設備保全とは
設備保全とは
設備保全とは、機械や設備の状態を把握し、安全・安定的に稼働できる状態を維持すること、設備に突発的に発生した故障など異常を発見した場合に適切な処置を実施することの2つの要素からなります。
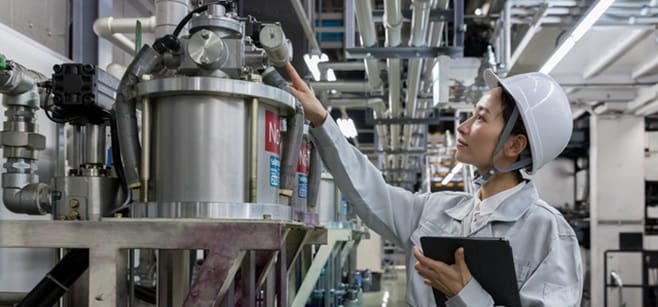
設備保全の課題
製造業を取り巻く環境変化により、対応すべき課題は多数あります。例えば食品工場の場合は生産年齢人口の減少にともなう人材不足、多品種少量生産への対応や短納期化への対応、進む生産設備の高度化と重要設備の老朽化対策など対応すべき課題はさまさまです。
このような環境下において重要度を増しているのが設備保全です。生産設備の高度がか進み、生産設備の停止による機会損失が以前より大きくなっており、一方で生産年齢人口の減少により新旧両設備の保全ができる人材が不足しているためです。
この課題を解決するためには、生産設備の保全方式を従来の予防保全・事後保全から、予知保全・予兆保全に切り替えることが有効で、さまざまな業界で保全方式の見直しが進んでいます。
設備保全の目的
設備保全の基本的な考え方には突発的な故障を減らし、機械・設備機能を維持すること、機械・設備の長寿命化とライフサイクルコストの低減などがあります。
設備機能の維持
工場現場で機械・設備の突発的な故障による停止は、修繕費用が必要になるだけでなく、生産活動が停止することによる機会損失を被ることになります。これを予防し、機械・設備の性能・機能を維持するためには設備や機器の保全活動が重要になります。
設備の保全活動・ライフサイクルコストの最小化
設備保全を行うことでライフサイクルコスト(LCC:Life Cycle Cost。機械・設備を取得してから、役割を終えるまでにかかる総コスト)を最小化する狙いがあります。
設備の長寿命化
機械・設備を適切に保全することで、想定耐用年数よりも長く機械・設備を稼働させることが可能になります。
「国土交通省所管分野における社会資本の将来の維持管理・更新費の推計(2018年度)」(国土交通省) では、予防保全の 「長寿命化等による効率化の効果」を示すため、「事後保全」と「予防保全」の考え方を基本とする試算の比較が行われました。
この結果「事後保全」よりも、「予防保全」の考え方を基本とした推計のほうが、5年後、10年後、20年後で維持管理・更新費が 約30%減少し、30年後には約50%減少するという結果になりました。
「事後保全」から「予防保全」へ切り替えることによる費用の縮減効果が大きいことを示しており、言い換えると、予防保全は 「長寿命化等による効率化の効果」があると考えられます。
設備保全とメンテナンスの違い
設備保全とメンテナンスは同じ意味合いで使われています。厳密には設備保全の場合「設備の不具合・故障が発生しないように対処すること」の意味が含まれるのに対し、メンテナンスは「設備の不具合・故障箇所の修理・調整をすること」という意味で利用される場合が多くあります。
生産設備の保全方式
保全方式は「予防保全」「事後保全」「改良保全」の3つに分類できます。予防保全は機械・設備が故障や不具合がおこる前にメンテナンスを行い、これを回避する方式です。事後保全は故障や不具合が発生した後に実施する方式のことです。
一般的には故障や不具合が発生した場合のリスクや損失が大きいものについては予防保全を実施し、そうでない場合については事後保全を選択するなど、リスクに応じた保全方式の選択が求められます。
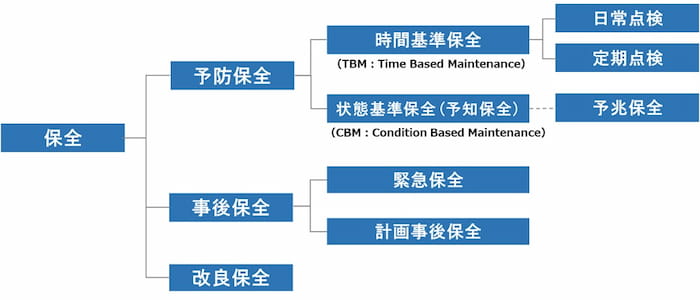
事後保全
事後保全とは、機械・設備の機能の異常や不具合が発生した場合や、障害・故障が発生して停止した際に行う保全対策のことです。事後保全の方式種類には「緊急保全」と「計画事後保全」があります。
