富士電機のSDGs
生産時温室効果ガス排出削減
吹上工場「SF6ガス」削減プロジェクト
~温室効果ガスを削減し、サステナブルなものつくりを~
~温室効果ガスを削減し、サステナブルなものつくりを~
2023年8月公開。所属・業務内容は取材当時のものです
富士電機は、持続可能な社会の実現への貢献を目指し、「環境ビジョン2050」に沿って環境活動に力を注いでいます。各生産拠点では、温室効果ガス排出量削減や化学物質・廃棄物の適正管理、放出の削減に向けて、さまざまな取り組みを推進中。吹上工場における温室効果ガス「SF6ガス」削減の取り組みは、その象徴的な事例です。新技術開発に全力を注いだメンバーたちが、プロジェクトの概要とそこに込めた想いを語ります。
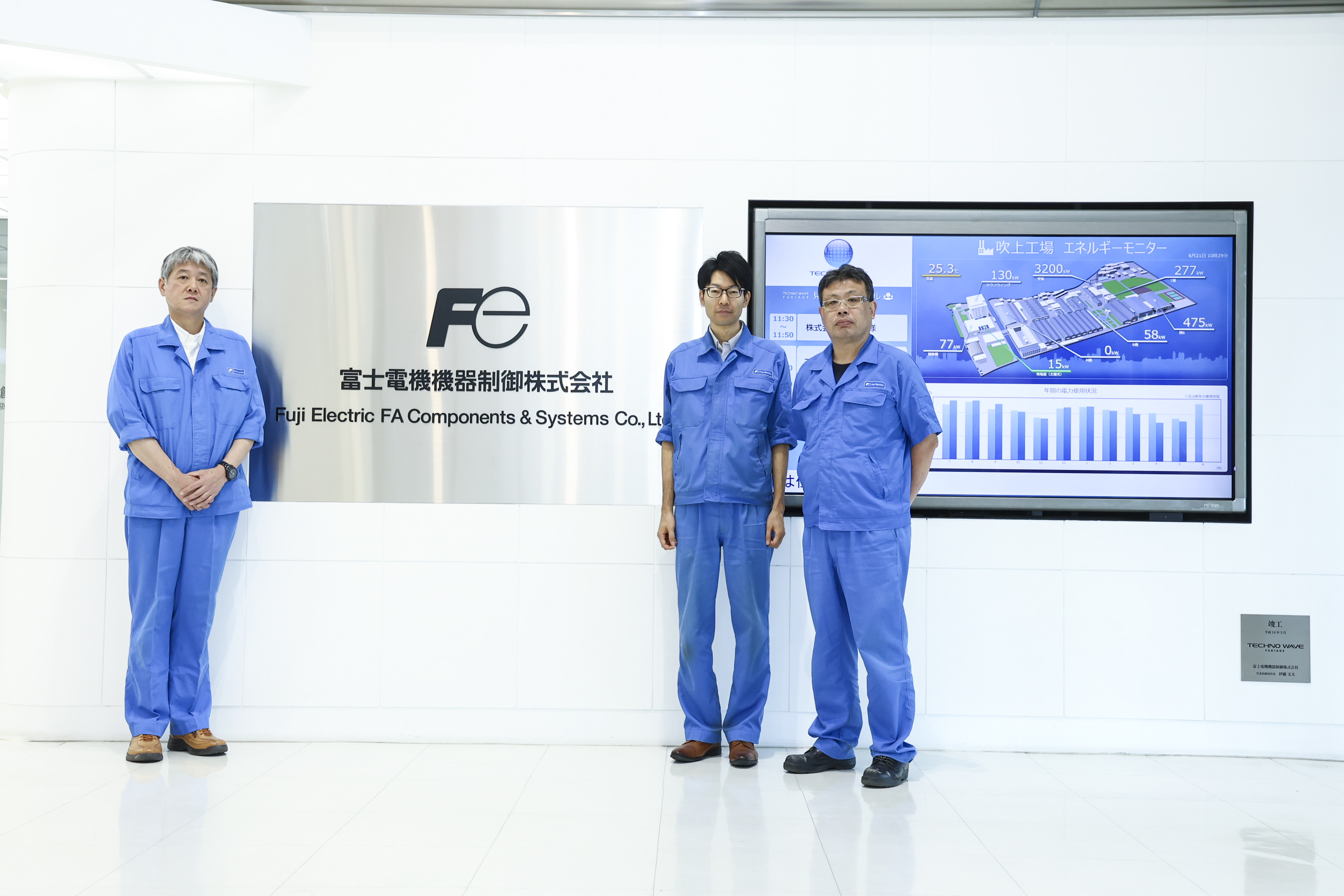
温室効果ガス削減を加速させる。
吹上工場で、環境への取り組みがスタートしたのは、今から10年以上前のことだ。社員が一丸となって省エネの促進と化石燃料からの脱却を目指し、確かな成果を残してきた。生産技術部長を務める小幡剛は、同工場におけるこれまでの活動を次のように話す。
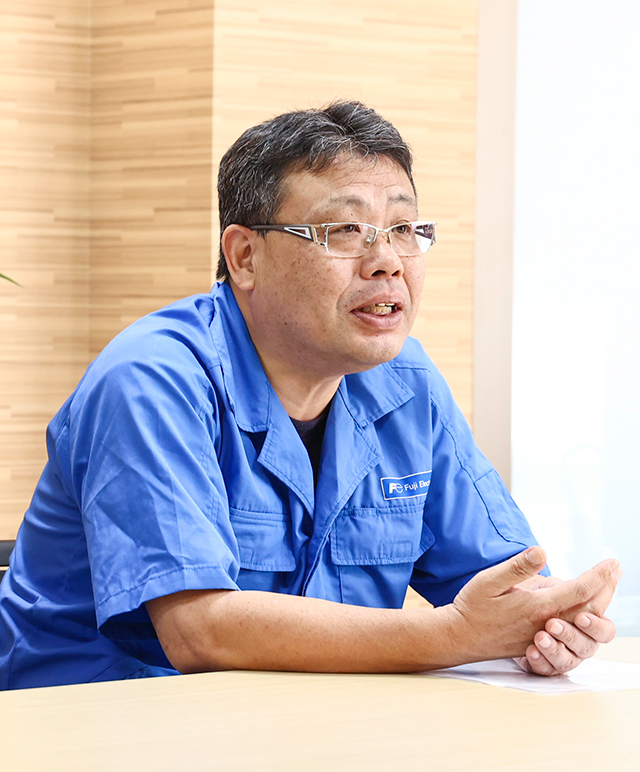
