食品製造業・食品工場に関する動向調査
食品工場の省エネルギー対策に関する実態調査
省エネルギー対策を推進するために必要となる「わかりやすい費用対効果」
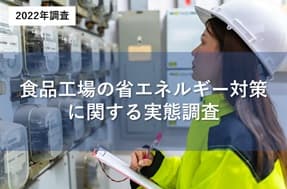
気候変動問題・SDGs(Sustainable Development Goals:持続可能な開発目標)への取り組みには省エネルギー対策が求められています。
2023年には改正省エネ法(エネルギーの使用の合理化等に関する法律)が施行されるため、省エネルギー対策をどのように進め、目標達成していくかは企業の重要なテーマの一つです。
省エネルギー対策に取り組むことは、食品工場の生産性を向上させる機会である一方で、どのように省エネルギー対策を実現していくかについては、食品工場の今後の課題となっています。
今回、富士電機の食品工場ソリューションサイトでは独自に食品工場の省エネルギー対策に関する調査を実施しました。
食品製造業勤務の工場・生産部門事業所・開発・研究所・物流・倉庫部門事業所に勤務している回答者を対象に、省エネルギー対策に関する取り組み状況、具体的に実施していること、問題・課題についての インターネット調査を実施し、「食品工場の省エネルギー対策に関する実態調査」としてまとめました。
配管工事不要で簡単に取付けられ、圧力損失の心配なしに蒸気流量を測定可能。高精度で飽和蒸気の流量を測定し、蒸気流量の「見える化」を実現。EMS連携で省エネにも貢献します。
食品工場の省エネルギー対策に関する実態調査概要
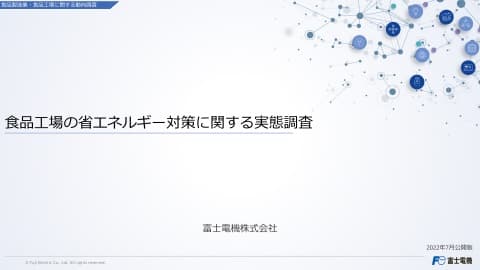
-
対象エリア
-
全国
-
調査対象者
-
食品製造業従事者
-
有効回答数
-
383人
-
調査方法
-
インターネット調査
-
調査期間
-
2022年6月24日~6月30日
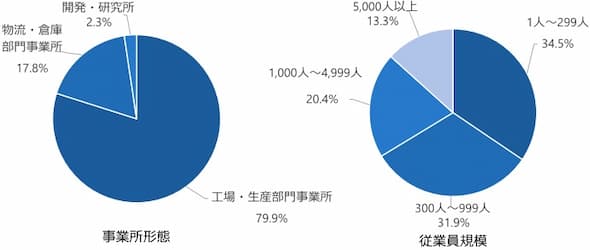
[左:回答者の事業所形態]
-
工場・生産部門事業所 79.9%
-
開発・研究所 17.8%
-
物流・倉庫部門事業所 2.3%
[右:従業員規模]
-
1人~299人 34.5%
-
300人~999人 31.9%
-
1,000人~4,999人 20.4%
-
5,000人以上 13.3%
調査項目
-
省エネルギー対策に関連した取組の実施状況
-
省エネルギー対策に取り組む理由
-
省エネルギー対策を推進していく上での問題・課題
-
エネルギー使用状況の見える化への取り組み
-
省エネルギー対策に対する具体的な取り組み状況
-
高効率・省エネ設備への切り替え
-
既存設備の改修・運用見直し
