富士電機が貢献する環境・社会課題
わずかな異常も見逃さない! 生産ラインの状況は離れた場所でも一目瞭然! 「次世代のクルマづくりの現場」を支えるデータ収集システムの実力とは
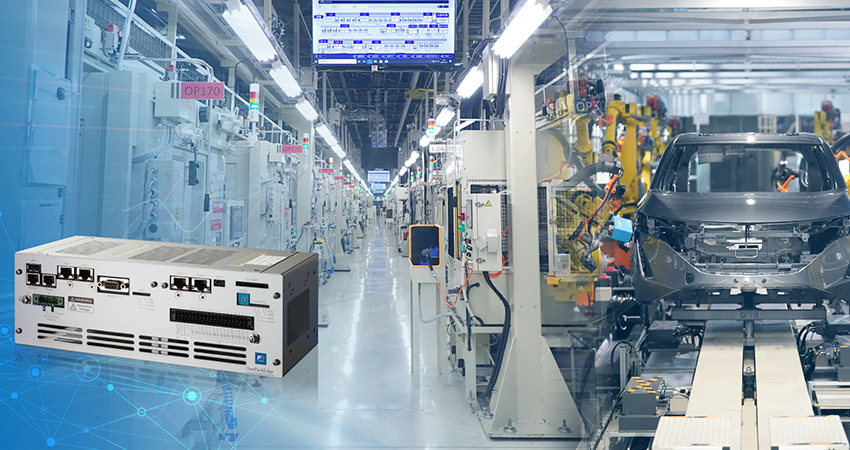
いまから100年以上前の1908年。「T型フォード」が誕生した。T型フォードが画期的だったのは、その生産方式だ。現在では当たり前に行われている「流れ作業」を開発した。これにより、自動車は一般人にも手が届くものとなった。
時は流れ、2021年。「次世代のクルマづくり」をコンセプトにした「ニッサン インテリジェント ファクトリー」が初公開された。舞台は、日産自動車栃木工場の生産ラインだ。
自動車製造の現場は、刻々と変化している。
富士電機の組立加工データ収集システム「OnePackEdge(ワンパックエッジ)」は、そんな歴史の一幕を陰で支えている。
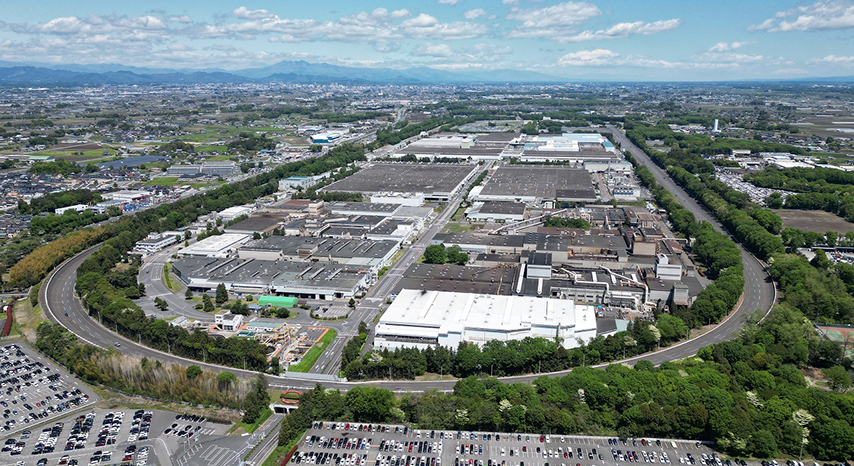
生産ラインを止めるな!止まってもすぐリスタート
「今後はますます『自動化』がキーワードになってきます。人が行っている作業をロボットに任せられたら、ミスも減りますし、より高品質な製品をつくることができます」
そう話すのは、日産自動車栃木工場のパワートレイン生産技術開発本部 パワートレイン生産技術部 量産技術グループの伊藤慎也さんだ。
自動車に限らず、製造業の現場では、部品を製造したり、それらを組み立てたりする人の「手腕」が、製造スピードや製品品質に影響を与えることがある。2021年に公開された「ニッサン インテリジェント ファクトリー」では、職人たちによって培われた技術をロボットに落とし込み、「最高品質」を安定的に量産することをめざしている。
