「IoT(Internet of Things)」が注目されています。
あらゆるものをインターネットにつなぐことで、さまざまなことが可能になる…という話ですが、
具体的に製造業では何ができるのでしょう。
特に中小規模の製造業においては、どんな課題の解決につながるのでしょうか?
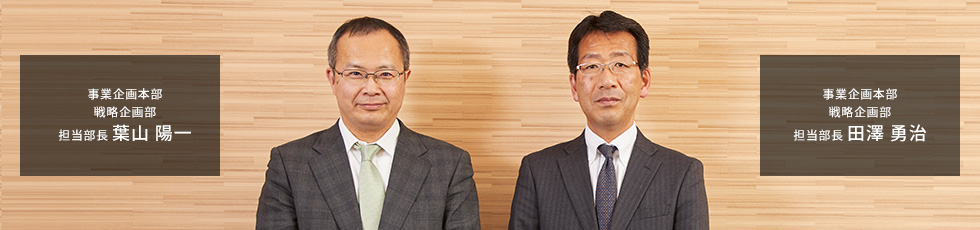
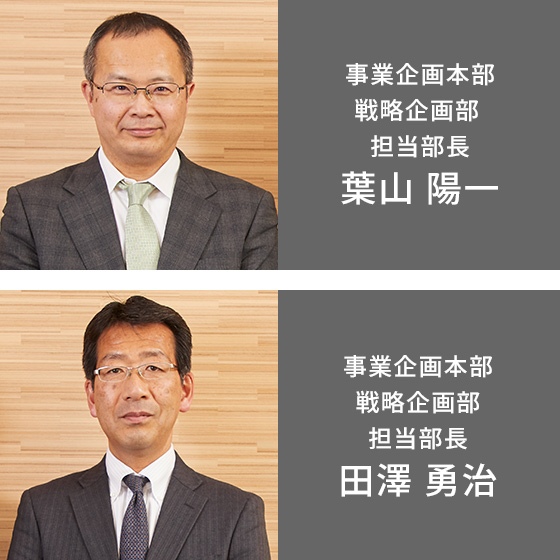
注目されるIoT。
それで何が変わるのか?
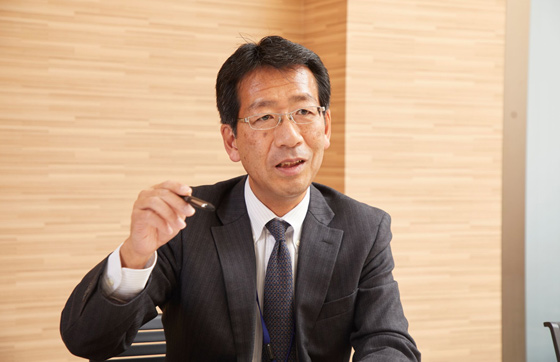
─ 製造業では「IoT(Internet of Things。以下IoT)」が高い注目を浴びていますね。
葉山:アメリカのIICやドイツのインダストリ4.0、日本でもロボット革命イニシアティブ協議会と、さまざまな団体で、その可能性についての議論や国際標準化に向けた活動が展開されています。世の中全体がIoTの実現に向かっていますから、競争力の確保のためには、大企業とともに中小企業での対応は喫緊の課題となりつつあります。
田澤:そういう意味で、上司から「キミ、我が社のIoT担当ね」と言われて、戸惑いながらあれこれ調べている方も多いのではないでしょうか。日本の製造業は、もともと自動化や色々なカイゼンの取組みが進んでいるので、その意味でもメリットをイメージしにくい面はあると思います。
─ 製造業でIoTを導入する場合、主に何を目指していくことになりますか?
