開発ストーリー
船舶分野で脱炭素社会の実現に挑む電気推進システムの開発
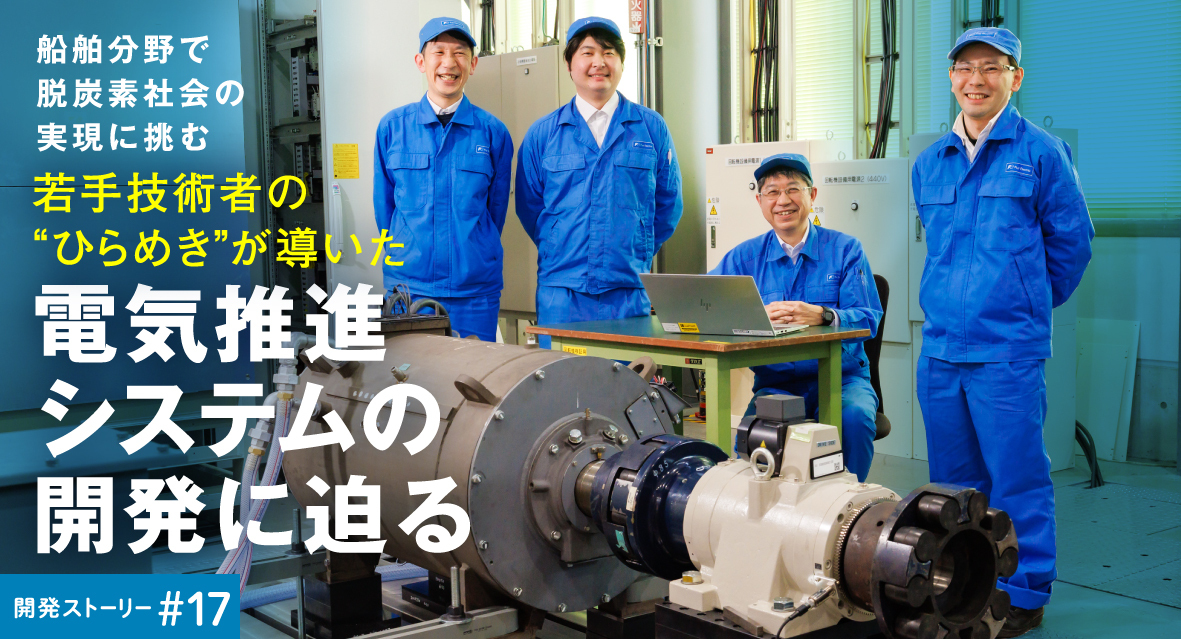
多くの船舶が、今もディーゼルエンジンの航行で多くのCO2を排出している。
富士電機はこれまで、排ガスから硫黄酸化物(SOx)を取り除く装置(スクラバ)を開発し、船から排出される大気汚染物質の削減に貢献してきた。
現在、富士電機の開発統括部(鈴鹿地区)の回転機開発部は、船舶においてもEVのように温室効果ガスを一切出さない、まったく新しい船舶用電気推進システムにチャレンジしている。課題を乗り越える開発の要となったのは若手技術者たちの「ひらめき」だった。
実例のない未知の世界への挑戦
まったく新しい船舶用の「電気推進システム」は、モータの他にインバータ、変圧器、バッテリーなど船舶全体の電気機器を1つにまとめたもので、2022年4月から開発が始まった。
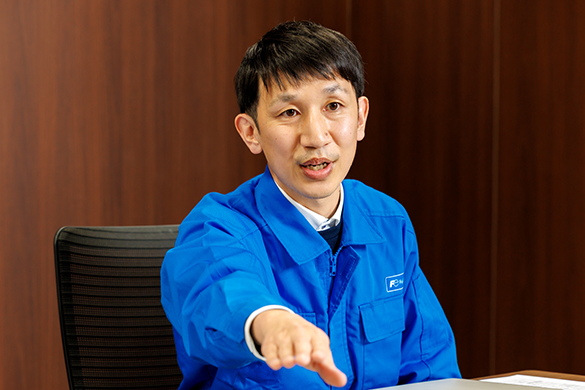
富士電機は戦前から船舶用モータを製造し、1965年に進水した南極観測船「ふじ」にも搭載されるなど、長い歴史と実績がある。
しかし、すぐにシステムの設計には進めなかった。電気推進システムの開発の取りまとめ役となった笹森は「産業用モータに携わってきた技術者たちはみんな右往左往していました」と開発当初を振り返る。
「これまではモータ単体の製造だったので、船の構造の一部だけ知っていればよかった。いざ『電気推進システム』を開発するとなったとき、船の全体像をまったく把握していないことに気づいたんです……」(笹森)
お客様の「生の声」を聞き、ユーザの真の思いに迫る
ベテラン技術者・伊藤もシステムの中でモータがどんな使われ方をするのかイメージが湧かないまま、開発をスタートさせた。
「お客様となる造船所側も、世の中に実例がない未知の世界で、お互いに手探りの状態でした。そこで、造船所・エンジン&プロペラメーカと交流会を開いて、技術者が直接お客様の“生の声”を聞くことにしたんです」(伊藤)

