開発ストーリー
蒸気発生ヒートポンプで「ミッション:ポッシブル」 脱炭素化を加速せよ!
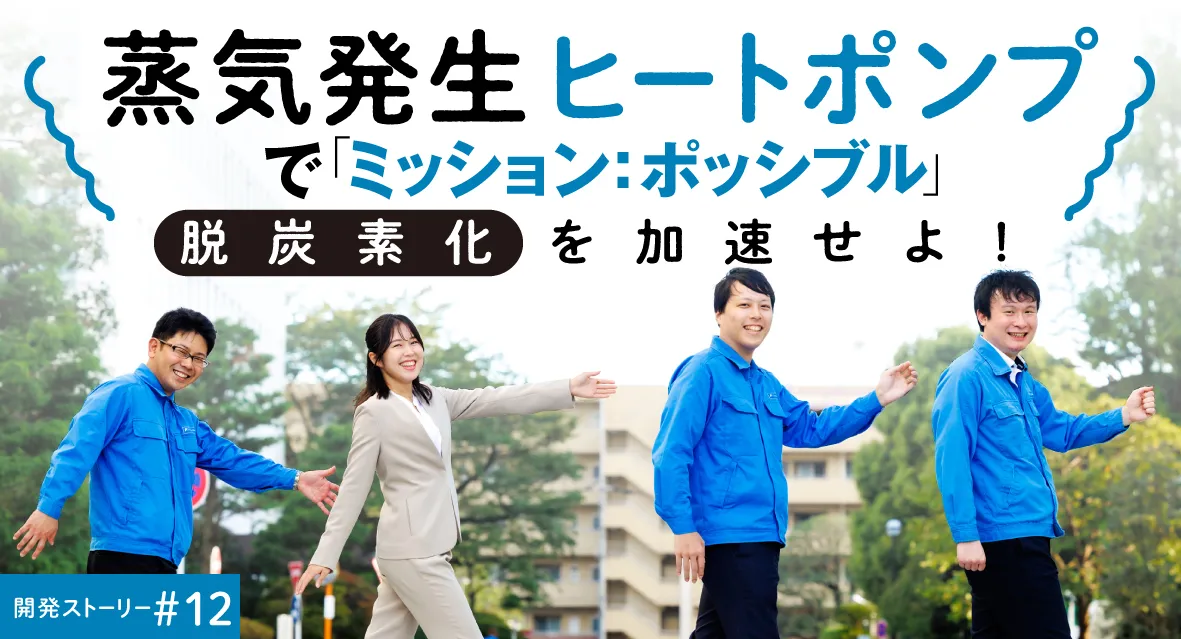
節電、再生可能エネルギーの利用など、企業はあの手この手で脱炭素化の実現を目指している。しかし、多くの担当者は「エネルギー消費を減らす手段に手を尽くしてきた」と思っているのではないか。
富士電機は、この課題を解決するため、「蒸気発生ヒートポンプ(以下、ヒートポンプ)」を製品化している。ヒートポンプの魅力と、進行中のプロジェクトについて4人の社員に話を聞いた。
CO2削減と燃料代削減を同時に実現
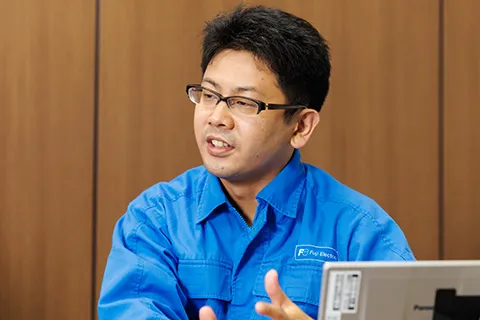
脱炭素化を目指す企業の多くはまず、工場や事務所の電気をつける時間を短くするなど、消費電力を削減する。次に、エネルギー源を変える。では、「蒸気発生ヒートポンプ」の役割とは?
