食品製造業・食品工場に関する動向調査
食品製造業における改善活動の実態調査
食品工場の改善活動、取り組み上位は「5S(7S)活動・3Mの排除・見える化」
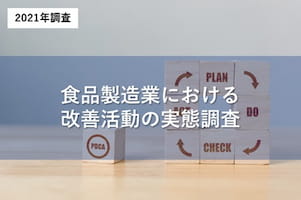
食品工場の生産性向上、品質維持と安心安全のためには日々の改善活動が重要です。
改善活動の手法にはさまざまな手法があり、HACCPへの対応を含め、5S・7Sの取組みが進んでいると考えられますが、実際にどのような施策に取り組むかは各工場によって異なります。
この「食品製造業における改善活動の実態調査」は食品製造業を対象に、食品工場で取り組まれている改善活動、改善活動で得られた効果、改善活動を継続するうえでの問題・課題についてインターネット調査を実施しました。
今後の食品工場の改善活動を実施するうえでの参考データとして利用いただくこと目的に調査結果を公開します。
-
食品製造業における改善活動の実態調査概要
-
調査項目
-
食品製造業における改善活動の実態調査結果
-
食品工場の改善活動への取り組み状況
-
食品工場における改善活動の取り組み単位
-
食品工場で改善活動に取り組む目的
-
改善活動を定着させるために実施している対応策・工夫
-
利用している改善活動の手法・取り組み状況
-
社内アンケート・意識調査
-
社内ヒアリング調査
-
QCサークル活動
-
IE手法/IE活動
-
見える化/見せる化
-
3M(ムリ・ムダ・ムラ)の排除
-
なぜなぜ分析
-
ISO9001の取得・継続
-
5S(7S)活動
-
5S(7S)活動に取り組んだことによる改善効果
-
KPIの活用状況
-
改善活動への取り組みに関する問題・課題について(FA)
-
調査結果ダウンロード
食品製造業における改善活動の実態調査概要
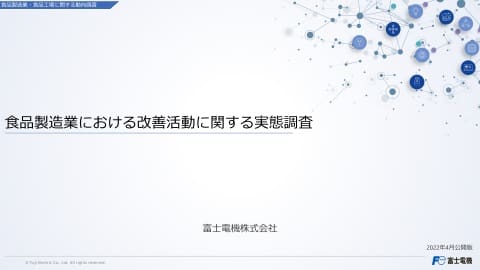
-
対象エリア
-
全国
-
調査対象者
-
食品製造業従事者
-
有効回答数
-
905人
-
調査方法
-
インターネット調査
-
調査期間
-
2021年10月26日~10月28日
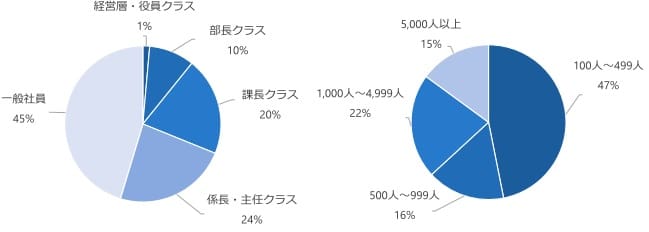
[左:回答者の役職]
-
経営層・役員クラス 1%
-
部長クラス 10%
-
課長クラス 20%
-
係長・主任クラス 24%
-
一般社員 45%
[右:従業員規模]
-
100人~499人 47%
-
500人~999人 16%
-
1000人~4999人 22%
-
5000人以上 15%
調査項目
-
食品工場の改善活動への取り組み状況
-
食品工場における改善活動の取り組み単位
-
食品工場で改善活動に取り組む目的
-
改善活動を定着させるために実施している対応策・工夫
-
利用している改善活動の手法・取り組み状況
-
社内アンケート・意識調査