1年かけて丁寧に話を聞き、「電気推進システム」の仕様が固まった。集めた声から見えた優先順位が高いニーズは「小型化」と「パワー」だった。
さらに、研究者が研究室を飛び出し、お客様(船主)を直接訪ねて潜在的ニーズを突きつめる。会話を重ねる中で、船内における本電気推進システムの位置づけや、船員(ユーザ)がどのような運用(保守メンテナンス)をするか、を把握することができた。
そして、システム開発を決めた1年後の2023年5月、本格的な開発が始動した。
しかしここでも、システム開発はベテラン研究者たちを手こずらせた。小型化とパワーはトレードオフの関係にあるからだ。さらに、過熱するモータの冷却が課題になるのは目に見えていた。
この難局を突破したのは、2人の若手技術者たちの思い掛けないアイデアだった。
きっかけはテレビの子ども番組
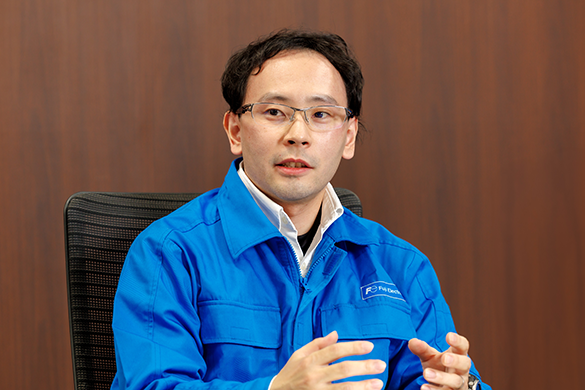
モータには正転と逆転がある。それぞれの動きの出力を均等に維持しようとすると、今までのモータを小型化できない。さて、どうするか。
2023年7月、入社9年目の太田は1歳半の子どもと一緒にテレビを見ていた。
子ども向け教育番組で「橋」を特集していた。橋の下を何隻もの船が左右に通り過ぎていく。早送りの映像をぼうっと眺めているうちに、太田はあることに気づいた。そしてひらめいた。
「船はほとんど前にしか進まない。それなら船のモータを前進に特化したらいい」
後退の出力を下げて前進の出力をアップさせることで、サイズを小さくしても前進のパワーを確保できる。意外に気づかない盲点だった。
船舶の左右に、それぞれ一方向に特化したモータを搭載して制御する試作品をつくり、2023年冬に実証実験をした。太田のアイデアで出力アップが立証され、本番用の製品開発にフェーズが進んだ。
「既存の概念にとらわれず少し見方を変えるだけで、意外と身近なところにヒントがあるんだと気づきました」(太田)
学生時代の経験を活かし水の流れを可視化!
