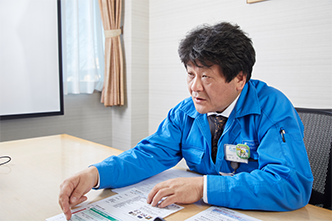
製品開発試験を
自社内で完結できる
集約型評価試験施設
「TECHNO LAB(テクノラボ)」
ものづくりには試験が欠かせません。富士電機機器制御(以下FCS)では、高い品質や信頼性を実現するためにさまざまな試験を自社内で完結させていますが、中には他ではあまり見かけないレアな試験設備もあります。今回は遮断器・開閉機器等の遮断試験に欠かせない大電流遮断試験設備をご紹介。短絡試験用発電機を併設し、大容量出力試験が可能です。国内では数少ないこの試験設備の大切な機能や役割について開発本部技術開発部の宮沢部長に聞いてみました。
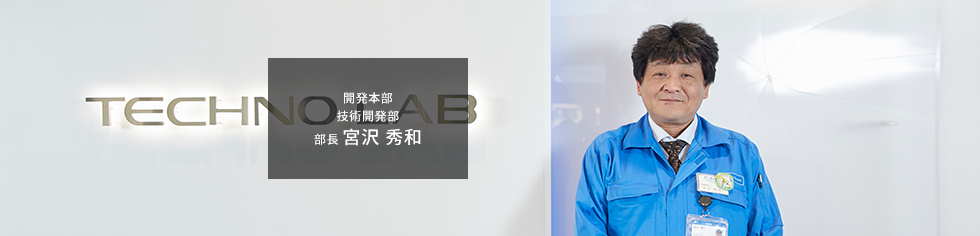
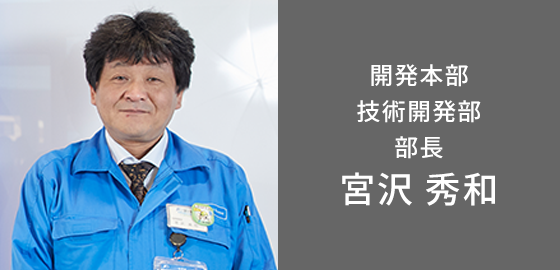
評価試験は設計開発と
二人三脚で品質をつくり込む。
─── テクノラボとは、どのような施設なのでしょうか?
宮沢:はい。簡単に言うと、工場内に散在していた試験施設、評価施設を一箇所に集約した、製品開発のための大規模評価施設です。約3,600m2の平屋建てで2014年12月に竣工しました。
開発の初期段階におけるシミュレーションから、素材開発や評価、試作品の制作、長期あるいは極限使用時の信頼性評価、さらには事故を想定した安全性評価など、製品開発の各段階における試験・評価を一手に行うことができます。
─── テクノラボを運用している技術開発部門とは、そもそもどんなことを行っているのでしょうか?
宮沢:一般の方は製品開発というと、まず「設計」を思い浮かべると思いますが、「設計」と「評価試験」は切っても切れない関係にあります。テクノラボを運用する技術開発部は、担当する技術領域に応じて3つの部門を設けています。開発試験部門は最も大きなチームで、すべての製品の評価試験を行っています。もう一つは製品化前の段階でシミュレーションを行う解析専門の部門、そして製品に使われる材料の評価・分析を行う材料研究部門があります。
宮沢:開発試験部門は、結果の○×を報告するだけでなく試験データから判断して、構造の改良案を提供し性能のつくり込みを行っています。具体的には、新商品開発の中で評価試験を行い、性能に影響する設計値から設計部門にアイデア改良点を提案することを主業務としています。その他にも国内外の規格認証のための試験、次期開発に向けた基礎技術検討や新たな試験方法・評価技術の検討など、やることは多いですね。さらに営業支援として、お客様からの試験依頼に応えることもしています。
─── 開発・設計部門と評価部門が一体になってのものづくりということですね。
宮沢:そうですね。評価試験はお客様の立場で品質をつくり込む作業だと考えています。試験は製品規格に厳格に決められた条件や手順があり忠実に実施するわけですが、さまざまな使われ方を想定した性能や品質をつくり込むことが、ものづくりにおいては重要なプロセスです。
宮沢:私たちの製品であるコンポーネントの性能を分類すると、動作、遮断、耐環境、振動・衝撃、寿命、取扱いなどが挙げられます。それぞれの性能を確保するために、設計シミュレーションだけでは決められない様々なパラメータの最適値を、施設で試験を重ねることで探っていきます。またお客様の使用環境を考慮した信頼性評価や、取扱性を意識したインターフェース評価は、徹底してお客様の視点から行われています。
希少な試験設備が
富士電機機器制御の
ものづくり品質を支える
─── 試験はすべて自社内で完結すると聞きましたが、それは珍しいことなのでしょうか?