開発の司令塔を担う中野は「ヒートポンプとは、一言で表すと、『エネルギーのリサイクルをする装置』です」と説明する。
工場など生産現場では、大量の排水が発生する。高温の排水は、条例などで40℃未満にして捨てる必要がある。この熱い排水の熱エネルギーを再利用するのが「蒸気発生ヒートポンプ」だ。
例えば清涼飲料水は容器に密封して加熱殺菌するが、殺菌用の蒸気の生成にはボイラーを使うことが多い。ここに化石燃料が使われる。
「ヒートポンプを使えば、ボイラーの焚き減らしを可能にし、CO2削減はもちろん、燃料代削減も実現します」(中野)
さらに、ヒートポンプは省エネにも貢献する。ボイラーは消防法でボイラー室に設置することが定められているが、ヒートポンプは燃料を燃やしていないため、加熱対象物の近くに置くことができる。これにより、蒸気を配管で運ぶ際に発生する熱損失を減らすことができる。
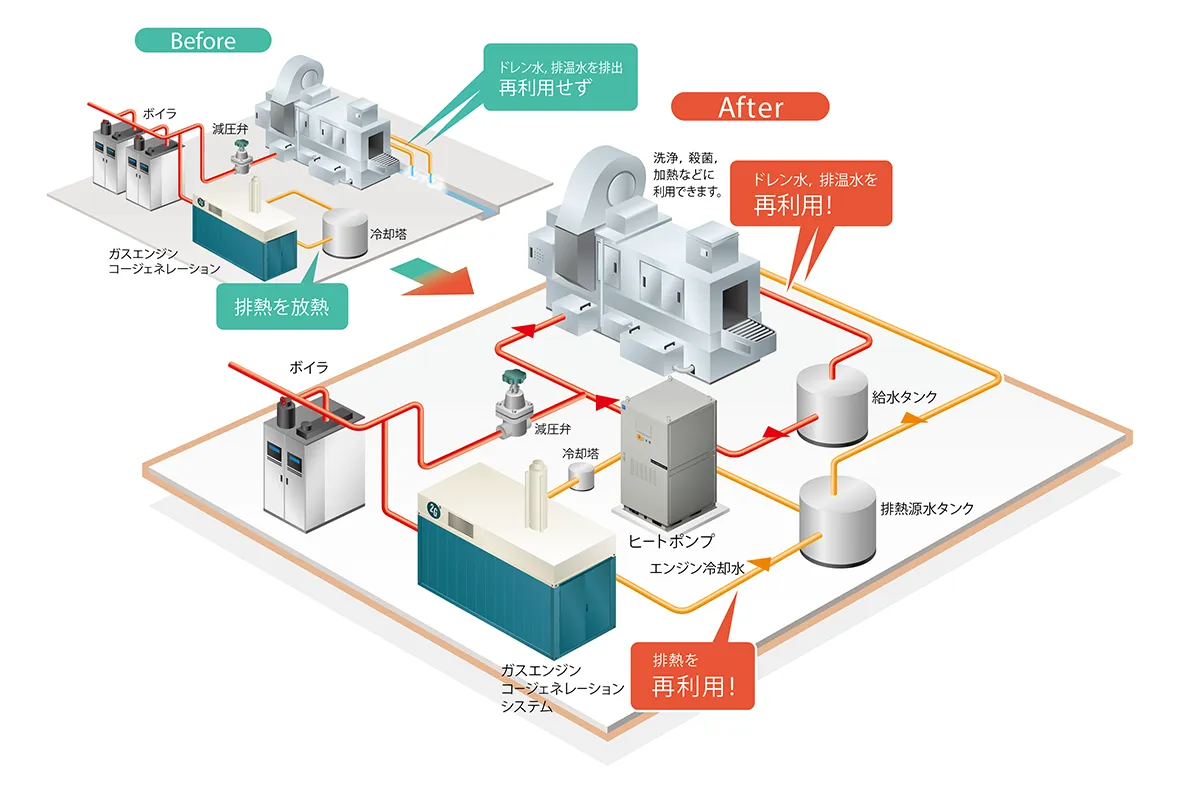
150℃になると適用範囲が拡大

富士電機は2016年から120℃の蒸気を発生させるヒートポンプを販売しているが、今、蒸気温度を150℃に引き上げる開発を進めている。
営業担当として中部支社で新事業を推進している片山は「150℃が実現したら、これまでの洗浄に加え、殺菌や脱脂処理も可能となります」と話す。
