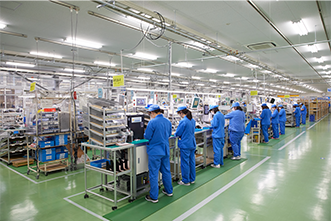
マクロとミクロ、
二つの視点で独自の
「ダブルKAIZEN」を実現。
日本企業のお家芸「改善・KAIZEN」は、いまやKARAOKEやOTAKUと並ぶ国際語。富士電機機器制御では多くの工場で生産ラインのあちこちに隠れている無駄を従業員全員で見つけ出し、解決法を考え、改善しています。当社のグループ会社である株式会社秩父富士の場合は、より強力な「ダブルKAIZEN」を実現。製造ライン全体から見直すマクロKAIZEN、そして現場から創意工夫を出し合うミクロKAIZEN。相乗効果で大きな実績を上げています。その秘密を田口元社長(取材は2018年2月に行いました)に聞いてみました。
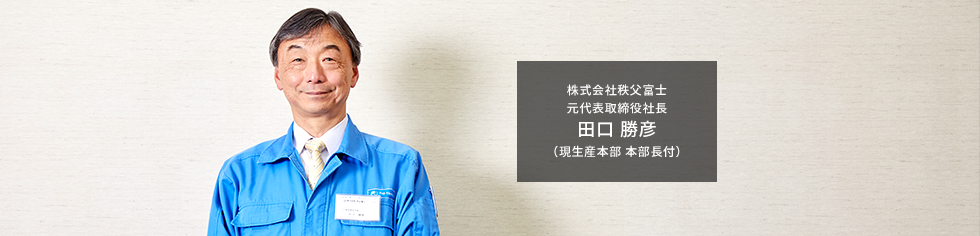
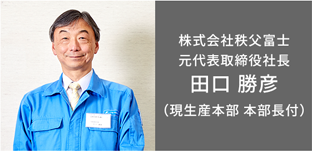
全体的な問題点を発見し、解決する。
それがマクロKAIZEN。
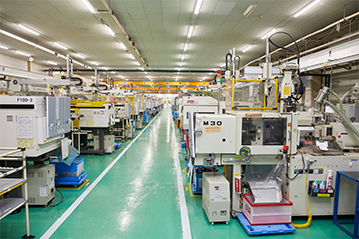
─── 製造ライン全体の改善は、どのようなポイントで行われたのでしょうか?
田口:大きく2つの方向性で進めました。1つは製造ラインのレイアウト変更です。今まで複雑だった製造の流れをシンプルに短く、一直線にして作業をスムーズにしました。直線だと動きやすく、全体が見えやすく、どこかで問題が起きてもすぐ発見できます。もう1つは統合化。例えばマグネットスイッチの組立てをしている事業所があって、別の事業所で製作していた部品の加工工程を移すことで、1拠点での一貫生産体制を完成させました。
新たな生産体制を実現したことで、材料の受け入れから部品加工、組立て、出荷までオーダーに応じて素早く無駄なく作ることができるようになりました。いま富士電機機器制御グループは国内外に5つの製造拠点を保有しているのですが、それぞれの拠点もこの一貫生産体制を構築しています。
一人一人が現場の問題点を発見し、解決する。
それがミクロKAIZEN。
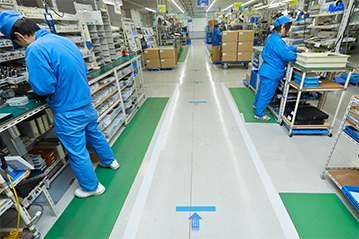
半分ほどに短縮されている。
─── もうひとつの柱である現場の改善については、どんな方法で進められたのでしょうか?
田口:こちらは従業員の自発的な改善となります。作業者本人でなければ気づかないことってありますよね。毎日の作業の中で「ここちょっとやりにくいよね」とか「これ無駄じゃない?」という問題点を発見し、どうすれば解決できるか、そのアイデアを現場のスタッフも協力して提案しています。提案数は毎月1,OOO件以上。個々の従業員の改善への創意工夫と熱意をダイレクトに感じています。採用案には賞金も出しています。
─── 具体的にはどんな提案が採用されたのでしょうか?