「吹上工場では、自社開発の電力予測システムを活用し、空調設備の電気化や照明・生産設備の更新・改善を行うなどして省エネに取り組み、2020年には『省エネ大賞』を受賞するなど、その成果は社内外から高く評価されています。その活動はさらに活発となり、2030年の生産時の温室効果ガス排出量46%超削減(2019年度比)を目指して、さまざまなチャレンジが進められてきました」
そこで着目したものは、高圧真空遮断器の製造過程で用いられる「SF6ガス」の削減だった。絶縁性に優れ、人体にも安全なこのガスは、生産工程における絶縁を目的に使われてきた。しかし、その一方で、地球温暖化係数がCO2の22,800倍に相当するというデメリットを抱えていたのだ。
「サステナブルなものつくりを実現する上で、『SF6ガス』の削減は喫緊の課題でした。その影響はきわめて大きく、当工場の温室効果ガス排出量の約70%を占めるほど。このガスを使わない『新たな工程・技術』を開発・確立することができれば、温室効果ガス削減の取り組みは、より一層加速していくことになります。このプロジェクトは、吹上工場の未来を切り拓く、新たなチャレンジであったと言えるでしょう」(小幡)
2030年度目標
産業革命前と比較した気温上昇を1.5℃に抑えるため、以下の目標達成を目指します。
-
サプライチェーン全体の温室効果ガス排出量(Scope1+2+3)
46%超削減(2019年度比)
-
生産時の温室効果ガス排出量(Scope1+2)
46%超削減(2019年度比)
-
製品による社会のCO2削減貢献量
5,900万トン超/年
期待と不安を抱き、ものつくりの革新に挑む。
