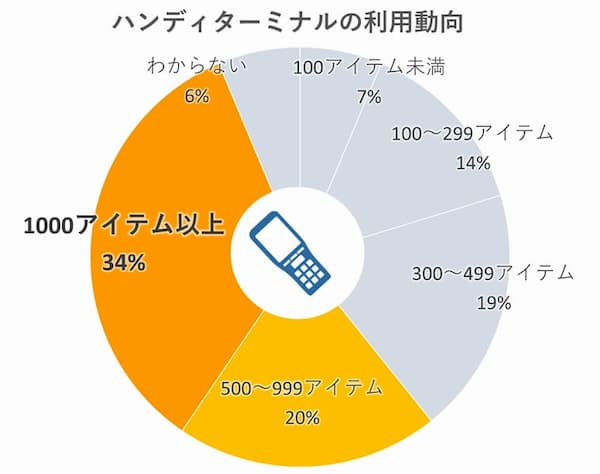
「ハンディターミナル」は多機能で、バーコードの読み取りに優れています。取り扱える情報量も多いため、様々な業務に利用されています。
ハンディターミナルは多機能ため、さまざまな倉庫業務に利用できます。また、他のピッキングシステムと組み合わせて利用されることもあります。
「ハンディ―ターミナル」の商品アイテム数別利用動向では、1000アイテム以上で多く活用されているという結果になりました。機能が多く、取り扱えるデータ量が多いため、商品アイテム数が多いほど有効に機能し、小規模での利用の場合は、機能が多すぎて使いこなせないという可能性が考えられます。
タブレットPC
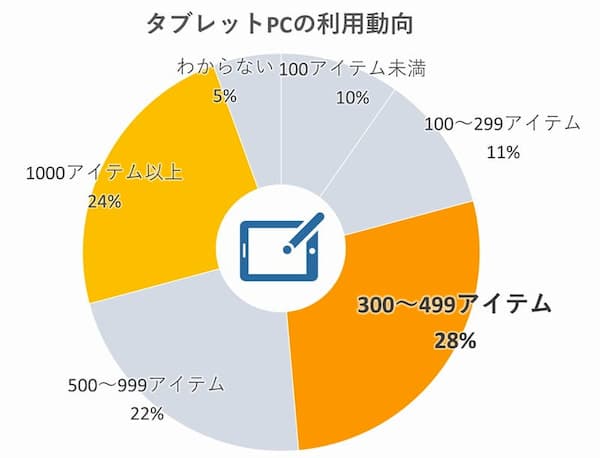
「タブレットPC」は他の機器と比較して画面が大きく、画像やマップの表示ができるのが特徴です。タブレットPCは主に「タブレットピッキングシステム」に利用されます。
単体利用の他、ピッキングカートと組み合わせることで、マルチピッキングカートシステムとして利用できます。
「タブレットPC」の商品アイテム数別利用動向では、300以上~500アイテム未満で多く活用されているという結果になりました。全体でみると商品アイテム数を意識することなく利用されているという特徴があります。
スマートフォン
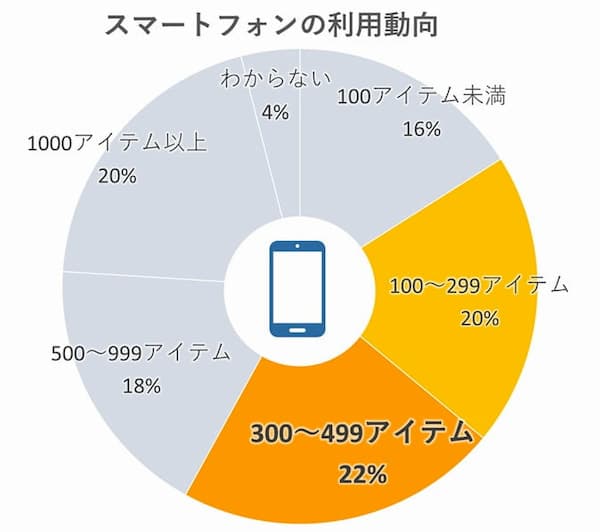
「スマートフォン」は操作性・携帯性に優れているのが特徴です。ハンディターミナルと比較する調達しやすく、機能の拡張もしやすいメリットがあります。
スマートフォンは多機能ため、ハンディターミナル同様さまざまな倉庫業務に利用できます。また、他のピッキングシステムと組み合わせて利用されることもあります。
「スマートフォン」の商品アイテム数別利用動向では、300以上~500アイテム未満で多く活用されているという結果になりました。ハンディターミナルより商品アイテム数が少ないところでの利用が多いのが特徴です。
音声認識デバイス
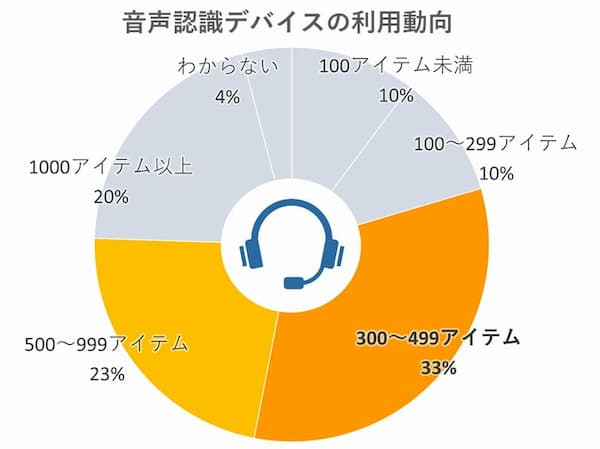