-
社内業務の改善・効率化
-
従業員の意識改革
-
EMS(エネルギー管理システム)の活用
-
省エネ関連サービスの活用
-
今後の省エネルギー対策に関連した取り組み
-
省エネルギー対策に関する問題・課題について(FA)
以下、動向調査の内容を抜粋してご紹介いたします。
食品製造業・食品工場に関する動向調査の結果
省エネルギー対策に関連した取組の実施状況
省エネルギー対策に関連した取り組みについて「取り組んでいる」と回答したのは全体の66.3%、「今後取り組む予定がある」が9.7%となった(図1)。
一方で、 「必要性は感じているが、取り組んでいない」が12.3% 、「取り組んでない」の回答は全体の5.7%となった。 従業員規模別では従業員数が多くなるほど省エネルギー対策に関連した取り組みが進んでいる傾向がみられた。
図1 省エネルギー対策に関連した取組の実施状況
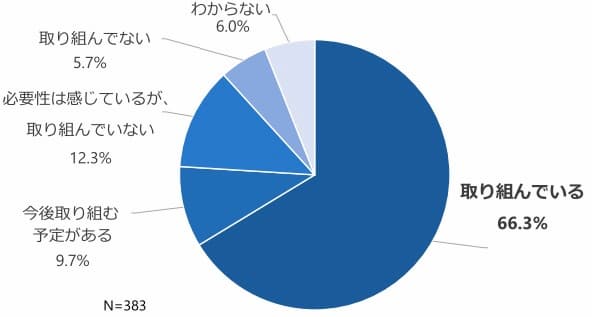
-
取り組んでいる 66.3%
-
今後取り組む予定がある 9.7%
-
必要性は感じているが、取り組んでいない 12.3%
-
取り組んでない 5.7%
-
わからない 6.0%
省エネルギー対策に取り組む理由
省エネルギー対策に取り組む理由について、もっとも回答が多かったのは「コスト削減・原価低減」で80.1%、次いで「地球温暖化対策・環境負荷の低減」で59.1%、「企業の社会的責任への配慮」で55.7%の順に続く結果になった(図2)。
「コスト削減・原価低減」「地球温暖化対策・環境負荷の低減」の回答については、従業員規模別で大きな差はみられなかった。
図2 省エネルギー対策に取り組む理由
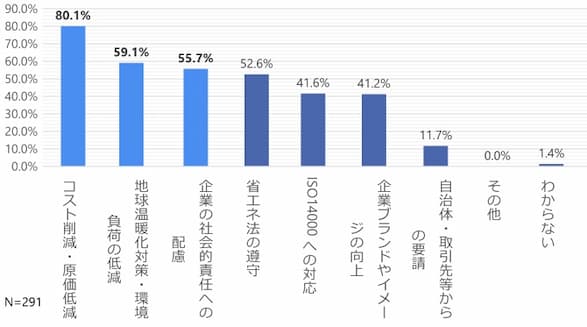
-
コスト削減・原価低減 80.1%
-
地球温暖化対策・環境負荷の低減 59.1%
-
企業の社会的責任への配慮 55.7%
-
省エネ法の遵守 52.6%
-
ISO14000への対応 41.6%
-
企業ブランドやイメージの向上 41.2%
-
自治体・取引先等からの要請 11.7%
-
その他 0.0%
-
わからない 1.4%
省エネルギー対策を推進していく上での問題・課題
省エネルギー対策を推進していく上での問題・課題について、もっとも回答が多かったのは「費用対効果がわかりにくい」で42.1%、次いで「必要な予算の確保」で39.4%、「従業員の理解・モチベーションが低い」で38.6%の順に続く結果になった(図3)。
従業員規模別では、特に大きな差はみられなかった。
図3 省エネルギー対策を推進していく上での問題・課題