緊急保全とは、突発的におこった故障や生産設備の停止に対し、現場で直ちに修理などの保全作業を行うことです。
計画事後保全とは、あらかじめ代替え機械・設備を用意しておき、有事の際に切り替えることで設備機能が完全停止しないようにする方式です。
事後保全のメリットは、故障がおきなければ日々のメンテナンス費用や保全作業が発生しないことです。故障しても部品の交換が短時間でできることがわかっており、 生産ラインへの影響も軽微な場合は、事後に対応することにメリットがあります。
デメリットは、部品や予備機などの設備を用意する必要があること、事後対応となるため、原因の調査に時間がかかる場合や、代替え機の手配状況により復旧までの時間がかかってしまう場合があります。
予防保全は故障や事項を未然に防ぐことを目的としますが、どのような保全計画を立てたとしても突発的な故障や事故を100%回避するのは不可能です。 そういった事態が起こりえることを前提とし、設備機能が停止してしまうのを避ける・軽減することを目的としていることが事後保全の考え方になります。
予防保全
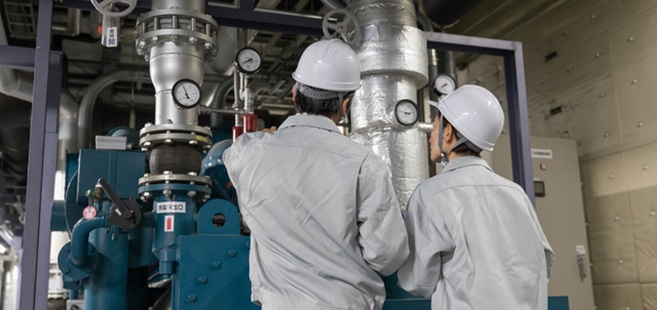
予防保全とは、機械・設備の機能の異常や不具合が発生する可能性がある場合に、予防的に行われる保全対策のことです。設備の故障を回避し、安定稼働を維持するために行う定期メンテナンスを指します。
例えば耐用年数・耐用時間などをあらかじめ決めておき、機械・設備のメンテナンスや部品の交換を行うことで設備の保全を行うことで、故障から復旧するまでの時間が短くなり、設備の長寿命化ができ、ライフサイクルコストを抑えることが期待できます。
一方で、設備の状態を問わず、保全計画どおりに作業が実行されるため過度の保全、もしくは想定以上に早く劣化しているなどの不十分な状況が発生する可能性があります。
予防保全の方式種類には、経過時間や稼働時間などを基準にした「時間基準保全」、稼働状態をモニターする「状態基準保全(予知保全)」があります。
予防保全のメリット
製品品質の向上
機械・設備の故障や機能の低下が起こることは製品不良が発生する可能性があることを意味します。予防保全を行うことで、機械設備を常に正常な状態に保つことで、製品不良を出さない・製品品質を落とさない安定した生産が可能になります。
ダウンタイムの最小化による機会損失の低減
故障した設備や機械を修理・交換し正常な状態に戻るまでには時間がかかり、その設備や機械が可動しなかっただけの損失が生じます。予防保全を行うことで、このような事態を未然次防ぐことや機会損失を最小化することが可能になります。
予防保全のデメリット
過剰な保全活動によりメンテナンスコストがかかる場合がある
予防保全は故障する前に機械や部品を交換する方式です。まだ正常に稼働していたとしても、保全作業を実施するため、結果としてメンテナンスコストなどが高くなってしまう可能性があります。
予防のための適切な閾値の設定が難しい
定期的な保全でも、時間経過の保全でもなにをもって保全を行うかという閾値をどう設定するのかは課題になります。この設定が適切でない場合は、過剰保全や予防保全ができない状態になりえます。
予防保全の種類
予防保全には一定時間稼働した設備について行う時間基準保全(TBM:Time Based Maintenance)と、設備の状態を監視する予知保全/状態基準保全(CBM:Condition Based Maintenance)があります。
予知保全/状態基準保全のうち、とくにIoTなどを活用して、常時監視・計測を行い、機械や部品の劣化や故障を予知する保全方式のことを、予知保全もしくは予兆保全と呼ぶことがあります。
予防保全をいつ実施するのかを計画するための考え方として、バスタブ曲線(故障率曲線)があります。バスタブ曲線とは、時間が経過にしたがって発生する機械・装置の故障割合の変化がしますが、この故障率の変化曲線がバスタブのような形に似ていることからこう呼ばれています。