「音声認識デバイス」は音声によるピッキング作業指示と応答で仕分け・ピッキング作業ができるのが特徴です。ハンディターミナルを操作したり、紙に記入するといった作業がないためハンズフリー化が実現でき、他のマテハン機器と組わせて利用することも可能です。
音声認識デバイスは「音声ピッキングシステム」「ボイスピッキングシステム」に利用されます。
「デジタル表示機」の商品アイテム数別利用動向では、300以上~500アイテム未満で多く活用されているという結果になりました。
プロジェクションマッピング
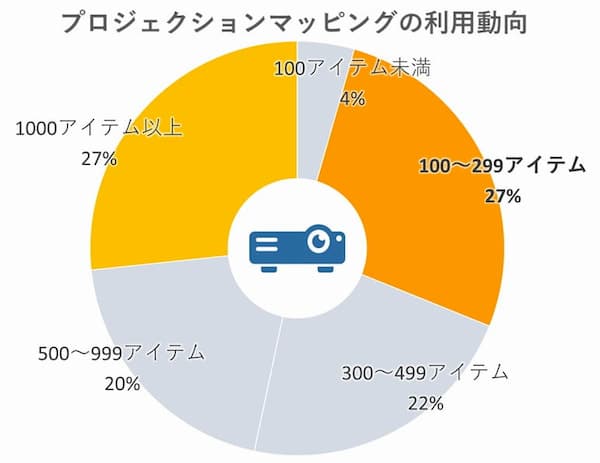
「プロジェクションマッピング」はプロジェクターを棚などに画像投影することでピッキング作業指示を行う仕組みです。棚への投影によりデジタル表示機のような配線が不要で、投影するデータや対象を変えることが簡単にできるのが特徴です。
「デジタル表示機」の商品アイテム数別利用動向では、300以上~500アイテム未満で多く活用されているという結果になりました。
デジタル機器別・ピッキングシステム比較表
ここまでピッキングシステムに利用されるデジタル機器の利用動向について紹介しました。各デジタル機器の特徴と商品アイテム数別の利用動向をまとめると以下のようになります。
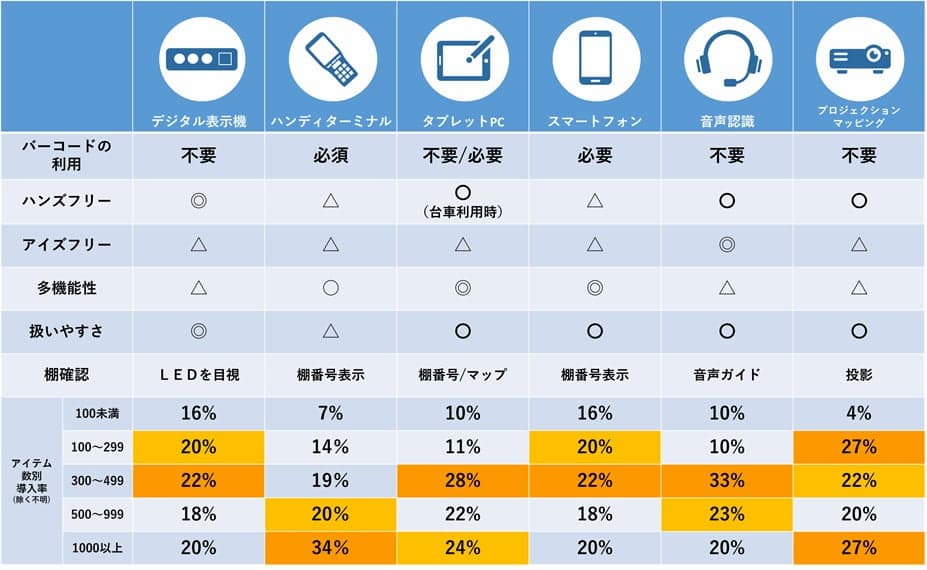
このようにデジタル表示機、ハンディターミナル、タブレットPC、スマートフォン、音声認識デバイス、プロジェクションマッピングにはそれぞれ機能的な特徴があり、適用されている商品アイテム数にも差があります。
例えばデジタル表示器やスマートフォンは、商品アイテム数が500以下の物流倉庫現場で利用しやすく、タブレットPCは商品アイテム数が300以上で広く利用されていることがわかります。
ピッキングシステムの特徴を理解し、物流倉庫現場の商品アイテム数に最適なピッキングシステムを選択することで、ピッキング作業の効率化・生産性向上が可能になります。
ピッキングシステムによる物流倉庫改善事例
続いて、デジタル機器のうち「デジタル表示器」と「タブレットPC」を活用したピッキングシステムの具体的な事例をご紹介します。