例えば、飲料殺菌の工程に適用した場合の試算では、CO2排出量とエネルギーコストを4割減らす効果があった。さらに、工場設備の洗浄や化学品の蒸留、静電気対策が必要なクリーンルームの加湿など、食品・飲料分野だけでなく、化学分野や半導体分野でもヒートポンプは役立つという。
しかも、150℃のヒートポンプは120℃のものと比べて対象物を温める速度が早い。また、蒸気の圧力も上がるので、120℃のヒートポンプでは配管内に蒸気を送り出す際に必要だった昇圧機器を省くことができ、設置などにかかる工事費用が少なくなるケースもある。
「ヒートポンプの存在を知らない方も多いので、120℃も興味を持っていただけますが、適用範囲がぐんと広がり、コストダウンの可能性がある150℃のヒートポンプは、発売を待ってくださっているお客様もいらっしゃるほど注目を浴びています」(片山)
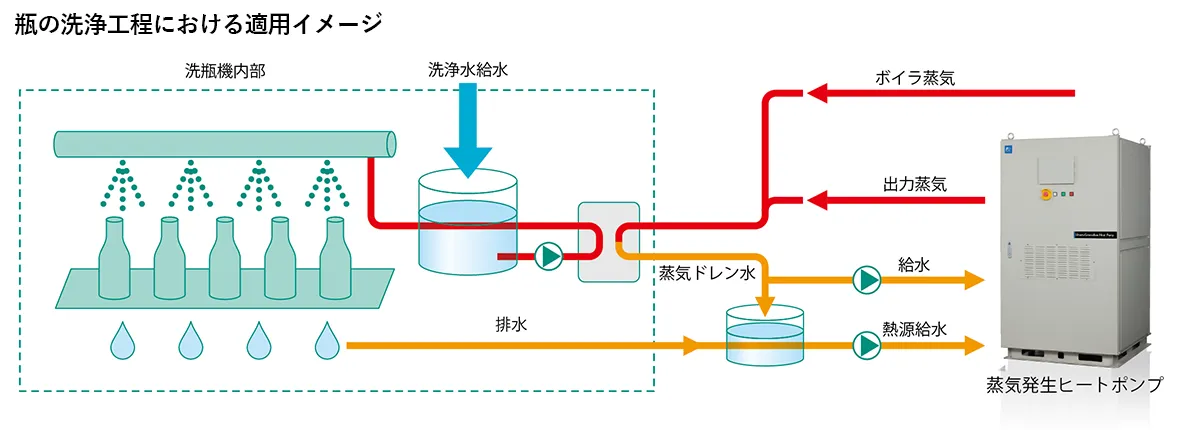
前例のない未開の地を進む開発
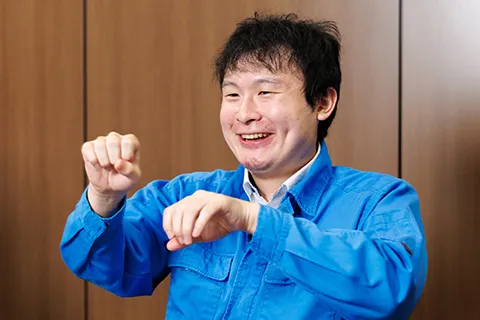
ヒートポンプの心臓部である圧縮機(コンプレッサ)の開発と回路設計を担う杉原は「研究自体は2015年にスタートしていましたが、道のりは順風満帆だったわけではありません。当時は、現在ほど脱炭素化に向けた機運が高まっていませんでしたし、なんと言っても圧縮機の開発など、いくつもの技術難易度が高いハードルを越えていく必要がありました」と言う。