高電圧の電気を流すことで製品の表面を滑らかにする。コンディショニングと呼ばれる工程で、絶縁に使われていた「SF6ガス」に代わる手段を見出す。それが、このプロジェクトの概要だ。その課題を解決すべく、プロジェクトにアサインされたのが、真空遮断器に関する生産技術を知り尽くした生産技術部 吹上作業研究課の新井康功。そして、設備のエキスパートであるFE生産・調達本部生産技術センター 設備技術部 要素技術開発課の中原浩昭だ。二人はアサイン時の心境を次のように振り返る。
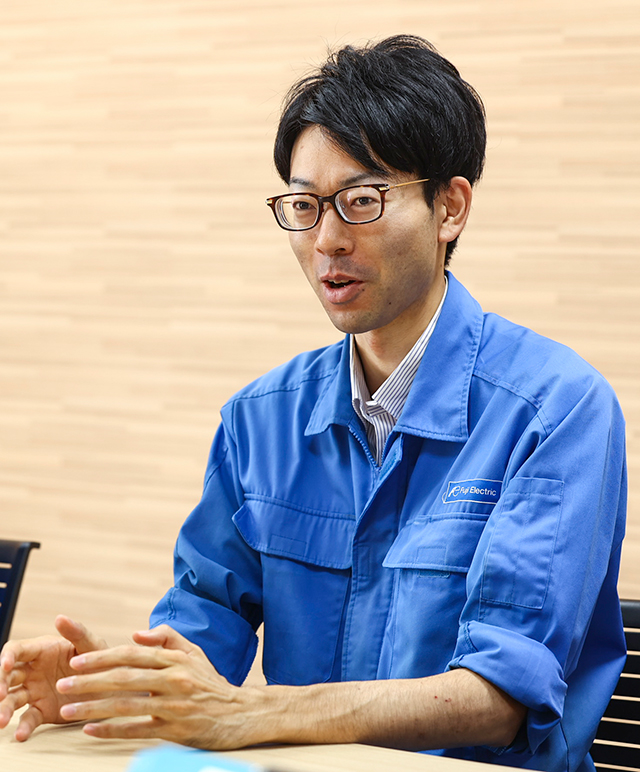
「技術的なハードルがきわめて高く、実現したくてもできない。『SF6ガス』の削減は、私たちにとって『念願のテーマ』だったんです。本プロジェクトでは、設備のエキスパートとしてさまざまな課題を解決してきた中原さんの協力を得られることになり、私としては『是が非でも成し遂げてみせる』という心境でした。もちろん、プロジェクトの成功が難題であることはわかっていましたが、今までにない期待感があったと思います」(新井)
「これまでに数々の設備や技術に関わってきましたが、これほど高圧の設備に関わることは初めての経験。これまでの方法から脱却し、より安全で、より品質の高いものつくりを実現することは、きわめてハードルの高いチャレンジでした。期待してくれていた新井さんには申し訳ないですが、不安しかなかったというのが本音です」(中原)