「私が担当しているエンジン部品を例に挙げても、1時間につき、百台単位で製造しています。そうしてできた部品を、次のエンジンを組み立てる部門へ送っていきます。つまり、エンジン部品の生産スケジュールが遅れると、後の工程にも影響を及ぼすことになります」
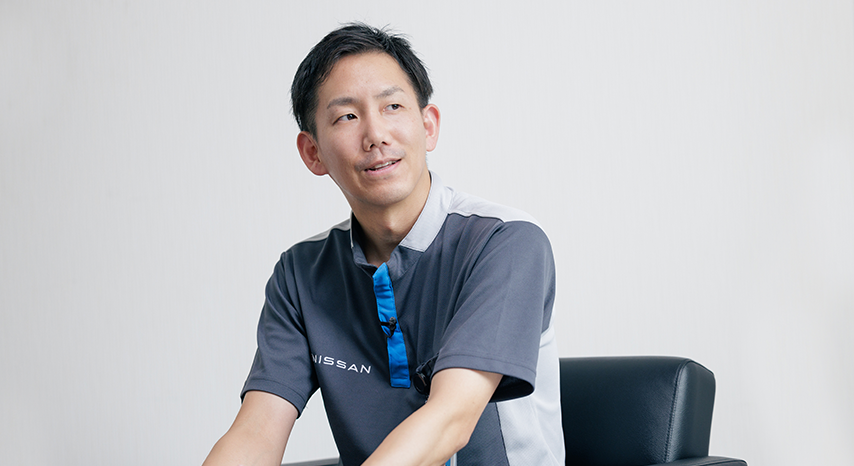
5分、10分の遅れが、後の工程に進むにつれて、大きく響いていく。
いかにして、生産ラインを止めないようにするか……。日産自動車をはじめ、製造に携わる企業は、常に気を配っている。
「けれども、どうしてもストップしてしまう場面はあります。そのようなときには、少しでも早く製造を再開させること。そして、何をすれば、次回はエラーが起きないのか、分析することが欠かせません。このとき、必要になってくるのが、日ごろからさまざまな工程を『見える化』しておくことと、データの蓄積です」(伊藤さん)
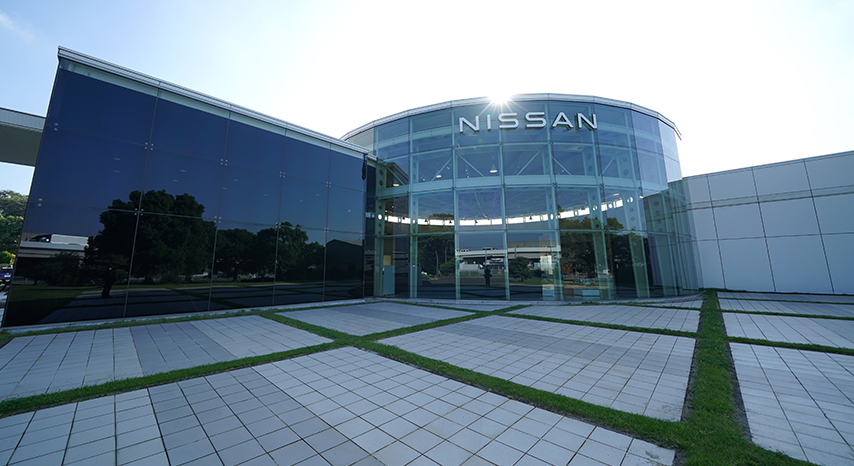
匠の技”を数値化し、蓄積し、「見える化」する
「新たに立ち上げるエンジン部品生産ラインにデータ収集システムを導入したい」——。
日産自動車から富士電機に相談があったのは、2016年だった。
日産自動車側から富士電機への要望を大別すると、
1.データを収集したいが生産設備の改造はなるべく少なくしたい
2.どの設備からも同じ形式でデータを収集したい
3.さまざまな用途に活用できる共通データベースをつくりたい
の3点だった。
そのような思いに応える形で導入されたのが、 組立加工データ収集システム「OnePackEdge」だった。
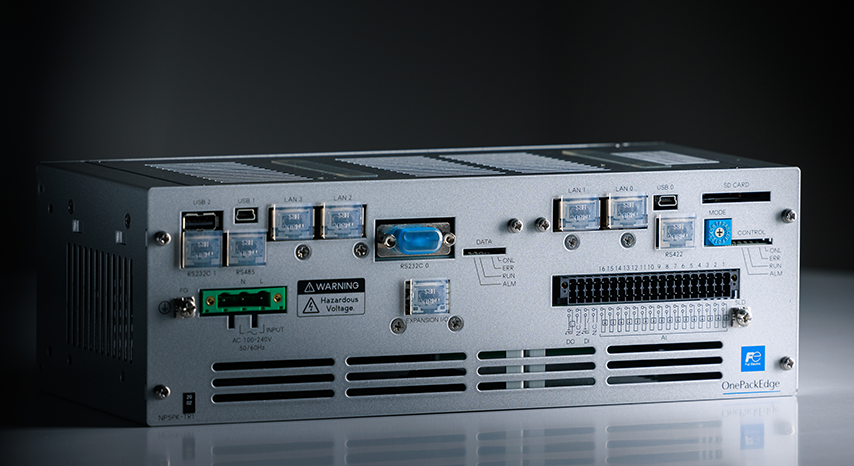