土台となる技術は、富士電機が国内トップシェアを誇る自動販売機(以下、自販機)にある。
自販機では配管に通した冷媒の「圧縮・膨張」を上手にコントロールすることで飲み物を効率的に温めたり、冷やしたりしている。
圧縮機の制御を始めとした自販機で培った技術が今回のヒートポンプの開発にも生かされているのだが、自販機で温める飲料の温度は50℃~60℃で、工場で利用されるヒートポンプとは求められる熱の温度が大きくことなる。だから、内部の機器や部品はまったく異なる。真似できる前例となる製品もない。開発は未開の地を切り拓くように進む。
「まず、150℃という高温に耐えうる部品を探さなければいけないのですが、今はメーカーの皆さんと打合せを重ねて部品の選定を進めています」(杉原)
温度を上げる分、ヒートポンプ本体のサイズも大きくなる。
「工場には多くの設備が並び、設置できる場所には制約がありますから、マーケティング部門がリサーチした寸法に収めるよう設計を工夫しています」と杉原が話すと、中野が間髪入れずに続ける。
「よくこんなものを考えたなっていうくらい配管が“ぐるぐる”張り巡らされていて、杉原さんたち設計メンバーの苦労と工夫が伝わってきます」。
異例の開発体制「オール富士電機」
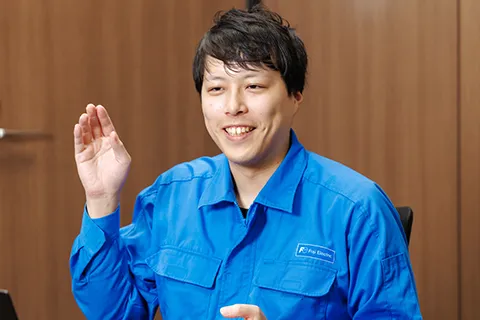
今回のヒートポンプ開発は、富士電機内では異例の開発体制になっている。
自販機を開発する三重工場から杉原が、営業からは中部支社の片山が参加する。神戸工場が筐体の設計を担い、そして、東京工場のメンバーがプロジェクトをとりまとめる。「オール富士電機」の体制で開発が進んでいるのだ。
ヒートポンプの構造と、情報制御盤の設計(機械や設備が意図した通りに動くように、制御盤の仕様や盤内の部品選定・配置をすること)は、東京工場の大関が担っている。
「今回はヒートポンプを単体で販売するだけでなく、お客様のニーズに合わせた『エネルギーマネージメントシステム』として、他の機器やシステムと合わせてトータルで提案することを目標としています」
同じ富士電機でも工場(拠点)が違えば、使う部品や調達ルートが異なる。しかし、今後量産を目指す場合は、従来の進め方ではうまく事が運ばない。
「従来の東京工場のものづくりについて、根本からアプローチを変えていく必要があると痛感しています」と大関は語る。
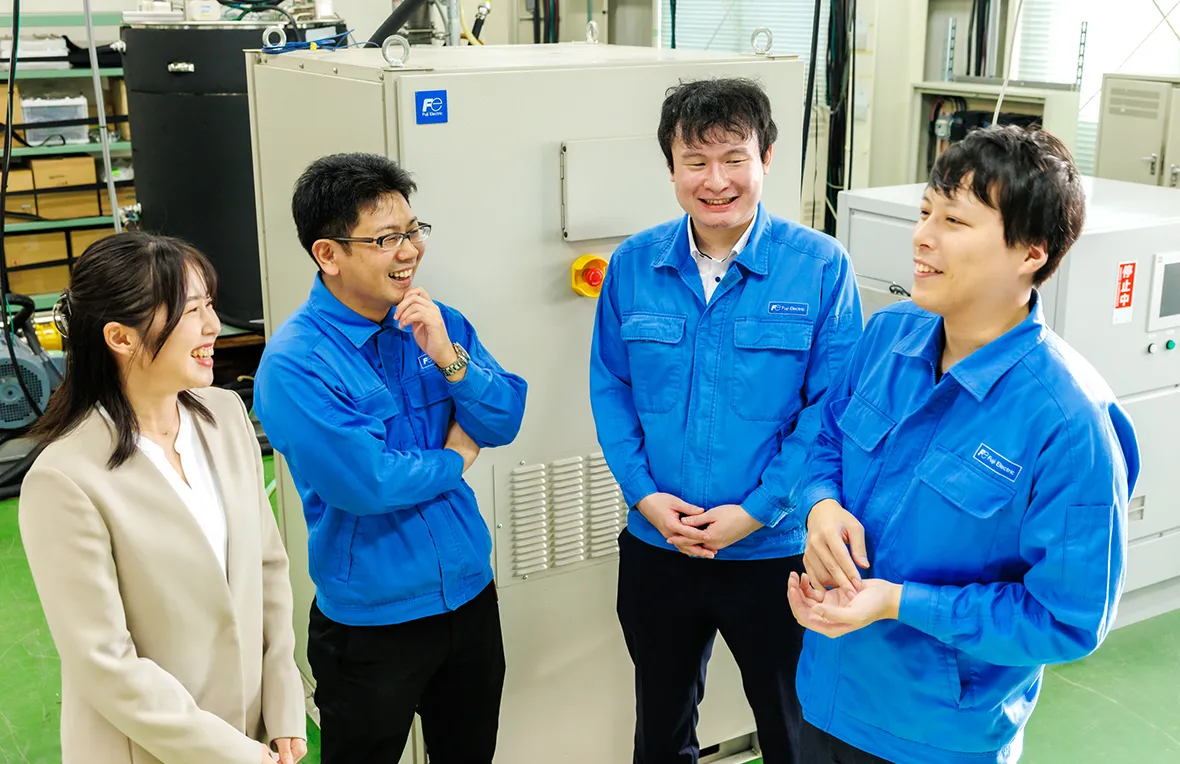