-
社内ヒアリング調査 ― QCサークル活動
-
IE手法/IE活動
-
見える化/見せる化
-
3M(ムリ・ムダ・ムラ)の排除
-
なぜなぜ分析
-
ISO9001の取得・継続
-
5S(7S)活動
-
-
5S(7S)活動に取り組んだことによる改善効果
-
KPI(Key Performance Indicator)の活用状況
-
改善活動への取り組みに関する問題・課題について(FA)
以下、動向調査の内容を抜粋してご紹介いたします。
食品製造業・食品工場に関する動向調査の結果
食品工場の改善活動への取り組み状況
勤務先の食品工場の改善活動への取り組みについて「取り組んでおり、全体で定着している」と回答したのは全体の39.4%、 「取り組んでおり、一部で定着している」が32.2%、「取り組んでいるが、まったく定着していない」が7.1%となった(図1)。
従業員規模5000人以上では「取り組んでおり、全体で定着している」の回答は53.4%という結果になった。
一方、従業員規模100人~499人では29.6%となり、取り組み状況に23.8%の差が開いた。
図1 食品工場の改善活動への取り組み状況
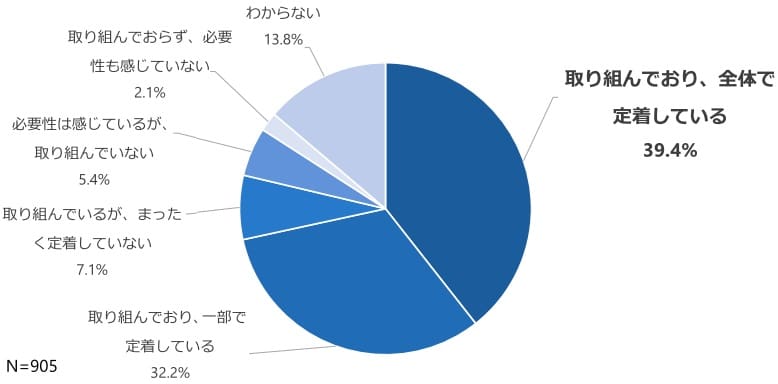
-
取り組んでおり、全体で定着している 39.4%
-
取り組んでおり、一部で定着している 32.2%
-
取り組んでいるが、まったく定着していない 7.1%
-
必要性は感じているが、取り組んでいない 5.4%
-
取り組んでおらず、必要性も感じていない 2.1%
-
わからない 13.8%
食品工場における改善活動の取り組み単位
改善活動の取り組み単位について、もっとも回答が多かったのは「全社単位で改善活動を行っている」で44.9%、 次いで 「食品工場の拠点単位で改善活動を行っている」で37.5%、「部門単位で改善活動を行っている」で28.8%の順に続く結果になった(図2) 。
従業員規模別の集計では「全社単位で改善活動を行っている」が最も多かったのは5000人以上の回答で61.1%、 最も少なかったのは100人~499人で回答は35.6%となった。
図2 食品工場における改善活動の取り組み単位
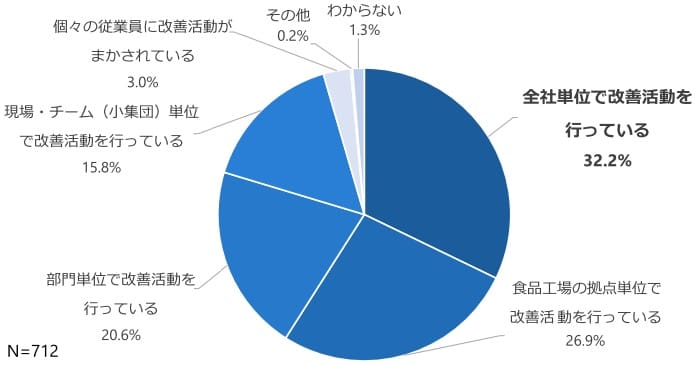
-
全社単位で改善活動を行っている 32.2%
-
食品工場の拠点単位で改善活動を行っている 26.9%
-
部門単位で改善活動を行っている 20.6%
-
現場・チーム(小集団)単位で改善活動を行っている 15.8%
-
個々の従業員に改善活動がまかされている 3.0%
-
その他 0.2%
-
わからない 1.3%
食品工場で改善活動に取り組む目的
改善活動に取り組む目的についてもっとも回答が多かったのは「生産性の向上」で74.3%、次いで「品質の向上」で71.9%、「コスト削減」で65.9%の順に続く結果になった(図3) 。
