導入事例
設備情報の可視化による状態監視保全
生産設備の保全作業の抽出・計画を自動化、年間の保全計画作成工数を約90%削減。
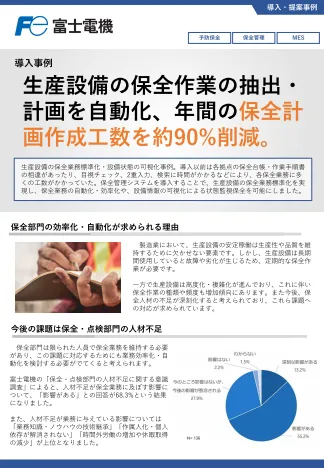
保全管理 ペーパレス化 DX
生産設備の保全業務標準化・設備状態の可視化事例。導入以前は各拠点の保全台帳・作業手順書の相違があったり、目視チェック、2重入力、検索に時間がかかるなどにより、各保全業務に多くの工数がかかっていました。保全管理システムを導入することで、生産設備の保全業務標準化を実現し、保全業務の自動化・効率化や、設備情報の可視化による状態監視保全を可能にしました。
保全部門の効率化・自動化が求められる理由
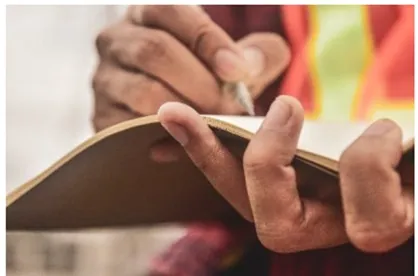
製造業において、生産設備の安定稼働は生産性や品質を維 持するために欠かせない要素です。しかし、生産設備は長期 間使用していると故障や劣化が生じるため、定期的な保全作 業が必要です。
一方で生産設備は高度化・複雑化が進んでおり、これに伴い 保全作業の種類や頻度も増加傾向にあります。また今後、保 全人材の不足が深刻化すると考えられており、これら課題へ の対応が求められています。
今後の課題は保全・点検部門の人材不足
保全部門は限られた人員で保全業務を維持する必要 があり、この課題に対応するためにも業務効率化・自 動化を検討する必要がでてくると考えられます。
富士電機の「保全・点検部門の人材不足に関する意識 調査」によると、人材不足が保全業務に及ぼす影響に ついて、「影響がある」との回答が68.3%という結果 になりました。
また、人材不足が業務に与えている影響については 「業務知識・ノウハウの技術継承」「作属人化・個人 依存が解消されない」「時間外労働の増加や休暇取得 の減少」が上位となりました。
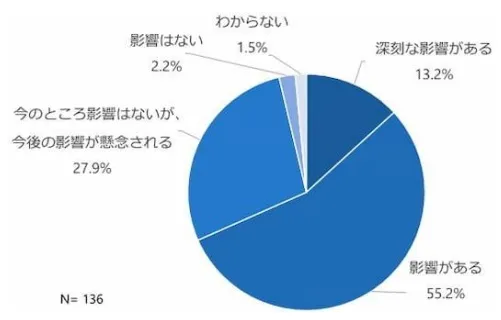
保全業務現場によくある課題
業種業界問わず、保全業務現場によくある課題としては、以下のようなものがあります。
・保全計画の作成・管理に工数がかかり、計画通りに実施できていない
・点検・作業の記録が煩雑で、作業内容の把握や分析が難しい
・設備の状態が把握できていないため、予防保全や修理のタイミングが適切ではない
これらの課題を解決する理想的な方法は、保全計画の作成から実績入力・分析までを、一元的に管理 できるようにすることです。この課題を解決する方法の一つが、保全管理システムの活用です。
保全管理システムとは
保全業務の一元化、効率化・自動化を実現するためには、保全管理システムの導入が有効です。一 般に保全管理システムでは、保全計画の作成や実績の入力・分析など、保全業務のさまざまなプロセ スを自動化・効率化する機能が提供されます。
保全管理システムを導入することで、 保全計画作成工数の削減、保全作業の予実管理の効率化、実績データの収集・集計工数の削減、設備状態の見える化による故障予防などの効果が期待できます。
導入事例:生産設備の保全業務標準化・設備状態の可視化事例
事例概要:保全部門では生産設備の保全作業の実施計画立案 から実績入力・分析を担っており、導入以前は各拠 点の保全台帳・作業手順書の相違があったり、目視 チェック、2重入力、過去実績の参照などが必要で あったため、各保全業務に多くの工数がかかってい ました。保全管理システムを導入することにより保全部門の 業務標準化を実現、保全業務の自動化・効率化や、 設備状態の可視化による状態監視保全を可能にしま した。
導入製品:保全管理システム(メンテナンスステーション)
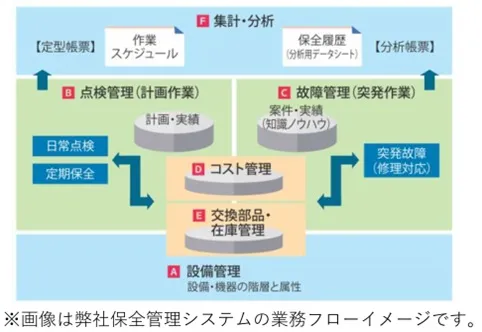
[導入以前の課題]
・保全計画作成・検索に時間がかかる
・作業内容の二重入力
・保全作業の予実管理を目視チェック
・実績データの収集・集計工数が大きい
・設備要因調査用の設備カルテがない
[導入効果]
記載内容の標準化、点検履歴の見える化、図の自動作成など保全業務の自動化・効率化を実現。
・保全計画作成工数:約90%削減
・点検/実績入力工数:約50%削減
・未実施項目抽出工数:約66%削減
・設備カルテ自動作成工数:75%削減 他
保全管理システム(メンテナンスステーション)について
設備や業務を統合し、最適化する設備管理ソリューション。設備情報や作業情報、故障情報等のデータ を活用し、何を・いつ・どのように保全すべきか、よりよい作業計画を立て業務を最適化します。業務 効率・安全性の向上、コスト削減、設備の長寿命化、そして「安全・安心」な環境を提供します。
資料ダウンロード
Webサイトのサービス向上のため、簡単なワンクリックアンケートへのご協力をお願いいたします。下記アンケートにご回答後、下記ボタンをクリックすると、新しいウィンドウでダウンロードページが開きます。
質問1:過去に富士電機のWebサイトへ訪問したことはありますか。
質問2:Webサイトの訪問目的についてお知らせください。
質問3:お勤め先の業種についてお知らせください。
関連事例:設備保全・予防保全
カテゴリ一覧
業種別ソリューション