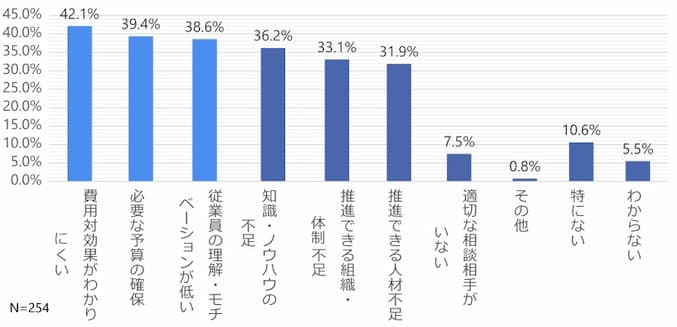
-
費用対効果がわかりにくい 42.1%
-
必要な予算の確保 39.4%
-
従業員の理解・モチベーションが低い 38.6%
-
知識・ノウハウの不足 36.2%
-
推進できる組織・体制不足 33.1%
-
推進できる人材不足 31.9%
-
適切な相談相手がいない 7.5%
-
その他 0.8%
-
特にない 10.6%
-
わからない 5.5%
エネルギー使用状況の見える化への取り組み
エネルギー使用状況の見える化への取り組みについて、「エネルギー使用状況の見える化を行っている」と回答したのは全体の76%となった(図4)。
このうち、「エネルギー使用状況の見える化を行っており、省エネルギー対策にも活用している」と回答は70.5%となった。一方で、「エネルギー使用状況の見える化を行っているが、省エネルギー対策には活用していない」が29.5%となった。 従業員規模別では従業員数が多くなるほどエネルギー使用状況の見える化への取り組みが進んでいる傾向がみられた。
図4 エネルギー使用状況の見える化への取り組み
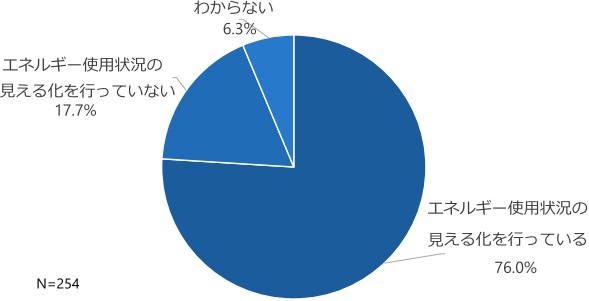
-
取り組んでいる 76.0%
-
エネルギー使用状況の見える化を行っていない 17.7%
-
わからない 6.3%
省エネルギー対策に対する具体的な取り組み状況
省エネルギー対策に対する具体的な取り組みについて、「高効率・省エネ設備への切り替え」の回答が最も多く50.4 %、次いで「既存設備の改修・運用見直し」が43.7 %、「社内業務の改善・効率化」が35.4%となった。(図5)。
図5 省エネルギー対策に対する具体的な取り組み状況
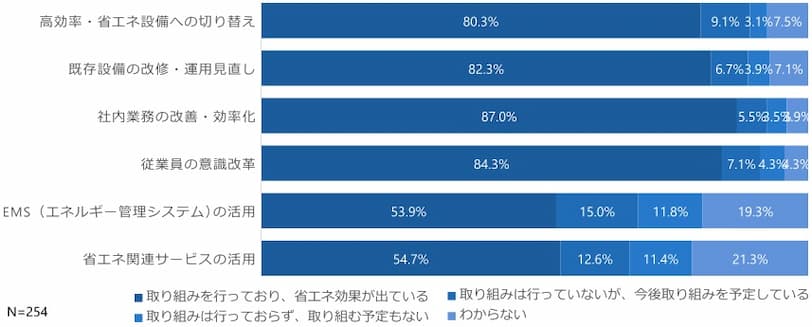
[「取り組んでいる」との回答比率]
-
高効率・省エネ設備への切り替え 80.3%
-
既存設備の改修・運用見直し 82.3%
-
社内業務の改善・効率化 87.0%
-
従業員の意識改革 84.3%
-
EMS(エネルギー管理システム)の活用 53.9%
-
省エネ関連サービスの活用 54.7%
高効率・省エネ設備への切り替え
高効率・省エネ設備への切り替えについて、「取り組んでいる」と回答したのは全体の80.3%となった(図6)。
このうち、 「取り組みを行っており、省エネ効果が出ている」と回答したのは62.7%、「取り組みを行っているが、省エネ効果が出ていない」が11.8%、「取り組みを行っているが、省エネ効果はまだわからない」が25.5%となった 。 従業員規模別では従業員数が多くなるほど高効率・省エネ設備への切り替えが進んでいる傾向がみられた。