製品を提案する際、通常は外部のサプライヤーとして話をするケースが多い。だが今回は、2016年から2018年にかけて富士電機の社員が実際に生産現場に入り、導入効果の事前検証に協力した。
「生産設備それぞれの計測データを集約し、文字通り、ワンパッケージ化できるのが最大の特徴」と話すのは、インダストリー事業本部 情報ソリューション事業部 DX推進室 企画部 システム企画課の伊藤勇作だ。
「お客様が大きな設備改造をすることなく、設備が持っているデータを簡単に集められます。そうして収集した複数の生産設備のデータをひとまとめにして蓄積し、見える化してくれるのが、本製品の利点です」
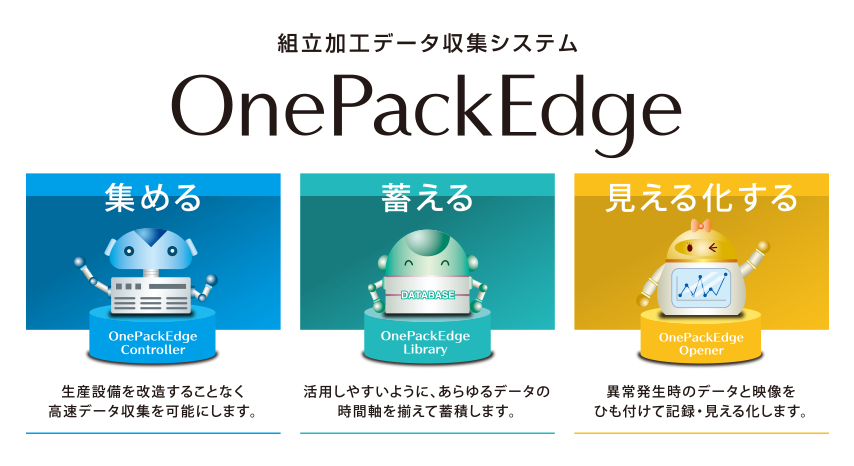
-
(注)
-
OnePackEdgeの特長や導入のメリットについて詳しくはこちら
日産自動車に限らず、多くの工場では、採用している設備メーカーが複数に及ぶ。そのような場合も、「OnePackEdge」を活用することで、各メーカーの設備のデータ出力方法を統一することができる。
富士電機パワエレ営業本部 ファクトリーオートメーション統括部FAシステム営業部 営業第一課の神原弘樹はこう話す。
「今回導入した工場も、1ラインに20メーカー以上の設備が入っていました。その中で、日産自動車様が求めているデータを収集・出力するために、設備メーカーの方々と何度も交渉をしました。今回は、富士電機にとっても初めての大規模案件でしたから、設備メーカー様各社の意見を調整するのには困難が伴いましたが、弊社のシステム側を工夫して設備改造を最小限に抑えることで乗り越えることができました」
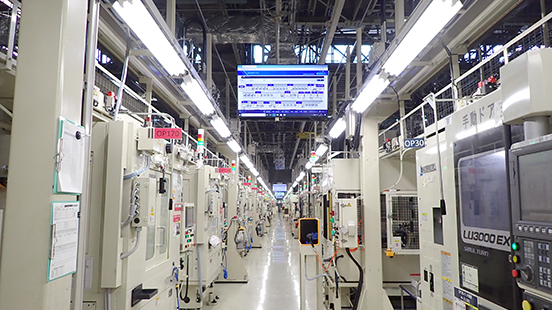
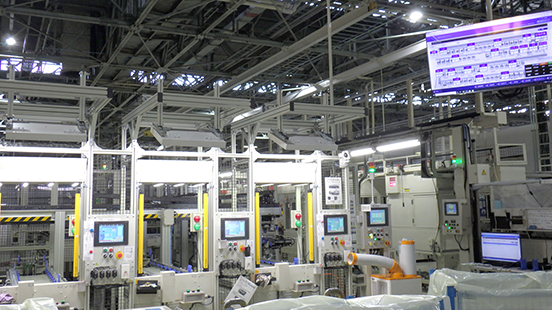
エンジン部品加工ライン(日産自動車提供)