田口:製造ラインの細かな改善が多数あります。たとえば、3mのラインを2mに短縮する。3人の作業を2人でできるように削減。一工程を誰でも10分で完了。作業はその場を動かず行えるように。などさまざまです。次に現場作業の自動化。一度セットすればその場で単純な作業を自動的に行うような工夫ですね。最後に整理整頓の徹底。決まった物を決まった量だけ決まった位置に置く。さらに、そのレベルをお互いが評価し合うことで取組みのモチベーションを高めています。
田口:またさらに、マクロKAIZENやミクロKAIZENのベースとして、当社が金型や自働化設備を自前で設計・製作できることも大きいと思います。この技術が秩父富士の強みであり、これらKAIZENの源泉になっています。
スタートして約3年。
エンジンがかかってきたと実感。
─── これらのKAIZENは、いつ始められたのでしょうか?
田口:以前から各現場の個別改善は行っていました。毎月講師を招いて勉強会を開き、一緒に現場を見ながら学ぶというスタイルです。それは、まだ工場全体ではなく製造ラインに限られていまして、成果がいまひとつ上がらなかった。大きく変えたのは私が就任した2015年の後半からです。まず全体を8つのグル―プに分け、それぞれの持ち場で問題点と解決策を明らかにしました。改善後は定期的に報告会を開催し、課題や解決策のチェックを行い、視点がマンネリ化しないよう気をつけています。
─── 現場の従業員とはどのようにコミュニケーションをとっておられますか?
田口:報告を受けるだけでなく、私は定期的に現場を巡回し、じかに話し合うこともあります。一番訴えてきたのは、いつまでに誰がどこまでやるかを明確にすることでした。こういう改善活動は、ともすればあいまいになりがちなんですよね。またコミュニケーションという意味では他の工場との交流も始めました。レベルの高い工場を見ると「ああ、こんなやり方があるのか」と従業員に気づきがたくさん出てくるので富士電機機器制御グループ内外の工場の見学も積極的に行っています。
これだけ変わったビフォー⇒アフター。
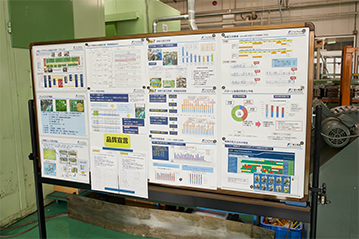
スキル評価表などが貼り出されている。
─── そのような改善への取組みによって、現場はどのように変わりましたか。
田口:改善の成果が目に見える形で出てくると、現場の意欲に火がつきました。そうなるともう現場が自分たちで考えて改善し、結果を評価してさらにまた改善するというプラスのループになったんです。小ロットずつまとめるパターン生産や、かんばん(部品名や必要数等の情報が記入されたリスト)の活用でその日必要な分だけ作る、などの改善によって部品欠品や仕掛在庫を減らすことができました。
田口:さらに金型を使う部品加工ではいわゆる「段取り替え」の短縮化ですね。つくるものを変えるとき、金型も替えるわけですが、次に使う金型をすぐそばに置いて、これまで20分かかっていた作業を数分に短縮しています。ほかにもアイデアを持ち寄る実演会を開いたり、一人一人の金型交換作業分析を行って改善を進めています。
─── 改善によって製品を買うお客さまには、どんなメリットがありますか?
田口:品質と納期の向上ですね。まず材料や仕掛在庫が減らせます。纏め生産ではなく一個ずつ組立てるから、ロスや間違いが起こりにくい。結果的に生産性が上がり、不良品も減るので、最終的には高品質の製品をスピーディにお届けできるというわけです。
従業員の意識も大きくKAIZEN。
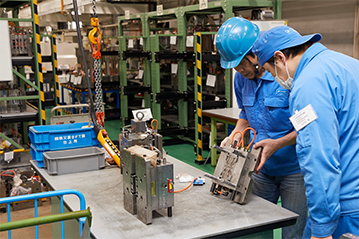
───ものづくり現場の改善を通じて、社員一人一人の取組み方も変わりましたか?
田口:当社の場合、秩父地域の特徴なのでしょうか。誠実で忍耐強く伝統的に進取の気風というかチャレンジ精神があったせいか、この1~2年で急速に進みました。部長クラスには、「5年後会社をどうしたいか」など自発性を高める意識改革を進めています。この先はIoTやAIの時代ですが、これも単純に頼るのではなく、人の感性や創造力を生かして頑張ることが大切だと思います。そして、製造現場の進化・発展のためには継続的な改善への取組みと毎日の試行錯誤が何よりも大切だと考えています。