従業員規模別の集計では「品質の向上」が最も多かったのは5000人以上の回答で80.6%、最も少なかったのは100人~499人で回答は67.5%となった。
図3 食品工場で改善活動に取り組む目的
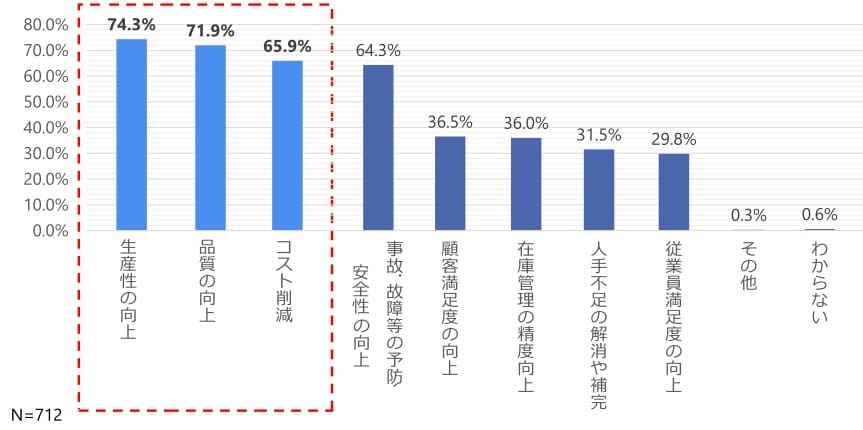
-
生産性の向上 74.3%
-
品質の向上 71.9%
-
コスト削減 65.9%
-
事故・故障等の予防、安全性の向上 64.3%
-
顧客満足度の向上 36.5%
-
在庫管理の精度向上 36.0%
-
人手不足の解消や補完 31.5%
-
従業員満足度の向上 29.8%
-
わからない 0.6%
-
その他 0.3%
改善活動を定着させるために実施している対応策・工夫
改善活動を定着させるために実施している対応策・工夫について、もっとも回答が多かったのは「教育・研修の実施」で44.8%、 次いで「改善活動グループの組織化」で36.2%、「定期報告会の実施」で35.5%の順に続く結果になった(図4) 。
従業員規模別では、5000人以上で「改善活動グループの組織化」が全体と比べやや高くなっている。
図4 改善活動を定着させるために実施している対応策・工夫
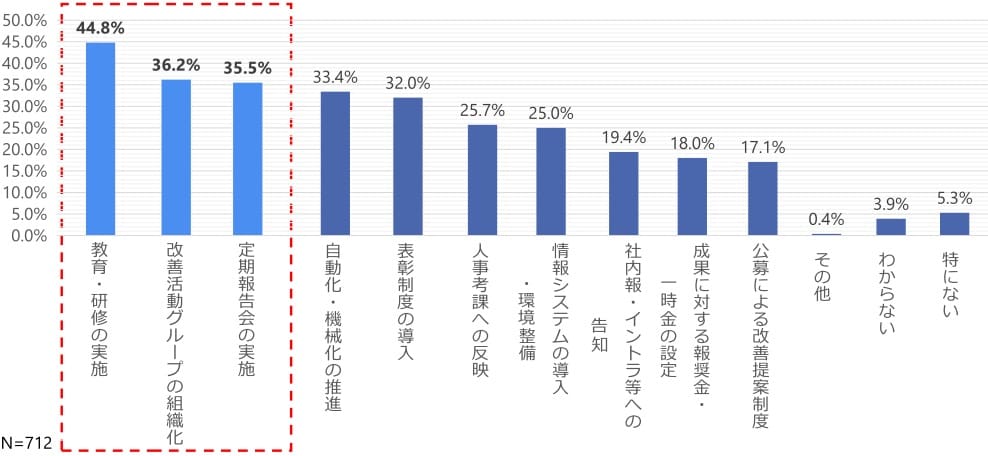
-
教育・研修の実施 44.8%
-
改善活動グループの組織化 36.2%
-
定期報告会の実施 35.5%
-
自動化・機械化の推進 33.4%
-
表彰制度の導入 32.0%
-
人事考課への反映 25.7%
-
情報システムの導入・環境整備 25.0%
-
社内報・イントラ等への告知 19.4%
-
成果に対する報奨金・一時金の設定 18.0%
-
公募による改善提案制度 17.1%
-
その他 0.4%
-
わからない 3.9%、・特にない 5.3%
利用している改善活動の手法・取り組み状況
利用している改善活動の手法・取り組み状況について、「5S(7S)活動」の回答が最も多く85.1%、次いで「3M(ムリ・ムダ・ムラ)の排除」が70.4%、「見える化/見せる化」が69.1%となった。(図5)。
図5 利用している改善活動の手法・取り組み状況
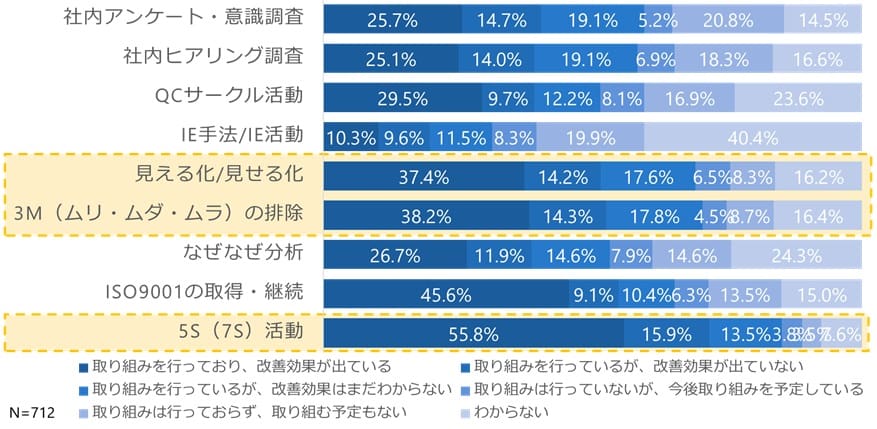
[「取り組んでいる」との回答比率]
-
社内アンケート・意識調査25.7%
-
社内ヒアリング調査25.1%
-
QCサークル活動29.5%
-
IE手法/IE活動10.3%
-
見える化/見せる化37.4%
-
3M(ムリ・ムダ・ムラ)の排除38.2%
-
なぜなぜ分析26.7%
-
ISO9001の取得・継続45.6%
-
5S(7S)活動55.8%
社内アンケート・意識調査