図6 高効率・省エネ設備への切り替え
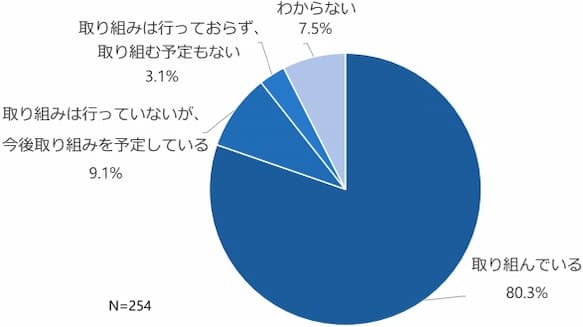
-
取り組んでいる 80.3%
-
取り組みは行っていないが、今後取り組みを予定している 9.1%
-
取り組みは行っておらず、取り組む予定もない 3.1%
-
わからない 7.5%
既存設備の改修・運用見直し
既存設備の改修・運用見直しについて、「取り組んでいる」と回答したのは全体の82.3%となった(図7)。
このうち、「取り組みを行っており、省エネ効果が出ている」と回答したのは54.4%、「取り組みを行っているが、省エネ効果が出ていない」が19.6%、「取り組みを行っているが、省エネ効果はまだわからない」が28.4%となった 。 従業員規模別では従業員数が多くなるほど既存設備の改修・運用見直しが進んでいる傾向がみられた。
図7 既存設備の改修・運用見直し
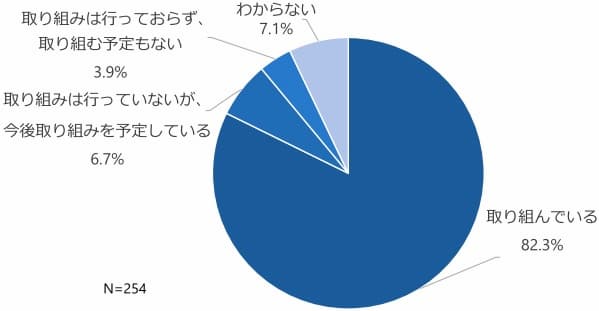
-
取り組んでいる 82.3%
-
取り組みは行っていないが、今後取り組みを予定している 6.7%
-
取り組みは行っておらず、取り組む予定もない 3.9%
-
わからない 7.1%
関連導入・提案事例
社内業務の改善・効率化
社内業務の改善・効率化について、「取り組んでいる」と回答したのは全体の87.0%となった(図8)。
このうち、「取り組みを行っており、省エネ効果が出ている」と回答したのは44.1%、「取り組みを行っているが、省エネ効果が出ていない」が27.9%、「取り組みを行っているが、省エネ効果はまだわからない」が36.3%となった 。 従業員規模別では従業員数が多くなるほど社内業務の改善・効率化が進んでいる傾向がみられた。
図8 社内業務の改善・効率化
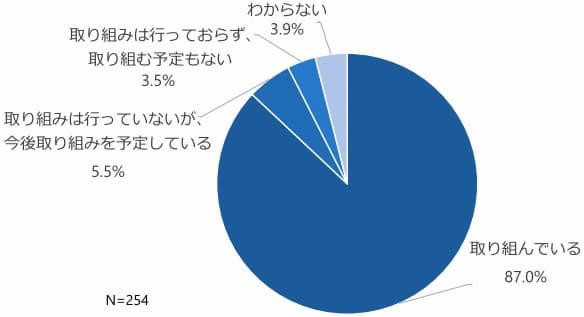
-
取り組んでいる 87.0%
-
取り組みは行っていないが、今後取り組みを予定している 5.5%
-
取り組みは行っておらず、取り組む予定もない 3.5%
-
わからない 3.9%
従業員の意識改革
従業員の意識改革について、「取り組んでいる」と回答したのは全体の84.3%となった(図9)。
このうち、「取り組みを行っており、省エネ効果が出ている」と回答したのは29.4%、「取り組みを行っているが、省エネ効果が出ていない」が28.9%、「取り組みを行っているが、省エネ効果はまだわからない」が46.6%となった。 従業員規模別では従業員数が多くなるほど従業員の意識改革が進んでいる傾向がみられた。
図9 従業員の意識改革