同じころ、入社6年目の濱田はモータの冷却装置に頭を悩ませていた。
大きなパワーを出すとモータが高温になり、部品の破損や故障につながる。そのため、モータの周りに設けたフレームに水を流して発熱部を冷やす。しかし、冷却構造には大きなコストが掛かる。
チームにはコストを下げつつ冷却能力を高めるアイデアはあったが、解析で考案した手法を検証する手立てが無かった。金属フレーム内の水の流れが解析通りになるのか、自信が持てなかった。水の流れを可視化すべく、弁当箱サイズのミニモデルを自作し、検証を重ねた。
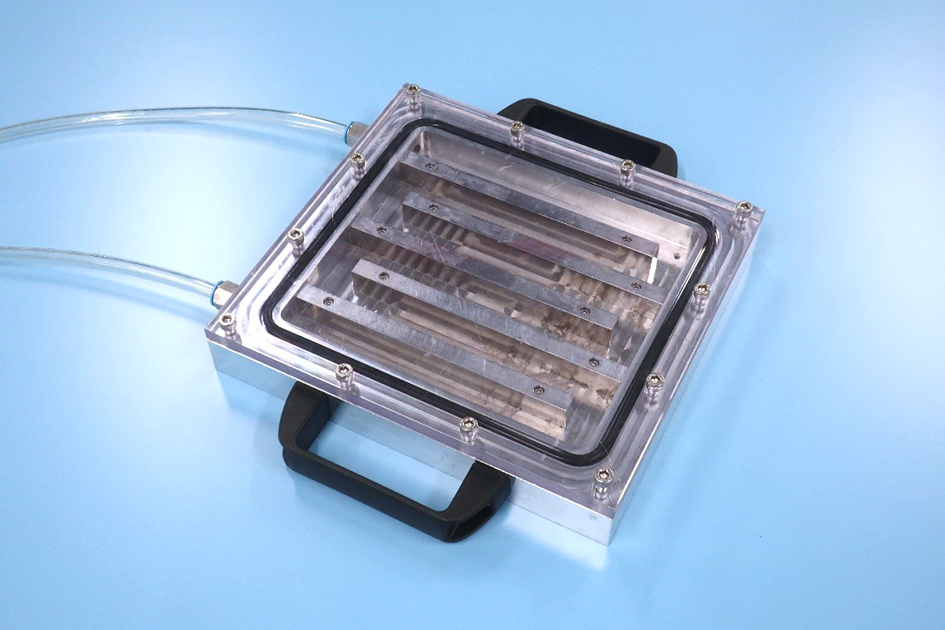
最初に食紅を流してみた。水路に沿って水が赤くなれば、正しく水が流れている証明になる。しかし、しばらく水を流すと、流路全てが赤くなり水がどの方向に流れているか分からない。
そこで学生時代に流体力学を学んでいた濱田はひらめいた。
「“流れの可視化”の研究で使っていた糸が使えるのでは?」
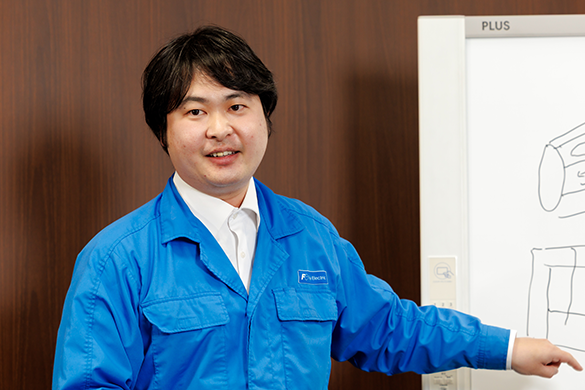
エアコンの送風口に紙を張り付けると、紙がなびく向きで風の方向がわかる。それと同じように、仕切りに糸を付けたら、糸の向きで水の流れを可視化できる。
「パソコンでのシミュレーションだけでなく、メーカーとしてお客様の目に見える形で立証することがとても大事です。私たちも、データに不安を抱えながら開発を進めることはできません。糸で水の流れを可視化できたことは大きな一歩でした」(濱田)
ここから一気に開発スピードが加速し、モータとほぼ同時期に冷却装置の試作品が完成した。
業界トップ性能を生む土壌