削減するだけでは、意味がない。
「SF6ガス」を使用しない、新たな技術・製造方法を見出す。その命題を実現するために、メンバーたちは、あらゆる可能性を模索し続けた。常に意識していたのは、今ある製造方法に新たな手間やコストをかけないことだった。排出した「SF6ガス」を回収する方法では、今まで以上にコストがかかる。絶縁のために、製品を油に浸す「湿式」の方法では、洗浄と乾燥という二つの工程が増えてしまう。最終的な結論は、「圧縮空気」を用いることだった。
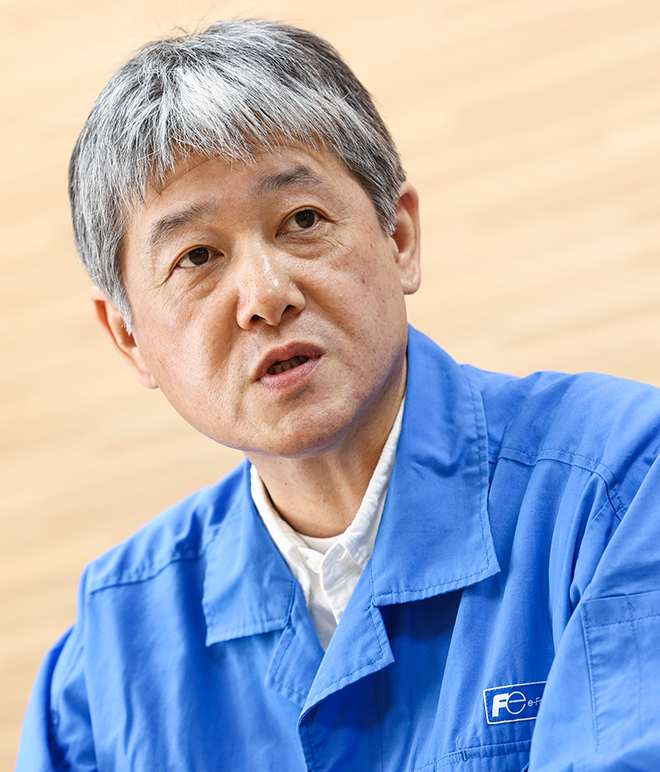
「作業性やガスの管理、費用の面を考慮して、空気を使う方法を考えました。ところが、それでは目標としていた絶縁性能を実現できないという課題に直面したんです。そこで、至った結論が、空気を圧縮し、絶縁性を向上させることでした」(中原)
メンバーたちが試行錯誤を重ねて導き出した答え。そこから生まれた価値は、きわめて大きく、当初の目標よりも20%近く高い絶縁性能だった。量産に向けては、季節変動、各部品の加工バラツキを想定する必要があり、ゴールを高く設定し直したのだ。そして、新たな設備・製造方法の実現にあたっては、現場の作業性を最大限に考慮した改良が施されたのだという。