葉山:製造業にとって大きな目標は「設備のゼロダウンタイム(以下ZDT)」だと考えています。機械設備の故障等による工場の停止時間(ダウンタイム)をゼロにするということですね。業種にもよりますが、ダウンタイム1日の損失は数億円にも上るとも言われており、出来るだけ短時間にとどめたいと考えているお客様が多いのです。
田澤:そこで我々の出番になります。一般的に製造業でのIoTとは、様々なデータを収集するために各種センサを現場に設置して、そこからデータを取得し、それを解析することでカイゼンなどにつなげていく行為です。我々のコンポーネント製品は、電気システムに必須な制御・保護機器として、すでに現場に設置されており、電気設備や各種装置に対する電気エネルギーや稼働監視のセンサとしても機能することができるのです。
コンポーネントをセンサとして利用してIoTをスモールスタート
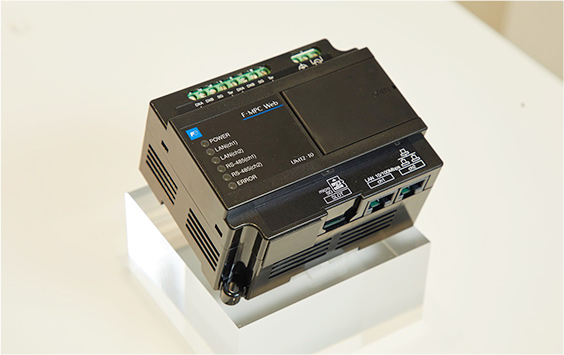
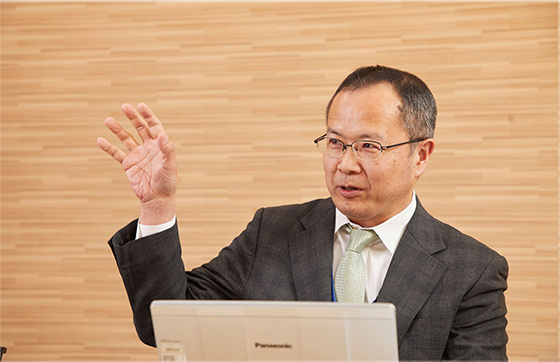
─ センサと言うと、振動や速度、温度を検知するようなものを思い浮かべますが。
葉山:ブレーカや電磁開閉器等のコンポーネントは、電気の流れを感知して電気を流したり、止めているわけですから、役割としてはセンサでもあるんです。ただ今は直接ネットワークにはつながっていませんので、そこをつなげる作業は必要です。
田澤:こうしたコンポーネントのセンシング機能を利用した電力監視、エネルギー監視のシステム製品群を、F-MPCシリーズとして、我々はIoT以前から持っていました。これらの製品群をIoTの入り口にしませんか?というのが私たちの提案です。お客様の配電盤や制御盤に既に設置されているブレーカや電磁開閉器のI/Oと組合わせることにより、比較的簡単に導入できるのです。
葉山:またF-MPCシリーズは、PLC(プログラマブルコントローラ)や専用のプログラムをご用意いただかなくても、電力監視や省エネ制御の仕組みが、パッケージとして組み込まれていますので、F-MPCを設置すれば、汎用パソコンと汎用ブラウザで、すぐに開始できます。私たち富士電機グループで提案しているIoTのスモールスタート、クイックスタートの一例になります。
─ エネルギー監視だけだとIoTと言うにはできることが少ないようにも感じます。
田澤:はい、ですからこの仕組みをベースにさらにIoTらしく発展させて、従来のエネルギー監視だけでなく、設備・装置の状態監視や、寿命診断による予防保全、つまり設備・装置の運転管理にまで広げよう、というのが我々のいまの提案です。
葉山:電力監視というのはエネルギーを計って、使用量を見て、一定の値を超えそうになったらアラームを出したり、装置の制御をしたりするというのが基本的な仕組みですが、設備管理も技術的な理屈としては同じなんですね。お客様が実際管理している機械装置や製造設備の運転回数、運転時間、運転電流というものを見てあげれば、それは予防保全につながるんです。
田澤:多くのお客様では、設備の診断は決められた周期で実施する定期点検や、部品が壊れたら交換する事後保全によるものが多いと思います。こうして設備の稼働状況や運転時間、運転回数などをきちんとデータとして製造ライン全体で集めることができれば、故障予知まではいかなくても、予防保全としてはかなりの前進になります。
まずは設備の運転管理から。いずれはものづくりの本丸へ
─ 電気の流れを計るだけでも、いろいろなデータが取れるのですね。
田澤:人間の体における「血圧」に似ているかもしれません。装置の稼働回数や時間はわりとダイレクトに取れますし、装置や機器のスペックに対して、これだけの運転回数がある、稼働時間がこれだけあるんだから、健康状態はどれくらいだろうと推測もできます。また電流の状態も、通常よりも高くなっているようなら、不具合の可能性がありますよね。そういった意味では、製造設備の中身を詳細に診断しなくても設備または機器に流れる電気のデータを介して不健康な状態に至る前の不具合や故障の予兆を見ることができるんです。
葉山:電気のデータをとると言う意味では、我々にはブレーカや電磁開閉器などの長い歴史で培った過電流などの電気に対するセンシング技術がありますから、精度の高いデータを取ることができます。ただ、まだIoTに対応する製品化は始まったばかりですので、現在のところはお客様が欲しいと思われるデータの全てを取れている訳ではありません。
IoTの可能性に早く触れて欲しい
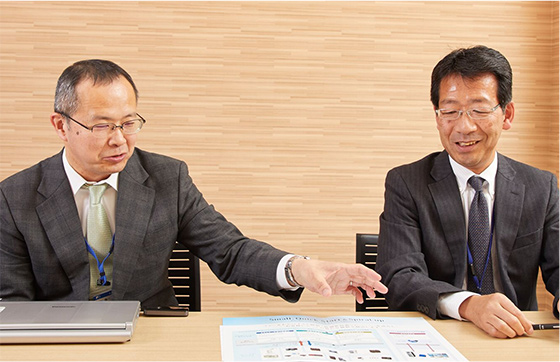
─ IoTにはどんな可能性があると考えますか?