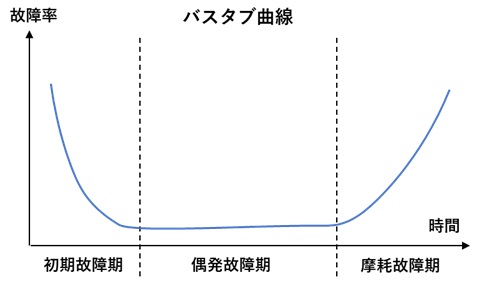
使用開始時は初期不良などの故障が発生するため故障率は高く(初期故障期)、初期故障が落ち着き偶発的な故障が発生(偶発故障期)、一定時間経過後は機械の劣化などが始まり、故障率が上昇する(摩耗故障期)という曲線です。時間を基準としたメンテナンス計画を行う際の有用な考え方となります。
時間基準保全(TBM:Time Based Maintenance)
一定の期間や時間稼働した機械や設備を予防的に更新するという保全方式です。時間基準保全には定期保全と経時保全があります。この方式はまだ故障していない設備や部品であっても、予防的に更新するやり方のため、保全コストにムダが生じる可能性があります。
時間基準保全には、日々点検・保全作業を実施する「日常点検」と、定期的に点検・保全作業を実施する「定期点検」があります。
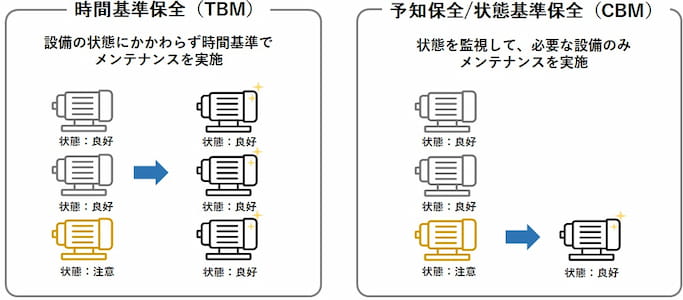
予知保全/状態基準保全(CBM:Condition Based Maintenance)
機械・設備を常時モニターし、状態異常や性能低下があった場合に更新する方式です。一般的に状態異常を診断するため閾値をあらかじめ準備・設定しておき、この閾値を越したら保全対策を行う等の方法をとります。
予防保全と予知保全の違いは保全のための点検や交換時期の違いにあります。
予防保全は、故障の兆候が見られない機械や設備に対しても予め決められた期間を過ぎれば、正常に稼働していたとしても部品交換やメンテナンスを実施します。
一方で予知保全の場合、異常や故障の予兆を検出して部品交換やメンテナンスを行うため、保全費用の最適化が可能になります。
予知保全によるコスト削減・IoT活用事例。予防保全から予知保全へ保全方式を切り替えることで、メンテナンスコストの低減やいままで対応が難しかった異常値の検知ができるようになります。
IoTを活用した設備保全
設備保全については従来熟練作業者の知識・経験にたよることが多く、退職などによりこのノウハウがなくなってしまうという課題がありました。 また、設備保全の人材育成には時間がかかります。さらに、近年では機械の高度化、製造プロセスの複雑化により、従来の知識・経験では保全活動や製品品質の維持が難しくなりつつあります。
これら課題を解決する方法が、AI・IoTやセンサーを活用した設備保全です。
AI・機械学習や統計解析を活用し、いままで熟練作業者でしか判断できなかった生産設備の故障予兆や不具合を 早期に発見できるようになります。これにより、設備保全作業の省力化や、工場全体の稼働率向上、製品品質の改善などが可能になります。
予知保全としてAI・IoTやセンサーを活用した設備保全が普及しつつあり、とくにリアルタイムで故障予兆を検知する設備保全の場合は予兆保全と呼ばれることがあります。
予兆保全
予兆保全はIoTを活用して設備の稼働状況や状態をリアルタイム監視・管理を行います。デジタルデータを活用し、故障の兆候をつかんだ時点で機械や部品の交換を行う保全方法です。
IoTやAI・機械学習を活用することにより、熟練作業員でも判断が難しい想定以上に早く劣化している設備や部品を検知し、生産ラインを停止するなどのリスクを回避することが可能になります。
このように予兆の検知にIoTやAIの分析手法を用いる保全方式を、従来の予知保全と区別して予兆保全と呼ぶことがあります。
機械・設備のメンテナンス作業
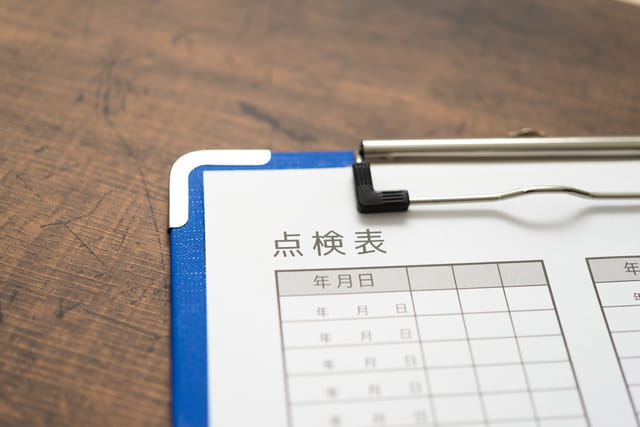
機械や設備が故障したり、不具合が起きてしまうと、工場の生産性の低下や機会損失を被ることにつながります。