「圧縮した空気を使った新たな製造方法を実現するにあたって、従来設備の50%ほどを刷新・改造することになりました。コンディショニングの工程では、製品を特殊な容器で覆い、そこに圧縮した空気を送り込み、高圧の電気が流されます。その容器はきわめて重く、それを手作業で運ぶとなれば、作業者に大きな負担をかけてしまうわけです。それらを自動化する機能を新たに開発するなど、何よりも現場を意識したラインが完成したと自負しています」(新井)
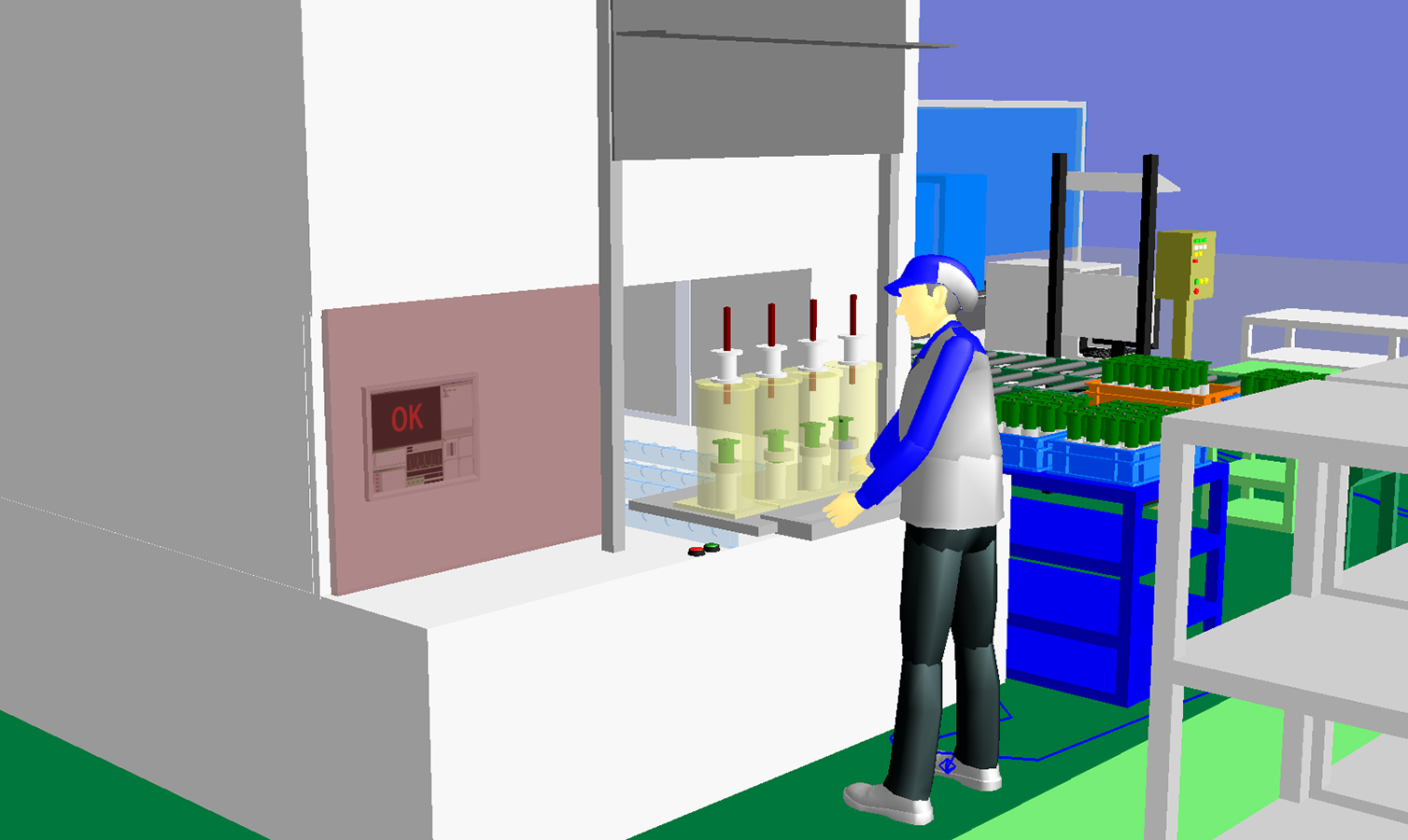
2030年の目標を前倒しで達成。
本プロジェクトの成功によって、吹上工場は「SF6ガス」の95%削減を達成することができた。これによって、吹上工場では2030年度の「温室効果ガス削減46%超削減」という目標を前倒しでクリアする。多くの富士電機社員が彼らの偉業を称えたことは言うまでもない。メンバーたちは、この一大プロジェクトをそれぞれに振り返る。
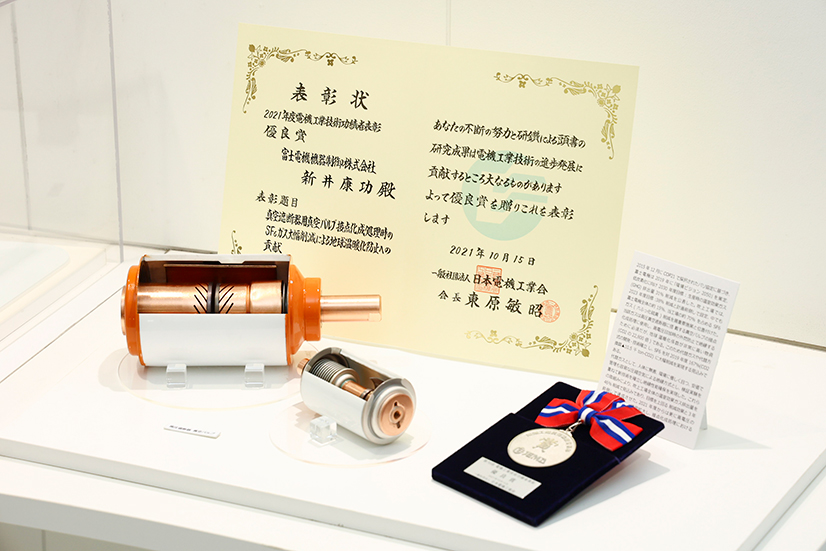
「ずっと解決できなかった難題をクリアし、量産化までをスムーズに進めることができたのは、部門を超えたメンバーが想いをひとつに、一体となってプロジェクトを推進できたからだと思っています。このプロジェクトを成功させることができたことを誇らしく感じていますが、ここがゴールではありません。今後もチームワークで改善に取り組み、次代のものつくりを実現していきたいですね」(新井)