2026年の上市を目指す
現在、150℃ヒートポンプはようやく試作の第一段階を迎えたところだ。
材料の選定・調達、限られた条件下での設計、そして、システムのトータルプロデュースと、完成まで、あとひと山も、ふた山もありそうだが、メンバーは至って前向きだ。
「これまでヒートポンプの心臓部にあたる圧縮機はドイツの会社から調達していましたが、今回はパートナー企業の方と一緒に開発しています。圧縮機の自社開発は今回のプロジェクトの成否に大きな影響を及ぼしますし、これは、長年ヒートポンプに注力してきた富士電機にとっての悲願でもあります」(中野)
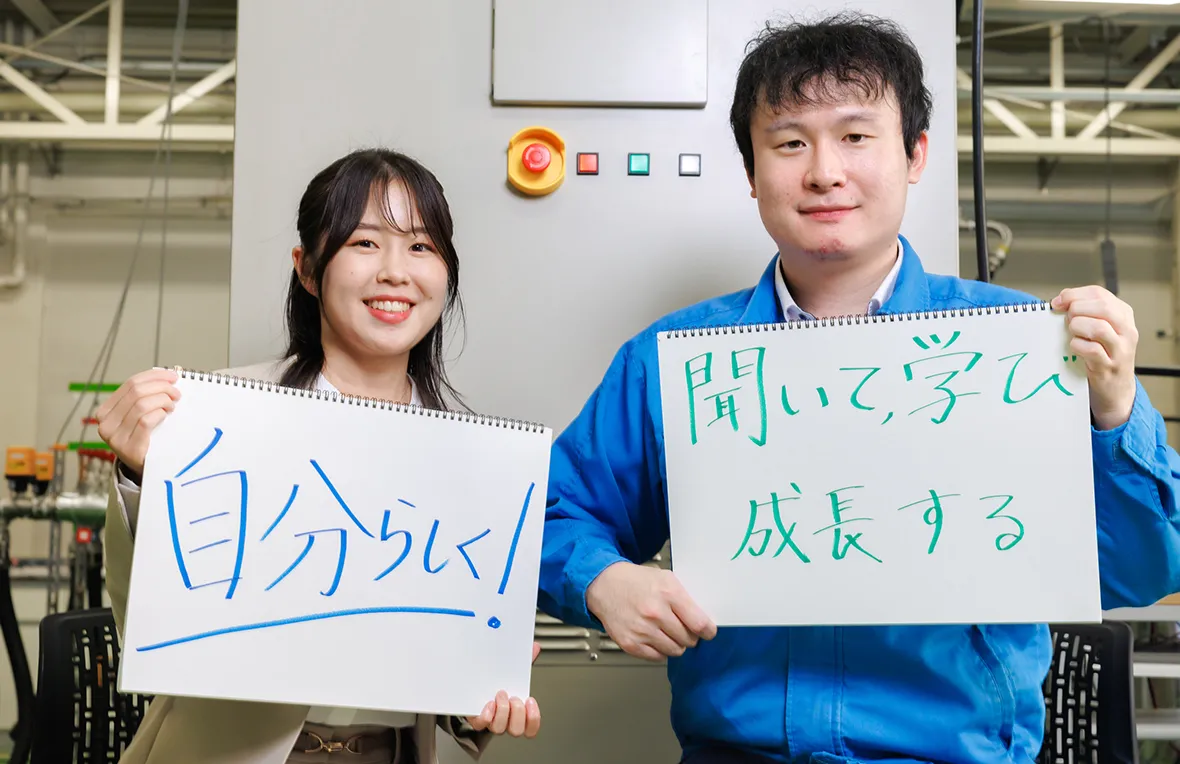
「『あなたから富士電機の商品を買いたい』と思ってもらえるよう、営業職として自分らしさを大切にしてほしい」(片山=左)。杉原(右)は「いつまでも聞いてばかりではダメ。そのたびに、自分自身が成長していく必要がある」と話した。
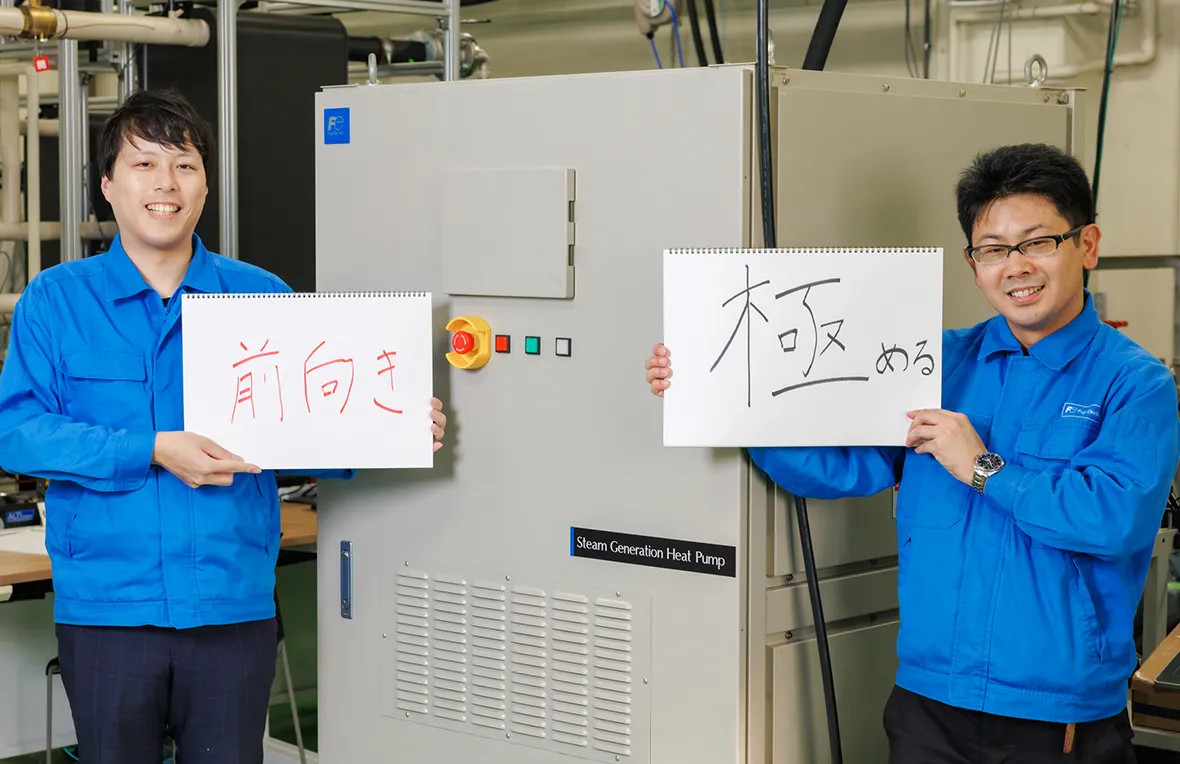
脱炭素社会の実現に向けて新たなアプローチをする「150℃蒸気発生ヒートポンプ」は2026年の上市に向け、開発は今後、佳境を迎える。「今は一つずつ目の前の課題をクリアしていくだけだ」。4人はそう言い合って、うなずいた。