社内アンケート・意識調査について「取り組みを行っており、改善効果が出ている」と回答したのは全体の25.7%、「取り組みを行っているが、改善効果が出ていない」が14.7%、「取り組みを行っているが、改善効果はまだわからない」が19.1%となった(図6) 。
従業員規模別では従業員数が多くなるほど社内アンケート・意識調査が進んでいる傾向がみられた。
「取り組みを行っており、改善効果が出ている」が最も多かったのは5000人以上の回答で38.0%、最も少なかったのは100人~499人で回答は16.2%となった。
図6 社内アンケート・意識調査
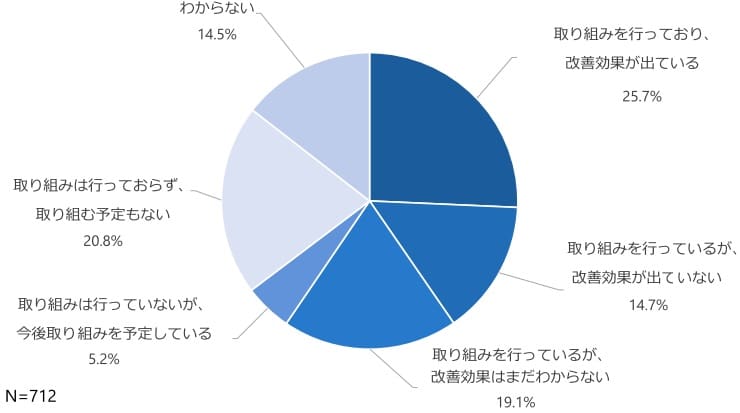
-
取り組みを行っており、改善効果が出ている 25.7%
-
取り組みを行っているが、改善効果が出ていない 14.7%
-
取り組みを行っているが、改善効果はまだわからない 19.1%
-
取り組みは行っていないが、今後取り組みを予定している 5.2%
-
取り組みは行っておらず、取り組む予定もない 20.8%、・わからない 14.5%
社内ヒアリング調査
社内ヒアリング調査について「取り組みを行っており、改善効果が出ている」と回答したのは全体の25.1%、「取り組みを行っているが、 改善効果が出ていない」が14.0%、「取り組みを行っているが、改善効果はまだわからない」が19.1%となった(図7) 。
従業員規模別では、1000人~4999人で「取り組みを行っており、改善効果が出ている」が全体と比べやや高くなっている。
図7 社内ヒアリング調査
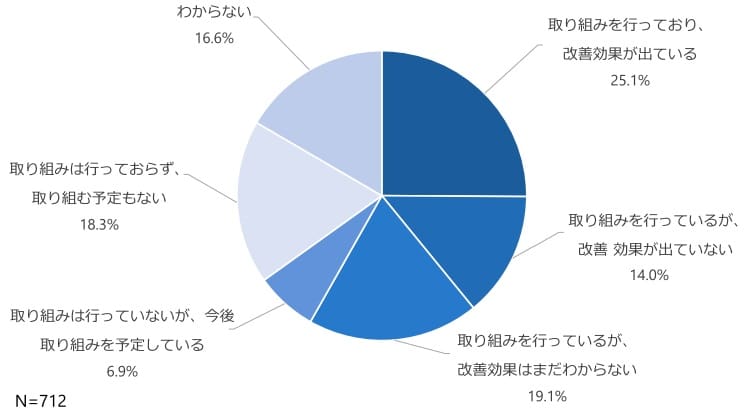
-
取り組みを行っており、改善効果が出ている 25.1%
-
取り組みを行っているが、改善効果が出ていない 14.0%
-
取り組みを行っているが、改善効果はまだわからない 19.1%
-
取り組みは行っていないが、今後取り組みを予定している 6.9%
-
取り組みは行っておらず、取り組む予定もない 18.3%
-
わからない 16.6%
QCサークル活動
QCサークル活動について「取り組みを行っており、改善効果が出ている」と回答したのは全体の29.5%、「取り組みを行っているが、 改善効果が出ていない」が9.7%、「取り組みを行っているが、改善効果はまだわからない」が12.2%となった(図8) 。
従業員規模別では従業員数が多くなるほどQCサークル活動が進んでいる傾向がみられた。
従業員規模5000人以上では「取り組みを行っており、改善効果が出ている」の回答は39.8%という結果になった。一方、従業員規模100人~499人では23.4%となり、取り組み状況に16.4%の差が開いた。
図8 QCサークル活動
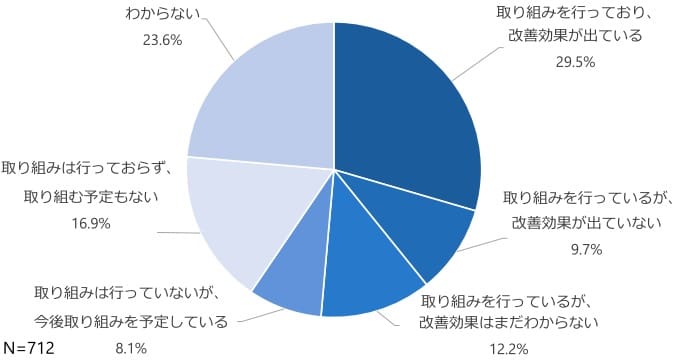
-
取り組みを行っており、改善効果が出ている 29.5%
-