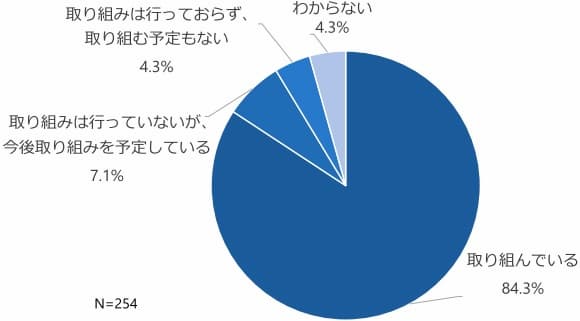
-
取り組んでいる 84.3%
-
取り組みは行っていないが、今後取り組みを予定している 7.1%
-
取り組みは行っておらず、取り組む予定もない 4.3%
-
わからない 4.3%
EMS(エネルギー管理システム)の活用
EMS(エネルギー管理システム)の活用について、「取り組んでいる」と回答したのは全体の53.9%となった(図10)。
このうち、 「取り組みを行っており、省エネ効果が出ている」と回答したのは33.8%、「取り組みを行っているが、省エネ効果が出ていない」が10.8%、「取り組みを行っているが、省エネ効果はまだわからない」が22.5%となった。
従業員規模別では1人~299人では「取り組みを行っており、省エネ効果が出ている」の回答は22.7%という結果になった。一方、従業員規模5,000人以上では45.5%となり、取り組み状況に22.8%の差が開いた。
図10 EMS(エネルギー管理システム)の活用
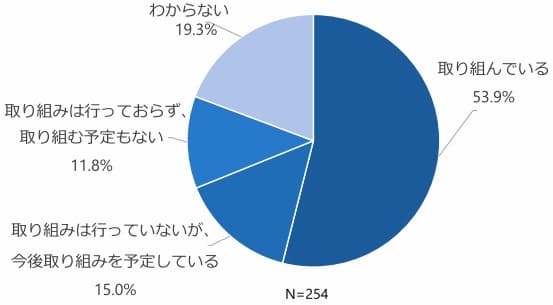
-
取り組んでいる 53.9%
-
取り組みは行っていないが、今後取り組みを予定している 15.0%
-
取り組みは行っておらず、取り組む予定もない 11.8%
-
わからない 19.3%
関連ソリューション
省エネ関連サービスの活用
省エネ関連サービスの活用について、「取り組んでいる」と回答したのは全体の54.7%となった(図11)。
このうち、 「取り組みを行っており、省エネ効果が出ている」と回答したのは21.3%、「取り組みを行っているが、省エネ効果が出ていない」が10.6%、「取り組みを行っているが、省エネ効果はまだわからない」が22.8%となった。 「取り組みは行っていないが、今後取り組みを予定している」の回答は全体の12.6%となった。
図11 省エネ関連サービスの活用
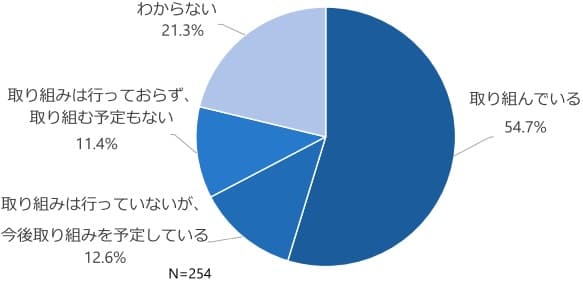
-
取り組んでいる 54.7%
-
取り組みは行っていないが、今後取り組みを予定している 12.6%
-
取り組みは行っておらず、取り組む予定もない 11.4%
-
わからない 21.3%
今後の省エネルギー対策に関連した取り組み
今後の省エネルギー対策に関連した取り組みについて「そう思う」と回答したのは全体の48.4%、 「ややそう思う」が36.2%となった(図12)。
一方で、「あまりそう思わない」が4.7%、「まったくそう思わない」の回答は全体の0.4%となった。 従業員規模別では、特に大きな差はみられなかった。