「このプロジェクトの成功を受けて、表彰の機会などもありましたが、もっとも達成感を得られたのは、現場から『SF6ガス』のボンベがなくなったことを見た瞬間でした。私たちの技術開発によって、明確にそれがなくなったことを意識できたわけですから。これほど、誇らしいことはありません。この経験を活かして、ものつくりのさらなるブラッシュアップに貢献していきたいと思っています」(中原)
「新技術の確立によって、『SF6ガス』を大幅削減することができた。プロジェクトのとりまとめ役として、新たな価値を創り出したメンバーたちを心から誇らしく思っています。とはいえ、これですべてを解決できたわけではありません。このプロジェクトで得られた経験や知見は、今後の改善に向けて、貴重な財産となるものです。温室効果ガス排出ゼロを目指して、さらなるチャレンジに邁進し、『環境ビジョン2050』を早期に実現したいと考えています」(小幡)
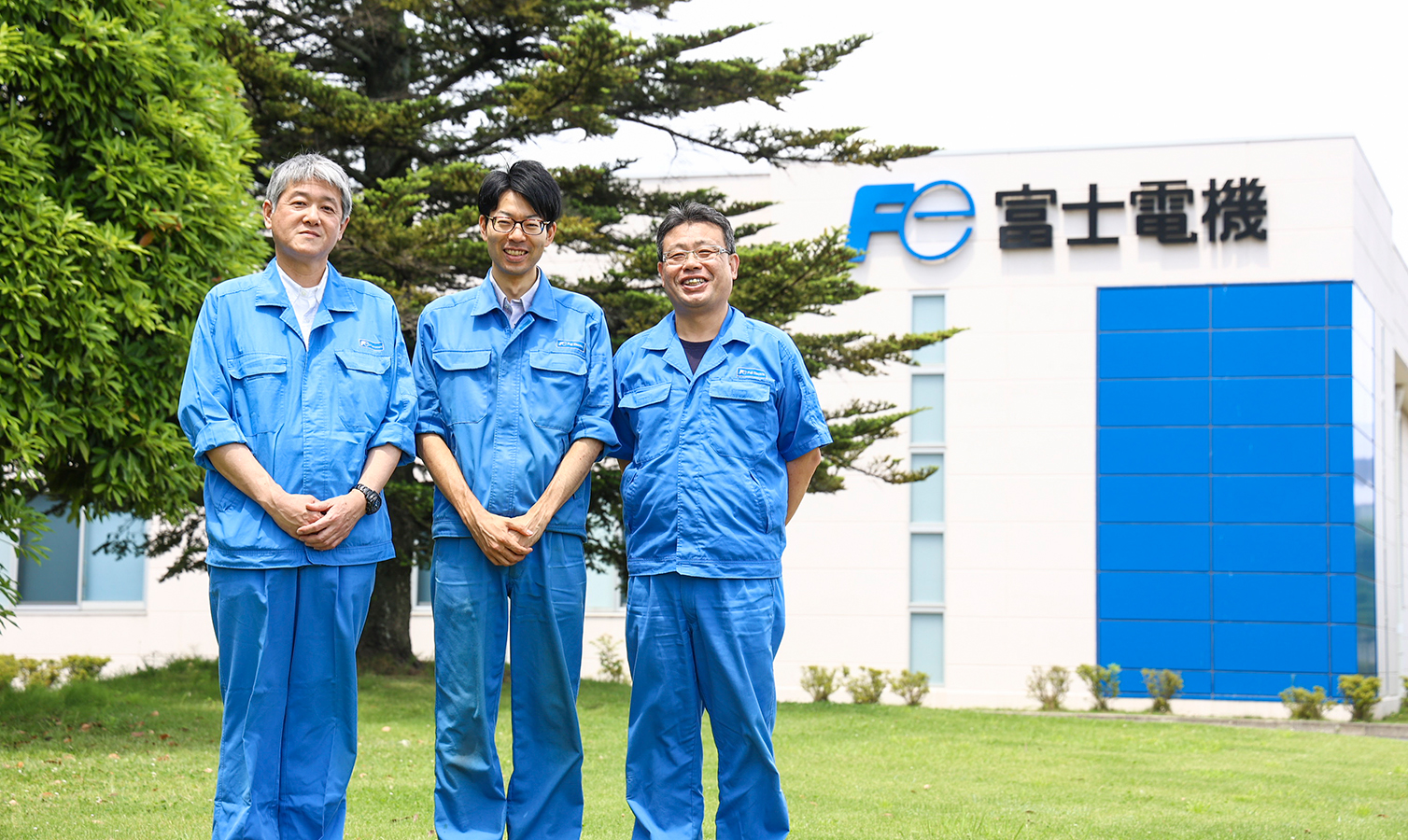
貢献するSDGs目標
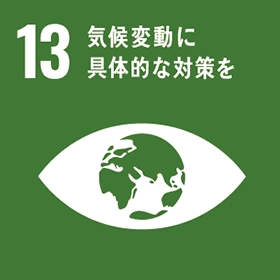
当社は、企業行動基準に「地球環境を大切にします」を掲げ、地球環境保護への取り組みを経営の重要課題の一つと位置づけています。SDGs目標「13. 気候変動に具体的な対策を」を当社が取り組む重点目標の一つに掲げており、長期的に取り組むべき環境活動の方向性として、「環境ビジョン2050」および「2030年度目標」を策定し、生産活動を含めたサプライチェーン全体での温室効果ガス排出量削減に向けて取り組んでいます。