宮沢:大手メーカなら、同じように自社で完結できるところもあると思いますが、たとえば大電流が必要な開閉や事故を想定した短絡などを試験できる設備を持っている会社はあまりないと思います。当社は「テクノラボ」に新設した直流1500Vの遮断試験設備を含め3つの大電流試験設備を保有していますが、その中でも最も大きな電流が流せる短絡試験用発電機が事業所敷地内にあり、この容量の設備は国内でも数えるほどしかない特殊な設備だと思っています。
宮沢:当社の主力商品であるマグネットスイッチ(電磁接触器)の商品化に際してはJISの形式試験が欠かせません。形式試験には、温度、動作、耐電圧、閉路遮断、短絡など多様な試験項目がありますが、当社ではすべて社内で完結することができます。また開閉器ですから、実際に開閉させて通電した時の電気的耐久性などの寿命評価も重要です。モータの起動停止を模擬した大電流による電気的な耐久性試験設備があるのですが、これもなかなか「レア」な試験設備だと思いますよ。お客様に満足していただくために、当社ではこれらすべての試験を内製化された設備を使い、自社のノウハウで実施しています。
─── 一つの製品の試験にどのくらいの期間がかかるのでしょうか?
宮沢:開発の規模によって必要な試験項目が決まってくるので一概には言えませんね。個別の一つの試験で説明するならば、環境試験であれば2か月程度で評価を行います。耐久性試験であれば2~3ヶ月程度。器具製品は設置されてから期間にして10年~20年、電磁接触器においては電気的200万回、機械的1000万回使われる製品もあります。これらを加速的に数ヶ月で評価を行っています。これらを各開発工程の中で一連の試験を行うわけですから、一つの製品の性能確認には数ヶ月程度の評価期間が掛かっいると思います。その意味でこの「テクノラボ」では、いたる所で常に何らかの試験が行われていますね。
自社内で製品試験を
完結できる強みとは?
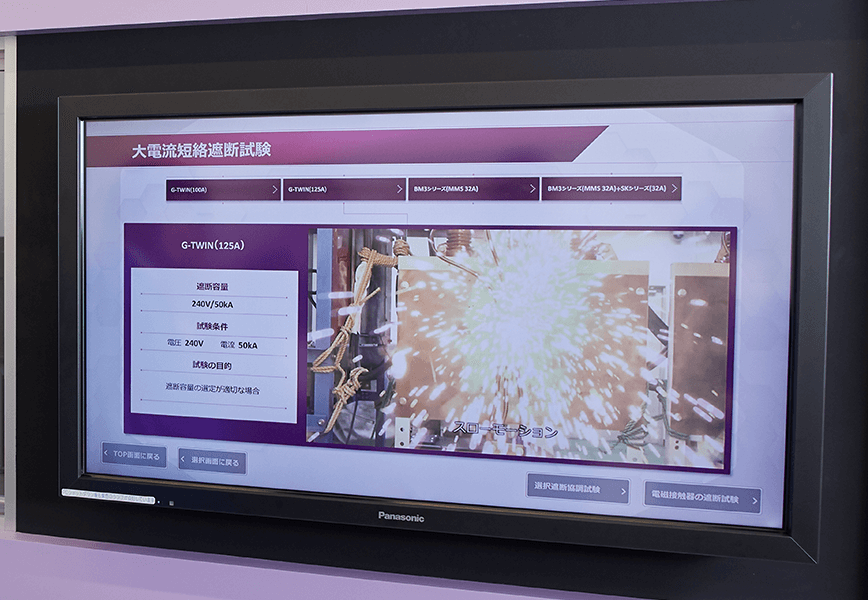
─── 試験の自社内完結でお客さまにはどんなメリットがありますか?
宮沢:まず時間の節約です。試験を外部委託する場合はスケジュールがこちらの自由には調整できず開発期間やお客様への納期に影響が出てしまいますが、必要な試験設備は自社内で調整可能なので最短の試験期間が設定できます。さらに試験設備を「テクノラボ」に集結したので、建屋内で一貫した試験が効率的に行われるようになりました。そして自由度でしょうか。製品規格から要求される試験条件だけでなく、条件をいろいろ変えて追加試験や試行錯誤の試験がタイムリーに実施できます。製品の使用環境は年々厳しくなってきていますから判定基準のレベルを上げることも必要で、自社内ならそれを臨機応変に実施することが可能です。
「テクノラボ」は今後、どのように進化するのでしょうか?
宮沢:試験の効率化と自動化をさらに進化させたいですね。たとえばブレーカの特性を測定する試験の自動化です。以前は一つの試験電源に製品を数台繋いで、製品がOFFになったら手作業で電線を繋ぎかえ再通電させる必要があり、試験員が付きっきりになっていました。そこで一連の作業を自動化できるように設備を自作したんです。夜セッティングしておけば朝には試験が完了しているので作業時間の大幅改善ができました。そのような改善が期待できる試験が他にもあるので、どんどん進めていきたいと思っています。「テクノラボ」は製品品質における最後の砦。それがFCS製品の品質をさらに高める原動力になると思っています。