取り組みを行っているが、改善効果が出ていない 9.7%
-
取り組みを行っているが、改善効果はまだわからない 12.2%
-
取り組みは行っていないが、今後取り組みを予定している 8.1%
-
取り組みは行っておらず、取り組む予定もない 16.9%
-
わからない 23.6%
IE手法/IE活動
IE手法/IE活動について「取り組みを行っており、改善効果が出ている」と回答したのは全体の10.3%、「取り組みを行っているが、 改善効果が出ていない」が9.6%、「取り組みを行っているが、改善効果はまだわからない」が11.5%となった(図9) 。
従業員規模別では、1000人~4999人で「全社的に利用されている」が全体と比べやや高くなっている。
図9 IE手法/IE活動
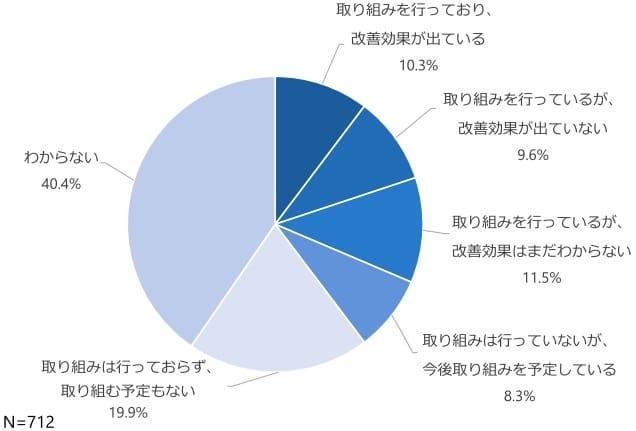
-
取り組みを行っており、改善効果が出ている 10.3%
-
取り組みを行っているが、改善効果が出ていない 9.6%
-
取り組みを行っているが、改善効果はまだわからない 11.5%
-
取り組みは行っていないが、今後取り組みを予定している 8.3%
-
取り組みは行っておらず、取り組む予定もない 19.9%
-
わからない 40.4%
見える化/見せる化
見える化/見せる化について「取り組みを行っており、改善効果が出ている」と回答したのは全体の37.4%、「取り組みを行っているが、改善効果が出ていない」が14.2%、「取り組みを行っているが、改善効果はまだわからない」が17.6%となった(図10) 。
従業員規模5000人以上では「取り組みを行っており、改善効果が出ている」の回答は51.9%という結果になった。一方、従業員規模500人~999人では27.4%となり、取り組み状況に24.5%の差が開いた。
図10 見える化/見せる化
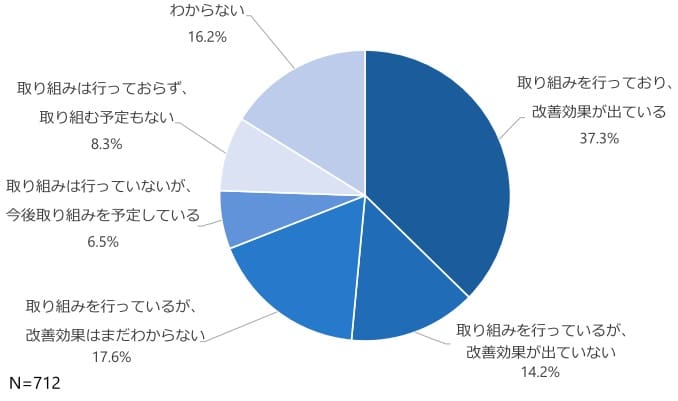
-
取り組みを行っており、改善効果が出ている 37.4%
-
取り組みを行っているが、改善効果が出ていない 14.2%
-
取り組みを行っているが、改善効果はまだわからない 17.6%
-
取り組みは行っていないが、今後取り組みを予定している 6.5%
-
取り組みは行っておらず、取り組む予定もない 8.3%
-
わからない 16.2%
3M(ムリ・ムダ・ムラ)の排除
3Mの排除について「取り組みを行っており、改善効果が出ている」と回答したのは全体の38.2%、「取り組みを行っているが、 改善効果が出ていない」が14.3%、「取り組みを行っているが、改善効果はまだわからない」が17.8%となった(図11) 。
従業員規模別では、1000人~4999人で「全社的に利用されている」が全体と比べやや高くなっている。