生産性向上のためには保全活動を実施し、設備・機械の稼働率向上が必須で、このためには保全作業を保全計画にそって実施する必要があります。
機械・設備の保全の場合、具体的には点検、保守、運転・監視、清掃、修繕と改修があります。
点検
機械・設備の外観や運転状況等を確認します。点検には日常点検と定期点検があります。
保守
機械や設備の機能・性能を維持する目的で行われます。機械・設備の調整や消耗品の交換などを行います。
運転・監視
機械・設備の稼働状況・運転状況を監視・制御します。ネットワークやIoTなどを活用することで、設備の状態をリアルタイムで監視することも可能です。
清掃
機械・設備の劣化原因を取り除き、機械の性能の維持や腐食の防ぐことが目的です。
修繕
機械・設備の故障・破損などを修理、故障以前の稼働状態に回復させる作業です。
改修
既存の機械・設備に、新しい機械や付帯設備を追加し、設備機能を拡張することを指します。
設備保全・メンテナンス作業の効率化事例
保全管理システムの導入事例。輸送業A社では、保守・点検業務を紙ベースで行っていたため、承認業務や点検後の結果記録の効率が悪く、転記ミスが発生するなどの課題がりました。そこで、設備保全管理システムを導入、保守・点検業務のペーパレス化したことで部品在庫の管理制度の向上や過去の故障対応履歴の情報共有も可能にし、保全業務の生産性向上を実現しました。
/products/chemical/solution_detail/case01.html
化学系メーカーの予防保全導入事例。ファン監視による予防保全について、導入前の課題としてはインバーターノイズの影響で、回転機のベアリングの振動診断が難しい場合がありました。 今回、インバータキャリアノイズ除去に対応した回転機故障予兆監視システムを導入し、振動診断を実現。故障停止回避することで年間3千万円~7千万円の損失対策ができると試算しました
スマート保安の自社導入事例。山梨工場では多くのエネルギーを使用し、生産設備は連続稼働しているため電力供給は止めることができません。 設備管理上の課題は、「トレンドなどで監視して傾向管理したい」「高齢化が進んでいるため、ノウハウを伝承したい」などで、まるごとスマート保安サービスを導入することで、これらの課題解決を実現しました。
生産設備の保全業務標準化・設備状態の可視化事例。導入以前は各拠点の保全台帳・作業手順書の相違があったり、目視チェック、2重入力、検索に時間がかかるなどにより、各保全業務に多くの工数がかかっていた。保全管理システムを導入することで、生産設備の保全業務標準化を実現し、保全業務の自動化・効率化や、設備情報の可視化による状態監視保全を可能にしました。
化学工場の保全管理システムによる部品在庫の見える化事例。同社は設備修繕時に部品在庫が不足したことで、設備復旧まで設備稼働が停止してしまうことがありました。そこで設備点検計画を故障実態に合わせるために、保全管理システムを導入し、設備修繕部品在庫の見える化を実現。部品在庫不足を解消し、計画や生産への故障停止の影響を大幅に削減できました。
化学製造業A社のAI技術を活用した設備診断システム導入事例。同社は以前から数値管理と遠隔操作による設備診断を行っていたが、人による判断スピード・監視対象が増えることによる負荷について課題があった。そこで、富士電機のAI技術を搭載したMainGATE/MSPCを導入し、異常兆候検知の自動化を実現。異常兆候をスピーディに検知、高度な故障予知を可能にしました。
電気集塵機用電源設備のリニューアル対応事例。電気集塵機は火力発電所、化学プラント、硝子工場等に多数設置されてきた一方で、当時の納入業者の事業撤退などにより適切なサポートされていない場合があります。当社では機械メーカーとタイアップにより電気集塵機用電源設備のリニューアルに対応。電気集塵機の性能低下、生産ラインの停止や品質低下低減を可能にします。