富士電機自社の半導体製造工場における、FEMS(工場エネルギー管理システム)を活用した電気と熱の最適利用による省エネと、
エネルギー供給リスク回避の両立における取組みが評価され、平成28年省エネ大賞の最高賞[経済産業大臣賞]を受賞しました。
FEMSを活用し、「自社:山梨製作所」を
"エネルギーセキュリティ"と"省エネルギー化"の両立を実現したエネルギーのスマート化工場へと変革をすることができました。
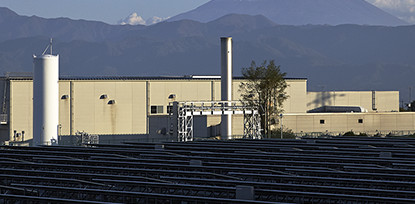
- ■所在地 ⼭梨県南アルプス市飯野221番地1
- ■敷地⾯積 ⼯場敷地 162,425㎡、
- ■取り扱い製品 産業⽤IGBT、⾞載IGBT
-
ガスコージェネ
導入による電力自給率
100%の実現 -
FEMSの活用による
持続的な
省エネ -
外気冷熱を利用した
クリーンルーム空調
大幅な改善
何故、エネルギーのスマート化工場を富士電機が目指したのか?
半導体製造工場においては、エネルギー消費が多く、エネルギー使用量の低減は大きな課題です。また、瞬低や停電などによる製造ロスコストも多大となります。
これらの課題を解決するため、FEMSを活用した電気と熱の最適利用による省エネと、エネルギー供給リスク回避の両立に取り組みました。省エネ対策として、クリーンルームの FFU(ファンフィルタユニット)最適運転制御、加湿・温度制御方式の改良、FEMSと連携したフリークーリング運転等を実施。また省エネだけでなくBCP(事業継続計画)の観点からも、 UPS、燃料電池とガスエンジンによるコージェネレーションシステムの導入を図り、コージェネの排熱も徹底的に活用しました。これらにより、2015年度には2010年度比34%のエネル ギー使用量削減を実現。瞬低・停電リスクの回避、電力自給率100%も達成しました。
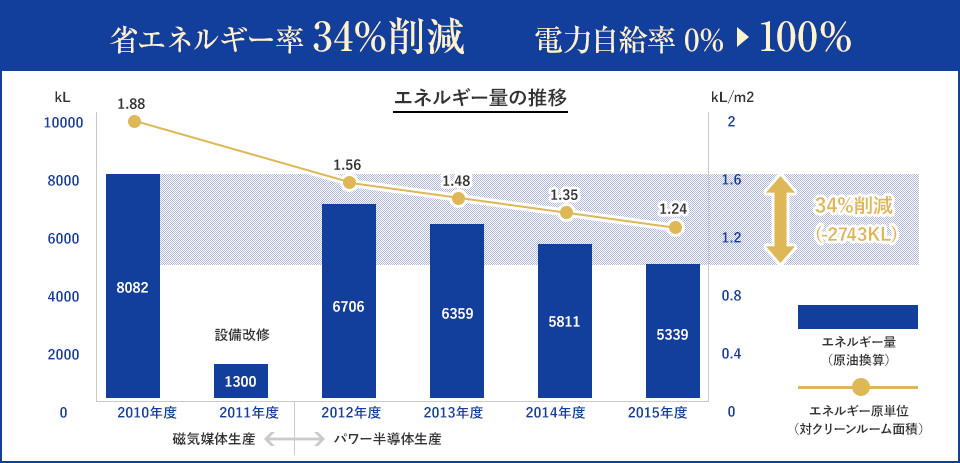
FEMSを中心とした富士電機の新たな取り組み
-
工場内のクリーンルーム(CR)や、
外気冷熱、熱排気の利活用による空調エネルギー改善空調エネルギー改善による燃料削減 削減効果 (原油換算) 削減率 66 %
ものつくりにおいては、「工場=生産の現場」です。省エネや工場内の最適化に取り組む場合には、まず最初に生産ラインの見直しを行うのが一般的な考え方なのかもしれません。ただ、工場エネルギー全体を包括的に考えた場合、実はそれ以外の部分の最適化を行う方がスマートな場合があります。
山梨製作所の場合、気象条件を活用し、外気冷熱を利用したフリークーリングや、機器から出る熱排気で屋外に排気していたものを有効活用するなどの改善を最初に実施しました。
このような空調関係のような"ものつくりの本質とは異なる側面"の省エネ内容に着目、実行していったことが大幅な省エネ効果を生み、工場内のスペース削減、ひいては工場全体の最適化に繋がりました。 -
ガスコージェネ(ガスエンジン、燃料電池)で
電力自給率100%達成と排熱利用ガスコージェネの排熱利用による燃料削減削減効果 (原油換算) 削減率60%
省エネはもちろんのコト、自然災害を含めた様々なリスク回避対策を行うことは非常に重要なコトであるといえます。特に山梨製作所は、東日本大震災の計画停電に伴うエネルギー供給の悪化。本格的にプロジェクトに着手する前は、雷や雪、鳥獣被害に悩まされていました。そこでガスコージェネ(ガスエンジンと燃料電池)を導入し、工場内の電力自給率100%を達成することで、系統電力の瞬低/停電リスクを最小限にすることができました。また、このガスコージェネ自体から発生する排熱(排ガスや温水)を有効活用することで、工場内で利用される燃料自体の削減にも繋がっています。
-
FEMSを活用したスマート工場化
ムダなボイラーの稼働停止による燃料削減削減効果 (原油換算) 削減率66%
オールシーズン排熱有効利用削減効果 (原油換算) 削減率68%
FEMS=工場エネルギー管理システム(Factory Energy Management System)を活用することで、工場内の様々なエネルギー消費の見える化・制御をすることが可能です。山梨製作所では、エネルギー管理や生産設備のエネルギー使用・稼働状況を把握、見える化、分析を行うことにより例えば
- ・ムダなボイラーの稼働停止による燃料削減
- ・オールシーズン排熱有効利用
を実現しました。
- 見える化
- 分かる化
- 最適化