決め手は「スピーディーな対応と価格競争力」
2016年からスタートしたプロジェクトは、2020年に栃木工場の1ライン目、2021年に2ライン目が稼働を始めた。
2ラインのうち、一つ目のラインには「OnePackEdge」が87台、二つ目には83台設置されている。栃木工場での稼働を開始した後は、福島県のいわき工場や、関連会社の日産工機でも活用がスタートした。
日産自動車の伊藤さんは「OnePackEdge」を導入した効果について、こう話す。
「トラブルが起きた際、従来は事務所から現場まで駆けつけ、状況を確認し、再び事務所に戻って対策を立てる、という対応をしてきました。けれども、『OnePackEdge』を導入してからは、パソコンを立ち上げるだけで、どの設備で、何が起きているのかが一目でわかります。また、これまでは手書きで作成していた稼働状況日報などのアナログの情報を、デジタルデータとして集めることが可能になったことで、不具合発生から解決までのスピードが格段に上がりました。本当に、役立っています」
生産ラインが動き始めて以降も、現場の要望を受け、システムのアップデートは続いている。
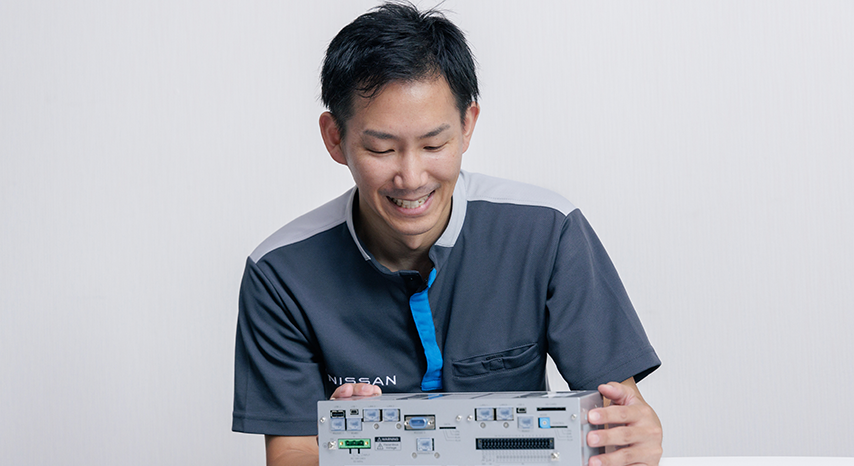
「エンジン部品ごとに付与されたシリアルナンバーのデータを、生産設備ごとに設置された『OnePackEdge』が収集する仕組みになっているので、ナンバーを追えば、対象のエンジン部品がどういう条件で、どの設備を通ったのかがわかりますし、一定の期間を選んでデータをダウンロードすることもできます。日産自動車では『最高品質』をめざして、集めたデータをさらにどう活用していくか、検討中です」
と話す日産自動車の伊藤さんは、こう続けた。