図12 今後の省エネルギー対策に関連した取り組み
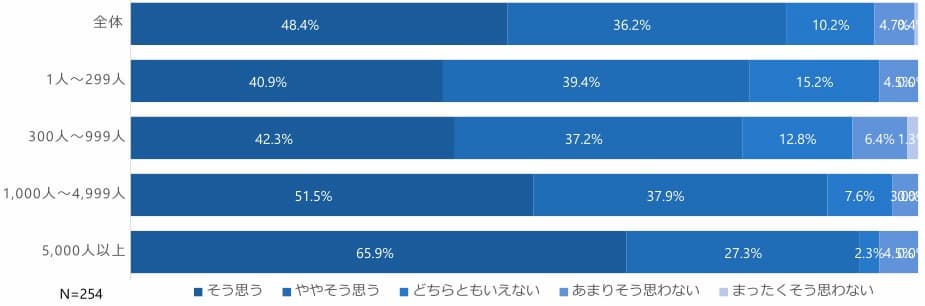
-
そう思う 48.4%
-
ややそう思う 36.2%
-
どちらともいえない 10.2%
-
あまりそう思わない 4.7%
-
まったくそう思わない 0.4%
省エネルギー対策に関する問題・課題について(FA)
省エネルギー対策に関する問題・課題についてのFA(フリーアンサー)では、「費用対効果」「社員の意識改革」「設備投資のための予算」に関連する回答が多くみられた(以下FA回答の抜粋)。
-
大きな成果を上げるためには投資が必要であり、費用がない。
-
費用対効果がでないと投資できない。環境取組は一概にコストだけでは語れないが実際は厳しい。
-
食肉生産加工の工場なので、冷蔵庫が必要不可欠だが、この夏の電力不足に節電協力したいが製品の安全面から、難しい。
-
数値の見える化 どう従業員に問題意識を植えるかが課題。
-
24時間稼働しているのでなかなか節電しにくい。設備を停められないことが多く、節電できない。
-
デマンドを利用しているが、それ以外ではまだ出来ておらず、具体的な対策が出来ていない。
-
対費用効果が見えにくい部分があるので、予算取り時の役員の理解が必須になる。
-
受注から出荷までの時間に制約があり、電力ピークをずらすことが困難。
-
省エネ対策が進むと成果が出にくくなる。これによって、社員のモチベーションが下がる可能性がある。
-
機械化できない細かい手作業が多い為、省エネルギー化がなかなか進まない。
-
省エネ活動で効果を確認しているが、金額で見た時に削減してもエネルギー価格の上昇が早く、金額的なメリットが実感できない。
-
継続して省エネに取り組んでいくと、徐々に原単位での省エネが厳しくなってきている。
-
導入した際の費用対効果がわかりにくいことや、見える化をおこなっていないので効果が実感しにくい。
-
部門毎に、省エネルギー対策への意識に温度差があるように感じる。
-
冷凍食品の、製造なので、大型冷凍庫にかかる電気代の削減方法が課題。
-
いろいろな取り組みがあるが、どれがベストなのかどれが効果があるのか不明。
-
取りまとめる組織がなく個別対応が行われ全体最適化がされない。
調査結果ダウンロード
本調査結果については以下よりダウンロードすることができます。
富士電機では食品製造業・食品工場に関連する動向調査を不定期に実施し、お客様に役立つ情報を発信しています。本調査に関するお問い合わせは「お問い合せ・導入に関するご相談」ページよりお知らせください。
[2023年調査]
[2022年調査]
[2021年調査]