従業員規模1000人~4999人では「取り組みを行っており、改善効果が出ている」の回答は50.3%という結果になった。 一方、従業員規模100人~499人では30.0%となり、取り組み状況に20.3%の差が開いた。
図11 3M(ムリ・ムダ・ムラ)の排除
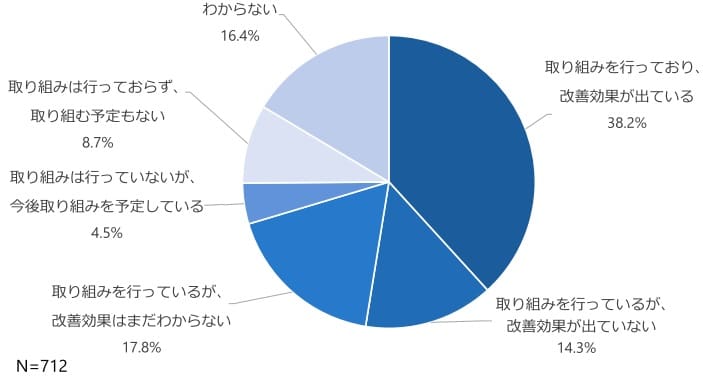
-
取り組みを行っており、改善効果が出ている 38.2%
-
取り組みを行っているが、改善効果が出ていない 14.3%
-
取り組みを行っているが、改善効果はまだわからない 17.8%
-
取り組みは行っていないが、今後取り組みを予定している 4.5%
-
取り組みは行っておらず、取り組む予定もない 8.7%
-
わからない 16.4%
なぜなぜ分析
なぜなぜ分析について「取り組みを行っており、改善効果が出ている」と回答したのは全体の26.7%、「取り組みを行っているが、 改善効果が出ていない」が11.9%、「取り組みを行っているが、改善効果はまだわからない」が14.6%となった(図12) 。
従業員規模別では従業員数が多くなるほどなぜなぜ分析が進んでいる傾向がみられた。
従業員規模5000人以上では「取り組みを行っており、改善効果が出ている」の回答は38.0%という結果になった。一方、従業員規模100人~499人では19.4%となり、取り組み状況に18.6%の差が開いた。
図12 なぜなぜ分析
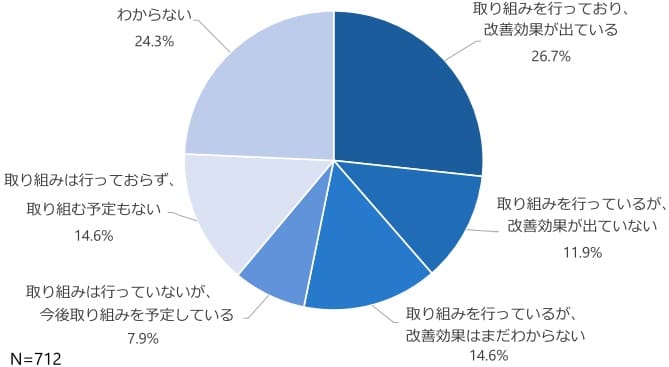
-
取り組みを行っており、改善効果が出ている 26.7%
-
取り組みを行っているが、改善効果が出ていない 11.9%
-
取り組みを行っているが、改善効果はまだわからない 14.6%
-
取り組みは行っていないが、今後取り組みを予定している 7.9%
-
取り組みは行っておらず、取り組む予定もない 14.6%
-
わからない 24.3%
ISO9001の取得・継続
ISO9001の取得・継続について「取り組みを行っており、改善効果が出ている」と回答したのは全体の45.6%、「取り組みを行っているが、改善効果が出ていない」が9.1%、「取り組みを行っているが、改善効果はまだわからない」が10.4%となった(図13) 。
従業員規模別では、1000人~4999人で「取り組みを行っており、改善効果が出ている」が全体と比べやや高くなっている。
図13 ISO9001の取得・継続
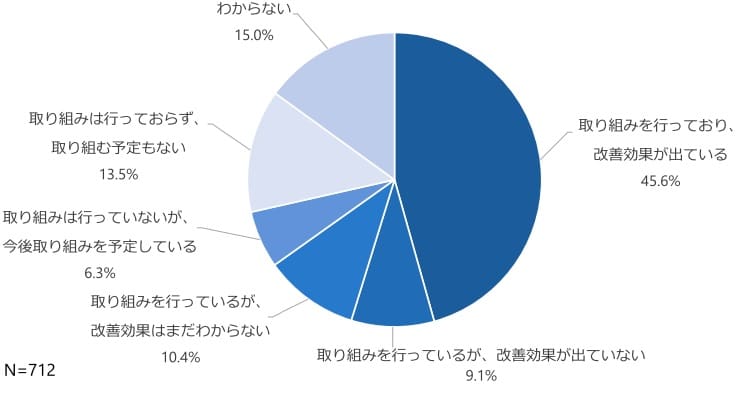
-
取り組みを行っており、改善効果が出ている 45.6%
-
取り組みを行っているが、改善効果が出ていない 9.1%
-
取り組みを行っているが、改善効果はまだわからない 10.4%
-
取り組みは行っていないが、今後取り組みを予定している 6.3%
-
取り組みは行っておらず、取り組む予定もない 13.5%
-
わからない 15.0%
5S(7S)活動