「例えば、ドリルで穴を開ける際に起きる振動が基準値を超えていたら、目に見えなくても、その製品に『不良』が起きている可能性があります。そういった数値をデータとして可視化することで、不良品が後の工程に流れていったり、故障によって生産ラインが停止したりするのを、未然に防ぐことができるはずです」
伊藤さんによると、他のラインに従事する人たちから「こんな取り組みをしているのか、便利そうだね」と声を掛けられるなど、栃木工場の中でも、「OnePackEdge」を導入した新ラインは注目されているという。
最後に、伊藤さんに、「OnePackEdge」導入の決め手を尋ねると、「スピーディーな対応と価格競争力」と答えてくれた。
「『このデータがほしい』といった、こちらの要望にも迅速に対応いただきました。同時に『こうされてはいかがですか』など、新しい提案もくださり、大助かりでした。また、導入にかかるコストも、他社と比較して抑えられていました」
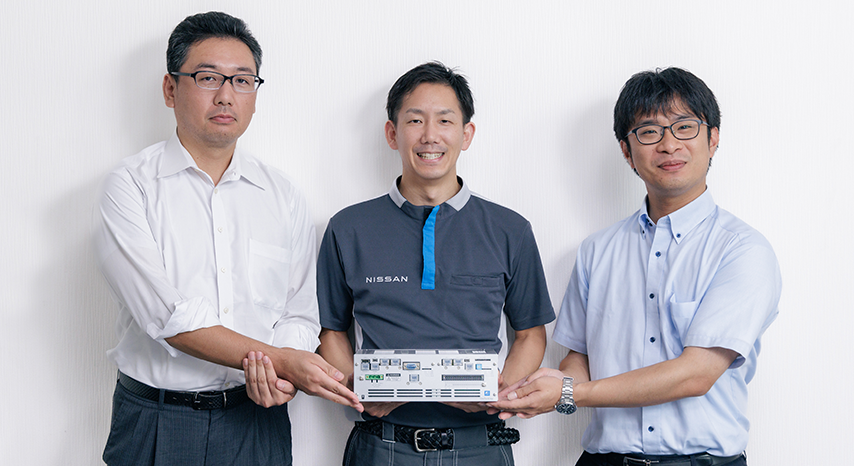
「『OnePackEdge』の導入をご検討されているお客様は、まずはお気軽に当社の営業窓口までご相談いただきたいです。お客様が抱えておられる生産現場の課題を解決に導くソリューションをご提案いたします」(神原)
富士電機の技術が、自動車製造の歴史に、新たなページをめくろうとしている。
貢献するSDGs目標
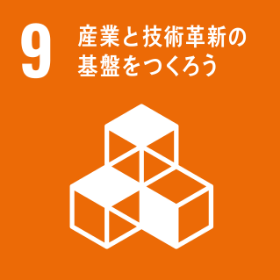
OnePackEdge は、ものづくりの革新を推進する独自のIoTソリューションです。
生産現場が抱える「人材不足による現場力低下を防ぐ」、「マスカスタマイゼーションに対応する」、「品質を向上させる」、「ロスコスト・ロスタイムを削減する」などの課題解決に貢献します。これは、当社のSDGs目標「9.産業と技術革新の基盤を作ろう」に貢献しています。