葉山:ものづくりにおけるIoTの可能性ということでいうと、ものづくりには「QCDS」と言われる指標があります。QはQuality。CはCost、DがDelivery、SはSafety/Securityです。IoTはこれらのすべてに対して貢献できる。たとえばQの品質。製造工程に関する膨大なデータの中から、製品不具合に関与するデータを取得して不具合原因の見える化や解析を行うとか。いずれはAIを使って、その対策を自律的に実行するというところぐらいはいくでしょう。
田澤:いまはまだ各社、IoTで何ができるか、どこにお客様の需要があるかを一生懸命探っているところです。お客様の中には、当社の製品やサービスでIoTを始めると、そこで囲い込まれてしまって他社の製品は使えなくなるのではないか、という不安を持つ方もいるかもしれません。しかしIoTはオープンシステムを前提にしており、弊社もIoTのオープンプラットフォームであるi-BELTなどのコンソーシアム活動に積極的に参画していて、そんな心配を少しでも払拭できるように努めています。
葉山:さらに、電子デバイスや情報通信に関する急速な技術発展を背景とする第4次産業革命の動向を踏まえ、IoTの普及を前提にした新しい国際標準化活動が進行中です。数年後には国際標準規格も定まる見込みで、分かりやすく言うとVHSとベータのように、選んだ規格やメーカーによって使用上の融通がきかず、投資が無駄になると言うリスクはかなり低くなっていくと思います。
田澤:IoTというのは、お客様の日々の業務の中に課題解決の糸口を見つけるツールです。今まではファクトとして取得できないデータだったり、取得しても扱えない膨大な量のデータだったりしたものが、様々な技術革新や通信インフラの整備でそれが扱えるようになってきたことで、新しい扉が開いたのです。早くその扉を開いて、宝の山を取り出す準備をして欲しいと思います。
こんなお客さまにおすすめ
- これからIoTに取組もうとされているお客様
- 中~小規模工場(監視点数1,000点規模)
のお客様 - 生産設備のゼロダウンタイムを
目指しているお客様 - 大規模工場の一部でIoTの導入を
検討しているお客様
⇒中小システムから大規模システムへの拡張が可能
課題や背景
- ◎IoTを活用していく意向はあるが、現実には何から手を付ければ良いか分からない。
また現時点で費用対効果が不明瞭なため、あまり費用もかけられない。 - ◎生産設備の稼働状況に関して、モニタリングはされておらず、定期点検や日報程度の情報しかないため事後対応(事後保全)に留まっていた。
成果・改善
- ◎IoT導入の第一歩として、機械設備の稼働状況をモニタリングできるようになった。また導入も比較的ローコストですんだ。
- ◎汎用パソコンで稼働状況のモニタリングやアラームの管理が出来るようになった。アラームの設定変更も容易にでき、変化に即応できるようになった。
- ◎生産設備の稼働状況をモニタリングすることで、稼働に関する具体的なデータを取ることができるようになった。
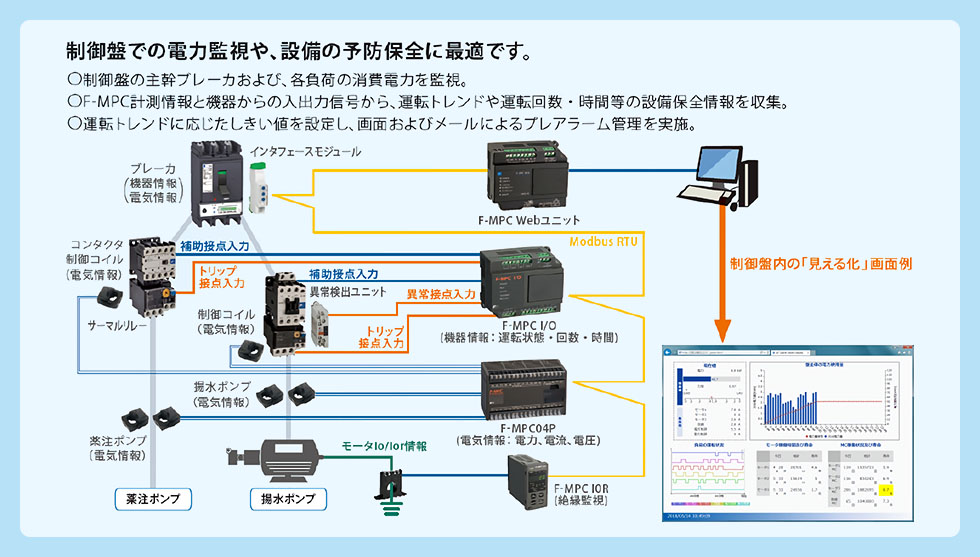
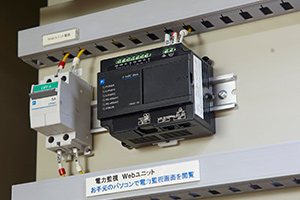
- ・省エネ施策のためのデータ収集・「見える化」・帳票作成が簡単に実現。
- ・デマンド監視とパターン制御により、空調制御などの省エネ施策をサポート。
- ・設備・機器の運転状態監視とアラーム機能により予防保全をサポート。
富士電機機器制御はココが違う
- 汎用パソコン、汎用ブラウザで設定から制御・監視、予防保全まで。
- 専用のプログラムやPLCなどの機器も不要のため、ローコストではじめられる。
- 部分的な導入でも後から拡張可能。