・デジタル表示機を活用したピッキング作業のシステム化事例
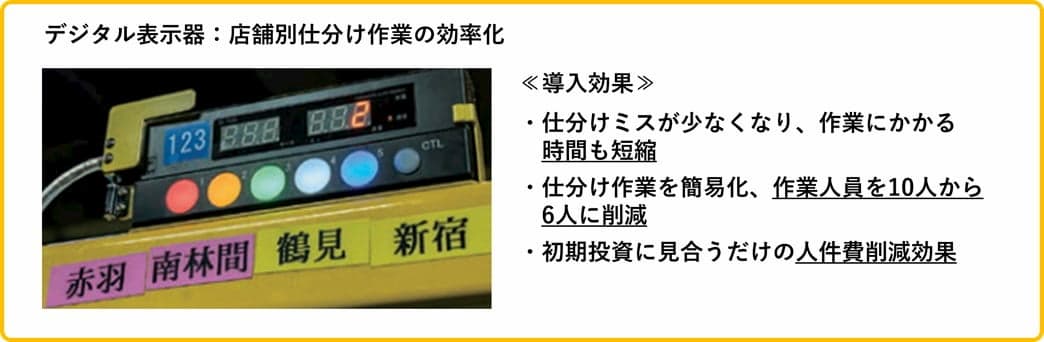
上記事例ではデジタル表示器を利用することで、店舗向けの仕分け作業を簡単にし、結果としてピッキング作業の効率化と人件費削減を可能にしました。
導入事例のインタビューによるとピッキング作業のシステム化による生産性向上の他に、「人材採用の募集をかける時に1つの武器になった」という効果もありました。
理由は仕分け作業が簡単になり、初心者でも簡単に作業ができるようになったからです。
・タブレットPCを活用したピッキング作業のシステム化事例
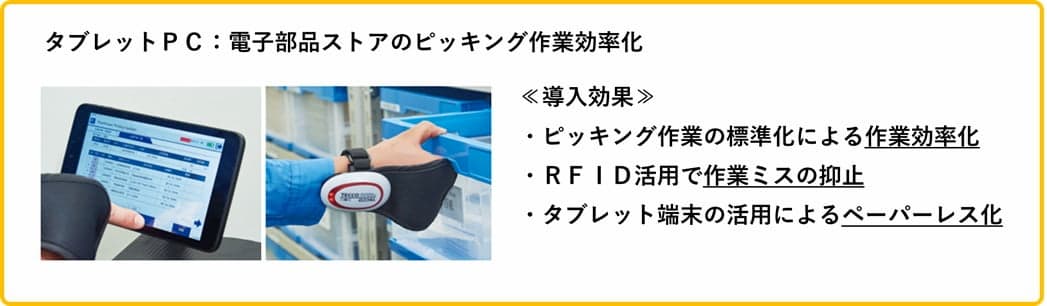
こちらの事例は弊社東京工場の導入事例です。こちらもピッキング作業のシステム化を行ったことで、いわゆる属人的な作業を標準化し、さらにRFIDを活用して誤取り出し/出荷ミスを減らすことに成功しています。
このようにピッキング作業のシステム化を適切に行うことができれば、物流倉庫現場の効率化・生産性向上が可能になります。
まずは物流倉庫の現状把握から
物流倉庫現場に適したデジタル機器の選択がするためには、物流倉庫現場の現状把握が重要です。
物流倉庫に利用できるピッキングシステムはさまざまあり、ピッキングシステムの導入動向からピッキング作業のシステム化しても導入効果が必ずしも得られるわけではないことがわかりました。
ピッキングシステムはデジタル機器とシステムで構成されており、デジタル機器に注目して特徴や商品アイテム数でどのような利用動向があるかについてご紹介しました。
現状把握をすることで「ピッキングシステムと作業規模があっていない」「必要な機能が不足している」「ピッキングシステムが複雑で利用が進まない」を回避できる可能性が高くなり、期待する導入効果が得られます。
ピッキング作業のシステム化を検討する場合は、まずは現状把握から始めてはいかがでしょうか。
業務改善を進めるためには現状を把握することが必要です。このサービスは「物流現場のIT化や自動化を検討したい」と考えている企業様向けに、物流・倉庫現場のデータを分析し、改善方針とその改善効果を、簡易的に報告するサービスです。