5S(7S)活動について「取り組みを行っており、改善効果が出ている」と回答したのは全体の55.8%、「取り組みを行っているが、 改善効果が出ていない」が15.9%、「取り組みを行っているが、改善効果はまだわからない」が13.5%となった(図14) 。 従業員規模別では従業員数が多くなるほど5S(7S)活動が進んでいる傾向がみられた。
従業員規模5000人以上では「取り組みを行っており、改善効果が出ている」の回答は64.8%という結果になった。 一方、従業員規模100人~499人では52.8%となり、取り組み状況に12.0%の差が開いた。
図14 5S(7S)活動
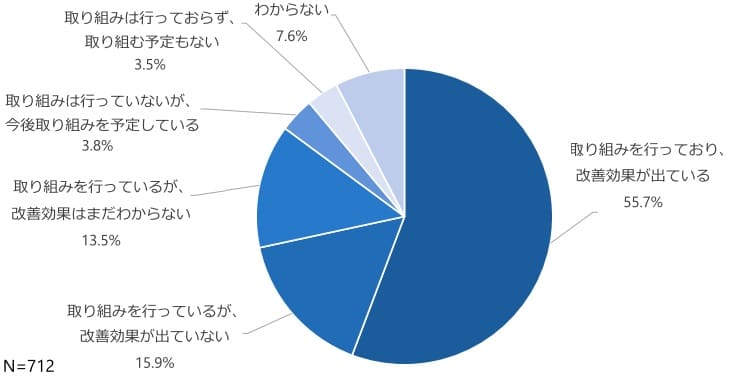
-
取り組みを行っており、改善効果が出ている 55.7%
-
取り組みを行っているが、改善効果が出ていない 15.9%
-
取り組みを行っているが、改善効果はまだわからない 13.5%
-
取り組みは行っていないが、今後取り組みを予定している 3.8%
-
取り組みは行っておらず、取り組む予定もない 3.5%
-
わからない 7.6%
5S(7S)活動に取り組んだことによる改善効果
5S(7S)活動に取り組んだことによる改善効果についてもっとも回答が多かったのは「作業品質の向上」で69.8%、 次いで「安全性の向上」で69.8%、「作業生産性の向上」で69.3%の順に続く結果になった(図15) 。
従業員規模別では従業員数が多くなるほど5S(7S)活動に取り組んだことによる改善効果が高くなる傾向がみられた。
図15 5S(7S)活動に取り組んだことによる改善効果
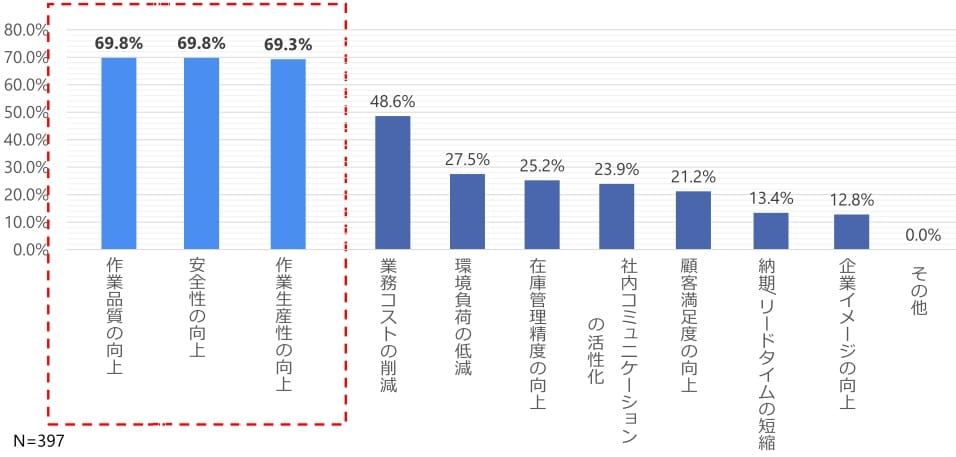
-
作業品質の向上 69.8%
-
安全性の向上 69.8%
-
作業生産性の向上 69.3%
-
業務コストの削減 48.6%
-
環境負荷の低減 27.5%
-
在庫管理精度の向上 25.2%
-
社内コミュニケーションの活性化 23.9%
-
顧客満足度の向上 21.2%
-
納期/リードタイムの短縮 13.4%
-
企業イメージの向上 12.8%
-
その他 0.0%
KPI(Key Performance Indicator)の活用状況
KPI(Key Performance Indicator)を活用した改善活動について「積極的に活用している」と回答したのは全体の20.1%、 「積極的ではないが、活用している」が20.2%、「まだ活用していないが、今後活用を検討している」が12.1%となった(図16) 。
従業員規模別では従業員数が多くなるほどKPI(Key Performance Indicator)を活用した改善活動が進んでいる傾向がみられた。 従業員規模5000人以上では「積極的に活用している」の回答は32.4%という結果になった。一方、従業員規模100人~499人では11.9%となり、取り組み状況に20.5%の差が開いた。