富士電機の電気推進システムは、他社に対し1.2倍の出力密度で、業界トップにいる。2024年4月の展示会では「富士電機のモータは小さいのにパワーがある」と評価も上々だった。
若手のアイデアを後押ししたことが、開発のブレイクスルーになった。伊藤は「どんな開発でも、成功するかどうかはやってみないとわからない」と語る。
「富士電機には、たとえ失敗しても周りの人がカバーしてくれる土壌があります。だから若い人たちは臆せず、どんどん挑戦してもらいたい」(伊藤)
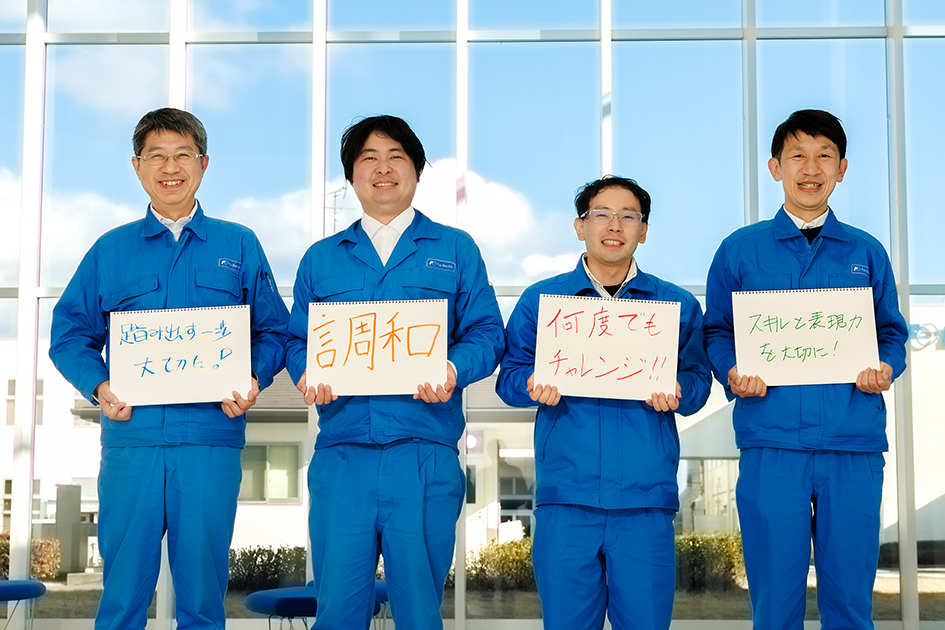
伊藤「1人では無理でも、チームだから大きいことができる。学生の皆さんには“踏み出す一歩を大切に”してと伝えたい。どんなことでもサポートします」
濱田「多くの方にサポートしていただき、ここまで来ました。部門の垣根を超えて協力し合える、 “調和”の大切さを感じました」
太田「一番大事なのは諦めないこと。失敗することはたくさんありますが、“何度でもチャレンジ!”する精神で新しいものを生み出していきたいです」
笹森「技術者は専門的なことしか話さないと思われがちですが、お客様からニーズを聞く力や、自分たちがつくった製品をアピールする“スキルと表現を大切に”しています」
「まずは2025年4月から営業が受注活動できる状態になるよう、上市を目指しています。業界トップの性能を実現できた強みもあるので、期待感があります」(笹森)
また、この技術は船舶以外にも応用できる可能性があるという。例えば、建設機械の重機などだ。すでにコアになる部分はできている。建設現場の過酷な環境でもパワーを出せる出力密度を達成できれば、「電気制御システム」の汎用も夢ではない。
未知なる製品を生み出したフロンティア集団は、若手とベテランが手を取り合って、チャレンジを続けている。