図16 KPI(Key Performance Indicator)の活用状況
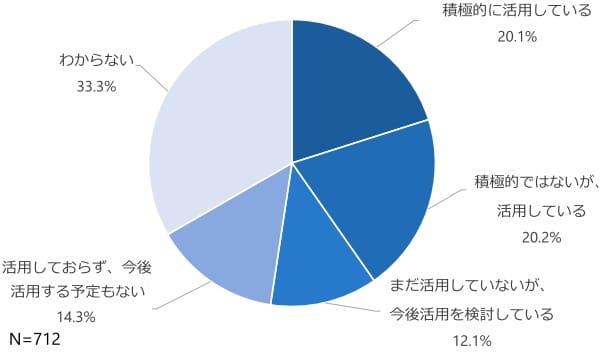
-
積極的に活用している 20.1%
-
積極的ではないが、活用している 20.2%
-
まだ活用していないが、今後活用を検討している 12.1%
-
活用しておらず、今後活用する予定もない 14.3%
-
わからない 33.3%
改善活動への取り組みに関する問題・課題について(FA)
改善活動への取り組みに関する問題・課題についてのFA(フリーアンサー)では、「現場への浸透・周知」「改善活動の形骸化」「PDCA」に関連する問題・課題が多くみられた(以下FA回答の抜粋)。
-
PDCAをうまく回せられるとよい改善活動になるが、そうでないと、場当たり的になり、改善活動にならない。
-
改善するとメリットの部分が改善されるが、デメリットの部分が出てきて結果的に改善されてない気がする。
-
進捗管理が形骸化しているような気がする。改善活動の資料を作るのがメインになって実際が出来てない。
-
改善項目が得意なものに限られており、フードディフェンスといった新しいテーマに取り組みがない。
-
現場作業員に派遣社員が多く、人の入れ替わりが多いことにより周知しきれない点が課題である。
-
改善活動が、考課に結びついていない。また、原理原則を理解していない改善も多く見られる。
-
食品衛生環境改善に取り組んでいるが、工場建屋の老朽化が顕著で改善効果に限界がある。
-
社内の業務等マニュアル化できておらず、誰か異動でいなくなると業務が進まない。
-
デジタル化が進むなか、どのような生産の向上に努めるべきか、今後の課題になっている。
-
改善活動のディスカッションなど活動することが目的となり、提案をするが果たせない。
-
機械が古くメンテナンスもやりにくく、部品も廃盤が多くなっている。生産性の減少や社員の負担に。
-
KPIの視点や、現場レベルの改善活動に興味を示さないので、改善活動事態が進まない。
-
現場からの声が届きにくい場合があり、改善に時間を要してしまう。
-
改善進捗にフィードバックが無いことがあり、管理が煩雑になる。
-
課題・問題点はその都度、工場内業務にフィードバック(反映)しているので、現時点では特に大きな問題点はない。
調査結果ダウンロード
本調査結果については以下よりダウンロードすることができます。
(ファイル形式:PDF、1.39 MB)
富士電機では食品製造業・食品工場に関連する動向調査を不定期に実施し、お客様に役立つ情報を発信しています。本調査に関するお問い合わせは「お問い合せ・導入に関するご相談」ページよりお知らせください。
[2023年調査]
[2022年調査]
[2021年調査]